Field effect transistor key
Perhaps even a person far from electronics has heard that there is such an element as a relay. The simplest electromagnetic relay contains an electromagnet, when voltage is applied to it, two other contacts are closed. With the help of a relay, we can switch a fairly powerful load, applying or vice versa, removing voltage from the control contacts. The most widespread are relays controlled from 12 volts. There are also relays for voltages of 3, 5, 24 volts.
However, you can switch a powerful load not only with the help of a relay. Recently, high-power field-effect transistors have become widespread. One of their main purposes is to operate in key mode, i.e. the transistor is either closed or completely open when the resistance of the Drain-Source junction is practically zero. You can open a field-effect transistor by applying voltage to the gate relative to its source. You can compare the operation of a switch on a field-effect transistor with the operation of a relay - voltage is applied to the gate, the transistor opens, and the circuit closes. The voltage was removed from the gate - the circuit was opened, the load was de-energized.
In this case, a field-effect transistor switch has some advantages over a relay, such as:
- Great durability. Quite often, relays fail due to the presence of mechanically moving parts, but a transistor under the right operating conditions has a much longer service life.
- Economical. The relay winding consumes current, sometimes quite significant. The gate of the transistor consumes current only when voltage is applied to it, then it consumes virtually no current.
- No clicks when switching.
Scheme
The switch circuit for the field effect transistor is presented below:
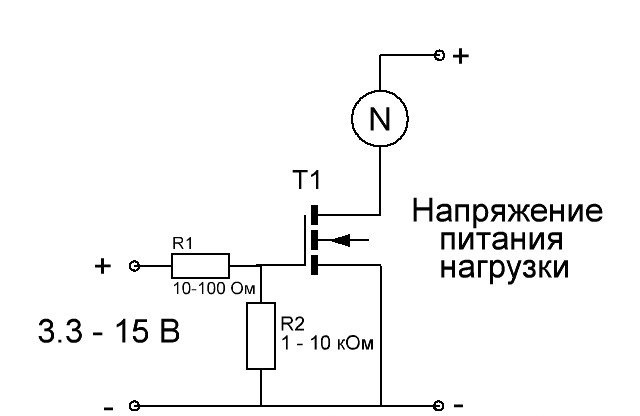
The resistor R1 in it is current-limiting; it is needed in order to reduce the current consumed by the gate at the moment of opening; without it, the transistor may fail. The value of this resistor can be easily changed within a wide range, from 10 to 100 Ohms, this will not affect the operation of the circuit.
Resistor R2 pulls the gate to the source, thereby equalizing their potentials when no voltage is applied to the gate. Without it, the gate will remain “hanging in the air” and the transistor cannot be guaranteed to close. The value of this resistor can also be changed within a wide range - from 1 to 10 kOhm.
Transistor T1 is an N-channel field-effect transistor. It must be selected based on the power consumed by the load and the value of the control voltage. If it is less than 7 volts, you should take a so-called “logical” field-effect transistor, which reliably opens from a voltage of 3.3 - 5 volts. They can be found on computer motherboards. If the control voltage is in the range of 7-15 volts, you can take a “regular” field-effect transistor, for example, IRF630, IRF730, IRF540 or any other similar ones.In this case, you should pay attention to such a characteristic as the open channel resistance. Transistors are not ideal, and even in the open state, the resistance of the Drain-Source junction is not zero. Most often it amounts to hundredths of an Ohm, which is not at all critical when switching a low-power load, but is very significant at high currents. Therefore, in order to reduce the voltage drop across the transistor and, accordingly, reduce its heating, you need to choose a transistor with the lowest open-channel resistance.
“N” in the diagram – any load.
The disadvantage of a transistor switch is that it can only work in DC circuits, because the current flows only from Drain to Source.
Making a field-effect transistor switch
It is possible to assemble such a simple circuit using surface mounting, but I decided to make a miniature printed circuit board using laser-iron technology (LUT). The procedure is as follows:
1) Cut out a piece of PCB that fits the dimensions of the printed circuit board design, clean it with fine sandpaper and degrease it with alcohol or solvent.
2) We print the design of the printed circuit board on special thermal transfer paper. You can use glossy magazine paper or tracing paper. The toner density on the printer should be set to maximum.
3) Transfer the design from paper to textolite using an iron. In this case, you should ensure that the paper with the design does not move relative to the textolite. The heating time depends on the temperature of the iron and ranges from 30 to 90 seconds.
4) As a result, a mirror image of the tracks appears on the PCB. If the toner does not stick well to the future board in some places, you can correct the flaws using women's nail polish.
5) Next, we put the textolite to be etched.There are many ways to make an etching solution, I use a mixture of citric acid, salt and hydrogen peroxide.
After etching, the board takes on this form:
6) Then you need to remove the toner from the PCB, the easiest way to do this is with nail polish remover. You can use acetone and other similar solvents; I used petroleum solvent.
7) It’s just a matter of small things - now all that’s left is to drill holes in the right places and tin the board. After this it looks like this:The board is ready for parts to be soldered into it. You only need two resistors and a transistor.
The board has two contacts for supplying control voltage, two contacts for connecting the source powering the load, and two contacts for connecting the load itself. The board with soldered parts looks like this:
As a load to test the operation of the circuit, I took two powerful 100 Ohm resistors connected in parallel.
I plan to use the device in conjunction with a humidity sensor (board in the background). It is from this that the control voltage of 12 volts is supplied to the key circuit. Tests have shown that the transistor switch works perfectly, supplying voltage to the load. The voltage drop across the transistor was 0.07 volts, which in this case is not at all critical. The transistor does not heat up even with constant operation of the circuit. Happy build!
Download the board and diagram:Similar master classes
Particularly interesting
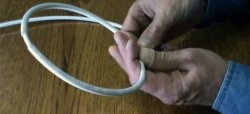
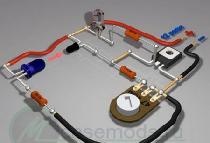
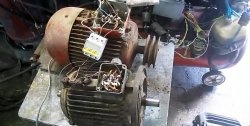
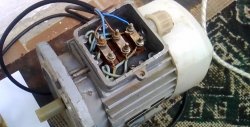
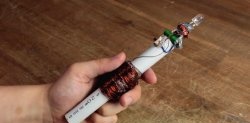
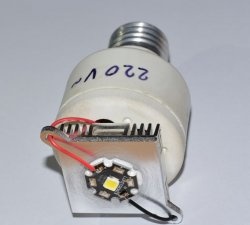