Twisting of wires without soldering that cannot be broken
It happens that it is necessary to connect several pieces of a certain type of wire. We are not talking about wiring of different sections. As for connecting wiring from different metals, here you need to be extremely careful, and without knowledge in this particular area, you shouldn’t even think about it. We will talk about twisted connections of identical wires. For example, when a portable lamp, extension cord, or a long wire breaks from a house window to the engine heater in a car in winter, as well as in a summer cottage when a suspended cable from a house to a bathhouse, barn or enclosure with an animal breaks. There are different cases, somewhere someone tripped and broke the wire, somewhere it was torn by the wind, or an ice floe fell from the roof - it doesn’t matter. The main thing is that it is important to apply reliable twisting to each type of wire so that the connection is no weaker than a solid cable.
Of course, many will say that in the event of a break, you can simply twist the two exposed (and de-energized!) ends of the wire with a regular twist, thoroughly tin this twist with tin and wrap it with electrical tape.But a soldering iron is not applicable everywhere. For example, if the wires are aluminum. Soldering aluminum wires is, of course, quite possible, but not with what is usually used when soldering copper. And in general, soldering aluminum is a headache... And for one reason or another, a soldering iron may not always be available. Also, braiding plays an important role in the strength of a wire or cable. On some of our connections it will be double - as an additional strengthening of the break point, the inner layer is made of electrical tape, the outer layer is made of heat-shrinkable tubing. And now I propose to consider several types of reliable twists that will help you do without a soldering iron with tin.
Use wire cutters or scissors to straighten the uneven ends of the wire after breaking. Remove two centimeters of braid from the end of the wire.
Divide the copper hairs in the wire into two halves. You will get a bifurcated ending.
Repeat the procedures with the second wire. Place the forked ends next to each other and twist them, each branch separately.
Next, lightly pull the wire so that it becomes straight, and twist each branch around the wire in the opposite direction from each other.
Wrap with electrical tape and crimp with heat shrink tubing.
This twisting method for small-section aluminum wiring is the most tensile. Moreover, it is not so labor-intensive. Let's prepare the wiring.For example, I took segments - it’s not easy to handle long wires in front of the camera... But the process is not too different, as you understand, the only difference is that during real work you may have to stand on a stepladder or a chair... So, we strip the core from the braid by 3-4 cm.
We retreat from the edge of the braid about 6-7 mm. and bend the remaining wire at an angle of 90 degrees.
We apply the bent ends of the wire to each other, like this:
We wind the bent ends of the wire onto the wire of the opposite wire.
We help ourselves with pliers, since bending the end of a rigid wire with your fingers is very problematic. Finally, we insulate it with electrical tape and place a heat-shrink tube on top of the electrical tape.
Ready. And it is more likely (with excessive tension) that the wire will break in another place than this twist will unravel.
In fact, there is nothing complicated here either. First, we divide the double wire into two separate wires. Ten centimeters from above. Then we strip the wires by 3 cm and immediately put heat-shrinkable tubes on them so as not to forget to do this later, otherwise you will have to disassemble the twist back to correct this omission.
We repeat the above procedure with the second wire and immediately put another heat-shrinkable tube on it, of a slightly larger diameter, for general insulation of both wires.
Next, we twist the bare ends as follows: we apply the wires to each other so that there is a distance of about a centimeter and a half between the edges of the braids. We wind the end of one wire around the base of the other. Then, in the same way, the second wire. You will get a twist like this.
If in the description and in the photo it is not very clear how exactly the twisting is done: in the video, at the end of the article, everything is quite clearly visible and understandable. Now we move the heat-shrinkable tubes prepared in advance on the wires onto the twists themselves, and seat them with a lighter.
Next, we move the common tube to the places of the twists and also seat it with a lighter. In addition to strengthening the braid, the heat-shrinkable tube also performs some aesthetic function; it looks much better than wound electrical tape.
This is how the twist turned out. Strong and reliable, and most importantly – safe.
When working with electrical appliances and electrical wiring, do not forget about safety measures. Use tools with undamaged insulation and do not forget to disconnect the object being repaired from the power supply. Remember that exposure to electric current on the body is dangerous to health.
Of course, many will say that in the event of a break, you can simply twist the two exposed (and de-energized!) ends of the wire with a regular twist, thoroughly tin this twist with tin and wrap it with electrical tape.But a soldering iron is not applicable everywhere. For example, if the wires are aluminum. Soldering aluminum wires is, of course, quite possible, but not with what is usually used when soldering copper. And in general, soldering aluminum is a headache... And for one reason or another, a soldering iron may not always be available. Also, braiding plays an important role in the strength of a wire or cable. On some of our connections it will be double - as an additional strengthening of the break point, the inner layer is made of electrical tape, the outer layer is made of heat-shrinkable tubing. And now I propose to consider several types of reliable twists that will help you do without a soldering iron with tin.
Will need
- Stationery knife.
- Pliers.
- Wire cutters or scissors (depending on the wire).
- Insulating tape.
- Heat-shrinkable tubes (with a diameter corresponding to the thickness of each core separately, and to the thickness of the cable, in general).
Method 1: Flexible single copper wire.
Use wire cutters or scissors to straighten the uneven ends of the wire after breaking. Remove two centimeters of braid from the end of the wire.
Divide the copper hairs in the wire into two halves. You will get a bifurcated ending.
Repeat the procedures with the second wire. Place the forked ends next to each other and twist them, each branch separately.
Next, lightly pull the wire so that it becomes straight, and twist each branch around the wire in the opposite direction from each other.
Wrap with electrical tape and crimp with heat shrink tubing.
Method 2: Rigid single aluminum wire.
This twisting method for small-section aluminum wiring is the most tensile. Moreover, it is not so labor-intensive. Let's prepare the wiring.For example, I took segments - it’s not easy to handle long wires in front of the camera... But the process is not too different, as you understand, the only difference is that during real work you may have to stand on a stepladder or a chair... So, we strip the core from the braid by 3-4 cm.
We retreat from the edge of the braid about 6-7 mm. and bend the remaining wire at an angle of 90 degrees.
We apply the bent ends of the wire to each other, like this:
We wind the bent ends of the wire onto the wire of the opposite wire.
We help ourselves with pliers, since bending the end of a rigid wire with your fingers is very problematic. Finally, we insulate it with electrical tape and place a heat-shrink tube on top of the electrical tape.
Ready. And it is more likely (with excessive tension) that the wire will break in another place than this twist will unravel.
Method 3: flexible two-core copper wire.
In fact, there is nothing complicated here either. First, we divide the double wire into two separate wires. Ten centimeters from above. Then we strip the wires by 3 cm and immediately put heat-shrinkable tubes on them so as not to forget to do this later, otherwise you will have to disassemble the twist back to correct this omission.
We repeat the above procedure with the second wire and immediately put another heat-shrinkable tube on it, of a slightly larger diameter, for general insulation of both wires.
Next, we twist the bare ends as follows: we apply the wires to each other so that there is a distance of about a centimeter and a half between the edges of the braids. We wind the end of one wire around the base of the other. Then, in the same way, the second wire. You will get a twist like this.
If in the description and in the photo it is not very clear how exactly the twisting is done: in the video, at the end of the article, everything is quite clearly visible and understandable. Now we move the heat-shrinkable tubes prepared in advance on the wires onto the twists themselves, and seat them with a lighter.
Next, we move the common tube to the places of the twists and also seat it with a lighter. In addition to strengthening the braid, the heat-shrinkable tube also performs some aesthetic function; it looks much better than wound electrical tape.
This is how the twist turned out. Strong and reliable, and most importantly – safe.
When working with electrical appliances and electrical wiring, do not forget about safety measures. Use tools with undamaged insulation and do not forget to disconnect the object being repaired from the power supply. Remember that exposure to electric current on the body is dangerous to health.
Watch video instructions
Similar master classes
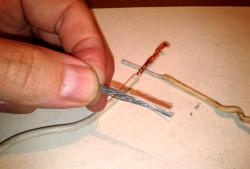
How to properly connect wires from different metals
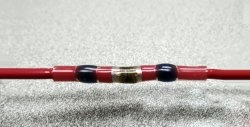
An innovative way to connect two wires
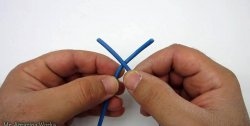
How to reliably connect wires without soldering
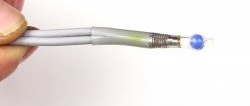
How to make tubes for quick soldering of wires from ordinary
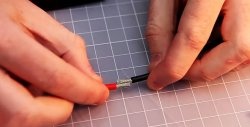
The strongest connection of large cross-section wires without thickening
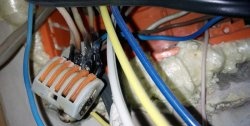
The three most reliable ways to connect wires in
Particularly interesting
Comments (47)