The strongest connection of large cross-section wires without thickening by twisting
Splicing stranded wires with a large cross-section only by twisting is subsequently accompanied by oxidation, deterioration of contact and an increase in resistance. Plus, ordinary twisting has an unesthetic appearance and a significant thickening at the junction. A more correct and reliable connection method would be soldering, but on thick wires from 10 mm sq. It's difficult to do this with a soldering iron. Of course, you can use a crucible, but not everyone has one. Let's look at a simple and reliable way to solder thick wires with a regular soldering iron.
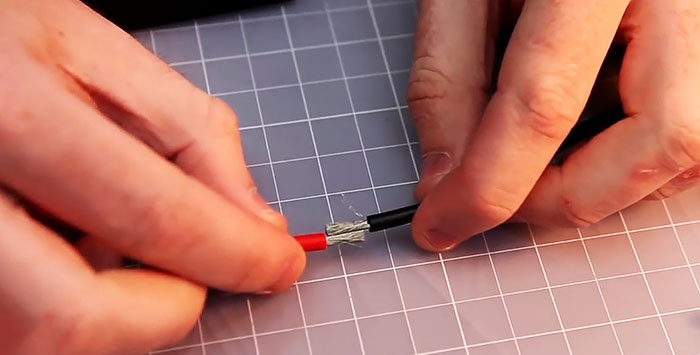
The ends of the wires must be cleaned of insulation with a stripper or knife. It is enough to open about 1 cm each. The exposed stranded strands should be fluffed up and joined at the ends.
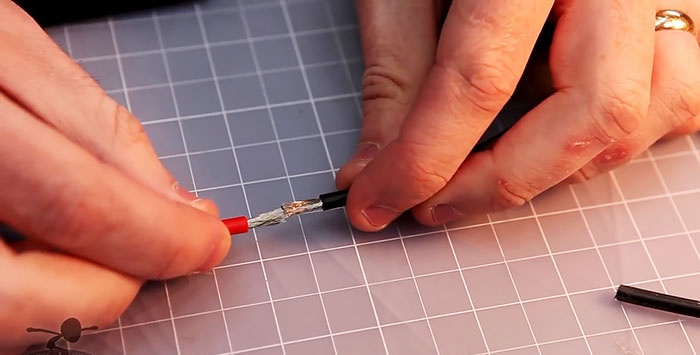
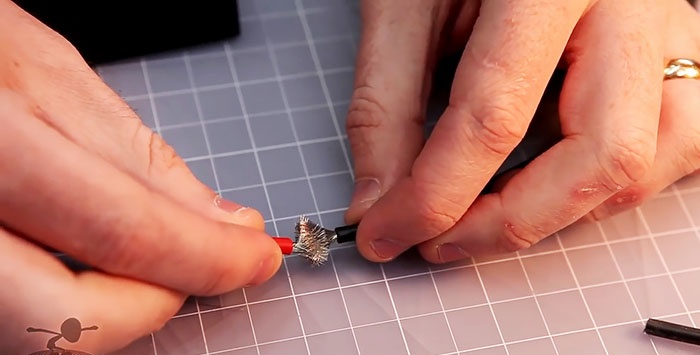
When connected, they will fan out, so you will need to gently squeeze them with your fingers.
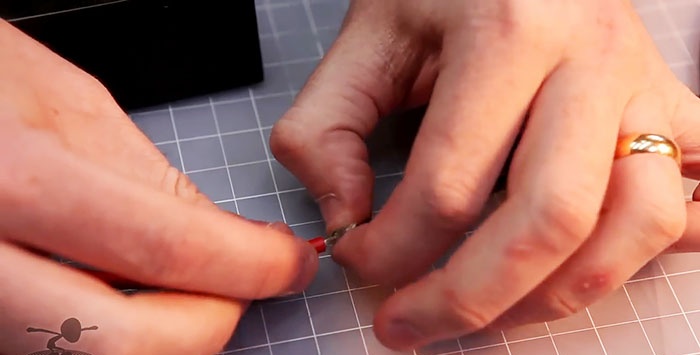
The cores at the splice point are wrapped with thin copper wire, preferably thicker than the individual wires in the wires being connected. It can be obtained from the cable PVZ, ShVVP and the like.
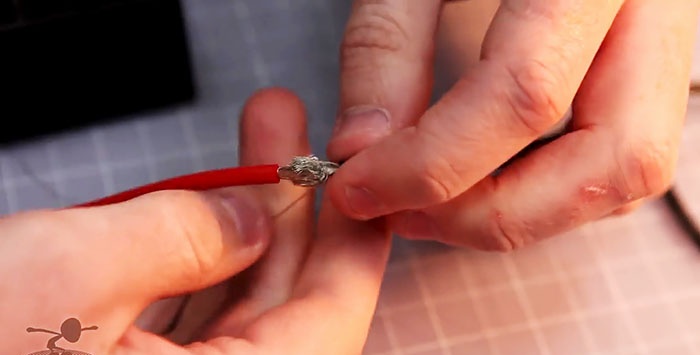
The winding should be carried out at medium frequency. If you lay the coil to the coil, the result will be neater and stronger. When winding, the wire should be tensioned; upon completion, its ends are connected by twisting or inserted into cores. The resulting bandage must be finally tightened. To do this, the connected wires are stretched. The more you pull them, the more the veins are compressed by the bandage. As a result, the connection will be no less resistant to breaking than a solid cable.
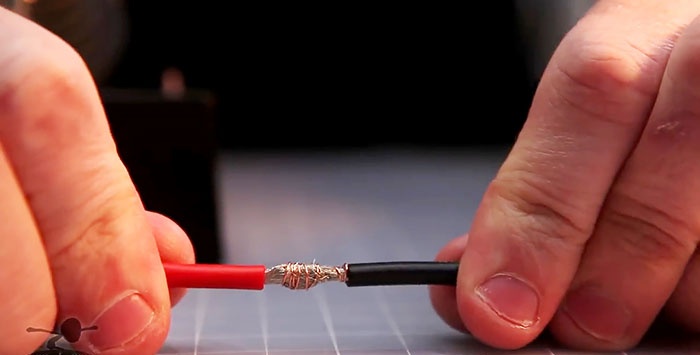
The exposed conductors at the splice site must be coated with flux or an alcoholic rosin solution. After this, the bandage and cores are heated with a soldering iron.
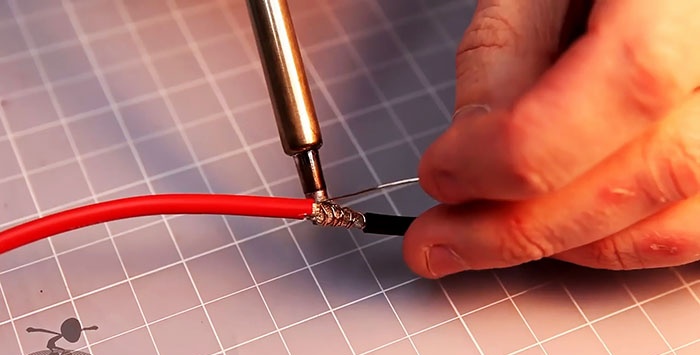
Solder is applied to the hot areas. As it melts, the soldering iron tip needs to be moved further to heat new places. Molten tin penetrates under the bandage and the voids between the interposed core wires. The solder does not drip and lies very smoothly.
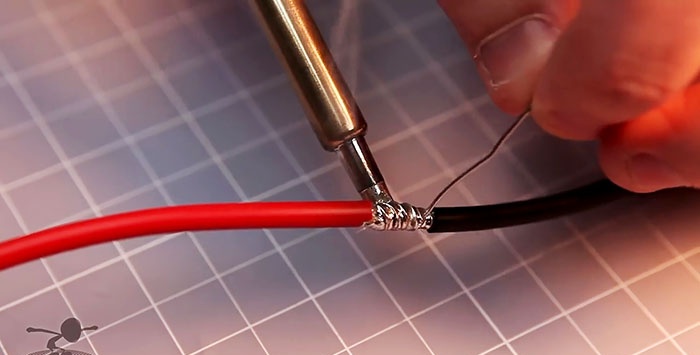
The proposed soldering method produces a very mechanically strong connection. Using a bandage eliminates wastage of tin, since it does not flow down and hang in drops. The splice itself looks neat and creates minimal resistance. If you use a sufficiently powerful soldering iron, then each connection can be prepared in a couple of minutes.
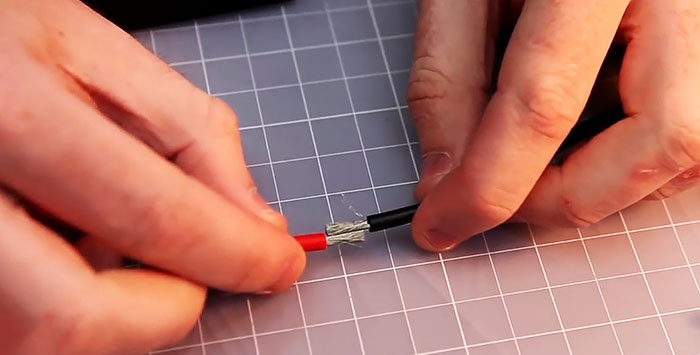
Tools and materials:
- solder;
- flux or alcohol solution of rosin;
- soldering iron;
- thin copper wire;
- stripper or mounting knife.
Preparing wires and soldering
The ends of the wires must be cleaned of insulation with a stripper or knife. It is enough to open about 1 cm each. The exposed stranded strands should be fluffed up and joined at the ends.
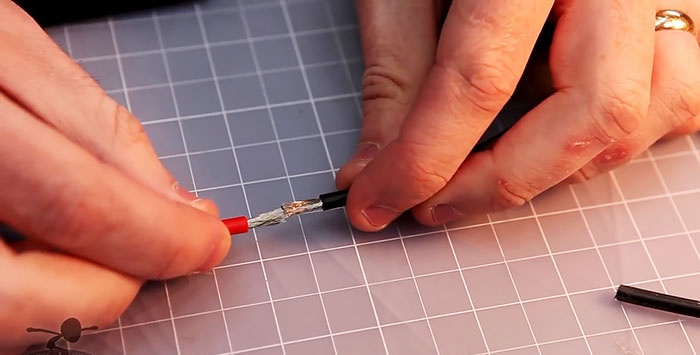
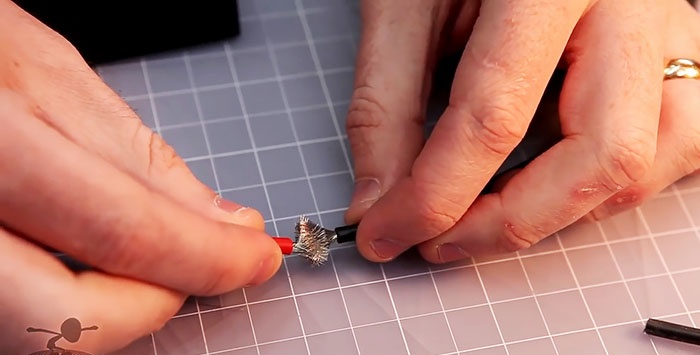
When connected, they will fan out, so you will need to gently squeeze them with your fingers.
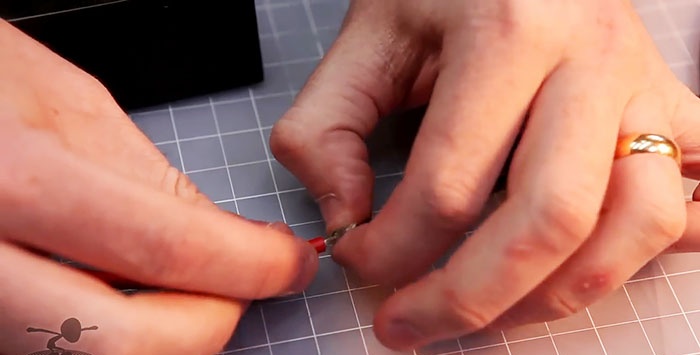
The cores at the splice point are wrapped with thin copper wire, preferably thicker than the individual wires in the wires being connected. It can be obtained from the cable PVZ, ShVVP and the like.
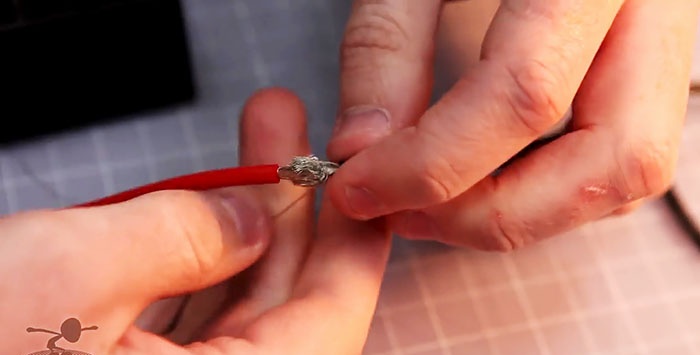
The winding should be carried out at medium frequency. If you lay the coil to the coil, the result will be neater and stronger. When winding, the wire should be tensioned; upon completion, its ends are connected by twisting or inserted into cores. The resulting bandage must be finally tightened. To do this, the connected wires are stretched. The more you pull them, the more the veins are compressed by the bandage. As a result, the connection will be no less resistant to breaking than a solid cable.
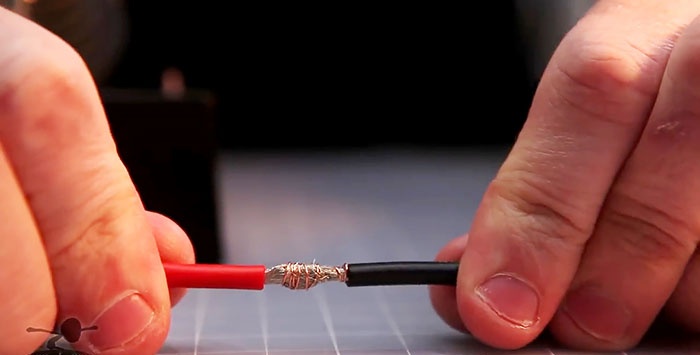
The exposed conductors at the splice site must be coated with flux or an alcoholic rosin solution. After this, the bandage and cores are heated with a soldering iron.
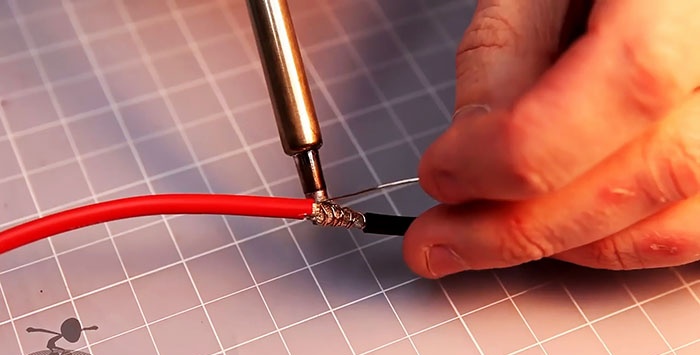
Solder is applied to the hot areas. As it melts, the soldering iron tip needs to be moved further to heat new places. Molten tin penetrates under the bandage and the voids between the interposed core wires. The solder does not drip and lies very smoothly.
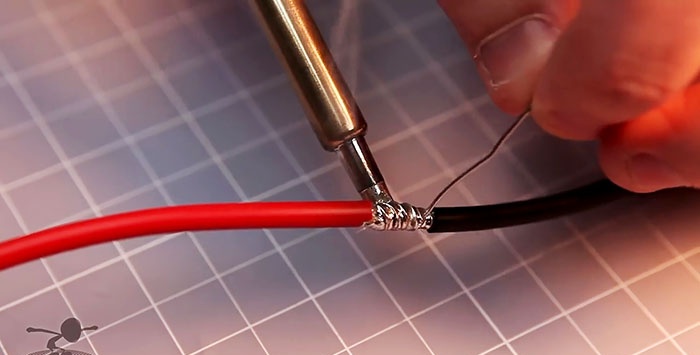
The proposed soldering method produces a very mechanically strong connection. Using a bandage eliminates wastage of tin, since it does not flow down and hang in drops. The splice itself looks neat and creates minimal resistance. If you use a sufficiently powerful soldering iron, then each connection can be prepared in a couple of minutes.
Watch the video
Similar master classes
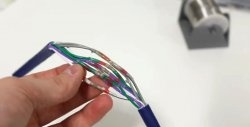
Solder sleeves - your salvation when there is no way
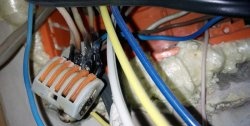
The three most reliable ways to connect wires in
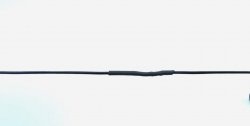
The most reliable connection of wires without a soldering iron
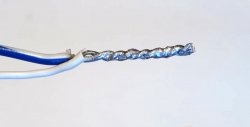
Soldering strands of aluminum and copper wire
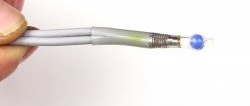
How to make tubes for quick soldering of wires from ordinary
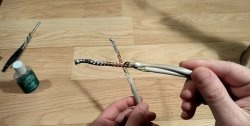
Device for soldering twisted wires
Particularly interesting
Comments (15)