How to turn an electric motor armature into an effective tool
From the rotor of a burnt brush electric motor, on the basis of which almost all power tools are assembled - grinders, drills, hammer drills, screwdrivers, drills, electric saws, etc. - you can make an interesting and practical tool that can be useful in any garage or workshop. What will we need for this?

In addition to the scarce anchor, which can be removed from a burnt drill, grinder, etc. or can be easily found at a metal collection point, we must have:
This is not at all difficult to do, even with basic plumbing skills. We remove all removable parts from the anchor - nuts, rings, gears, bearings, using a puller, hammer and pliers.
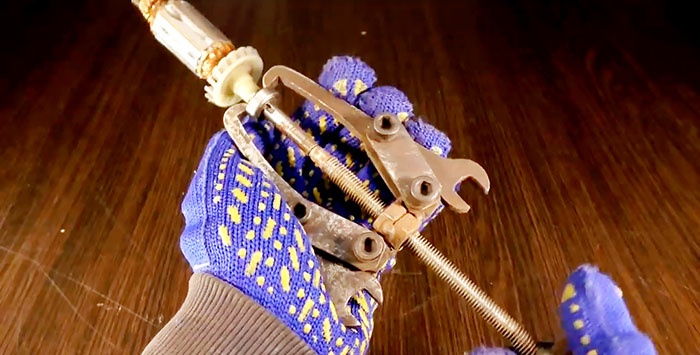
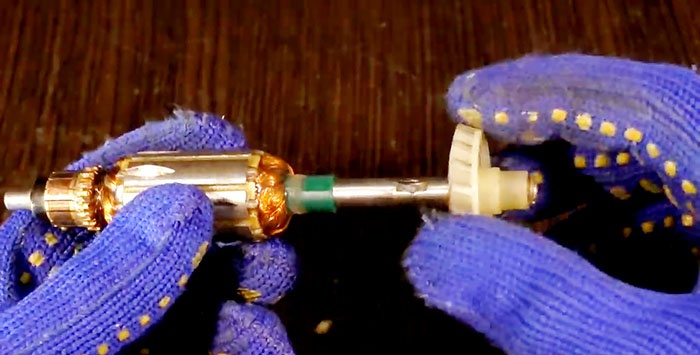
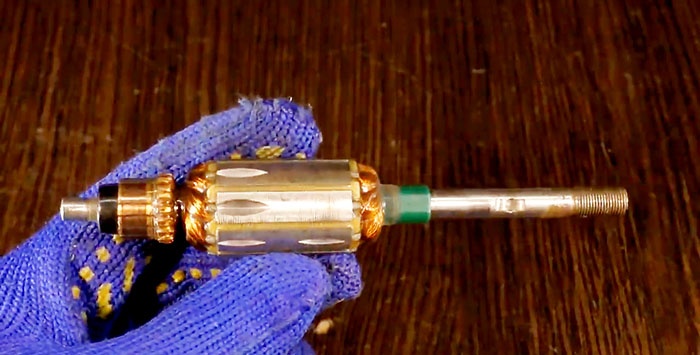
Using a hacksaw for metal, we cut off the part of the armature on which the contact plates of the brush assembly are located, making a cut strictly along the end of the magnetic circuit, having previously secured the rotor in the jaws of a bench vice.
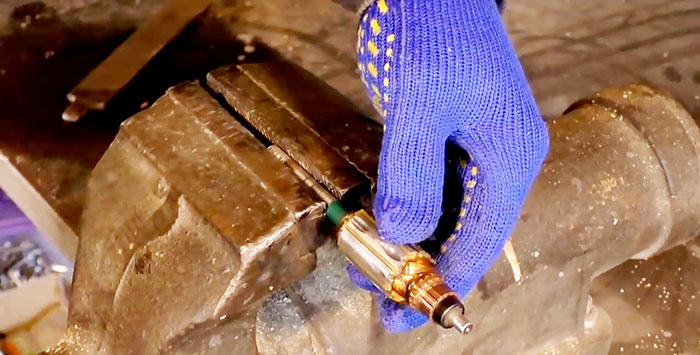
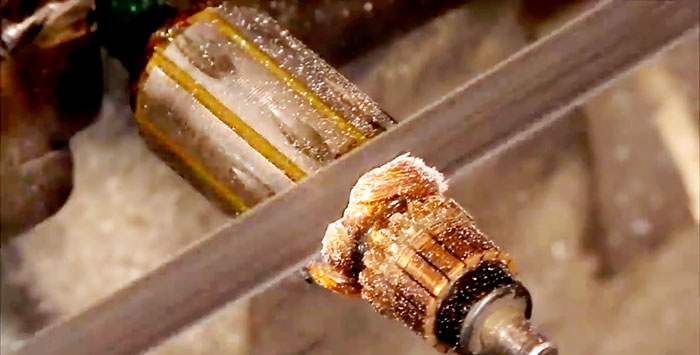
We remove the copper armature winding from the magnetic circuit. To do this, we fix it vertically to the shaft in a vice and, using a gas burner, heat and evaporate the varnish of the armature winding.
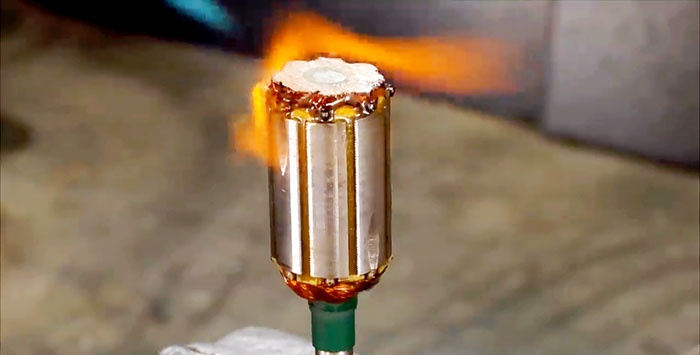
You can heat the rotor in one place. Since copper is an excellent conductor of not only electricity, but also heat, it will quickly spread throughout the entire winding and melt the electrical insulating varnish.
As soon as the varnish boils and begins to drip on the other side of the armature, you can finish heating and begin removing the winding by picking it out with a screwdriver and pulling it out of the grooves of the magnetic circuit with pliers. If the process becomes difficult, you can again slightly warm up the winding with the flame of a gas burner.
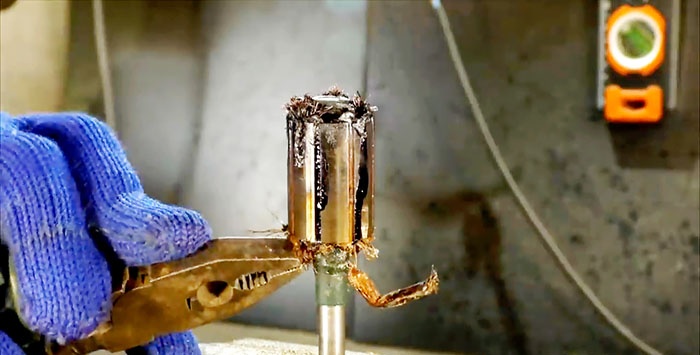
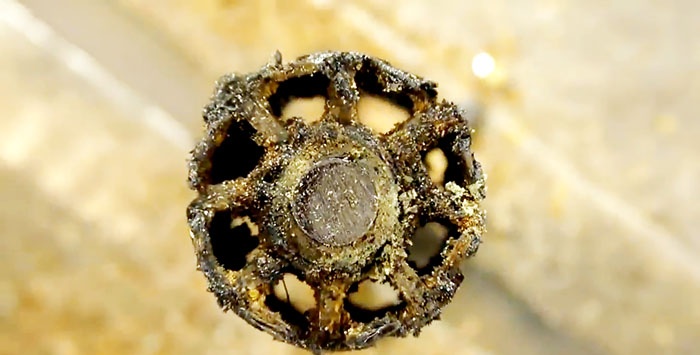
After removing the entire winding from the magnetic circuit, a system of through holes and grooves opens, which were previously filled with copper windings and filled with varnish.
Using available means, we clean the magnetic circuit from carbon deposits and residues of electrical insulating varnish.
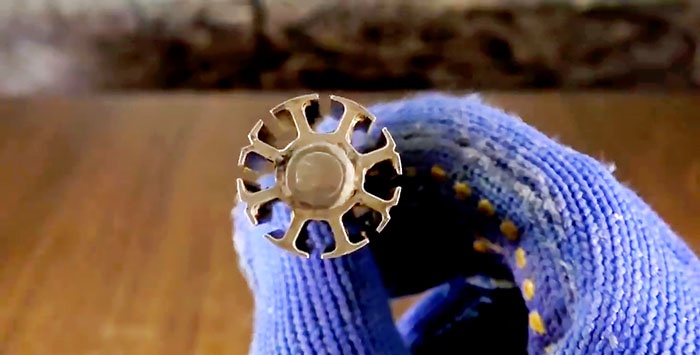
All we have to do is equip the magnetic core nozzle with pieces of sandpaper of the same length, which are very simply and securely attached to the grooves.
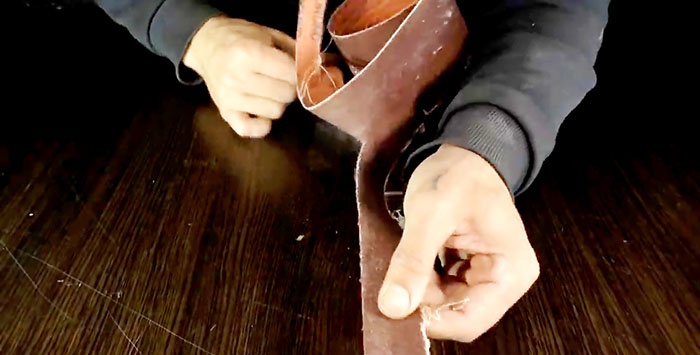
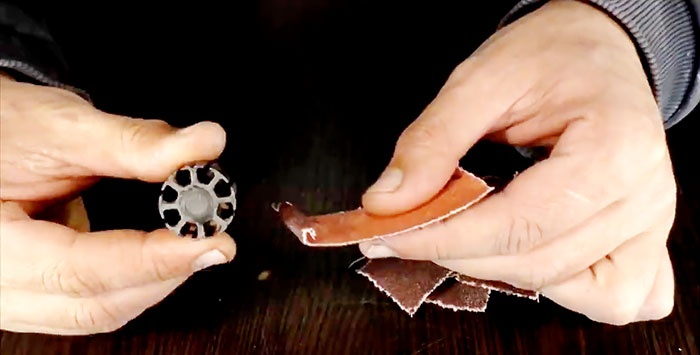
The result is a very effective abrasive tool, which, depending on the number of sanding tape, can perform certain operations.
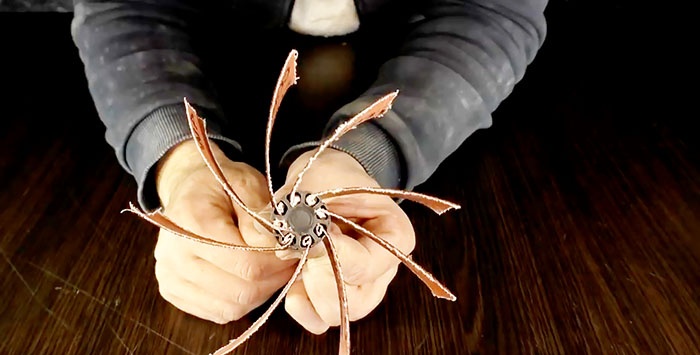
Let's check our homemade abrasive tool in action.
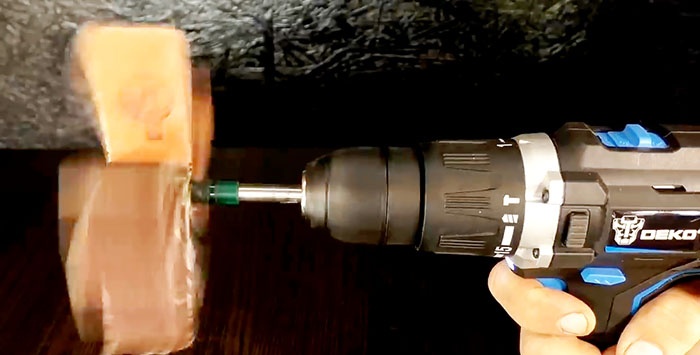
To do this, we fix the shaft of the former anchor, which now serves as a shank, into the drill chuck, and grind the surface of the wooden and metal workpiece.The result is excellent and the process is efficient.
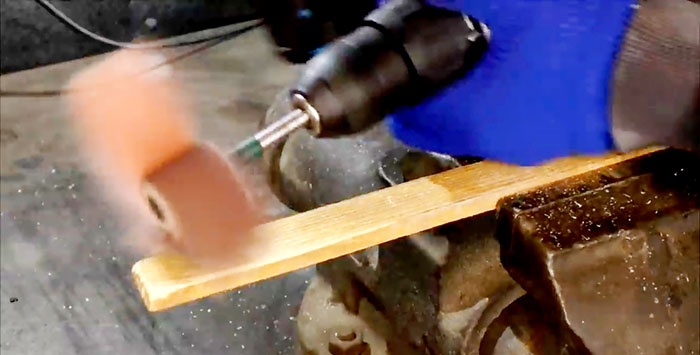
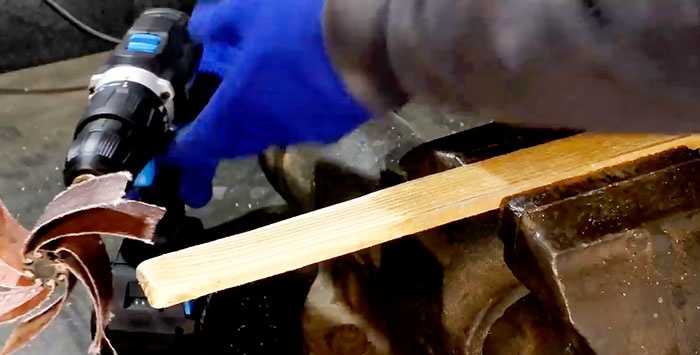
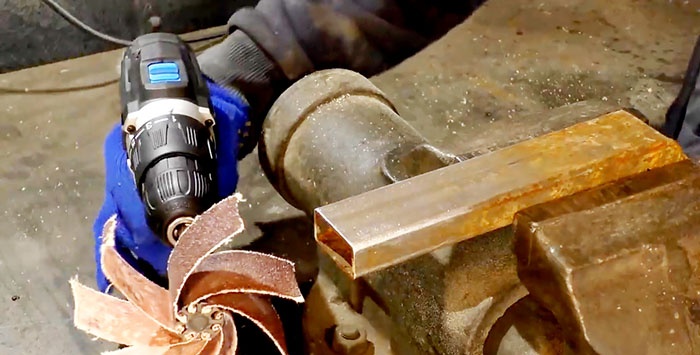
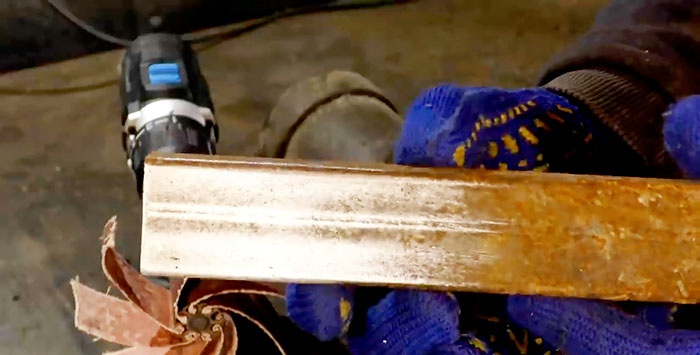
A homemade nozzle can be used in a slightly different way. Take a piece of sandpaper equal in length to the circumference of the nozzle and bend its ends at an angle. We wrap it around the nozzle, and tuck the bent and closed ends into the groove.
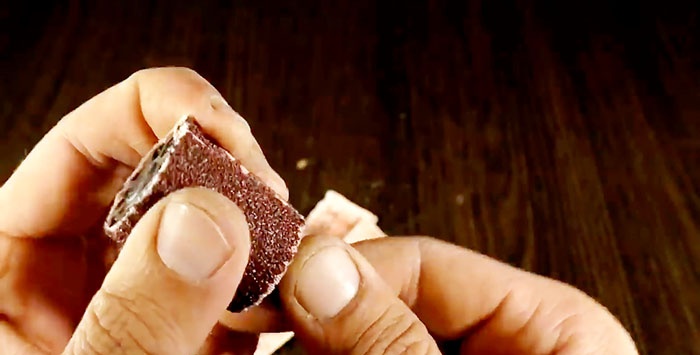
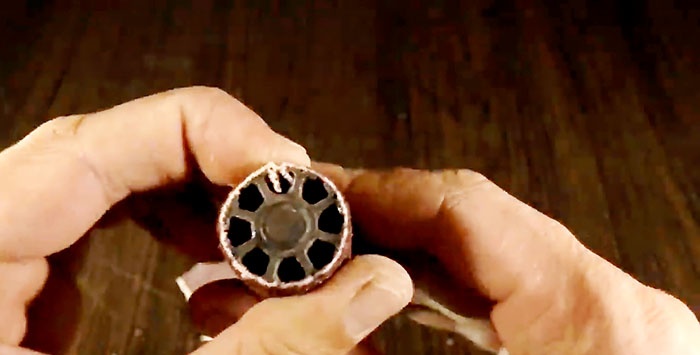
This version of the nozzle is able to easily and quickly make cylindrical recesses in wooden and metal workpieces.
Both versions of the tool allow you to bore, grind and polish various surfaces and holes.
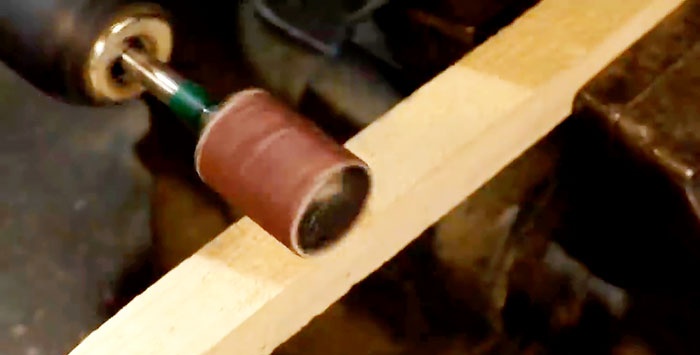
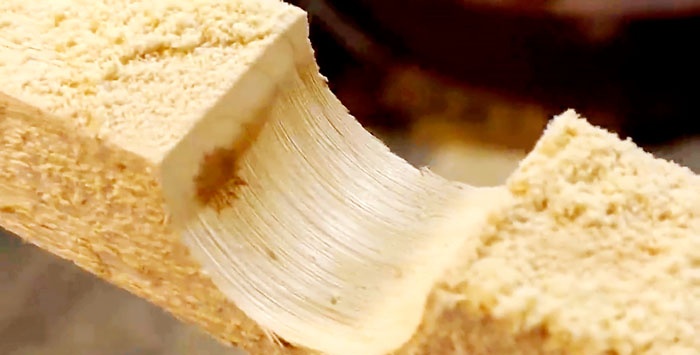
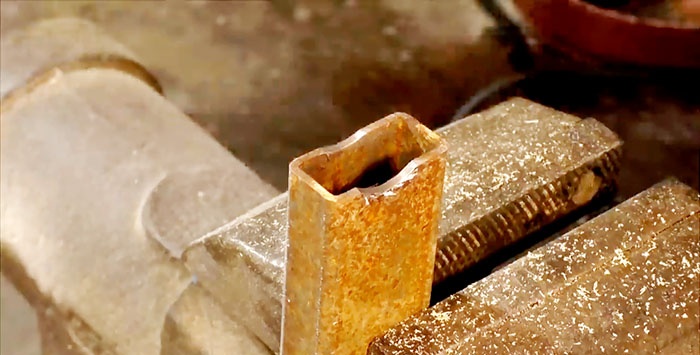
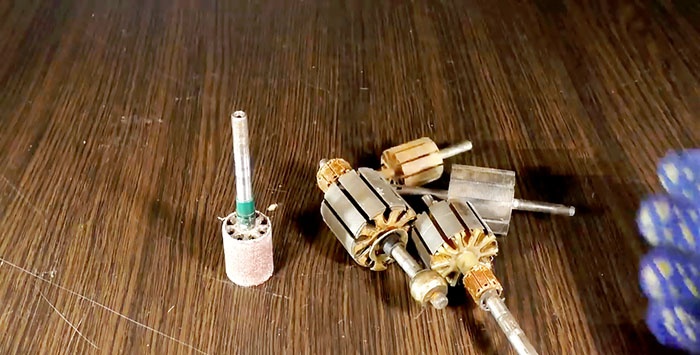

Will need
In addition to the scarce anchor, which can be removed from a burnt drill, grinder, etc. or can be easily found at a metal collection point, we must have:
- bench vice;
- bearing puller;
- hacksaw for metal;
- gas burner or electric oven;
- flat screwdriver;
- pliers;
- sandpaper of different grits.
Technology for converting an anchor into a tool
This is not at all difficult to do, even with basic plumbing skills. We remove all removable parts from the anchor - nuts, rings, gears, bearings, using a puller, hammer and pliers.
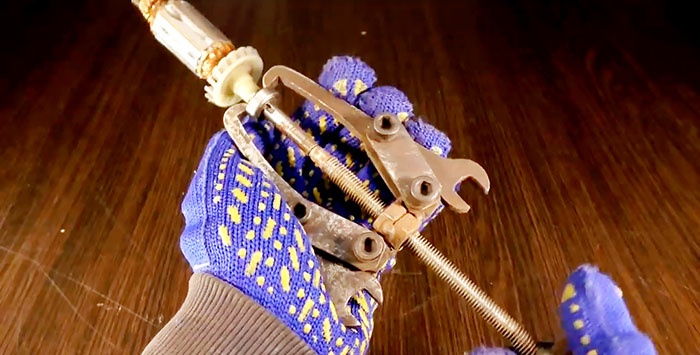
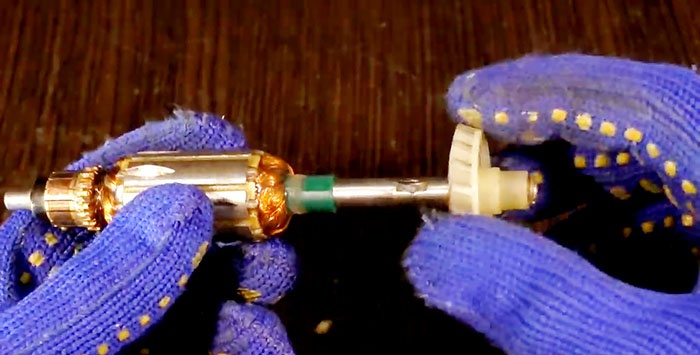
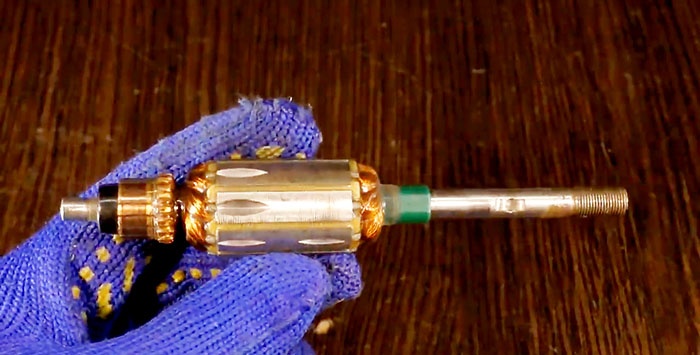
Using a hacksaw for metal, we cut off the part of the armature on which the contact plates of the brush assembly are located, making a cut strictly along the end of the magnetic circuit, having previously secured the rotor in the jaws of a bench vice.
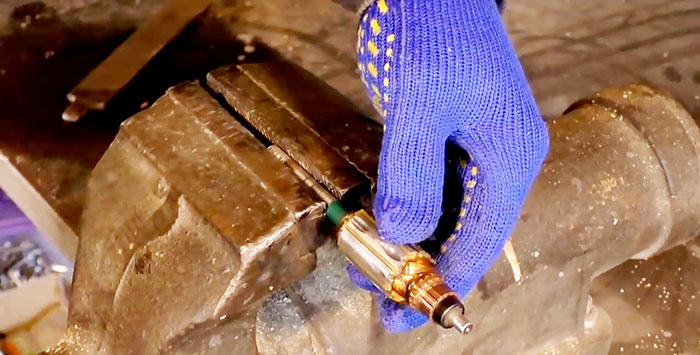
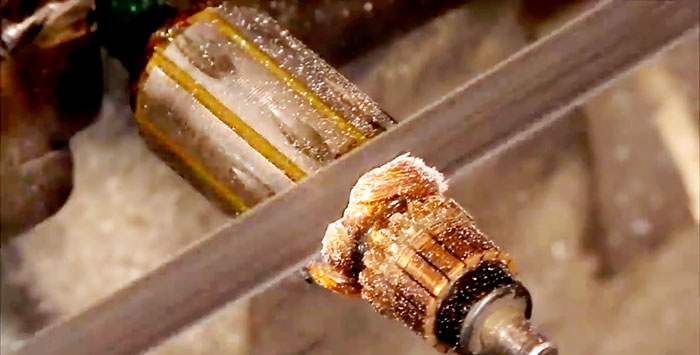
We remove the copper armature winding from the magnetic circuit. To do this, we fix it vertically to the shaft in a vice and, using a gas burner, heat and evaporate the varnish of the armature winding.
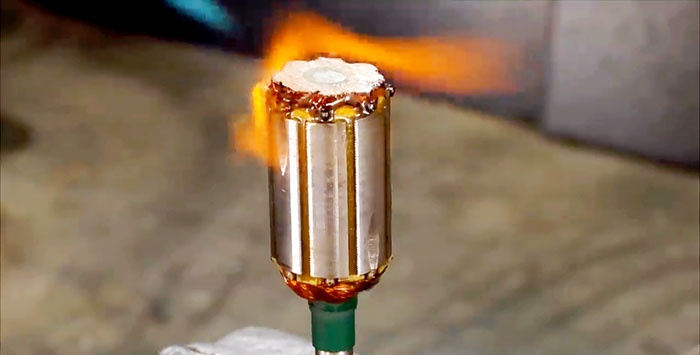
You can heat the rotor in one place. Since copper is an excellent conductor of not only electricity, but also heat, it will quickly spread throughout the entire winding and melt the electrical insulating varnish.
As soon as the varnish boils and begins to drip on the other side of the armature, you can finish heating and begin removing the winding by picking it out with a screwdriver and pulling it out of the grooves of the magnetic circuit with pliers. If the process becomes difficult, you can again slightly warm up the winding with the flame of a gas burner.
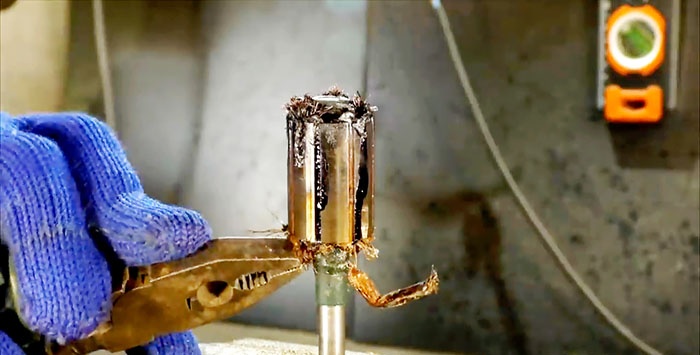
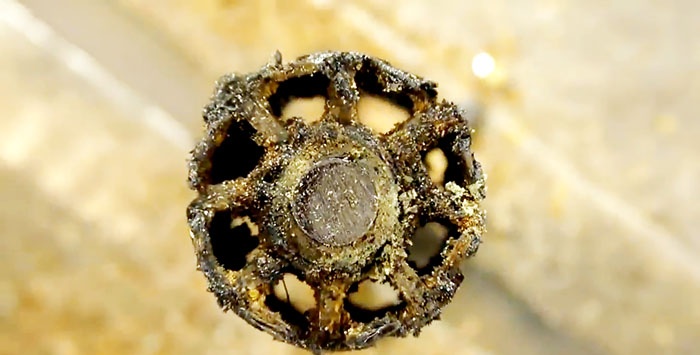
After removing the entire winding from the magnetic circuit, a system of through holes and grooves opens, which were previously filled with copper windings and filled with varnish.
Using available means, we clean the magnetic circuit from carbon deposits and residues of electrical insulating varnish.
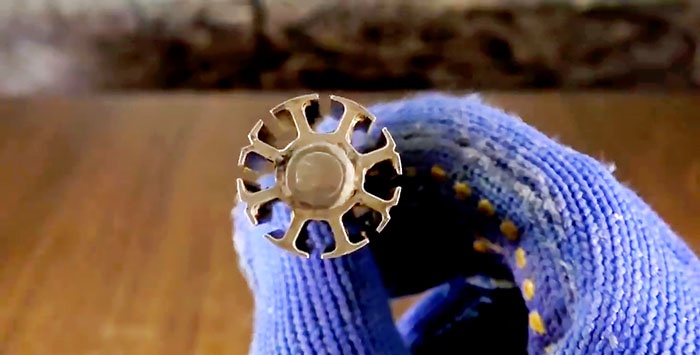
All we have to do is equip the magnetic core nozzle with pieces of sandpaper of the same length, which are very simply and securely attached to the grooves.
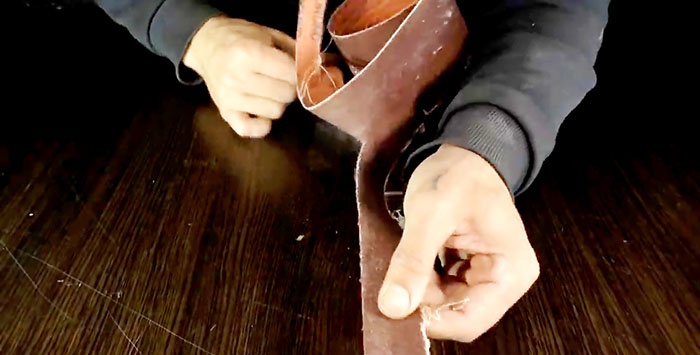
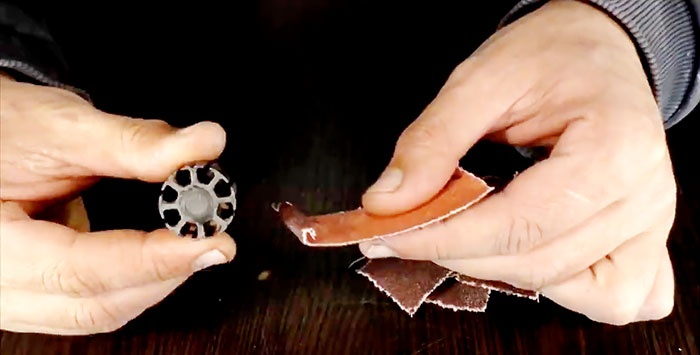
The result is a very effective abrasive tool, which, depending on the number of sanding tape, can perform certain operations.
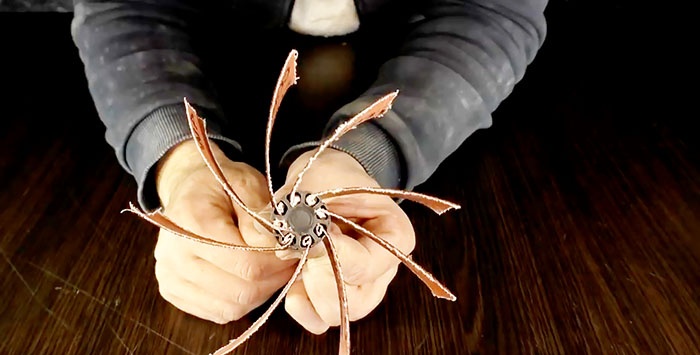
Practical use
Let's check our homemade abrasive tool in action.
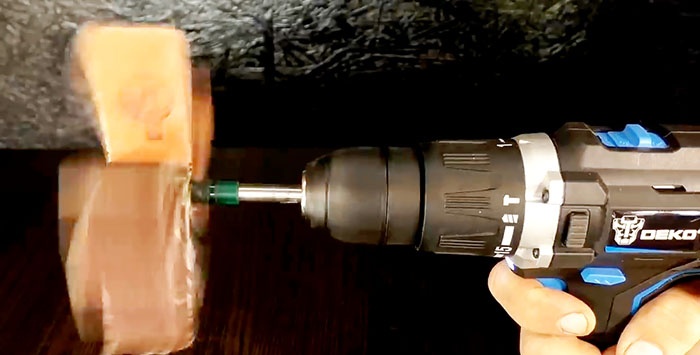
To do this, we fix the shaft of the former anchor, which now serves as a shank, into the drill chuck, and grind the surface of the wooden and metal workpiece.The result is excellent and the process is efficient.
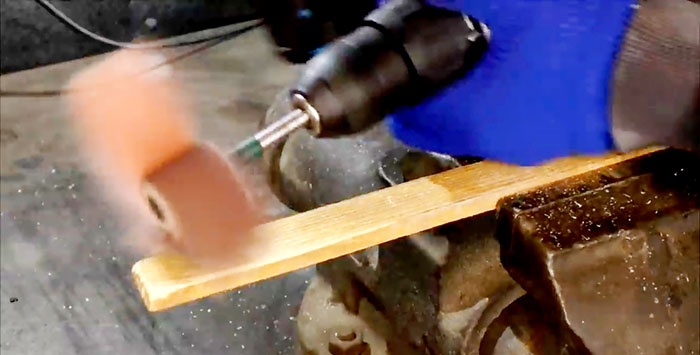
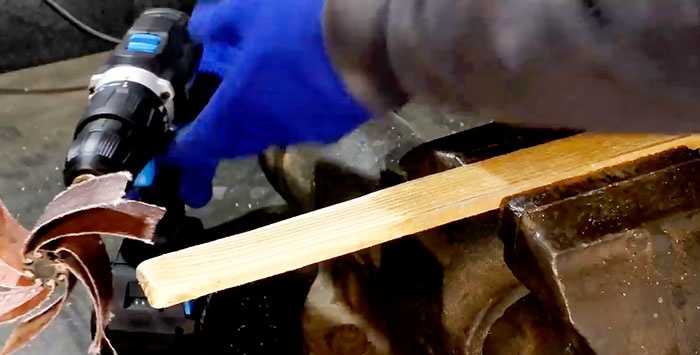
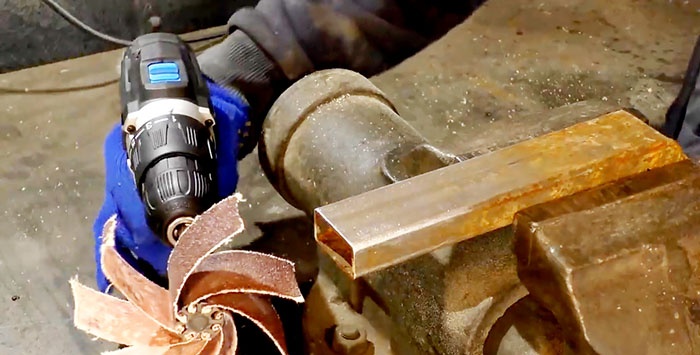
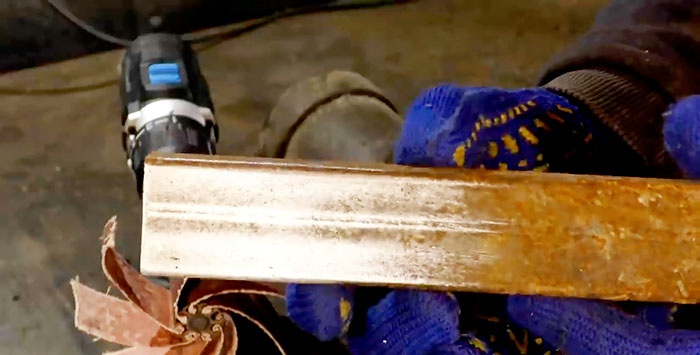
A homemade nozzle can be used in a slightly different way. Take a piece of sandpaper equal in length to the circumference of the nozzle and bend its ends at an angle. We wrap it around the nozzle, and tuck the bent and closed ends into the groove.
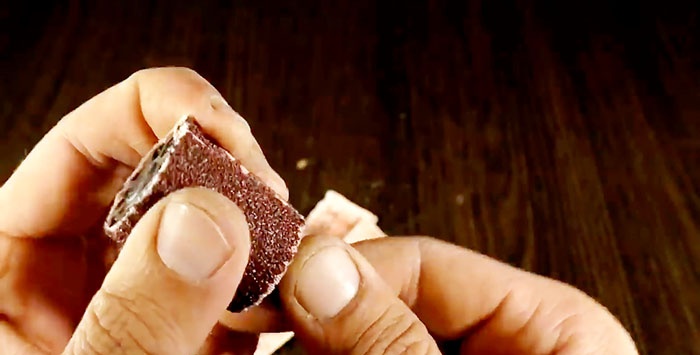
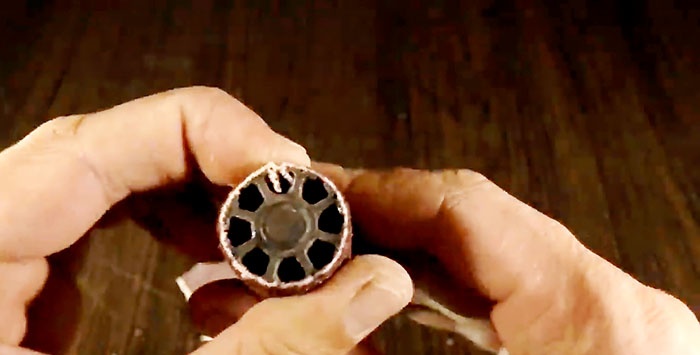
This version of the nozzle is able to easily and quickly make cylindrical recesses in wooden and metal workpieces.
Both versions of the tool allow you to bore, grind and polish various surfaces and holes.
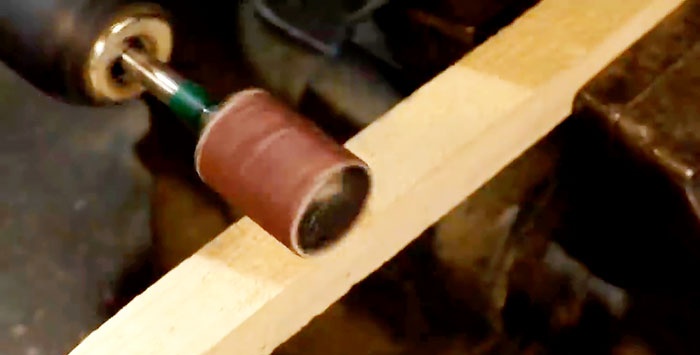
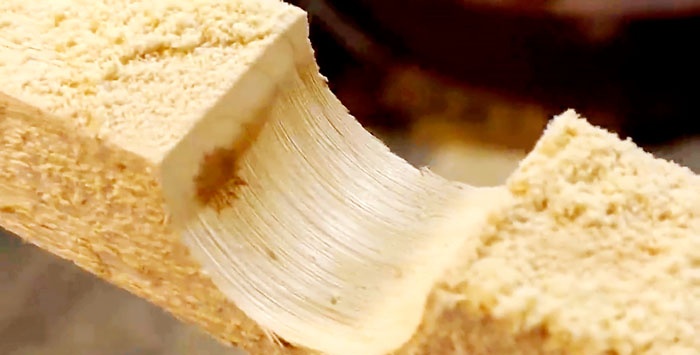
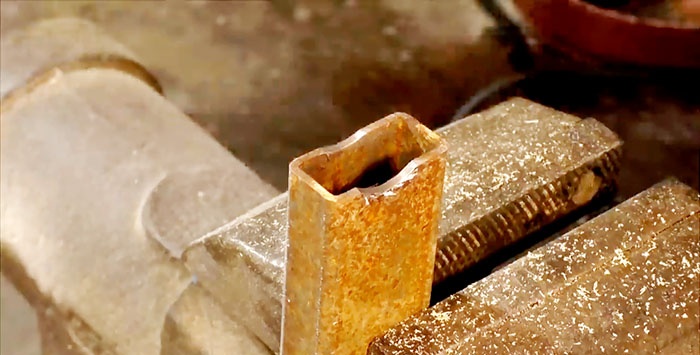
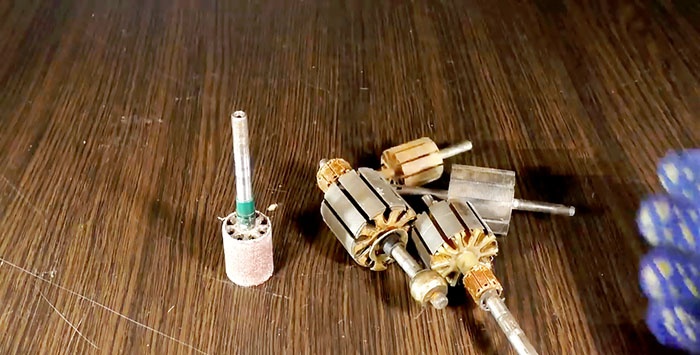
Watch the video
Similar master classes
Particularly interesting
Comments (1)