Connecting the washing machine motor, reverse and speed controller
In washing machines, the automatics most often fail, followed by bearings and rubber products. The engine is the most reliable component; it is used in the manufacture of various home machines. But for this you need to be able to change the direction of rotation and regulate the speed.
Carefully inspect the terminal blocks of the removed motor. It has six terminals: two contacts go to the speed sensor (tachometer) and two contacts each from the rotor and stator windings.
We don’t need a tachometer, we don’t touch it, we only need to connect the engine.
All single-phase motors of this type are connected in the same way. The output of the stator winding must be connected to the input of the rotor winding. The remaining two ends are connected to zero and phase. It makes no difference which winding will be the first and which will be the second.
Identify the winding outputs on the connector. You need to use a tester, keep one contact constantly on the terminal, and apply the second one in turn to the others. If the device shows a short circuit, then two terminals are connected to one winding.
In our case, the bottom and second from the top contacts are connected to one winding, and the second terminal is connected to the bottom and the third from the top. Accordingly, we need to connect the second and third upper contacts with a jumper. Make a jumper and make the connection. To guarantee, ring again, now your short should show between the two remaining terminals.
Connect a voltage of 220 V to the remaining two, if everything is normal, the engine will begin to rotate.
As mentioned above, to change the direction of rotation it is necessary to swap the connections of one of the windings with each other.
And the engine will begin to rotate in the other direction. Check the connection is correct, swap the wires on the terminal block according to the diagram described, and turn on the voltage. The direction of rotation of the motor should be reversed.
The contact to which the phase was supplied must be connected to the input of the second winding. The voltage reaches the free terminal, the zero position does not change. Changing the connection order can be done by clicking a toggle switch.
Turn the toggle switch upside down, on the bottom there are designations for each output and a diagram of their connection in the left and right positions of the switch.
To make it easier to understand, draw a basic connection diagram: two windings and two switch contacts. The middle contacts are connected/detached in turn to the two side ones. The connection is elementary.
Connect one winding to the bottommost contact and connect it with a jumper to the topmost one. Connect the second winding to the middle terminal, let the stator winding be connected in this way in our example.
Now it's time to connect the rotor. One contact of the toggle switch should be connected to the output of the rotor winding, and the second directly to the neutral power wire.
If everything is clear, then proceed to the connection. Make diagonal jumpers between the outer terminals. One middle terminal of the toggle switch is connected to zero, and the second to the second winding.
Connect all the wires and double check that the diagram is correct. Middle contacts: one to the power supply zero, the other to the stator winding. The second end of this winding is connected directly to the power phase (brown wire).
The diagonal contacts must have jumpers, the wires from them go to the second winding (rotor). Before turning on, be sure to check with a tester the changes in the short circuit when switching the toggle switch.
Carefully insulate the contacts and check the functionality of the motor. When switching, the direction of rotation must change. It is strictly forbidden to change the direction of movement until the rotor comes to a complete stop.
If you bought inexpensive Chinese products, then you should definitely check the device. Remove the filling from the case and pay attention to the triac.At best, it has a very small heatsink that cannot effectively remove heat. In the worst case, there is nothing at all.
Cut an M3 thread on the new radiator and adjust its length to the dimensions of the case. Spread the surface of the triac with thermal paste and secure the prepared radiator. Assemble the regulator.
Inspect the device. On the back of the case there is a strip with connectors and a plug with terminals. Every contact is signed.
Find zero, phase and ground at the input (if you have grounding in your house). Power is connected to them, in our case zero and phase (there is no ground).
Now you need to find the zero and phase output from the regulator. The cover should contain a detailed diagram indicating the purpose of each output wire and its color.
On the purchased regulator, yellow is for ground, two blue ones are for the tachometer sensor, and red is for phase. White and green are interchangeable, but to do this you need to change the position of the jumper. In our case, green is involved. The connection is determined by calling the terminals with the tester.
Connect the blue wires to the tachometer on the motor terminal block. In the example, a zero (green) is connected to the middle terminal of the toggle switch, and a phase (brown) is connected to the free contact of the winding. The yellow wires on the terminal block are connected to the tachometer. Apply voltage to the speed controller and check the engine operation in all modes and speeds.
On the body of the device there is a special hole for adjusting the rotation modes with a variable resistor. With its help, the speed change step is changed, the rotation of the rotor will not start with a jerk, but almost from zero. Set the desired modes.
Any electrical installation work should be done in strict accordance with the PUE.If you cannot decipher these three letters without the help of the Internet, then you should not risk your health.
What is needed
- Toggle switch with two groups of contacts 220 V 15 A, you can purchase it at Ali Express.
- Speed controller 400 W 220 V 50 Hz, also take on Ali Express.
- An electric motor from an automatic washing machine will suit almost any brand.
- Pieces of wires of different colors, preferably blue (zero) and brown (phase).
- You will need electrical tape; to install a powerful radiator, buy a new one and a tube of heat-conducting paste.
- To check the connection diagram, it is recommended to use an ordinary tester or at least an indicator.
Motor connection
Carefully inspect the terminal blocks of the removed motor. It has six terminals: two contacts go to the speed sensor (tachometer) and two contacts each from the rotor and stator windings.
We don’t need a tachometer, we don’t touch it, we only need to connect the engine.
All single-phase motors of this type are connected in the same way. The output of the stator winding must be connected to the input of the rotor winding. The remaining two ends are connected to zero and phase. It makes no difference which winding will be the first and which will be the second.
Identify the winding outputs on the connector. You need to use a tester, keep one contact constantly on the terminal, and apply the second one in turn to the others. If the device shows a short circuit, then two terminals are connected to one winding.
In our case, the bottom and second from the top contacts are connected to one winding, and the second terminal is connected to the bottom and the third from the top. Accordingly, we need to connect the second and third upper contacts with a jumper. Make a jumper and make the connection. To guarantee, ring again, now your short should show between the two remaining terminals.
Connect a voltage of 220 V to the remaining two, if everything is normal, the engine will begin to rotate.
Reverse connection
As mentioned above, to change the direction of rotation it is necessary to swap the connections of one of the windings with each other.
And the engine will begin to rotate in the other direction. Check the connection is correct, swap the wires on the terminal block according to the diagram described, and turn on the voltage. The direction of rotation of the motor should be reversed.
The contact to which the phase was supplied must be connected to the input of the second winding. The voltage reaches the free terminal, the zero position does not change. Changing the connection order can be done by clicking a toggle switch.
Turn the toggle switch upside down, on the bottom there are designations for each output and a diagram of their connection in the left and right positions of the switch.
To make it easier to understand, draw a basic connection diagram: two windings and two switch contacts. The middle contacts are connected/detached in turn to the two side ones. The connection is elementary.
Connect one winding to the bottommost contact and connect it with a jumper to the topmost one. Connect the second winding to the middle terminal, let the stator winding be connected in this way in our example.
Now it's time to connect the rotor. One contact of the toggle switch should be connected to the output of the rotor winding, and the second directly to the neutral power wire.
If everything is clear, then proceed to the connection. Make diagonal jumpers between the outer terminals. One middle terminal of the toggle switch is connected to zero, and the second to the second winding.
Connect all the wires and double check that the diagram is correct. Middle contacts: one to the power supply zero, the other to the stator winding. The second end of this winding is connected directly to the power phase (brown wire).
The diagonal contacts must have jumpers, the wires from them go to the second winding (rotor). Before turning on, be sure to check with a tester the changes in the short circuit when switching the toggle switch.
Carefully insulate the contacts and check the functionality of the motor. When switching, the direction of rotation must change. It is strictly forbidden to change the direction of movement until the rotor comes to a complete stop.
Speed controller, my modification
If you bought inexpensive Chinese products, then you should definitely check the device. Remove the filling from the case and pay attention to the triac.At best, it has a very small heatsink that cannot effectively remove heat. In the worst case, there is nothing at all.
Cut an M3 thread on the new radiator and adjust its length to the dimensions of the case. Spread the surface of the triac with thermal paste and secure the prepared radiator. Assemble the regulator.
Connect the regulator
Inspect the device. On the back of the case there is a strip with connectors and a plug with terminals. Every contact is signed.
Find zero, phase and ground at the input (if you have grounding in your house). Power is connected to them, in our case zero and phase (there is no ground).
Now you need to find the zero and phase output from the regulator. The cover should contain a detailed diagram indicating the purpose of each output wire and its color.
On the purchased regulator, yellow is for ground, two blue ones are for the tachometer sensor, and red is for phase. White and green are interchangeable, but to do this you need to change the position of the jumper. In our case, green is involved. The connection is determined by calling the terminals with the tester.
Connect the blue wires to the tachometer on the motor terminal block. In the example, a zero (green) is connected to the middle terminal of the toggle switch, and a phase (brown) is connected to the free contact of the winding. The yellow wires on the terminal block are connected to the tachometer. Apply voltage to the speed controller and check the engine operation in all modes and speeds.
On the body of the device there is a special hole for adjusting the rotation modes with a variable resistor. With its help, the speed change step is changed, the rotation of the rotor will not start with a jerk, but almost from zero. Set the desired modes.
Conclusion
Any electrical installation work should be done in strict accordance with the PUE.If you cannot decipher these three letters without the help of the Internet, then you should not risk your health.
Watch the video
Similar master classes
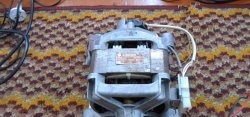
How to connect the motor from a washing machine to 220 V
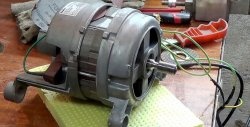
Powerful cutter from a washing machine engine
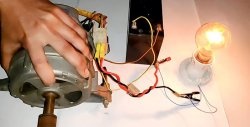
How to turn a washing machine motor into a 220 V generator
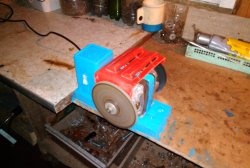
Sharpener from a washing machine engine
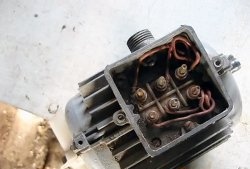
Connecting a three-phase motor according to a star and delta circuit
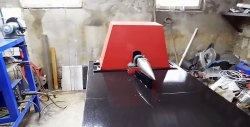
Wood splitter from an old flywheel and washing machine engine
Particularly interesting
Comments (6)