How to make sharp bends on a tube without a pipe bender so it doesn't get crushed
It is extremely difficult to make a sharp bend in a thin-walled copper tube with a small turning radius, especially if it is important not to deform its cross-section. And if the pipe needs to be wound into a coil, then even a pipe bender will not help. In this case, you can use one simple but painstaking method that allows you to make a high-quality bend without disturbing the patency of the tube.
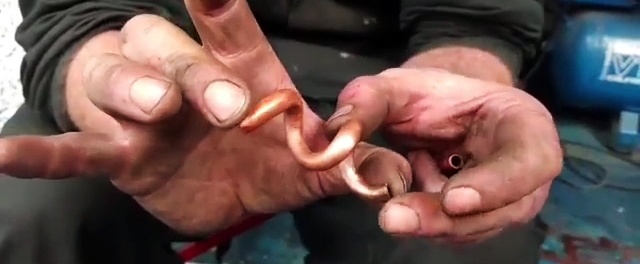
One end of the tube must be plugged by splashing it with a hammer or squeezing it with pliers. After this, a crucible is taken and solder is melted in it in such an amount as to completely fill the internal cavity of the tube at the bend. You can melt with a regular gas burner. Solder should be heated above its melting point so that it remains liquid longer.
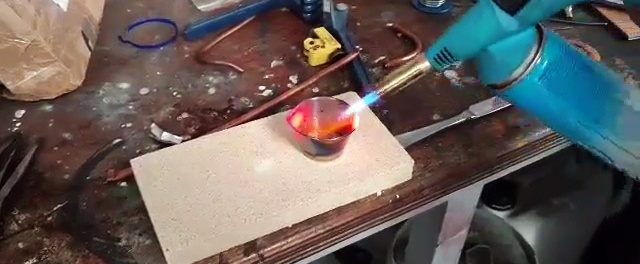
Molten solder is poured into a dry tube. Most likely you will have to pour in several passes.For convenience, you can bend a funnel made of tin from a tin can to make it easier to stream into the pipe.
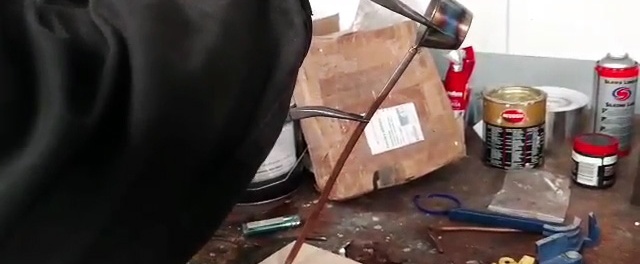
After the tin hardens, the pipe can be bent. This is done around a rod of the required diameter. The pipe simply rests on it and bends. If you need to bend from the very edge, then it can be pressed against the rod using a hand clamp.
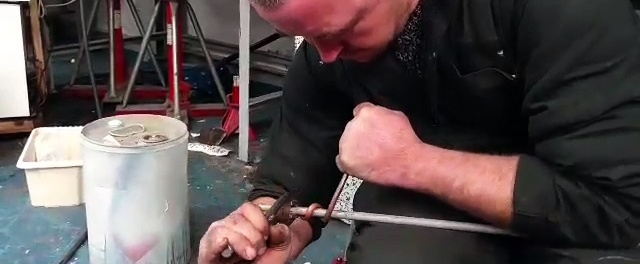
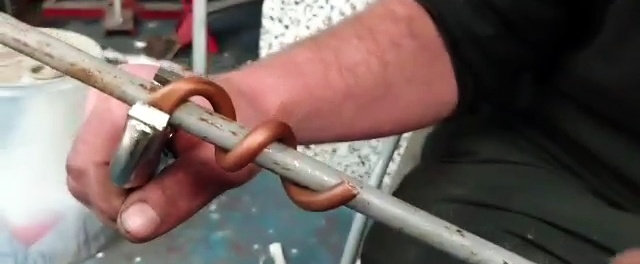
Upon completion of the bend, the tube is turned over with the open end down and heated with a burner. When it warms up, all the solder will completely flow back. To be sure there is nothing left inside, you can weigh the tube before bending and after draining the solder. If the weight turns out to be the same, then the solder stack is complete.
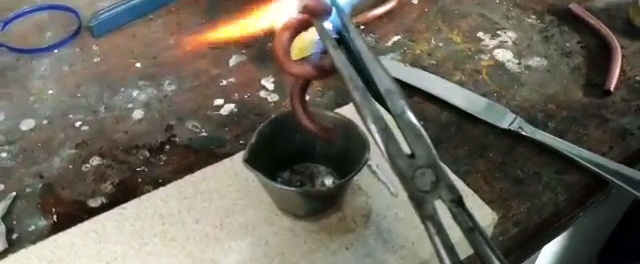
If it is necessary to make a very complex bend, for example, to wind a coil, then the tube, even with solder inside, can break. To prevent this from happening, it must first be annealed. To do this, it heats up red hot. For copper this is +600 degrees Celsius. The hot pipe must be cooled sharply in water. Annealing is conveniently done in a forge. In order for the pipe to fit into it, it can be laid inside in a coiled coil. The annealed tube bends very easily, and thanks to the solder inside it does not deform. In order to later restore the rigidity of the made coil, the copper is heated again, but is left to cool in the air. Hardening does not need to be done, since the annealed copper tube will become harder on its own over time.
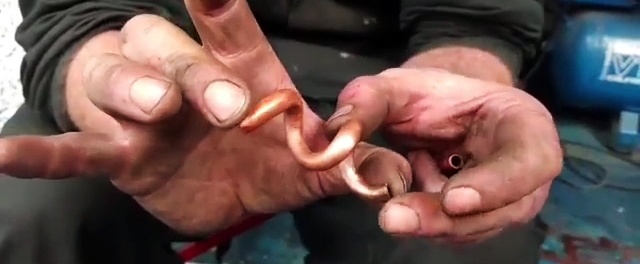
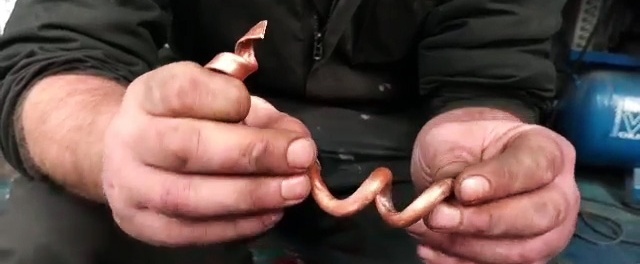
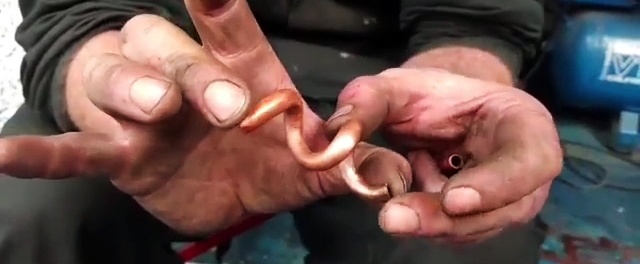
What you will need:
- soldering solder;
- crucible with a convenient spout;
- gas-burner;
- clamping pliers;
- steel rod
Copper tube bending process
One end of the tube must be plugged by splashing it with a hammer or squeezing it with pliers. After this, a crucible is taken and solder is melted in it in such an amount as to completely fill the internal cavity of the tube at the bend. You can melt with a regular gas burner. Solder should be heated above its melting point so that it remains liquid longer.
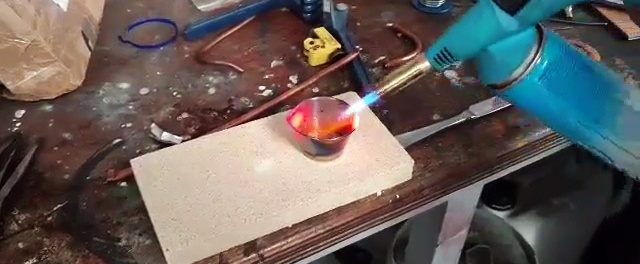
Molten solder is poured into a dry tube. Most likely you will have to pour in several passes.For convenience, you can bend a funnel made of tin from a tin can to make it easier to stream into the pipe.
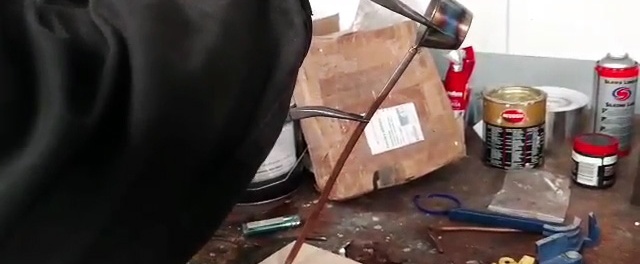
After the tin hardens, the pipe can be bent. This is done around a rod of the required diameter. The pipe simply rests on it and bends. If you need to bend from the very edge, then it can be pressed against the rod using a hand clamp.
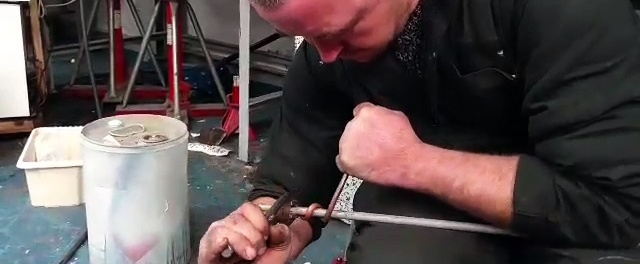
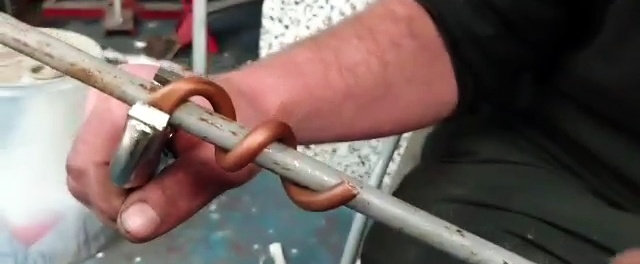
Upon completion of the bend, the tube is turned over with the open end down and heated with a burner. When it warms up, all the solder will completely flow back. To be sure there is nothing left inside, you can weigh the tube before bending and after draining the solder. If the weight turns out to be the same, then the solder stack is complete.
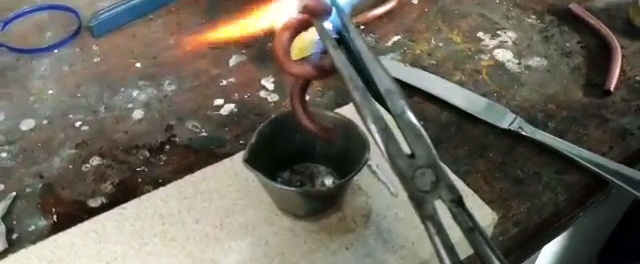
If it is necessary to make a very complex bend, for example, to wind a coil, then the tube, even with solder inside, can break. To prevent this from happening, it must first be annealed. To do this, it heats up red hot. For copper this is +600 degrees Celsius. The hot pipe must be cooled sharply in water. Annealing is conveniently done in a forge. In order for the pipe to fit into it, it can be laid inside in a coiled coil. The annealed tube bends very easily, and thanks to the solder inside it does not deform. In order to later restore the rigidity of the made coil, the copper is heated again, but is left to cool in the air. Hardening does not need to be done, since the annealed copper tube will become harder on its own over time.
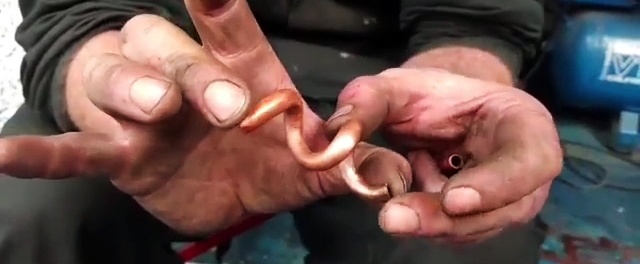
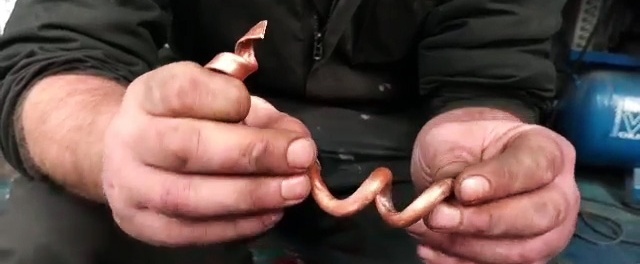
Watch the video
Similar master classes
Particularly interesting
Comments (2)