Anyone can make such a knife from PP pipes.
To sharpen a knife to razor sharpness, sharpeners are used that allow the blade to be brought out strictly at one fixed angle. Their use, even by a person without experience, guarantees that the knife will be perfectly sharp after sharpening. You can make such a device with your own hands from scraps of polypropylene pipes.
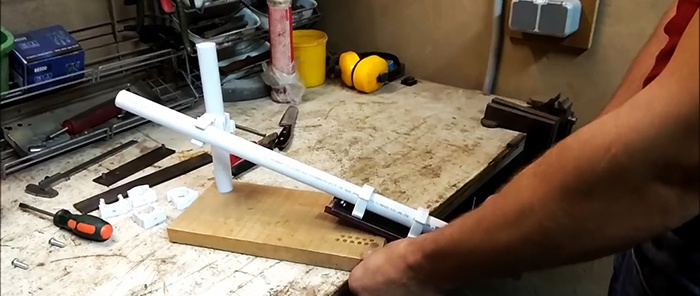
The first step is to make the base and stand of the sharpener. As a sole, you can use a small piece of board of sufficient size. A hole with a diameter of 25 mm is drilled in it near one of the corners, and a tube 25-30 cm long is pressed into it.
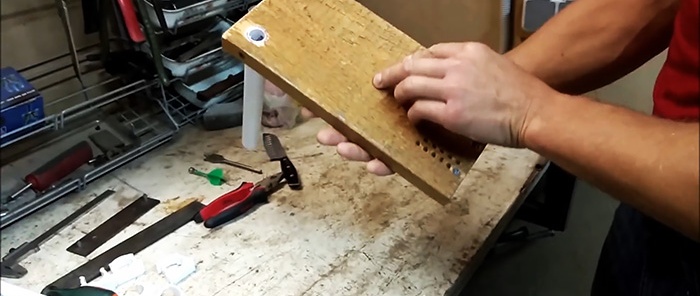
For reliability, it must be secured with self-tapping screws. They are screwed from the end and edge of the board opposite the hole so as to fit into the tube.
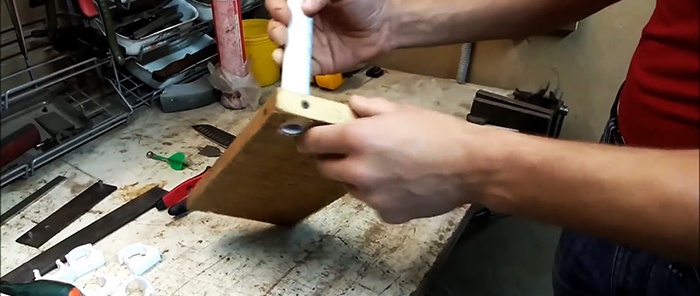
On the part of the board opposite the rack, closer to the edge, neodymium magnets are glued or screwed in. They are necessary to fix the knife blade. Holes are drilled in the board in several rows using a 6 mm drill.They are located from the magnets towards the rack. The holes will later be needed to support the knife. To do this, 2 M6 bolts will be inserted into them.
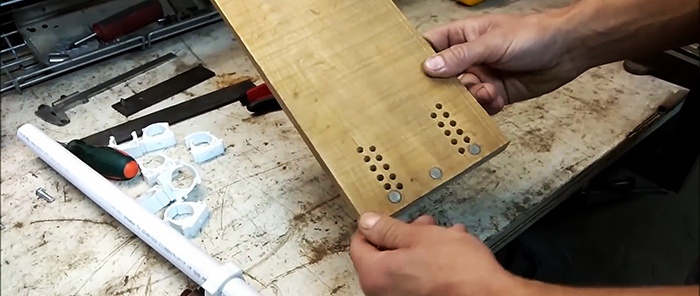
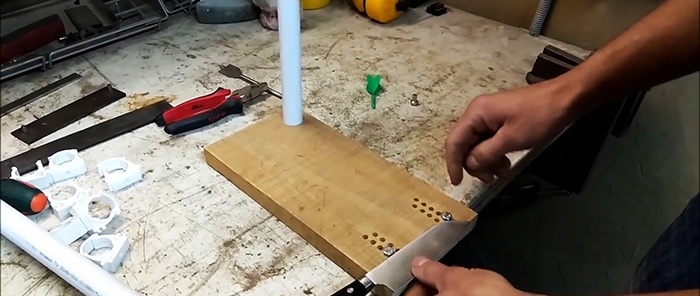
Next, you need to connect together 2 clips with and without a latch. To do this, they are twisted with flat surfaces towards each other using an M6 bolt. When screwed in, it will cut threads into them.
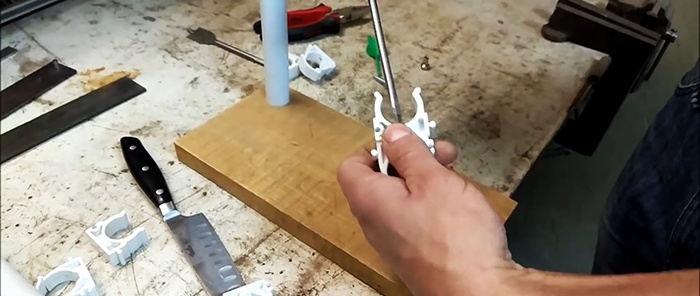
After this, one clip with a clamp is fixed to the stand. Spliced clips are placed on top of the tube. Fixation is performed by the one with the latch.
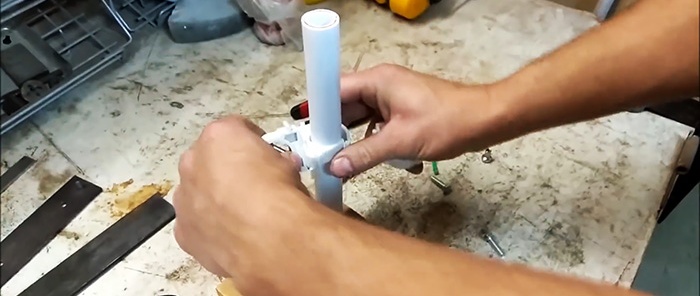
Next, a device is made to hold the sandpaper. For it, 2 metal plates are cut from the strip (they may not be metal). 2 clips with latches are screwed to one. After this, the plates are twisted together using 2 countersunk screws.
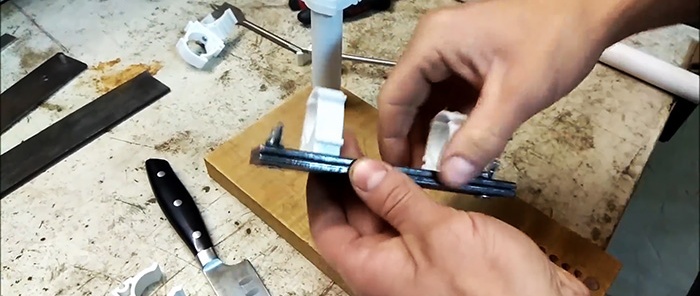
To do this, the holes in the bottom plate without clips need to be countersinked. IN
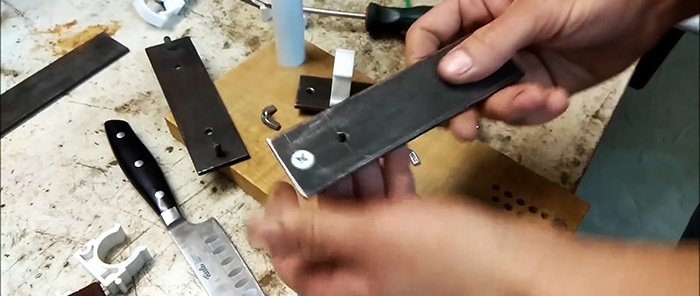
the screws are tightened with wing nuts. Now, releasing the wings, you can tuck the edges of sandpaper between the plates, placed under the plane of the bottom of them.
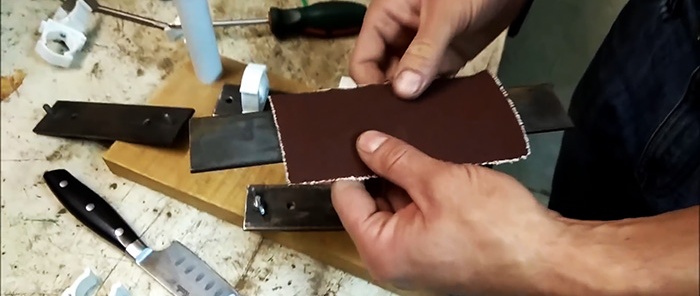
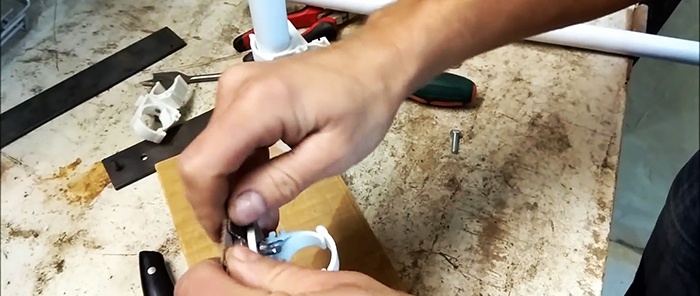
The tube is then snapped onto the plate clips. After this, it is inserted into the open double clip on the stand.
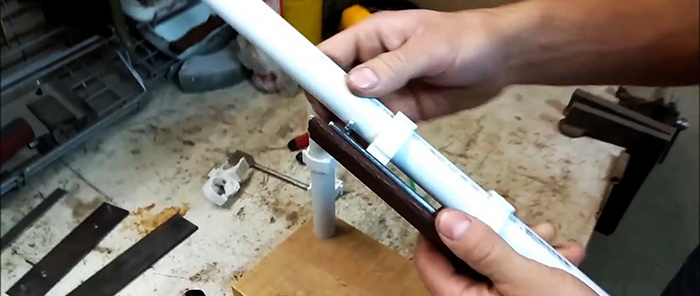
To use the sharpener, you need to place the knife on the neodymium magnets with the tip away from the stand. To support it, bolts are inserted into the nearest holes on the board. Then you should set the desired angle of attack of the sandpaper to the tip. This is done by changing the height of the support clips on the stand. After this, the knife is sharpened with reciprocating movements, first with coarse sandpaper, then with finer sandpaper. For better sliding of the tube in the clip, it can be lubricated.
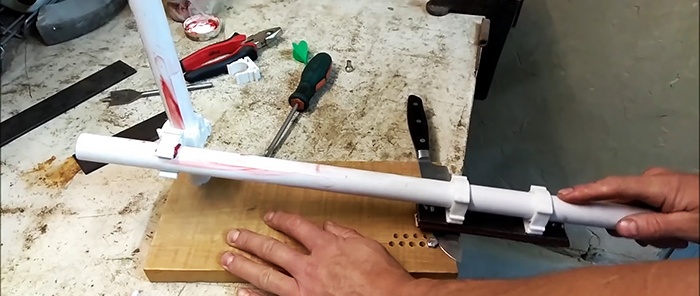
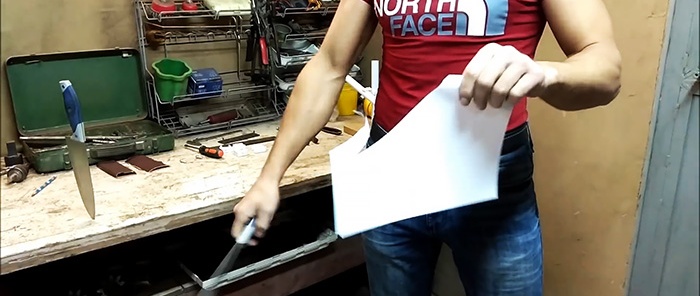
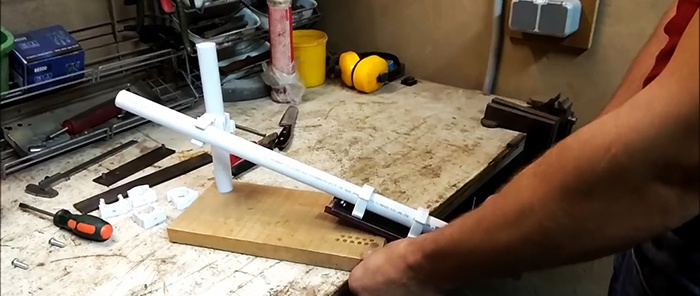
Materials:
- board;
- polypropylene pipe 25 mm;
- Neodymium magnets;
- clips for pipes 25 mm with a latch – 4 pcs.;
- clip for pipes 25 mm open – 1 pc.;
- self-tapping screws, screws, bolts, nuts;
- steel strip 60 mm.
Sharpener manufacturing process
The first step is to make the base and stand of the sharpener. As a sole, you can use a small piece of board of sufficient size. A hole with a diameter of 25 mm is drilled in it near one of the corners, and a tube 25-30 cm long is pressed into it.
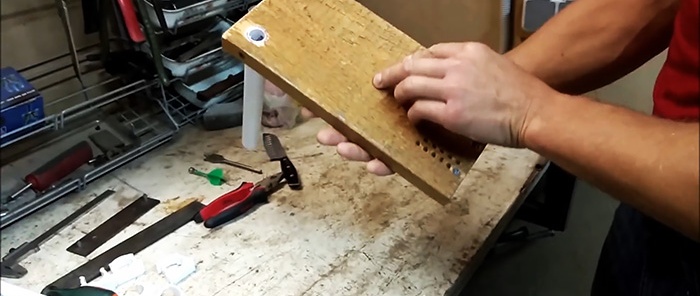
For reliability, it must be secured with self-tapping screws. They are screwed from the end and edge of the board opposite the hole so as to fit into the tube.
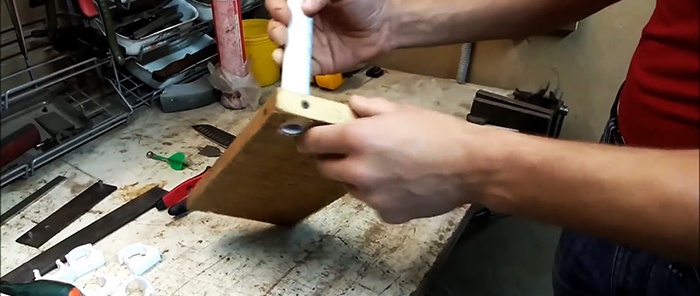
On the part of the board opposite the rack, closer to the edge, neodymium magnets are glued or screwed in. They are necessary to fix the knife blade. Holes are drilled in the board in several rows using a 6 mm drill.They are located from the magnets towards the rack. The holes will later be needed to support the knife. To do this, 2 M6 bolts will be inserted into them.
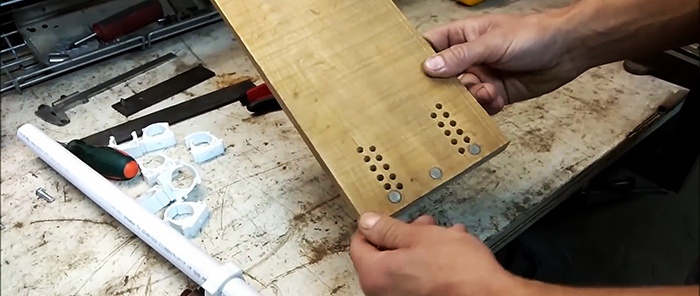
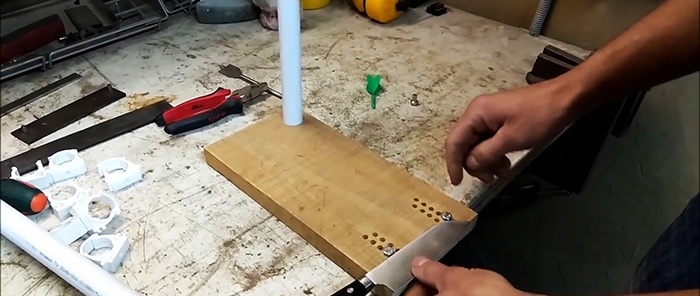
Next, you need to connect together 2 clips with and without a latch. To do this, they are twisted with flat surfaces towards each other using an M6 bolt. When screwed in, it will cut threads into them.
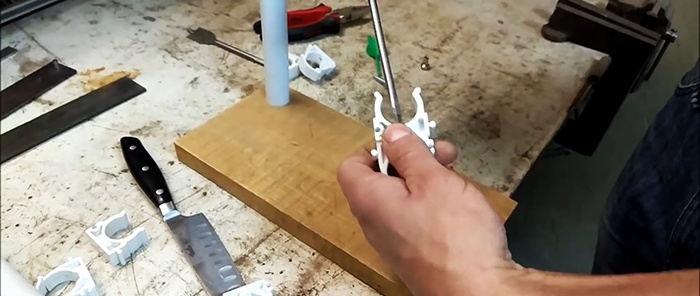
After this, one clip with a clamp is fixed to the stand. Spliced clips are placed on top of the tube. Fixation is performed by the one with the latch.
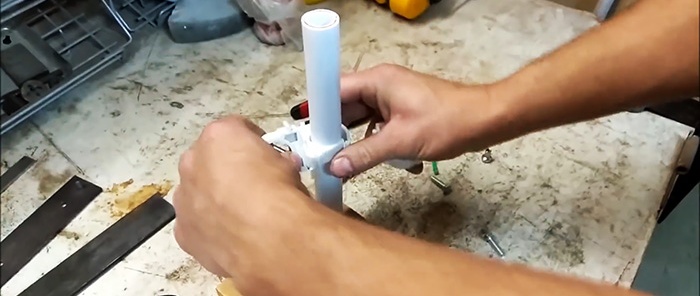
Next, a device is made to hold the sandpaper. For it, 2 metal plates are cut from the strip (they may not be metal). 2 clips with latches are screwed to one. After this, the plates are twisted together using 2 countersunk screws.
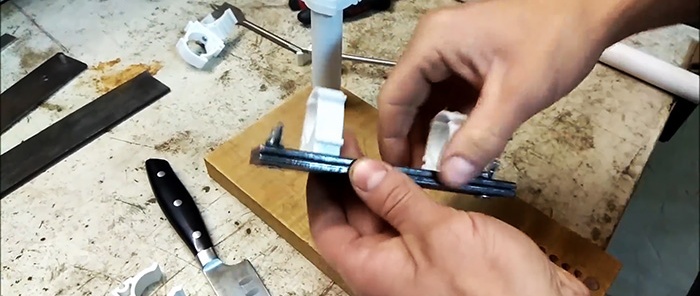
To do this, the holes in the bottom plate without clips need to be countersinked. IN
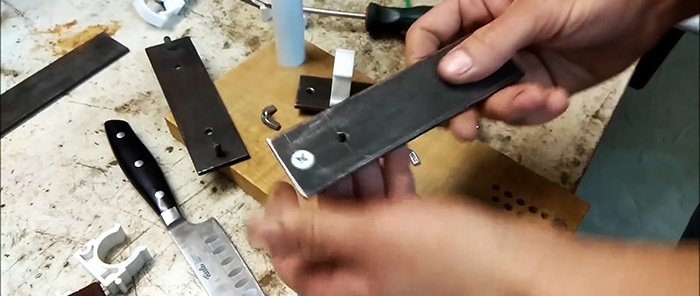
the screws are tightened with wing nuts. Now, releasing the wings, you can tuck the edges of sandpaper between the plates, placed under the plane of the bottom of them.
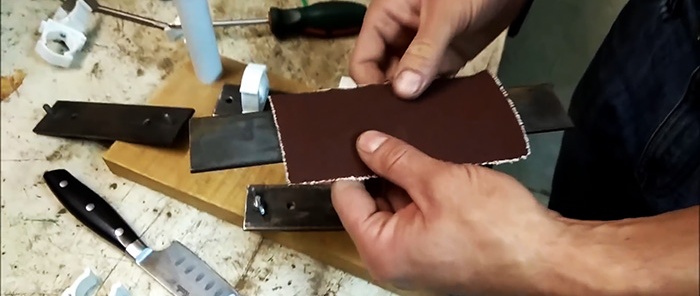
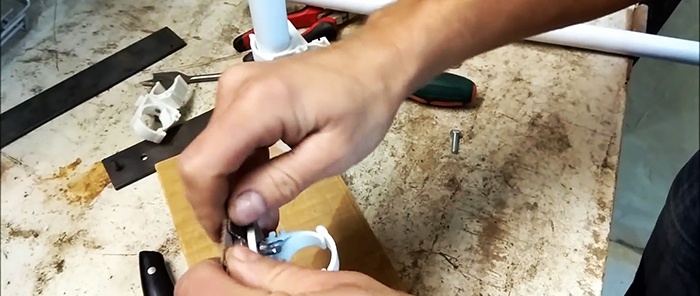
The tube is then snapped onto the plate clips. After this, it is inserted into the open double clip on the stand.
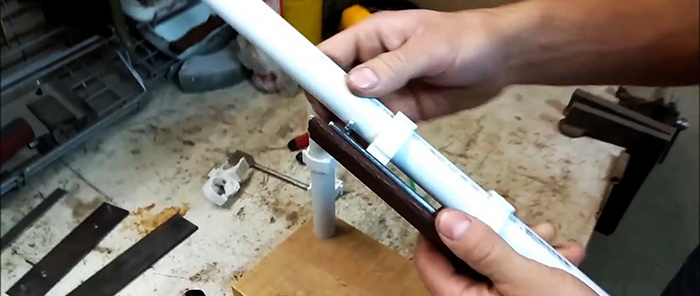
To use the sharpener, you need to place the knife on the neodymium magnets with the tip away from the stand. To support it, bolts are inserted into the nearest holes on the board. Then you should set the desired angle of attack of the sandpaper to the tip. This is done by changing the height of the support clips on the stand. After this, the knife is sharpened with reciprocating movements, first with coarse sandpaper, then with finer sandpaper. For better sliding of the tube in the clip, it can be lubricated.
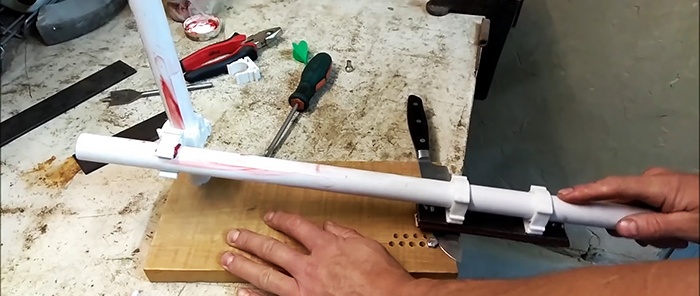
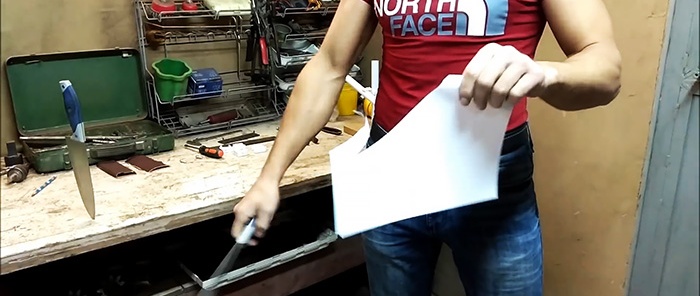
Watch the video
Similar master classes
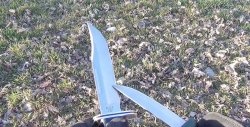
5 ways to sharpen a knife without a sharpener while traveling
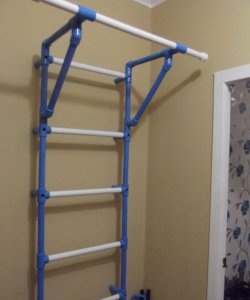
Gymnastic wall bars made of polypropylene pipes
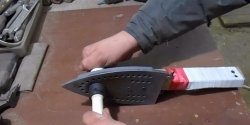
Soldering iron for polypropylene iron pipes
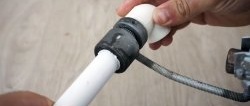
No electricity needed! Simple gas soldering iron for welding
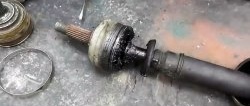
Homemade dismountable swing from old auto parts and pipes
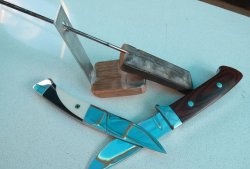
A simple tool for sharpening knives at a fixed angle
Particularly interesting
Comments (1)