How to make a very cool knife handle from plastic waste
HDPE plastic is an excellent raw material for recycling at home. It melts easily, practically does not smoke, and after cooling it acquires the necessary rigidity and density. All this allows it to be used for making various crafts. Let's look at how you can make a stylish handle for a kitchen knife from HDPE plastic.
HDPE plastic is not melted to a liquid state, as this will cause it to burn, but only heated until it becomes elastic. In this regard, casting from it at home is impossible. To work with it, you need to prepare a mold for pressing the softened raw materials. In the case of a knife handle, it is convenient to make it from plywood. The shape of the future handle is cut out in two pieces of plywood with a small tolerance.
Its model is turned from the same material, which fits exactly into the cut without gaps.
Next, the plywood with cutouts are connected to each other, and on one side they are covered with a single piece of plywood.
After the mold is ready, the plastic waste is cut up. These can be any products labeled HDPE. It looks like the number "2" in a triangle. This plastic is used to make canisters and bottles for yogurt, milk, and household chemicals. You can use raw materials of one color or several.
Plastic cut into strips melts in a regular electric oven at a temperature of 175-190 degrees Celsius or in an electric grill. It does not warm up well, so it is better to add it little by little, it will be faster than heating everything at once. In order not to spoil the coating of household appliances, you can heat them on a silicone baking mat.
The required amount of HDPE is brought to viscosity, then kneaded with gloves several times to mix the pattern. This will allow you to create stains of black burnt and the original color of the raw material on the finished product. Then the plastic mass is placed in a plywood mold and covered with the model. After this, everything is placed under a powerful press until it cools.
While the plastic is cooling, you can make the front part of the handle for the index finger from brass plates. To do this, 2 overlays with holes for rivets are cut out. They are glued onto the knife shank with epoxy, and additionally riveted with brass rivets.
Next, the cooled HDPE blank unfolds lengthwise into 2 strips. They are glued onto the shank with pigment-tinted epoxy glue. Then they are secured with ties. Rivets are not suitable in this case, as they will crack the plastic.
The result is a rough workpiece.It needs to be refined first with a rasp, then with a smaller file. Having obtained the desired shape, you need to remove the roughness with sandpaper of different grain sizes.
To add gloss, finishing is done with wax.
Materials:
- HDPE plastic;
- plywood;
- brass plates;
- brass rivets;
- brass knife ties;
- epoxy adhesive;
- color pigment.
The process of making a knife handle with your own hands
HDPE plastic is not melted to a liquid state, as this will cause it to burn, but only heated until it becomes elastic. In this regard, casting from it at home is impossible. To work with it, you need to prepare a mold for pressing the softened raw materials. In the case of a knife handle, it is convenient to make it from plywood. The shape of the future handle is cut out in two pieces of plywood with a small tolerance.
Its model is turned from the same material, which fits exactly into the cut without gaps.
Next, the plywood with cutouts are connected to each other, and on one side they are covered with a single piece of plywood.
After the mold is ready, the plastic waste is cut up. These can be any products labeled HDPE. It looks like the number "2" in a triangle. This plastic is used to make canisters and bottles for yogurt, milk, and household chemicals. You can use raw materials of one color or several.
Plastic cut into strips melts in a regular electric oven at a temperature of 175-190 degrees Celsius or in an electric grill. It does not warm up well, so it is better to add it little by little, it will be faster than heating everything at once. In order not to spoil the coating of household appliances, you can heat them on a silicone baking mat.
The required amount of HDPE is brought to viscosity, then kneaded with gloves several times to mix the pattern. This will allow you to create stains of black burnt and the original color of the raw material on the finished product. Then the plastic mass is placed in a plywood mold and covered with the model. After this, everything is placed under a powerful press until it cools.
While the plastic is cooling, you can make the front part of the handle for the index finger from brass plates. To do this, 2 overlays with holes for rivets are cut out. They are glued onto the knife shank with epoxy, and additionally riveted with brass rivets.
Next, the cooled HDPE blank unfolds lengthwise into 2 strips. They are glued onto the shank with pigment-tinted epoxy glue. Then they are secured with ties. Rivets are not suitable in this case, as they will crack the plastic.
The result is a rough workpiece.It needs to be refined first with a rasp, then with a smaller file. Having obtained the desired shape, you need to remove the roughness with sandpaper of different grain sizes.
To add gloss, finishing is done with wax.
Watch the video
Similar master classes
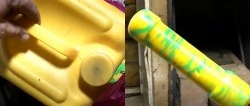
How to make a shockproof handle from a plastic canister for
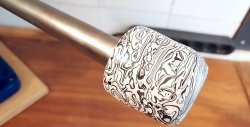
Home technology for making plastic handles from
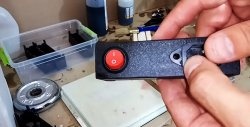
Molding plastic parts at home. As easy as pie
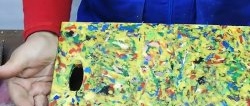
How to make a cutting board from plastic lids
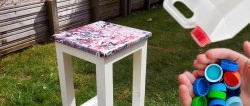
How to make a stool seat from PET covers and other plastic
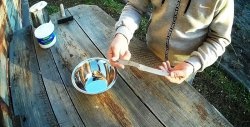
How to make a durable and anatomical knife handle in 10 minutes
Particularly interesting
Comments (0)