How to make a tool for installing forged rivets from a shock absorber spring and bearing
Forged rivets can be used in the manufacture of various decorative and power metal structures. However, in order for it to be not only reliable, but also accurate, special stamps must be used when installing it. Let's look at how to make them at home from scrap materials.
To make the device you will need a ball from a large bearing. To disassemble it, you need to remove the separator, move all the balls to one side and opposite them, squeeze the clips towards each other.
At the next stage, it is necessary to make a template from one ball for further work. To do this, a hole is drilled in a strip or a small section of a corner. It needs to be countersunk and the ball from the bearing placed on top.
On the back side of the hole it is welded to the base.
The resulting template is clamped in a vice with the ball facing up. Then the steel plate is heated in a forge until it turns light yellow. You need to quickly, while it is hot, apply it to the ball and tap it with a hammer. As a result, you need to get a deep dent in the shape of a ball.
Then you need to take a small piece of the same plate and drill it through approximately in the center to get a guide.
To do this, use a drill equal to the diameter of the rods from which the rivets will be made. You also need to make a blind hole in the end of the workpiece with a dent, cut a thread in it and screw in a pin.
Next, a high-quality steel rod is taken. An aligned section of a spring from a car is perfect for this.
The end of the rod is heated and placed against the template with the ball. It is necessary to form the same dent on it as on the previously made matrix. As a result of deformation, the shape of the resulting stamp will float a little, so it won’t hurt to sand it.
Then you need to harden the tools. They heat up to a red tarnish and drop sharply into the water. After this, the steel is tempered in a cooling forge.
To install the rivet, you need to cut a piece of mild steel rod slightly longer than the thickness of the through-hole guide.
It is heated, inserted into the plate, and its protruding part is seated by blows through a stamp with a concavity until a cap is formed.
Next, the rivet is knocked out, installed in place, and a matrix with a concavity is placed under the head. Then the opposite side is unforged with a strain from a rod without heating.
What you will need:
- large bearing;
- thick steel plate 15-25 mm;
- rod 10-20 mm;
- corner or strip;
- stud M6-M8.
The process of making rivet dies
To make the device you will need a ball from a large bearing. To disassemble it, you need to remove the separator, move all the balls to one side and opposite them, squeeze the clips towards each other.
At the next stage, it is necessary to make a template from one ball for further work. To do this, a hole is drilled in a strip or a small section of a corner. It needs to be countersunk and the ball from the bearing placed on top.
On the back side of the hole it is welded to the base.
The resulting template is clamped in a vice with the ball facing up. Then the steel plate is heated in a forge until it turns light yellow. You need to quickly, while it is hot, apply it to the ball and tap it with a hammer. As a result, you need to get a deep dent in the shape of a ball.
Then you need to take a small piece of the same plate and drill it through approximately in the center to get a guide.
To do this, use a drill equal to the diameter of the rods from which the rivets will be made. You also need to make a blind hole in the end of the workpiece with a dent, cut a thread in it and screw in a pin.
Next, a high-quality steel rod is taken. An aligned section of a spring from a car is perfect for this.
The end of the rod is heated and placed against the template with the ball. It is necessary to form the same dent on it as on the previously made matrix. As a result of deformation, the shape of the resulting stamp will float a little, so it won’t hurt to sand it.
Then you need to harden the tools. They heat up to a red tarnish and drop sharply into the water. After this, the steel is tempered in a cooling forge.
To install the rivet, you need to cut a piece of mild steel rod slightly longer than the thickness of the through-hole guide.
It is heated, inserted into the plate, and its protruding part is seated by blows through a stamp with a concavity until a cap is formed.
Next, the rivet is knocked out, installed in place, and a matrix with a concavity is placed under the head. Then the opposite side is unforged with a strain from a rod without heating.
Watch the video
Similar master classes

How to knock out a bearing race from the housing without special tools
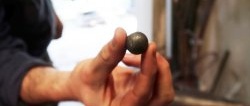
How to forge a cutter from a bearing ball
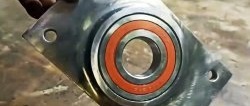
How to make a high-quality housing for installation without a lathe
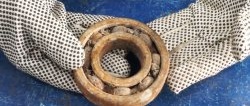
DIY bearing bending machine
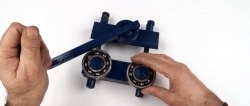
How to make a simple bending machine
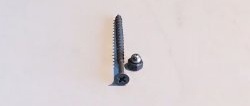
How to make a drill from a bearing for drilling hardened steel
Particularly interesting
Comments (0)