How to weld metal 1 mm thick without burning through
Making a high-quality permanent connection of thin metal using manual arc welding with a coated electrode is not an easy task even for an experienced craftsman. But with the correct selection of the welding mode, electrodes and their movements, even a novice welder can cope with this work.
Will need
- welding inverter ARC 375 - http://alii.pub/5udq1v
- electrodes E 6013 (analogue OK 46.30) - http://alii.pub/5udq0b
- sections of profile pipe;
- caliper - http://alii.pub/5udq6c
- hammer for removing slag.
The process of welding metal 1 mm thick
Let's weld sections of profile square pipes with a wall thickness of 1 mm.
With a high welding current there will be burns, with a low current there will be lack of penetration, which is aggravated by the incorrect selection of electrodes and their movements.
We choose electrodes E 6013 with a rutile coating with a diameter of 2.5 mm.
We set the current on the welding inverter to 75 A.
We press the square pipes against each other, making a system of equally spaced strips on one of them, and perpendicular to the contact line of the pipes.
Let us show the movement of the end of the electrode along the future welding seam, focusing on the stripes. We install the electrode on the first strip, thereby simulating the ignition of an arc. We lead him to the fourth and return him to the second.
Then we repeat everything: from the second strip we move the electrode to the sixth and return it to the third, etc., until we reach the last strip.
Such reciprocating movements of the electrode do not overheat the thin metal and contribute to the formation of a high-quality seam.
We weld metal 1 mm thick with a 2.5 mm electrode, at a current of 75 A and with the electrode movements shown earlier.
We knock the slag off the seam and make sure that the seam is without burns or lack of penetration along the entire length.
Be sure to see the process visually in the video below.
Watch the video
Similar master classes
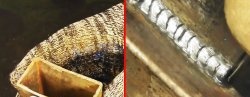
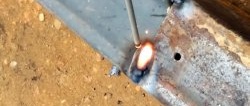
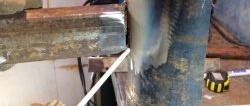
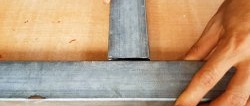
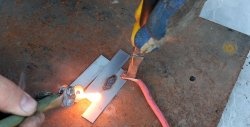
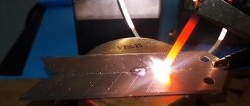