How to make a soldering and heating device from a microwave transformer
A magnetron transformer from an old microwave oven can serve as the basis for an apparatus for soldering copper products, in particular pipes. You can also use the device to heat steel parts, say, soured fasteners for easy unwinding. To make it, you will not need large expenses, time or special knowledge and skills. Any adult can cope with this work.
Will need
Materials:
- microwave magnetron transformer;
- insulated multi-core cable;
- computer power supply housing;
- legs for equipment;
- switch, wires, Light-emitting diode, cambrics, etc.;
- asbestos split tubes;
- copper cable lugs for crimping;
- bolts and nuts;
- ice tongs;
- worm clamps;
- handle-bracket for carrying equipment, etc.
Tools: drill, chisel, drift and hammer, marking and measuring accessories, grinder, pliers, dowel, etc.
Manufacturing process of soldering and heating apparatus
Carefully remove the magnetron transformer from the microwave so as not to damage the primary winding and magnetic circuits. We remove the secondary winding using a chisel, hammer and drift.
In the free space we place the winding of their multi-core cable in insulation until the free space is completely filled.
If it is difficult to pull through the last loops, the cable insulation can be lubricated with oil. We bring the ends of the cable out.
From the disassembled case of the computer power supply we remove the electronic “stuffing”, wires and fan.
We cut off the protruding sides of the transformer mounting flange.
We drill the necessary holes and secure the transformer to the housing with screws, using four support legs on the outside of the housing.
We install a two-position switch and a control switch on the outside of the case in a convenient place. Light-emitting diode and a resistor. We connect them using wires with cambrics between each other and the terminals of the primary winding of the transformer.
We assemble the body and fasten its parts with screws.
The ends of the cable used for the secondary winding of the transformer are stripped of insulation, put on asbestos split tubes and crimped with copper tips.
We insert the bolts into the holes of the tips until they stop into the pre-screwed nuts and tighten one more nut on top. We sharpen the ends of the bolts to a partial flat cone.
We cut off the grips from the ice tongs and firmly fasten the ends of the cable, covered with split asbestos tubes, to its handles using worm-drive clamps. Moreover, the pointed ends of the bolts should be directed towards each other and not touch in the non-working position.
We connect the power, turn on the switch, squeeze the handles until the electrodes touch the copper tubes and heat the soldering area until it glows white, adding solder. The result is a strong, tight and reliable connection.
To give the soldering device a marketable appearance, we paint it with aerosol paint, protecting areas that cannot be painted with electrical tape or tape. For ease of carrying, we attach a handle-bracket for the door or equipment on top.
Watch the video
Similar master classes
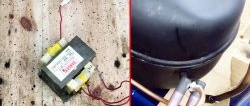
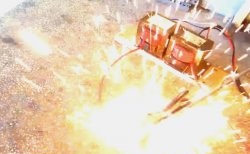
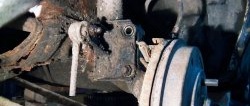
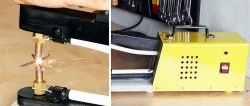
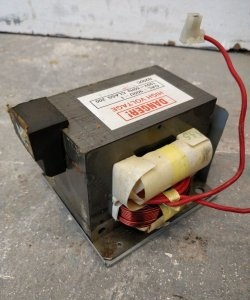
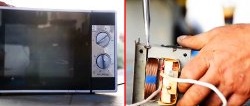