What current is preferable for welding parts 1 mm thick?
For a novice welder, the process of welding thin metal no more than 1 mm thick will not be an easy task. The lack of skills in managing the energy of an electric arc will inevitably lead not only to melting of the electrode metal, but also to through burning of the parts being welded. Professional welders with extensive experience, along with the use of special techniques when welding thin-walled metal, at the same time skillfully control the parameters of the welding process, in particular, the strength of the welding current. Let's see what a high welding current leads to when working with thin metal and what it should be to carry out high-quality welding of thin-walled parts without burns.
Unacceptability of high welding current when welding steel 1 mm thick
We will weld two pieces of profile square pipe with a wall thickness of 1 mm tightly pressed against each other in the longitudinal direction, simply moving the electrode along the contact line of the parts being welded at a certain speed, without slowing down or speeding up its progress.
Using a stepless regulator on the welding machine, we bring the welding current to 150 A.We will carry out the welding process using one of the most common electrodes of the E7018 brand.
The result of welding thin-walled square pipes with a welding current of 150 A turned out to be of depressingly poor quality. Instead of a continuous weld, there were only through burns along the entire length of the weld line. This result, of course, will not satisfy anyone.
Welding electrodes for general purposes on AliExpress at a discount - http://alii.pub/606j2h
Preference for low welding current when welding thin-walled parts
We reduce the welding current value of 150 A set on the welding machine by more than half, more precisely to 70 A. In connection with the change in this most important characteristic of the welding process, we also change the electrode: instead of grade E7018, we take grade E6013, made of softer steel and therefore lighter amenable to melting in an electric arc.
We leave the welding process the same: we move the electrode evenly along the contact line of thin-walled parts, except that we slightly reduce the speed of its movement.
After completing the welding process, we beat off the slag along the entire length of the weld and make sure that it is continuous throughout its entire length, of the same width and height, without any slag inclusions, and most importantly, without even a hint of burning through thin-walled parts.
So, one of the constant conditions for high-quality welding of thin metal is a small amount of welding current.
Welding with a graphite electrode from a battery is a cheap and accessible replacement for TIG welding - https://home.washerhouse.com/en/8404-svarka-grafitovym-jelektrodom-iz-batarejki-deshevaja-i-kazhdomu-dostupnaja-zamena-tig-svarke.html
Watch the video
Similar master classes
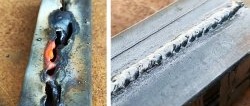
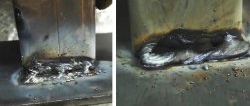
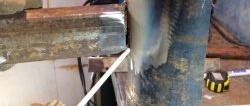
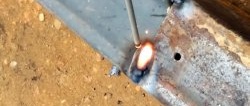
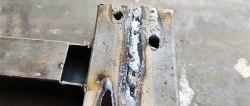
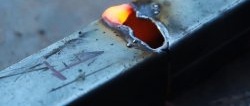