How to make a jack from an angle grinder gearbox, a motorcycle chain and sprockets
For any jack in a store you will have to pay from several thousand rubles. A significant loss for the family budget. A screw jack with a chain drive, which any adult with the skills of a metalworker can assemble, will help you save money.
Will need
Materials:
- remains of corners, strips, thick metal;
- steel pipe 28 cm long;
- rod with external thread;
- large and small stars;
- bolts, nuts and washers are different;
- angle gear from an angle grinder;
- motorcycle chain, etc.
Tools: welding, plasma cutter, drilling machine, vice, lathe, grinder, adjustable wrench, etc.
High-quality and durable drills on AliExpress at a discount - http://alii.pub/5zwmxz
The process of making a jack from a motorcycle chain
We weld steel corners to a thick and rigid steel strip at both ends so that the welded flanges of the corners lie in the same plane with the strip.
From the remains of thick steel, we cut out two circles with a plasma torch and a special device for cutting out circles of a given diameter.
In two smaller circles, drill holes in the center and grind the outer diameter to the size of the inner diameter of the pipe. In the rings we make a longitudinal groove on the lateral outer surface.
On a round steel pipe 28 cm long, measure 8 cm from one end and mark with marks. We drill a through radial hole according to the marks and place one ring in its section and weld it through the holes to the pipe from the inside.
We insert the second ring and weld it flush with the end of the pipe closest to the first ring.
We install the free end of the pipe with rings in the center of the strip between two corners and weld it.
Welding electrodes for general purposes on AliExpress at a discount - http://alii.pub/606j2h
In one of the circles cut out of thick metal, drill a hole in the center.
We screw a nut onto a rod with an external thread, press a circle against it, pulling it from the outside with another, and weld it with the internal nut. Remove the outer nut.
We clamp a rod with an external thread in the chuck of a lathe, screw a nut with a welded circle onto it and grind the side surface and outer diameter.
Then we place a large sprocket concentrically on it, drill 4 mounting holes and tighten these parts with bolts and nuts.
We drill a radial hole in a pipe with a ring at the end, insert a metal rod into it, and hammer it down until its end appears in the lumen of the ring.
In a rod with an external thread, we cut a longitudinal groove along almost the entire length with a grinder.
We insert it into the ring so that the protruding stopper fits into the groove and does not interfere with the threaded rod moving along the pipe.
We screw and weld a nut onto the end of the rod without a groove.
We screw a knot of a large asterisk, a circle and a nut onto the other end of the rod. As it rotates, the male threaded rod moves along the pipe and rises above the large sprocket.
We weld a small sprocket to the end of the low-speed shaft of the angular gearbox from an old angle grinder. We bolt two plates with holes at the ends to the holes in the gearbox housing, one of which is specially curved.
We put a chain on the sprockets and, making sure that they are in the same plane, weld the ends of the plates attached to the gearbox housing to a pipe with an externally threaded rod.
To give the structure greater rigidity and strength, we weld the jibs from profile square pipes, resting one end on the pipe and the other on the inner corners of the corners.
Screw the nut onto the free end of the threaded rod to the level of its end. It will serve as a heel when lifting a car or other products.
We attach a drive handle to the end of the horizontal shaft, the rotation of which leads to lifting the load.
Long-lasting discs for angle grinders on AliExpress at a discount - http://alii.pub/61bjly
Watch the video
Similar master classes
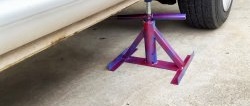
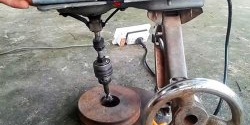
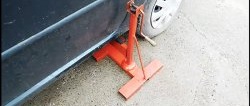
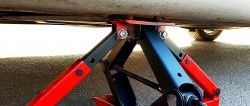

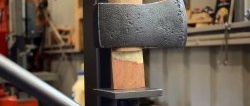