How to upgrade your jack for more rigidity and secure fit
Drivers do not have much confidence in the manually operated diamond screw jack as it is not strong and rigid. But it can be modified, which we will do using leftover metal. Moreover, such work does not require special qualifications. After modernization, the reliability of the jack when lifting a car for certain purposes will increase significantly. Moreover, its dimensions will hardly change, since the design will be foldable.
Will need
Materials:- steel equal angle angle 50×50 mm;
- profile rectangular pipe 25×40 mm;
- profile square pipes 25×25 mm and 30×30 mm;
- steel round bar or rod;
- sheet metal;
- a piece of hairpin;
- spray paint, etc.
Long-lasting discs for angle grinders on AliExpress at a discount - http://alii.pub/61bjly
We modernize a standard diamond jack ourselves
Use a grinder to cut off the heads of two locking pins to remove the lower support of the lifting device.
Instead, in the future we will install a reinforced support from a steel angle of 50x50 mm. It is now possible to strengthen the serrated edges of the lower control arms.
To do this, we cut out 4 steel plates 40x50 mm and weld them from the inside to the ends of the levers.
We turn them to obtain the required shape. Using the holes in the levers as guides, we make holes in the plates for the subsequent installation of locking pins.
To make a reinforced lower support, we take two corners 50x50 mm and 600 mm long. We weld them into a profile like a channel so that a jack can fit inside without unnecessary gaps. We cut the vertical shelves according to the slope of the upper lift arms when they are fully folded.
Focusing on the holes in the lower arms of the lifting device, we drill holes in the vertical shelves of the corner, which represents the reinforced lower support. We fasten it to the jack with locking pins. We place the washer on the ends of the fingers on both sides and scald it.
We take two steel corners 50x50x130 mm, weld the profile in the form of a channel and cut it according to the shelf markings. As a result, we get a plate with small beads on both sides. In its center we make a rectangular opening for support and weld the plate to the upper edge of the lift.
In the center, on both sides, to the shelves of the corner representing the lower support, we attach by welding 50x40 mm plates with rounded outer corners and holes in the middle.
They are needed for attaching additional support legs made of two 25x40x250 mm profile pipes, rounded at one end, and welded with a steel strip. We make the joints hinged so that it is possible to fold the support legs at the end of the work.
We weld sections of pins to the ends of the additional legs from below to provide 4 points of support lying in the same plane, and to the hinged side - limit stops in the form of narrow plates.
We weld parts in the form of U-shaped brackets (fasteners) with holes on top of the edges of the support legs.
We attach telescopic stops in them, made of square pipes 30x30x195 mm and 25x25x230 mm, and inserted into each other. The second ends of the stops are also hinged to the bottom side of the plate using U-shaped brackets, which also provide rotation relative to the plate.
All that remains is to clean the seams, remove burrs, round off sharp edges, paint, and the modernized jack is completely ready to reliably perform its functions in full.
When folded it is small in size.
You can always securely secure the lift with cotter pins.
Watch the video
Similar master classes
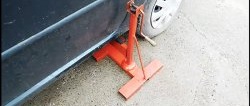
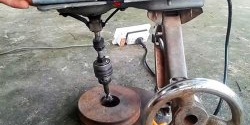
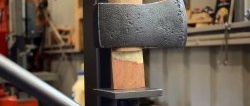
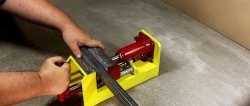
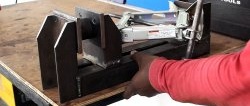
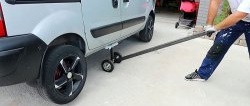