How to make a drilling machine from a jack and a washing machine motor
The motor and gearbox from an old top-drum washing machine can be used to make a drill press. The use of these parts makes the assembly process very simple and inexpensive since they are mounted on a mounting plate that can be used as part of the machine frame.
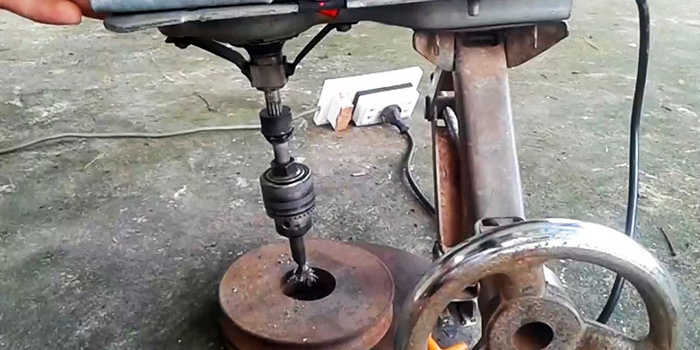
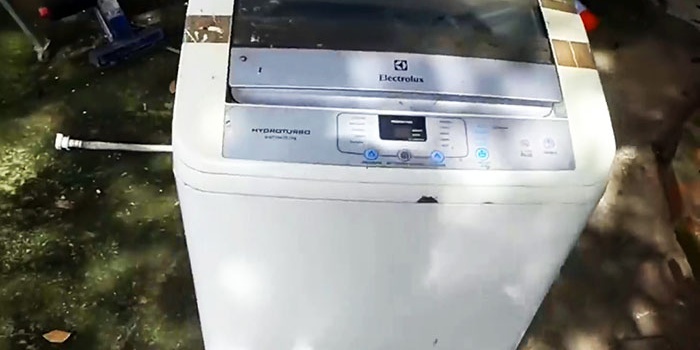
From a washing machine with a vertical drum, you need to remove the mounting plate with the motor and belt drive installed on it. You will also need to remove the splined bushing under the gearbox shaft, which allows you to put on the pulsator (a disk with blades at the bottom of the drum).
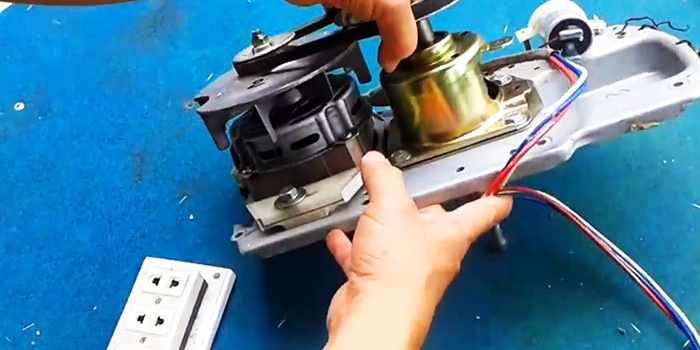
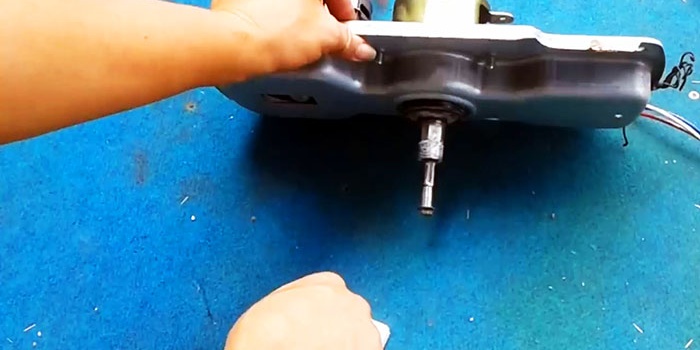
The engine of the machine is temporarily removed from the mounting plate to drill holes for attaching the diamond-shaped jack.
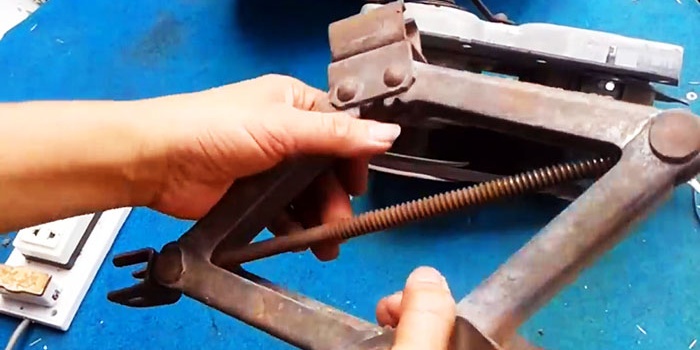
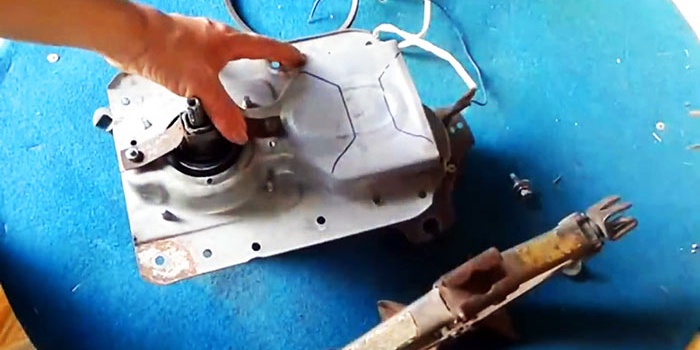
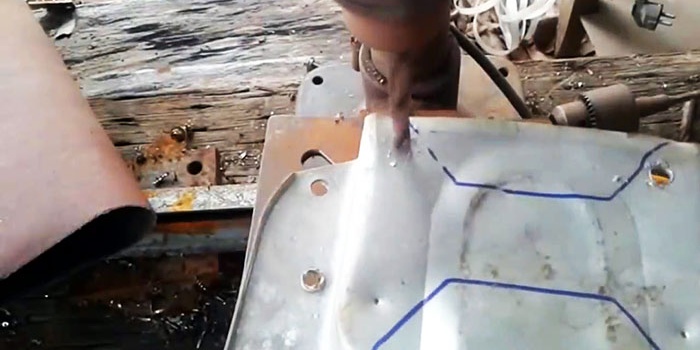
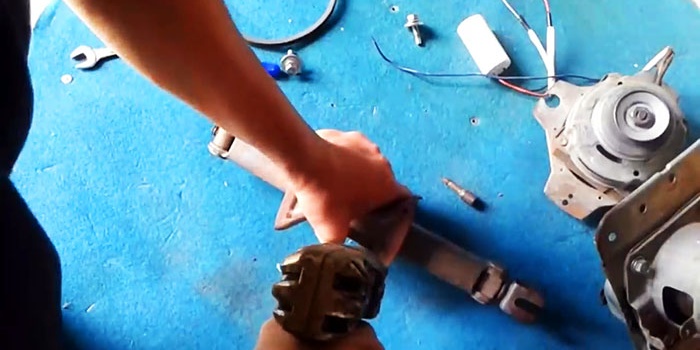
After this, the jack is screwed onto 4 bolts, and the electric motor is installed back.
Next you need to make an extension for the gearbox shaft. Its length together with the shaft must be equal to the height of the fully lowered jack. A bolt with an appropriate thread is used as an extension to screw on the drill chuck. A sleeve with slots is welded to its head.
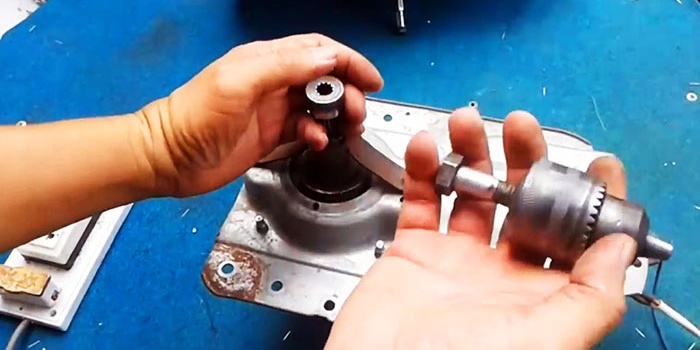
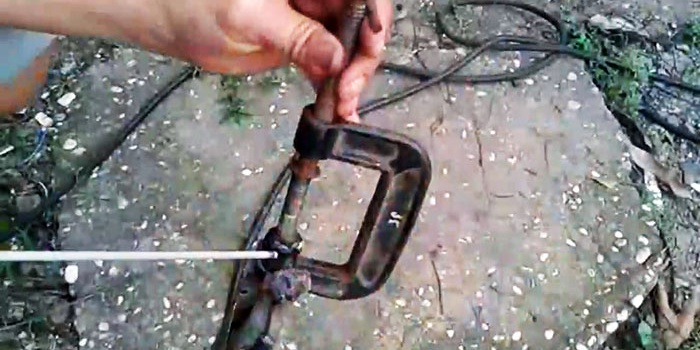
An extension made of a bolt and bushing is screwed onto the gearbox shaft. A drill chuck is screwed onto it. In order for the cartridge to hold securely, it must be locked.
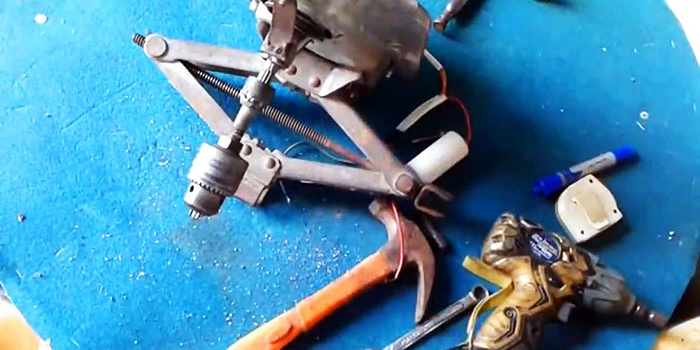
The resulting structure is placed on a heavy steel plate, which will serve as the sole of the machine. The extension cord must be positioned vertically, and then the sole must be welded to the jack stop.
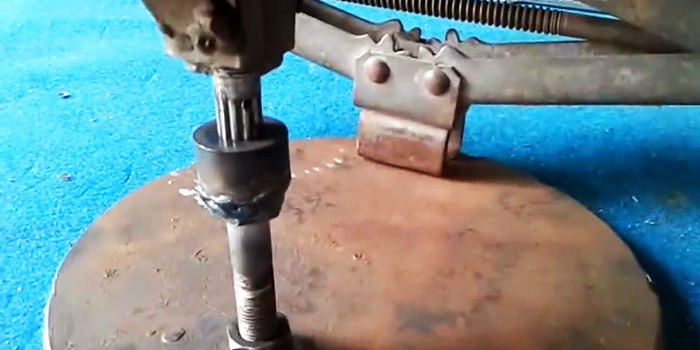
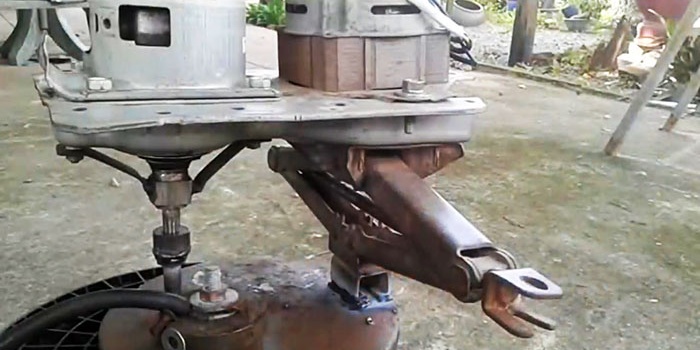
The final stage of assembly is to install the feed handwheel onto the jack adjusting screw. You can do without it, but working with it is much more convenient. To connect the screw and the flywheel, you will need to weld an adapter in the form of a tee. As a last resort, if the flywheel is steel, then you can simply weld it.
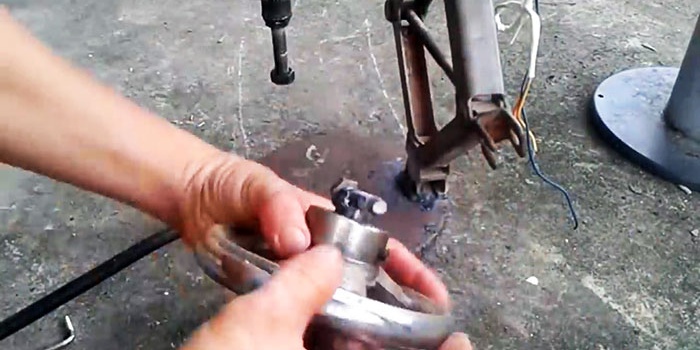
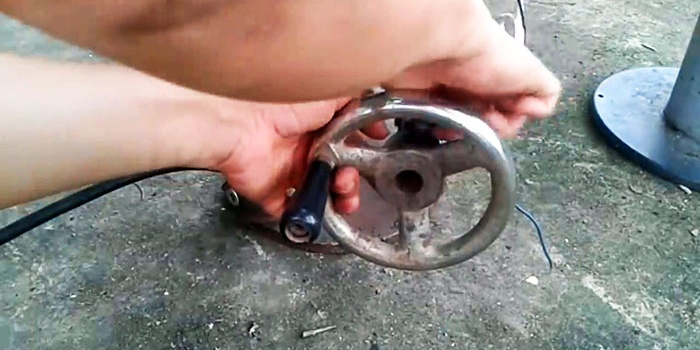
It also wouldn’t hurt to put a key switch on the machine so you don’t have to insert the plug into the socket every time. For safety reasons, you need to cover the drive belt between the gearbox and the engine with a sheet metal casing.
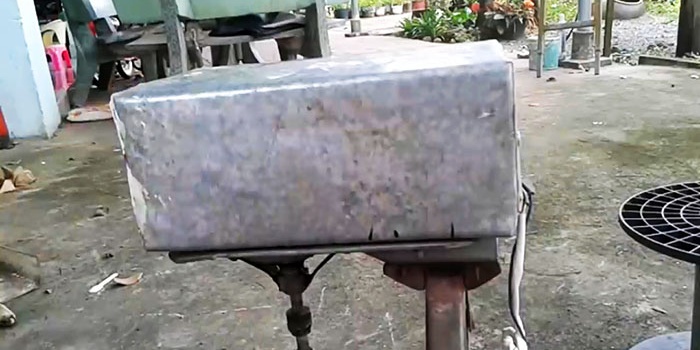
Thanks to the diamond-shaped jack, the resulting machine has a smooth lowering adjustment, which is convenient. There is also a drawback in the form of runout at the end of the drill, which is caused by wear of the gearbox, but if the extension is welded smoothly, then it will be acceptable.
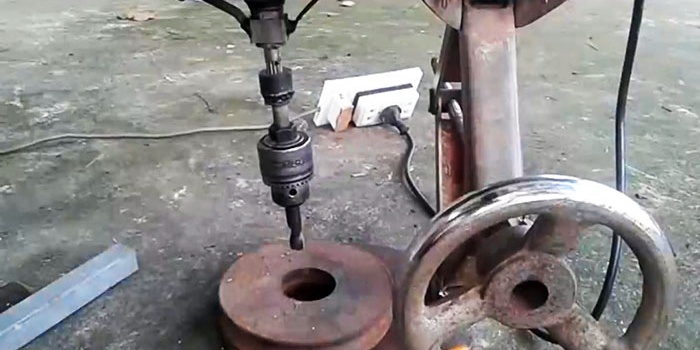
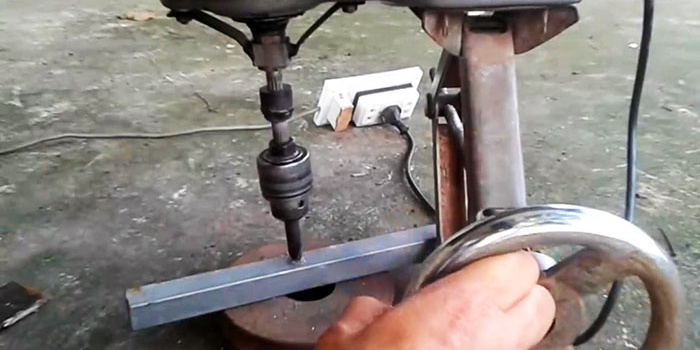
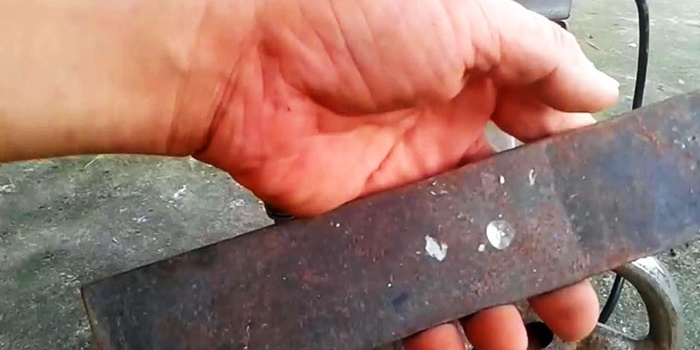
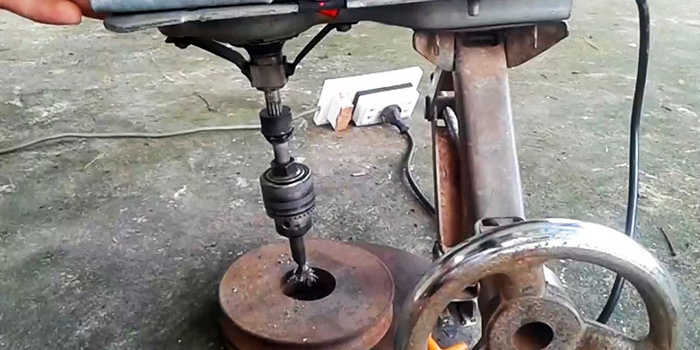
Basic materials:
- screw diamond jack;
- washing machine motor and gearbox with mounting plate;
- bushing with slots from the washing machine activator;
- drill chuck;
- heavy steel plate for making the sole;
- machine feed flywheel;
- key switch.
Making a drilling machine
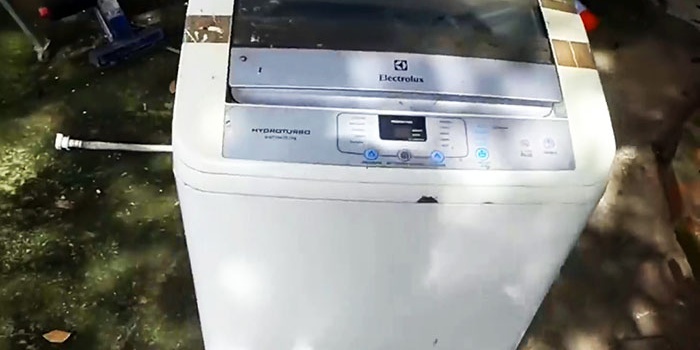
From a washing machine with a vertical drum, you need to remove the mounting plate with the motor and belt drive installed on it. You will also need to remove the splined bushing under the gearbox shaft, which allows you to put on the pulsator (a disk with blades at the bottom of the drum).
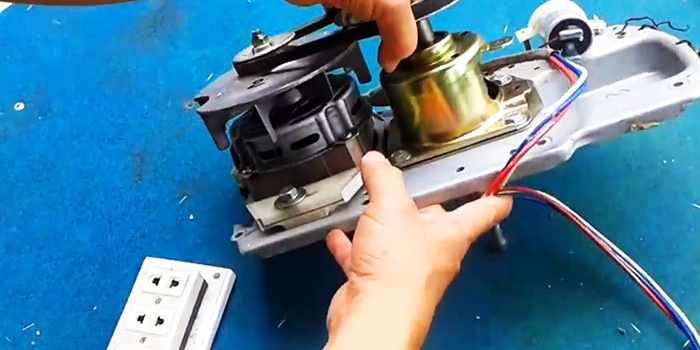
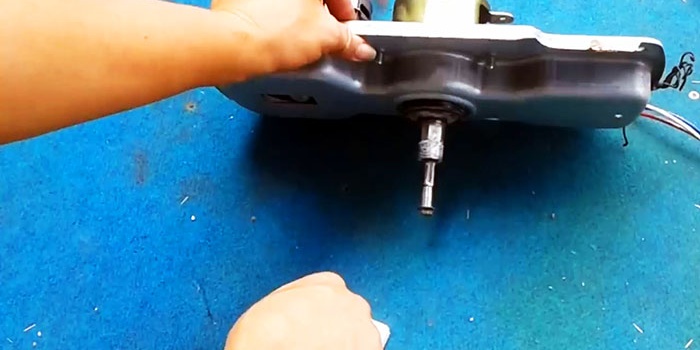
The engine of the machine is temporarily removed from the mounting plate to drill holes for attaching the diamond-shaped jack.
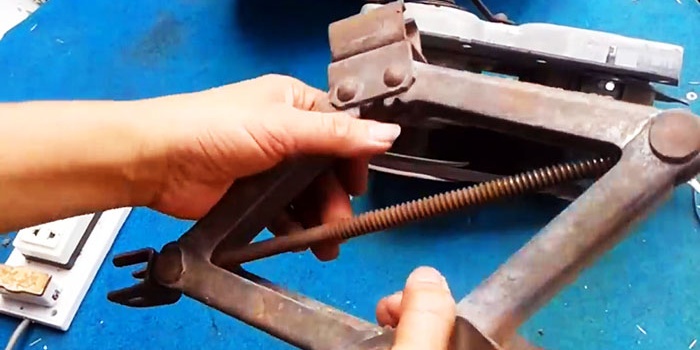
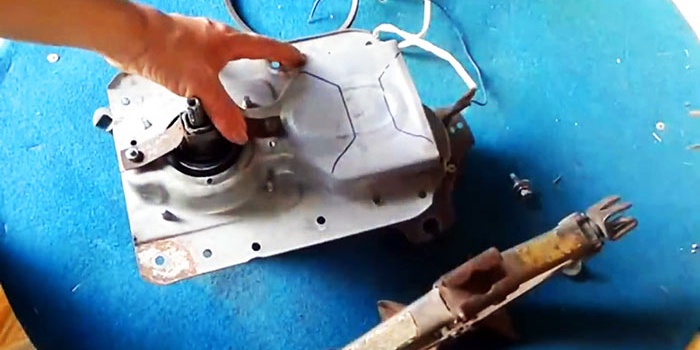
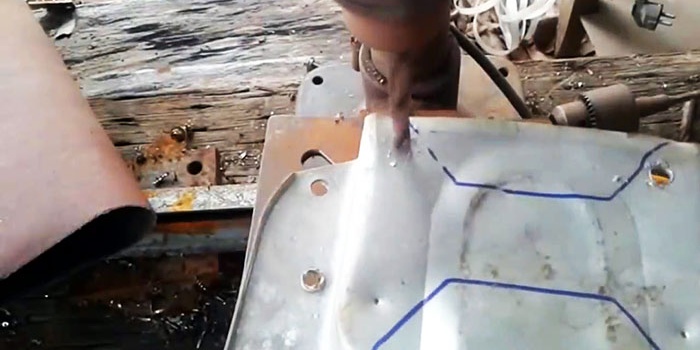
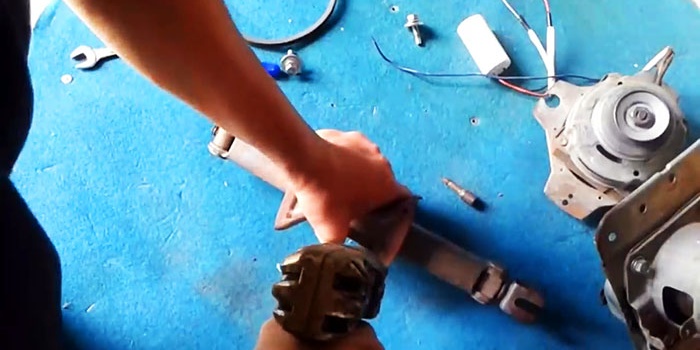
After this, the jack is screwed onto 4 bolts, and the electric motor is installed back.
Next you need to make an extension for the gearbox shaft. Its length together with the shaft must be equal to the height of the fully lowered jack. A bolt with an appropriate thread is used as an extension to screw on the drill chuck. A sleeve with slots is welded to its head.
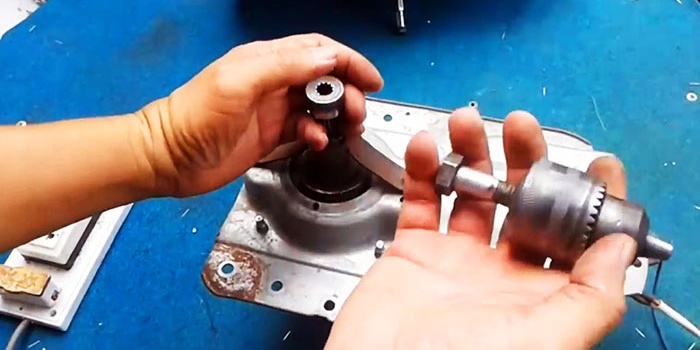
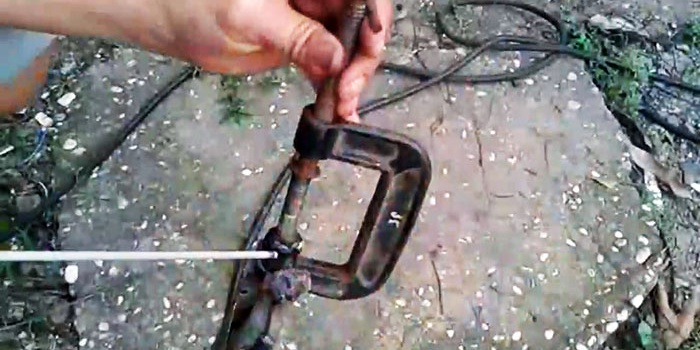
An extension made of a bolt and bushing is screwed onto the gearbox shaft. A drill chuck is screwed onto it. In order for the cartridge to hold securely, it must be locked.
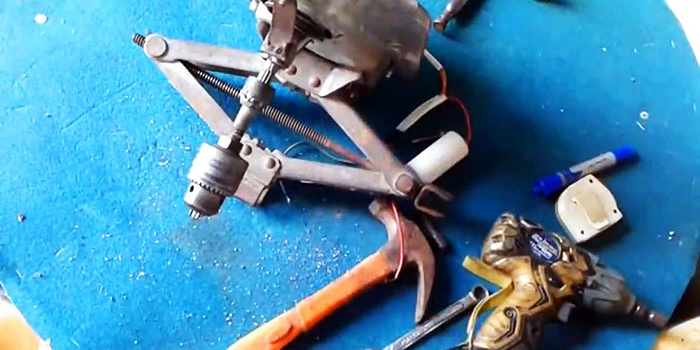
The resulting structure is placed on a heavy steel plate, which will serve as the sole of the machine. The extension cord must be positioned vertically, and then the sole must be welded to the jack stop.
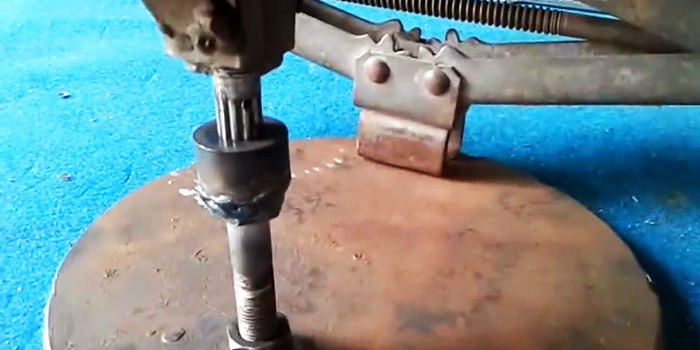
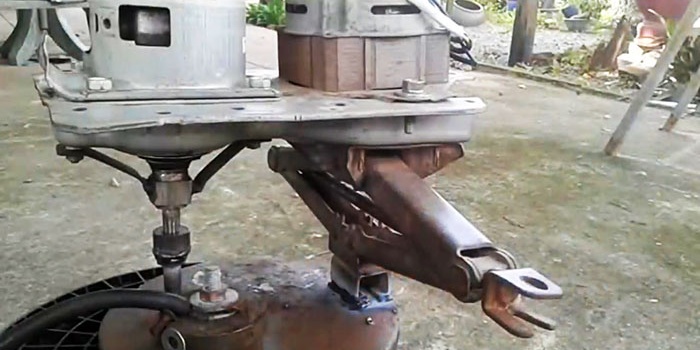
The final stage of assembly is to install the feed handwheel onto the jack adjusting screw. You can do without it, but working with it is much more convenient. To connect the screw and the flywheel, you will need to weld an adapter in the form of a tee. As a last resort, if the flywheel is steel, then you can simply weld it.
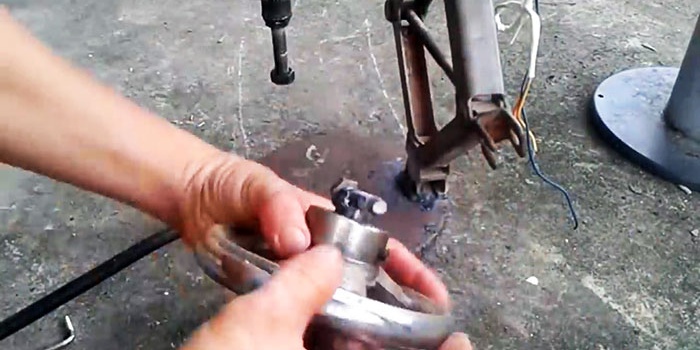
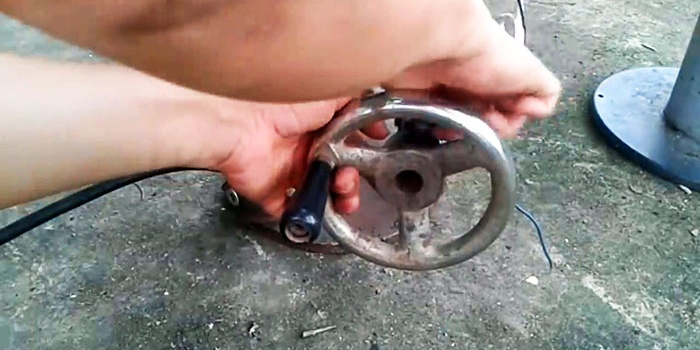
It also wouldn’t hurt to put a key switch on the machine so you don’t have to insert the plug into the socket every time. For safety reasons, you need to cover the drive belt between the gearbox and the engine with a sheet metal casing.
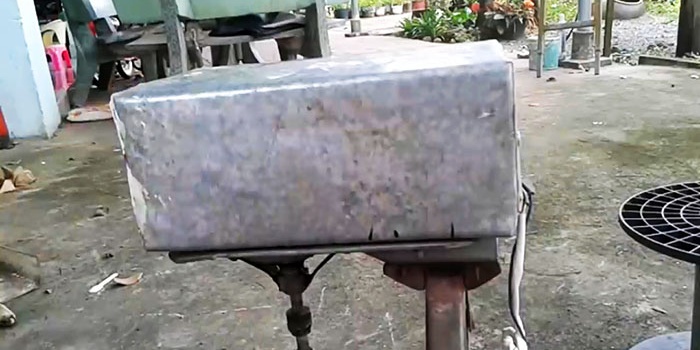
Thanks to the diamond-shaped jack, the resulting machine has a smooth lowering adjustment, which is convenient. There is also a drawback in the form of runout at the end of the drill, which is caused by wear of the gearbox, but if the extension is welded smoothly, then it will be acceptable.
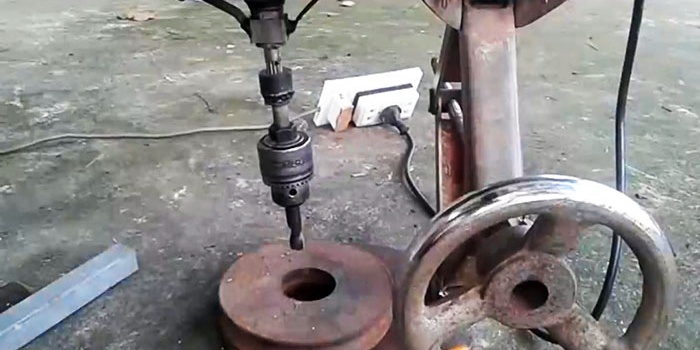
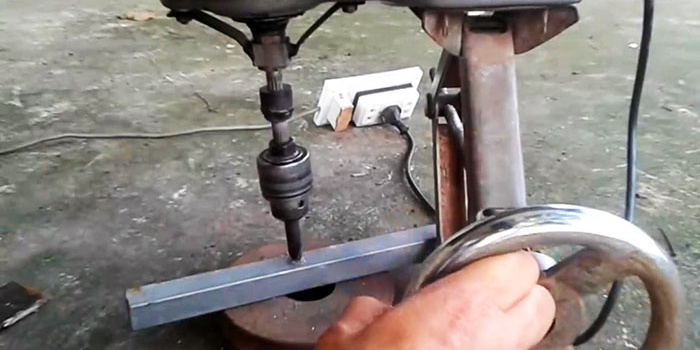
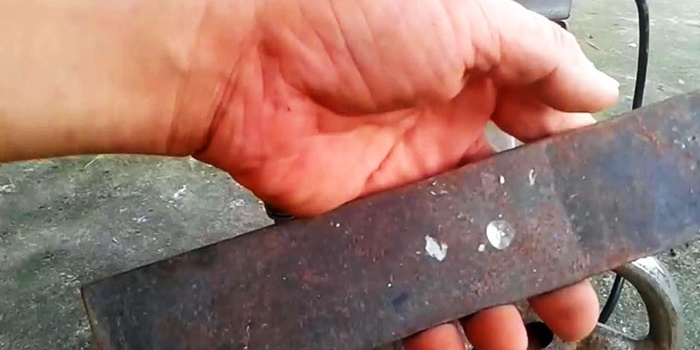
Watch the video
Similar master classes
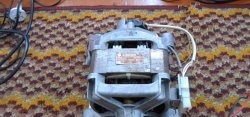
How to connect the motor from a washing machine to 220 V
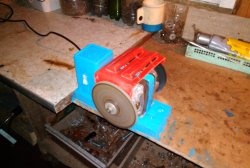
Sharpener from a washing machine engine
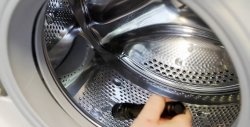
How to remove small objects caught in the washing machine from
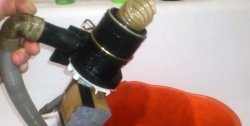
Submersible pump from a washing machine pump
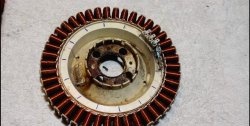
Electric generator - conversion of a washing machine engine
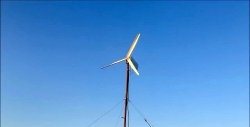
Wind generator from HDD and washing machine pumps
Particularly interesting
Comments (0)