The trick of an experienced welder when welding thin metal 0.3 mm
Welding thin metal 0.3 mm thick, especially galvanized, is a rather difficult and unsafe task even for an experienced welder, since zinc fumes are very poisonous and the welding process must be carried out outdoors or in a well-ventilated area, preferably with forced ventilation. You should wear canvas or leather mittens or gloves on your hands.
Thin metal welding process. The trick of an experienced welder
When welding thin metal, there are strict restrictions on the amount of welding current (should be in the range of 30-50 A), but this makes it difficult to hold the electric arc. It is also necessary to use thin electrodes with a diameter of 1.6 to 2.0 mm. Along the welding line, the zinc coating should be removed, for example, with a wire brush, and all contaminants in the form of dust, dirt, oils, paints, protective films and other coatings.
In order not to burn through thin metal, it is necessary to weld it not in a continuous seam without tearing off the electrode, but intermittently with a minimum gap between the workpieces being welded. It is preferable in this case to use reverse polarity, which promotes less sticking of the electrode and reduces the likelihood of burns through thin metal.
Welding electrodes for general purposes on AliExpress at a discount - http://alii.pub/606j2h
Traditionally, several methods are used for welding thin metal. The greatest difficulties arise when butt welding such metal. Usually, even an experienced welder is not always able to do butt welding, and even more so for a beginner. Metal burning in its design is 100% guaranteed at first, even with intermittent electrode guidance.
The overlapping welding process of two thin metal pieces makes the task somewhat easier. An experienced welder can almost always perform overlap welding, but for a beginner, even this option will present a certain difficulty. The task is somewhat easier due to the fact that the contact area of the parts being welded increases.
The most suitable method for joining thin metal sheets is welding with flanging of the edges of the parts being welded. To do this, we mark the edges of the workpieces to be welded and perform flanging, using, for example, a bench vice.
Then, holding and pressing the parts to be welded by both flanges with pliers, we perform an intermittent process of welding the flanges.
In this case, the thin metal seems to thicken and instead of welding two sheets of 0.3 mm thick each, we weld one sheet of double thickness (0.6 = 0.3 + 0.3 mm).
Welding electrodes for general purposes on AliExpress at a discount - http://alii.pub/606j2h
Watch the video
Similar master classes
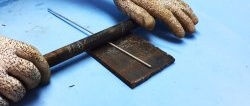
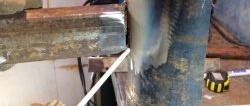
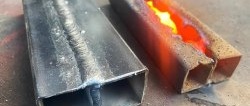
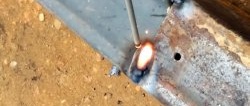
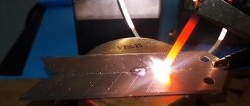
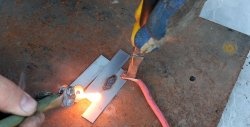