How to make a lead screw for a vice from a bar without a lathe
To make a lead screw for a bench vice, at the very least, a lathe is required. But with some skill in handling ordinary tools, it can be done, as they say, on the knee. To do this, it is enough to have a steady hand and a creative approach to business.
Will need
Materials:
- steel pipe with a diameter of 15 mm;
- wire with a diameter of 4 mm;
- plates of various thicknesses;
- rod from a car shock absorber with a diameter of 22 mm;
- worm clamp or blue electrical tape;
- wooden boards;
- perforated mounting angles;
- bolts, stud, nuts;
- nails and screws.
Tools: bench vice, metal chisel, locking pliers, marker, hammer, wrenches, etc.
Long-lasting discs for angle grinders on AliExpress at a discount - http://alii.pub/61bjly
Preparatory work
Since the thread of the lead screw must be precise so that the screw does not jam in the nut and the movement of the working element is uniform, we will make a spring from wire with a pitch equal to the thread pitch of the future screw.
To do this, we wind 5-6 turns of wire with a diameter of 4 mm onto a pipe with a diameter of 15 mm with a radial hole at the end.Then remove the resulting spring from the pipe by cutting off the end with a chisel.
We leave the most dense turns, remove the rest. Next, we expand the coils of the spring to the desired size using plates that increase in thickness. To do this, alternately insert plates of thickness 1, 2 and 3 mm between the first and second turns and scroll along the entire length of the spring.
In our case, the distance between the coils of the spring must correspond exactly to 3 mm, since the diameter of the shock absorber rod from which we will make the lead screw is 22 mm. If the diameter of the rod is different, then the distance between the turns will change accordingly.
Assembling the lead screw threading device
In order to maintain the pitch and inclination of the thread along the entire length of the screw, we fix the angle grinder in a certain position. To do this, to a horizontal board using two perforated corners at an angle to its longitudinal axis, we attach a second board, which can be rotated in a vertical plane, to the end with a bolt and a nut.
We attach the body of the angle grinder to the end of the vertical board from below using a metal plate, also with a bolt and nut. To adjust grinder disc We screw a pin into the vertical board along the height, which rests its lower end against the horizontal board.
We drive 3 nails into the horizontal board: one - outside the grinder disk, the second - at a distance that is a multiple of the pitch of the future screw thread, the third - outside the vertical board to limit its movement to the side.
Long-lasting discs for angle grinders on AliExpress at a discount - http://alii.pub/61bjly
The process of cutting threads of a lead screw using a tool based on a grinder
We put the spring on the end of the rod, secure it to it with a clamp, blue electrical tape or clamping pliers.Moving the marker between the coils of the spring, we apply at least two coils of the future thread to the surface of the rod.
Then we rest the rod against the nails so that the first turn coincides with the nail near the grinder disk and turn on the tool. Rotating the rod, in several passes we cut the thread of the lead screw of the given profile and pitch. You just need to make sure that the thread slides over the nails.
Periodically, using a previously made spring, we control the thread pitch along the entire length of the lead screw, aligning the thread protrusions with the coils of the spring, and, if necessary, adjust it.
Long-lasting discs for angle grinders on AliExpress at a discount - http://alii.pub/61bjly
Watch the video
Similar master classes
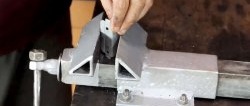
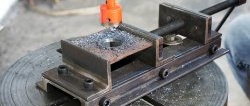
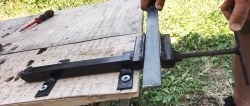
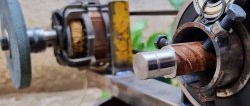
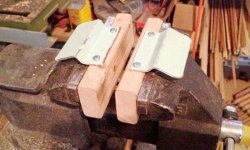
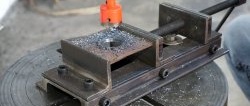