How to make soft and removable vise covers
The clamping force, which is developed by a manual screw with a lever on a conventional bench vice, reaches values from 1000 kg to 2000 kg. Taking into account the hardness of the jaws and the presence of notches, not only risks may remain on the workpiece, but also deformation and even breakage may occur. The smaller the area of the contact “spot” with the jaws and the softer the material of the part, the more real the probability and degree of damage.
To prevent damage to the workpieces, you should use pads made from soft metal (aluminum, brass, copper), polymers or wood. In addition to the safety of the workpiece being fixed, they protect the jaws of the vice from damage by a processing tool (grinder, milling cutter, chisel, etc.).
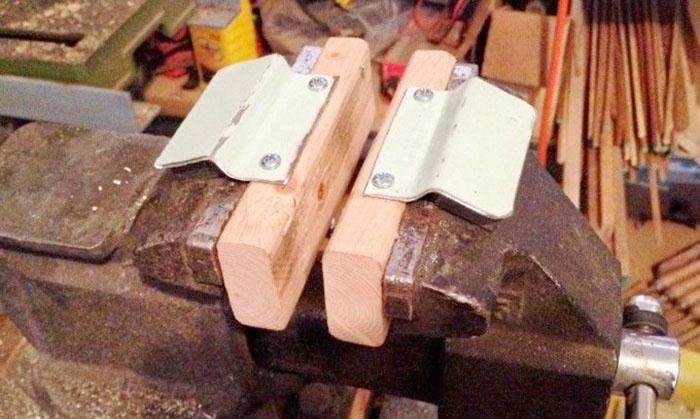
The pads can be attached to the jaws of the vice using round magnets installed from the back into the corresponding recesses using suitable glue. Below we will consider an option in which magnets are not built into the pads, but are simply fixed to the surface of the vice.
Before starting work, you should stock up on accessible and inexpensive materials:
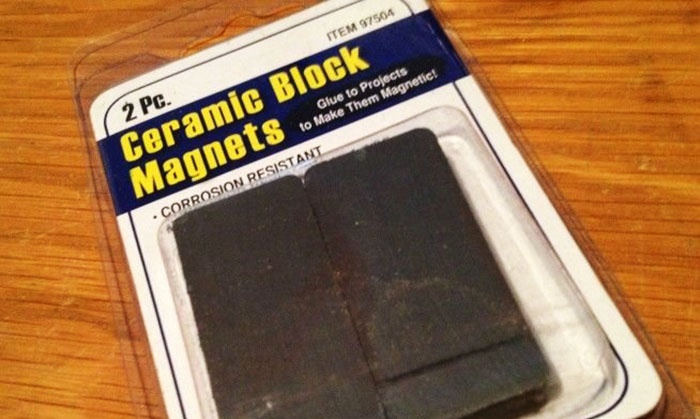
You will also need simple universal tools, used mainly in the household: metal scissors; grinding wheel; drill or drilling machine; bench vice; hammer; screwdriver.
1. First, let's make the most important part - a metal bracket, which is designed to fix the lining in the required position. To do this, we clamp one of the ready-made overlays in a vice in the position that has been previously determined and planned. We do the same with a block magnet: we fix it on a vice in the place where it is most firmly attached.
2. Then take a sheet of paper and make a template for the staple, applying it to the pad and magnet, and making the necessary folds.
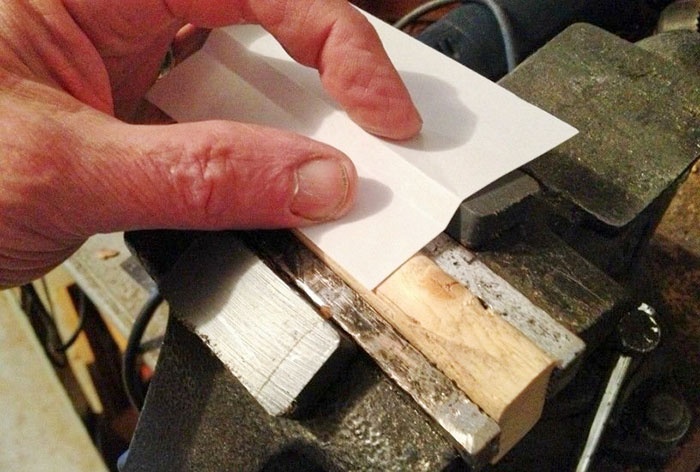
Now you can mark and cut the paper, making sure that all of the template is in contact with the surfaces formed by the pad and the magnet, and that its edges are in the right place.
3. Using metal scissors, we cut out a staple blank from a pre-prepared strip of sheet metal, attaching a straightened paper template to it, with an allowance of 1-2 mm for subsequent processing.
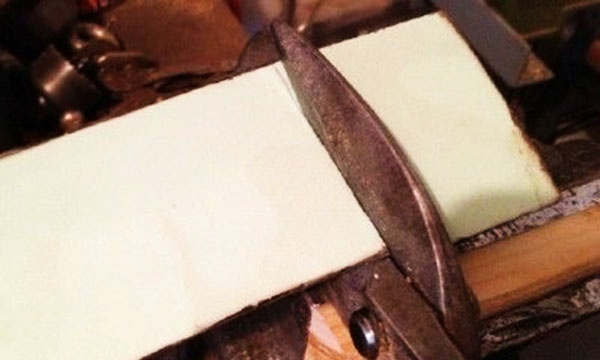
4. Using a vice and a hammer, we give the workpiece the necessary bend, constantly checking the degree of deformation by applying it to the pad and magnet, which are fixed to the vice in the calculated positions. In order to avoid injury from the sharp edges and corners of the staples during current work and in future use, we smooth and grind them on an emery wheel.

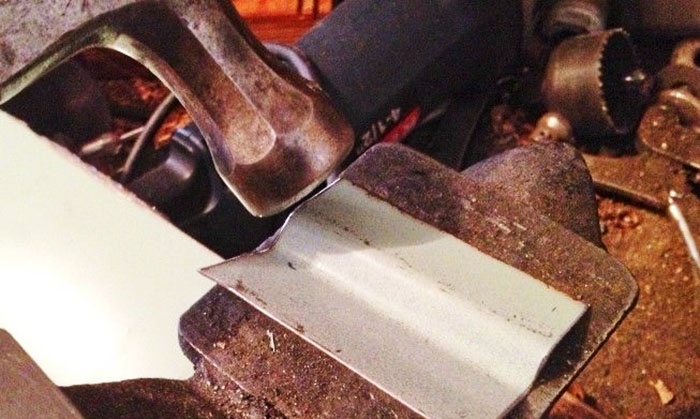
5. We fasten each bracket to its lining, having previously drilled two holes in them for screws, which we screw in using a hand screwdriver or drill with an appropriate bit.
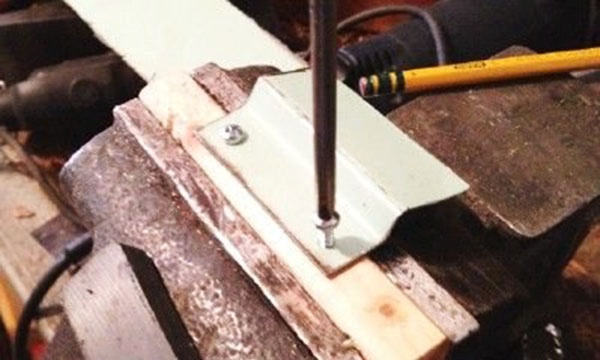
6.When the soft pads are not needed, they can be easily removed from the vice and stored with the magnets, attached to a metal surface in a hidden place until the next use.
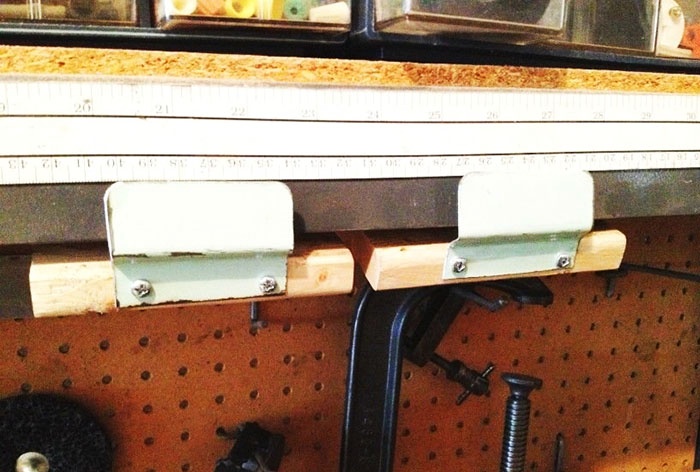
7. Our homemade pads will reliably protect the workpieces that we are going to clamp in a vice for marking or machining. Their fixation in the desired position is ensured by powerful magnets. The covers are quick and easy to install, as well as dismantle. Their production requires almost no costs, except for the purchase of magnets costing from 100 rubles.
To prevent damage to the workpieces, you should use pads made from soft metal (aluminum, brass, copper), polymers or wood. In addition to the safety of the workpiece being fixed, they protect the jaws of the vice from damage by a processing tool (grinder, milling cutter, chisel, etc.).
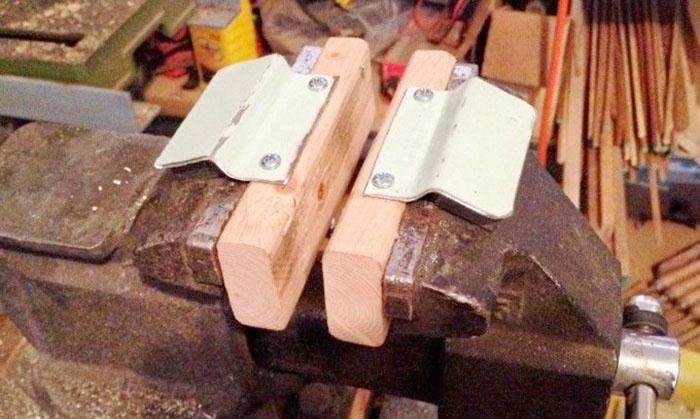
The pads can be attached to the jaws of the vice using round magnets installed from the back into the corresponding recesses using suitable glue. Below we will consider an option in which magnets are not built into the pads, but are simply fixed to the surface of the vice.
Accessories for making overlays
Before starting work, you should stock up on accessible and inexpensive materials:
- block magnets – 2 pcs.;
- wooden blocks measuring 25×50×110 mm – 2 pcs.;
- a strip of sheet metal 50-60 mm wide and no more than 2.0 mm thick;
- screws with a diameter of 4-5 mm – 4 pcs.
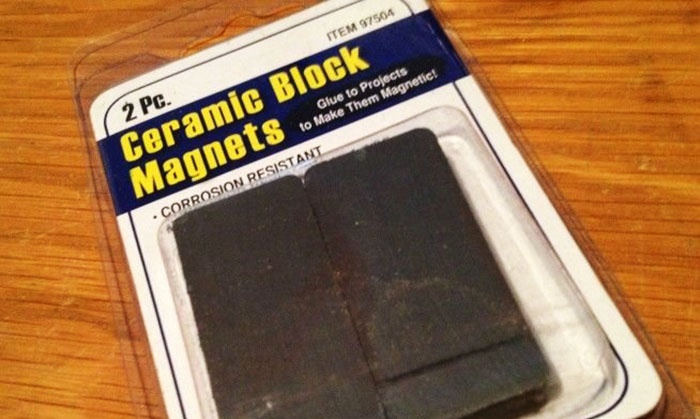
You will also need simple universal tools, used mainly in the household: metal scissors; grinding wheel; drill or drilling machine; bench vice; hammer; screwdriver.
Manufacturing of removable pads
1. First, let's make the most important part - a metal bracket, which is designed to fix the lining in the required position. To do this, we clamp one of the ready-made overlays in a vice in the position that has been previously determined and planned. We do the same with a block magnet: we fix it on a vice in the place where it is most firmly attached.
2. Then take a sheet of paper and make a template for the staple, applying it to the pad and magnet, and making the necessary folds.
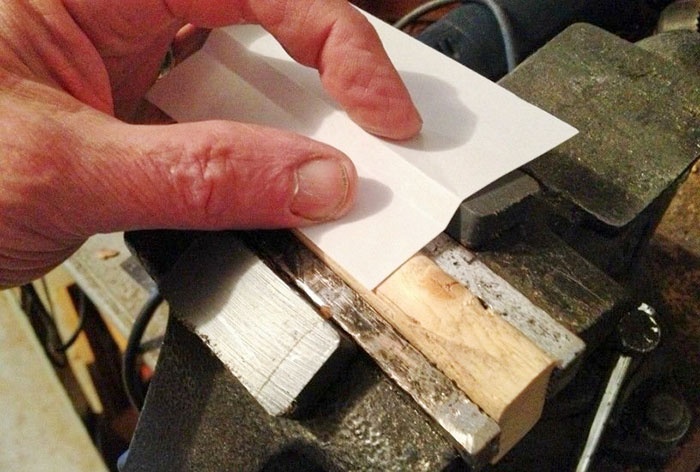
Now you can mark and cut the paper, making sure that all of the template is in contact with the surfaces formed by the pad and the magnet, and that its edges are in the right place.
3. Using metal scissors, we cut out a staple blank from a pre-prepared strip of sheet metal, attaching a straightened paper template to it, with an allowance of 1-2 mm for subsequent processing.
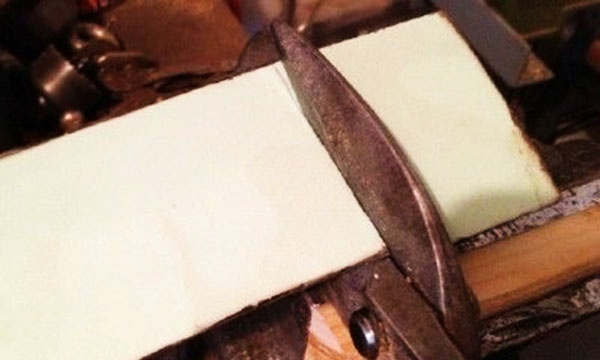
4. Using a vice and a hammer, we give the workpiece the necessary bend, constantly checking the degree of deformation by applying it to the pad and magnet, which are fixed to the vice in the calculated positions. In order to avoid injury from the sharp edges and corners of the staples during current work and in future use, we smooth and grind them on an emery wheel.

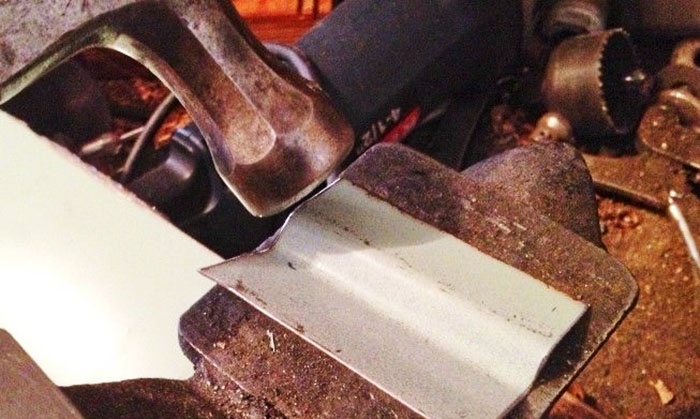
5. We fasten each bracket to its lining, having previously drilled two holes in them for screws, which we screw in using a hand screwdriver or drill with an appropriate bit.
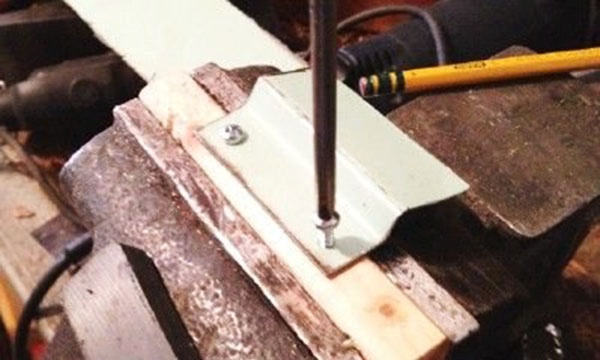
6.When the soft pads are not needed, they can be easily removed from the vice and stored with the magnets, attached to a metal surface in a hidden place until the next use.
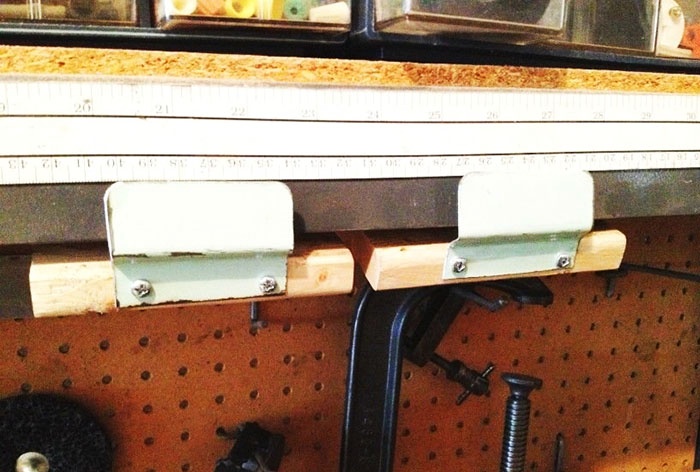
7. Our homemade pads will reliably protect the workpieces that we are going to clamp in a vice for marking or machining. Their fixation in the desired position is ensured by powerful magnets. The covers are quick and easy to install, as well as dismantle. Their production requires almost no costs, except for the purchase of magnets costing from 100 rubles.
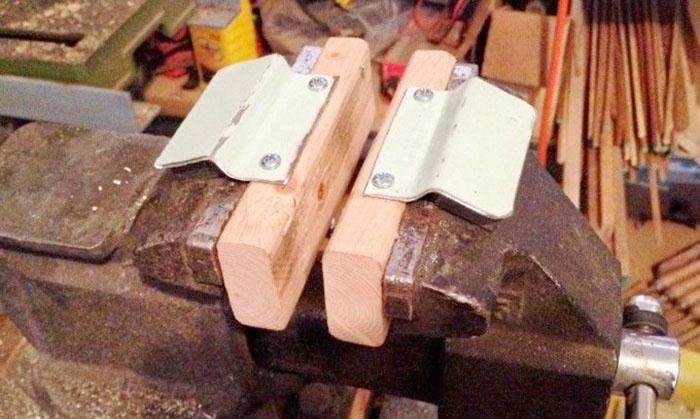
Similar master classes
Particularly interesting
Comments (0)