6 plumbing tricks
How to easily bend a propylene pipe using tin cans and bars
Draw a straight line on a sheet of multi-layer plywood or chipboard and attach one tin can so that it touches the line. We place the second jar in the same way on the other side of the line.
We lay a propylene pipe between the cans so that it touches them. In this position, we attach another jar to the sheet. On the outer sides of the cans, we also fix one wooden block at a distance of the diameter of the pipe. We heat the length of the pipe with a gas burner or a hot air gun and pass a flexible hose from the shower head through it.
We lay the pipe on the sheet between the bars and the cans. We speed up the cooling of the pipe with a rag soaked in cold water, and remove the pipe, smoothly bent in two places at an angle of 90 degrees.
We take out the flexible hose from the pipe.
How to make a bead on a propylene pipe under a metal American union nut
Using a machine for welding plastic pipes, we connect a plastic pipe with a coupling, the outer diameter of which is obviously larger than the diameter of the pipe.Taking into account the height of the union nut, we cut off most of the coupling with a hacksaw, and the remainder will serve as a collar with which the union nut will tightly press the pipe to the fitting or apparatus being connected.
How to increase a full-fledged bend of a plastic nut with a metal thread
In order to increase the bend of a plastic nut with a metal thread, we solder a piece of plastic pipe to it and, after waiting for the soldering area to cool, we cut off the excess, leaving only a small fragment.
Then we solder a bend onto it, the inner diameter of which coincides with the outer diameter of the previously soldered fragment.
How to cut internal and external threads on plastic pipes to connect them
To thread a connection between two plastic pipes of different diameters, you need to cut an internal thread in the larger diameter pipe, and an external thread in the smaller one. For this purpose, we install brass fittings with external and internal threads on the heating element of the machine for welding plastic pipes, and place a container of water next to it.
After heating the fittings, we form an internal thread in a pipe of larger diameter, marking a massive drill in it for heat removal. We wrap the end of the pipe around a brass fitting with an external thread and press on the pipe so that its end rests against the nut collar.
We keep the pipe in this position for some time and quickly cool the fitting and the end of the pipe in a container of water.
We unscrew the fitting and make sure that the internal thread in the pipe is formed. We form an external thread in a smaller diameter pipe in the same way. We screw a pipe with an external thread into a pipe with an internal thread and after tightening we obtain a strong and high-quality connection.
How to connect a plastic union nut to a larger diameter pipe
At the same time, we heat the end of the bend and the pipes on a machine for welding plastic pipes and press the bend inside the pipe.
After cooling, a reliable and completely sealed connection is obtained.
How to restore a flexible shower head hose with your own hands
Unscrew the union nut connecting the hose to the watering can. We remove the gasket and use a knife blade to press the inner bushing with the rubber tube mounted on it out of the outer one.
We pull out the rubber tube a little and find a break on it. We cut off the damaged area with scissors, put the rubber tube back on the bushing and press it into the outer one.
We put the gasket in place and screw the union nut onto the base of the watering can.
Watch the video
Similar master classes
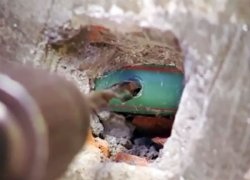

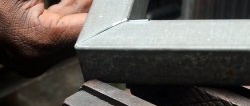
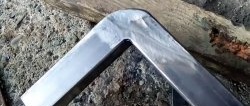
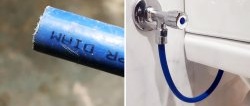
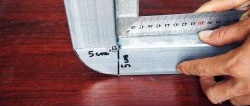