Cómo hacer un afilador complejo para afilar cuchillos de forma sencilla
Como todas las herramientas, los cuchillos requieren un cuidado adecuado, en particular un afilado de alta calidad, en el que es muy importante mantener un ángulo de afilado constante a lo largo de toda la hoja.
Por supuesto, esto no es difícil de lograr para un afilador experimentado incluso cuando trabaja manualmente. Para todos los demás, mantener el ángulo de afilado requerido será bastante difícil. ¿Seguirá siendo insoluble para ellos el problema de los cuchillos sin filo?
Hay tres formas de salir de esta situación: aprender a afilar cuchillos, pero esto requerirá mucho tiempo, paciencia y esfuerzo; recurra siempre a un profesional en busca de ayuda y pague por su costoso servicio; Haz tu propio afilador de cuchillos y no te preocupes por el ángulo de afilado.
A continuación consideraremos un método para fabricar un dispositivo para afilar cuchillos basado en un afilador eléctrico con dos muelas abrasivas.
Para que el trabajo no requiera mucho esfuerzo y tiempo, es bueno tener en stock: una máquina de soldar, máquinas (taladradora, fresadora y torneadora), una sierra pendular, un taladro, una amoladora, llaves, herramientas de marcado, etc.
Además del afilador eléctrico ya mencionado, es necesario abastecerse de materiales y componentes:
El trabajo constará de dos etapas relativamente independientes: disponer un afilador eléctrico y fabricar un portacuchillas que proporcione el ángulo de afilado requerido.
Una de las condiciones necesarias para un afilado de cuchillos de alta calidad es la estabilidad de la herramienta de afilado. Por eso, como base para un afilador eléctrico, utilizamos una chapa de metal de tamaño y grosor adecuados.
Con una cinta métrica, un núcleo y un martillo marcamos los centros de cuatro agujeros, repitiendo los agujeros de la placa del afilador eléctrico. Taladramos agujeros según las marcas de una perforadora y, utilizando tornillos y tuercas, fijamos el afilador eléctrico a una base de metal.
Con una sierra pendular, cortamos dos trozos de tubos cuadrados de longitud previamente calculada, y uno debe encajar libremente, pero sin dejar un gran espacio, en el otro.
En una tubería de sección transversal más pequeña, fresamos un orificio pasante en un extremo, cuyo diámetro debe ser ligeramente mayor que el diámetro de la varilla de metal. En el segundo tubo también marcamos y perforamos un agujero en un extremo para el perno de bloqueo.
Soldamos un tubo de mayor sección en el centro a la base, frente al afilador fijo, en una posición tal que el perno de fijación mire hacia afuera y quede arriba.Para evitar que las gotas de metal fundido, las chispas y las incrustaciones de la soldadura dañen el motor eléctrico, lo cubrimos con una manta de soldadura.
Insertamos la varilla en el orificio perforado en una tubería de una sección más pequeña estrictamente hasta el medio y la soldamos en esta posición a la tubería, habiendo verificado previamente la perpendicularidad de estas partes acopladas con un triángulo rectángulo.
Si esto no se ha hecho con antelación, retiramos el afilador eléctrico de la base e inspeccionamos la caja eléctrica, tras lo cual volvemos a instalar el afilador en su lugar y comprobamos su funcionalidad.
Insertamos el tubo con la varilla en el tubo soldado a la base y con la ayuda del perno podemos establecer la altura requerida para afilar un cuchillo en particular. Esta fue la última etapa de la disposición del afilador eléctrico. Comencemos la segunda fase de trabajo.
Para un afilador eléctrico, cambie la dirección de rotación.
Como ya se señaló, la calidad del afilado de un cuchillo depende, en primer lugar, de garantizar un ángulo de afilado constante. El soporte que vamos a realizar está diseñado precisamente para esto.
Marcamos la pieza de trabajo de metal de acuerdo con las dimensiones previstas de los tres elementos, lo que garantizará la captura y sujeción confiable de la hoja del cuchillo en un ángulo determinado con respecto a la superficie del círculo al afilar.
Los cortamos con una sierra pendular con el añadido de lubricante para mejorar la calidad del corte y la seguridad de la hoja de sierra.
Sujetamos los tres elementos en un "paquete" en el tornillo de banco de una fresadora y procesamos las superficies al tamaño requerido y, en cada cambio de posición, eliminamos las rebabas con una lima manual.
En dos espacios en blanco formamos mandíbulas para agarrar y sujetar la hoja del cuchillo. Para ello fresamos cada una de ellas a su tamaño por un lado.La tercera pieza se fresa por ambos lados a medida. Servirá de base para sujetarle empuñaduras laterales con mordazas.
En la parte que quedará en el medio, en la parte fresada hacemos marcas para dos agujeros, ubicados simétricamente al eje longitudinal más cerca de los bordes y ligeramente desplazados hacia la base. Los perforamos en una perforadora.
Tomando esta pieza como muestra, marcamos puntos de respuesta en las otras dos piezas utilizando un taladro y una broca fina.
Luego perforamos los lugares marcados con un taladro de gran diámetro hasta una pequeña profundidad (hacemos una especie de huecos para nidos).
En los orificios del elemento central atornillamos dos pasadores de la longitud requerida con la misma salida, que al instalar los elementos laterales encajarán en los huecos y los sujetarán, pero no interferirán con las mordazas, convergerán y divergirán.
En los elementos de las mordazas laterales, en el centro geométrico, marcamos y perforamos agujeros del mismo diámetro y con un grifo manual cortamos roscas en ellos.
Fresamos los bordes exteriores de las mandíbulas para completar la apariencia del dispositivo y la facilidad de uso. También retiramos los chaflanes de ambos lados en el extremo de fresado del elemento central para no interferir en el ajuste de las mordazas.
En el centro de la base del elemento central marcamos y perforamos un agujero ciego para el mandril.
Mezcle pegamento de dos componentes y utilícelo para fijar un mandril de la longitud requerida en el agujero ciego. Deje que el compuesto fragüe y se endurezca. Para ello fijamos el elemento central con el mandril en un tornillo de banco de madera.
Sujetamos una varilla de metal del diámetro calculado en el mandril del torno y perforamos un agujero en el centro un poco más grande que el diámetro del mandril, agregando periódicamente lubricante al área de perforación.
Luego cortamos el cilindro con una altura de aproximadamente 10-12 mm y perforamos un agujero en la superficie lateral, y luego cortamos la rosca con un macho para el tornillo de bloqueo.
En uno de los elementos laterales, desde el exterior, practicamos un agujero central para instalar la cabeza del cerrojo a ras de suelo.
Finalizamos las superficies del dispositivo procesándolo en una amoladora, primero con una banda de lijado sin fin y luego con una cinta de pelo.
Solo queda ensamblar los elementos del soporte ajustable atornillando el perno de conexión en las mordazas y fijando el anillo cilíndrico al mandril, instalándolo en el lugar correcto mediante un tornillo de bloqueo.
Sujetamos la hoja del cuchillo en las mordazas del soporte y ajustamos la altura requerida de la varilla transversal y la longitud del mandril moviendo el anillo cilíndrico hacia abajo o hacia arriba y bloqueándolo cuando sea necesario con un tornillo especial.
Para que el ángulo de afilado permanezca igual en toda la longitud de la hoja, basta con asegurarse de que un anillo cilíndrico montado en un mandril se deslice a lo largo de la superficie de una varilla instalada horizontalmente delante de las ruedas del afilador eléctrico.
Después de un breve afilado sin tensión, el cuchillo corta fácilmente una hoja de papel de escribir, lo que confirma su excelente afilado.
Por supuesto, esto no es difícil de lograr para un afilador experimentado incluso cuando trabaja manualmente. Para todos los demás, mantener el ángulo de afilado requerido será bastante difícil. ¿Seguirá siendo insoluble para ellos el problema de los cuchillos sin filo?
Hay tres formas de salir de esta situación: aprender a afilar cuchillos, pero esto requerirá mucho tiempo, paciencia y esfuerzo; recurra siempre a un profesional en busca de ayuda y pague por su costoso servicio; Haz tu propio afilador de cuchillos y no te preocupes por el ángulo de afilado.
A continuación consideraremos un método para fabricar un dispositivo para afilar cuchillos basado en un afilador eléctrico con dos muelas abrasivas.
Necesitará
Para que el trabajo no requiera mucho esfuerzo y tiempo, es bueno tener en stock: una máquina de soldar, máquinas (taladradora, fresadora y torneadora), una sierra pendular, un taladro, una amoladora, llaves, herramientas de marcado, etc.
Además del afilador eléctrico ya mencionado, es necesario abastecerse de materiales y componentes:
- chapa de metal de 10 mm de espesor;
- tubos cuadrados (dos piezas de tamaños adyacentes);
- una varilla de metal redonda de hasta 400 mm de largo y 15-20 mm de diámetro;
- sujetadores roscados (pernos, tuercas, arandelas), etc.
Hacer un afilador de cuchillos
El trabajo constará de dos etapas relativamente independientes: disponer un afilador eléctrico y fabricar un portacuchillas que proporcione el ángulo de afilado requerido.
Disposición del afilador.
Una de las condiciones necesarias para un afilado de cuchillos de alta calidad es la estabilidad de la herramienta de afilado. Por eso, como base para un afilador eléctrico, utilizamos una chapa de metal de tamaño y grosor adecuados.
Con una cinta métrica, un núcleo y un martillo marcamos los centros de cuatro agujeros, repitiendo los agujeros de la placa del afilador eléctrico. Taladramos agujeros según las marcas de una perforadora y, utilizando tornillos y tuercas, fijamos el afilador eléctrico a una base de metal.
Con una sierra pendular, cortamos dos trozos de tubos cuadrados de longitud previamente calculada, y uno debe encajar libremente, pero sin dejar un gran espacio, en el otro.
En una tubería de sección transversal más pequeña, fresamos un orificio pasante en un extremo, cuyo diámetro debe ser ligeramente mayor que el diámetro de la varilla de metal. En el segundo tubo también marcamos y perforamos un agujero en un extremo para el perno de bloqueo.
Soldamos un tubo de mayor sección en el centro a la base, frente al afilador fijo, en una posición tal que el perno de fijación mire hacia afuera y quede arriba.Para evitar que las gotas de metal fundido, las chispas y las incrustaciones de la soldadura dañen el motor eléctrico, lo cubrimos con una manta de soldadura.
Insertamos la varilla en el orificio perforado en una tubería de una sección más pequeña estrictamente hasta el medio y la soldamos en esta posición a la tubería, habiendo verificado previamente la perpendicularidad de estas partes acopladas con un triángulo rectángulo.
Si esto no se ha hecho con antelación, retiramos el afilador eléctrico de la base e inspeccionamos la caja eléctrica, tras lo cual volvemos a instalar el afilador en su lugar y comprobamos su funcionalidad.
Insertamos el tubo con la varilla en el tubo soldado a la base y con la ayuda del perno podemos establecer la altura requerida para afilar un cuchillo en particular. Esta fue la última etapa de la disposición del afilador eléctrico. Comencemos la segunda fase de trabajo.
Para un afilador eléctrico, cambie la dirección de rotación.
Hacer un portacuchillas
Como ya se señaló, la calidad del afilado de un cuchillo depende, en primer lugar, de garantizar un ángulo de afilado constante. El soporte que vamos a realizar está diseñado precisamente para esto.
Marcamos la pieza de trabajo de metal de acuerdo con las dimensiones previstas de los tres elementos, lo que garantizará la captura y sujeción confiable de la hoja del cuchillo en un ángulo determinado con respecto a la superficie del círculo al afilar.
Los cortamos con una sierra pendular con el añadido de lubricante para mejorar la calidad del corte y la seguridad de la hoja de sierra.
Sujetamos los tres elementos en un "paquete" en el tornillo de banco de una fresadora y procesamos las superficies al tamaño requerido y, en cada cambio de posición, eliminamos las rebabas con una lima manual.
En dos espacios en blanco formamos mandíbulas para agarrar y sujetar la hoja del cuchillo. Para ello fresamos cada una de ellas a su tamaño por un lado.La tercera pieza se fresa por ambos lados a medida. Servirá de base para sujetarle empuñaduras laterales con mordazas.
En la parte que quedará en el medio, en la parte fresada hacemos marcas para dos agujeros, ubicados simétricamente al eje longitudinal más cerca de los bordes y ligeramente desplazados hacia la base. Los perforamos en una perforadora.
Tomando esta pieza como muestra, marcamos puntos de respuesta en las otras dos piezas utilizando un taladro y una broca fina.
Luego perforamos los lugares marcados con un taladro de gran diámetro hasta una pequeña profundidad (hacemos una especie de huecos para nidos).
En los orificios del elemento central atornillamos dos pasadores de la longitud requerida con la misma salida, que al instalar los elementos laterales encajarán en los huecos y los sujetarán, pero no interferirán con las mordazas, convergerán y divergirán.
En los elementos de las mordazas laterales, en el centro geométrico, marcamos y perforamos agujeros del mismo diámetro y con un grifo manual cortamos roscas en ellos.
Fresamos los bordes exteriores de las mandíbulas para completar la apariencia del dispositivo y la facilidad de uso. También retiramos los chaflanes de ambos lados en el extremo de fresado del elemento central para no interferir en el ajuste de las mordazas.
En el centro de la base del elemento central marcamos y perforamos un agujero ciego para el mandril.
Mezcle pegamento de dos componentes y utilícelo para fijar un mandril de la longitud requerida en el agujero ciego. Deje que el compuesto fragüe y se endurezca. Para ello fijamos el elemento central con el mandril en un tornillo de banco de madera.
Sujetamos una varilla de metal del diámetro calculado en el mandril del torno y perforamos un agujero en el centro un poco más grande que el diámetro del mandril, agregando periódicamente lubricante al área de perforación.
Luego cortamos el cilindro con una altura de aproximadamente 10-12 mm y perforamos un agujero en la superficie lateral, y luego cortamos la rosca con un macho para el tornillo de bloqueo.
En uno de los elementos laterales, desde el exterior, practicamos un agujero central para instalar la cabeza del cerrojo a ras de suelo.
Finalizamos las superficies del dispositivo procesándolo en una amoladora, primero con una banda de lijado sin fin y luego con una cinta de pelo.
Solo queda ensamblar los elementos del soporte ajustable atornillando el perno de conexión en las mordazas y fijando el anillo cilíndrico al mandril, instalándolo en el lugar correcto mediante un tornillo de bloqueo.
Prueba de fijación
Sujetamos la hoja del cuchillo en las mordazas del soporte y ajustamos la altura requerida de la varilla transversal y la longitud del mandril moviendo el anillo cilíndrico hacia abajo o hacia arriba y bloqueándolo cuando sea necesario con un tornillo especial.
Para que el ángulo de afilado permanezca igual en toda la longitud de la hoja, basta con asegurarse de que un anillo cilíndrico montado en un mandril se deslice a lo largo de la superficie de una varilla instalada horizontalmente delante de las ruedas del afilador eléctrico.
Después de un breve afilado sin tensión, el cuchillo corta fácilmente una hoja de papel de escribir, lo que confirma su excelente afilado.
Ver el vídeo
Clases magistrales similares
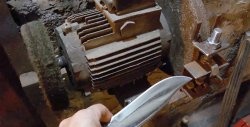
El dispositivo más sencillo para afilar cuchillos a 30 grados.
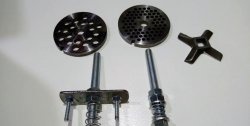
Dispositivo para afilar cuchillos para picar carne.
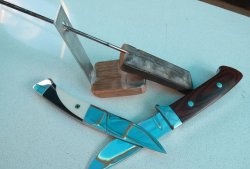
Una herramienta sencilla para afilar cuchillos en un ángulo fijo.

Cómo afilar fácilmente los cuchillos de una picadora de carne
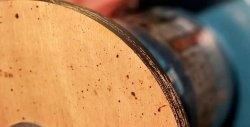
Usamos un disco de madera para afilar cuchillos rápidamente.
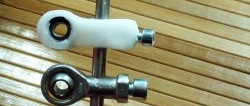
Cómo hacer rápidamente una bisagra para un afilador de cuchillos.
Particularmente interesante
Comentarios (5)