Cómo hacer un potente cuchillo de palanca para metal.
Este producto casero corta barras de metal de forma más rápida y sencilla que una sierra manual para metal. Su producción no requiere materiales especiales, equipos especiales ni altas calificaciones.
Antes de comenzar a trabajar, prepararemos los siguientes materiales y productos:
Realizamos la base casera a partir de dos esquinas de acero de 50 × 50 × 6 mm y 400 mm de largo. Los colocamos en estantes verticalmente sobre una superficie plana, cerramos los horizontales a lo largo y los preparamos.
Cerramos un extremo verticalmente con una placa de acero, por el otro hacemos un bisel con una amoladora y también soldamos la placa.
Limpiamos y rectificamos las soldaduras.
En los extremos inferiores de la base soldamos placas rectangulares de 8 mm de espesor con un saliente de 10 mm en todo el perímetro.
Procesamos dos círculos de acero de grado 40ХГМ con un diámetro de 100 mm y una altura de 35 mm.Las recortamos y trituramos al tamaño requerido. En un extremo hacemos un bisel ancho y perforamos un agujero en el centro.
Para procesar las piezas de trabajo juntas, las soldamos en dos lugares, conectándolas y centrándolas.
A lo largo de la parte superior del bisel, colocamos núcleos a una distancia de 35 mm a lo largo de la cuerda; estos son los centros de futuros orificios con un diámetro de 16 y 11 mm, hechos en una máquina perforadora. Con una escuadra y un trazador, trazamos líneas tangentes radiales desde los agujeros perforados hasta el central en los dos extremos y las conectamos a lo largo de una generatriz.
Con una amoladora, cortamos dos ranuras radiales según las marcas desde la superficie de los círculos hasta el orificio correspondiente. Pulimos las ranuras con una lima manual y retiramos los puntos soldados.
Calentamos los espacios en blanco en el horno hasta que estén rojos y los bajamos rápidamente a un frasco de aceite. Los dejamos ahí un rato, luego los sacamos y los enfriamos al aire.
Limpiamos los círculos de depósitos oscuros y aplicamos uno de ellos sobre una placa rectangular de 80 × 50 × 20 mm para que la generatriz del círculo conecte las esquinas. Usando un marcador en la placa, dibujamos un arco circular de esquina a esquina y cortamos un hueco con una amoladora.
Instalamos la placa en la esquina de la base paralela al lado largo y la soldamos allí. Colocamos uno de los círculos en el hueco, dirigiendo la ranura ancha hacia arriba y también lo soldamos.
Comencemos a ensamblar la palanca de accionamiento. En una placa de acero de 230 × 45 mm perforamos un agujero de 12 mm desde un borde, y en el otro hacemos un hueco para el diámetro exterior del círculo y lo soldamos allí.
En dos placas de acero de 12 mm de espesor, 180 mm de largo y 50 mm de ancho en un extremo y 35 mm en el otro, taladre un orificio de 12 mm desde el lado estrecho. En una placa del mismo espesor, de 250 mm de largo y 45 mm de ancho, hacemos dos agujeros de 12 mm y uno de 25 mm según las marcas.
Mediante perno, arandelas y tuerca ensamblamos estas tres piezas, colocando entre dos cortas una placa larga, que colocamos con sus extremos anchos sobre la base y soldamos.
Utilizando un par de placas de 110 × 25 mm con dos orificios de 12 mm en los extremos, conectamos la palanca del círculo móvil con la palanca del accionamiento manual.
En su extremo, hasta el orificio grande, cortamos una ranura con una amoladora, insertamos una varilla-palanca de acero con una muesca en el extremo y la aseguramos mediante soldadura.
Pintamos las partes fijas de un color y las móviles de otro.
Una vez seca la pintura, montamos y probamos el dispositivo en funcionamiento, cortando varillas, refuerzos y placas.
Además, colocamos material fino en una ranura estrecha y material grueso en una ancha.
Necesitará
Antes de comenzar a trabajar, prepararemos los siguientes materiales y productos:
- Igual ángulo;
- chapas de diversos espesores;
- círculo de acero;
- aceite de enfriamiento;
- barra de acero;
- pernos, tuercas, arandelas;
- pintar en dos colores.
- También necesitará una máquina de soldar, tornos y taladradoras, una amoladora, una lima, un horno para calentar metal, llaves inglesas, una pistola rociadora, etc.
Proceso de fabricación de cuchillos
Realizamos la base casera a partir de dos esquinas de acero de 50 × 50 × 6 mm y 400 mm de largo. Los colocamos en estantes verticalmente sobre una superficie plana, cerramos los horizontales a lo largo y los preparamos.
Cerramos un extremo verticalmente con una placa de acero, por el otro hacemos un bisel con una amoladora y también soldamos la placa.
Limpiamos y rectificamos las soldaduras.
En los extremos inferiores de la base soldamos placas rectangulares de 8 mm de espesor con un saliente de 10 mm en todo el perímetro.
Procesamos dos círculos de acero de grado 40ХГМ con un diámetro de 100 mm y una altura de 35 mm.Las recortamos y trituramos al tamaño requerido. En un extremo hacemos un bisel ancho y perforamos un agujero en el centro.
Para procesar las piezas de trabajo juntas, las soldamos en dos lugares, conectándolas y centrándolas.
A lo largo de la parte superior del bisel, colocamos núcleos a una distancia de 35 mm a lo largo de la cuerda; estos son los centros de futuros orificios con un diámetro de 16 y 11 mm, hechos en una máquina perforadora. Con una escuadra y un trazador, trazamos líneas tangentes radiales desde los agujeros perforados hasta el central en los dos extremos y las conectamos a lo largo de una generatriz.
Con una amoladora, cortamos dos ranuras radiales según las marcas desde la superficie de los círculos hasta el orificio correspondiente. Pulimos las ranuras con una lima manual y retiramos los puntos soldados.
Calentamos los espacios en blanco en el horno hasta que estén rojos y los bajamos rápidamente a un frasco de aceite. Los dejamos ahí un rato, luego los sacamos y los enfriamos al aire.
Limpiamos los círculos de depósitos oscuros y aplicamos uno de ellos sobre una placa rectangular de 80 × 50 × 20 mm para que la generatriz del círculo conecte las esquinas. Usando un marcador en la placa, dibujamos un arco circular de esquina a esquina y cortamos un hueco con una amoladora.
Instalamos la placa en la esquina de la base paralela al lado largo y la soldamos allí. Colocamos uno de los círculos en el hueco, dirigiendo la ranura ancha hacia arriba y también lo soldamos.
Comencemos a ensamblar la palanca de accionamiento. En una placa de acero de 230 × 45 mm perforamos un agujero de 12 mm desde un borde, y en el otro hacemos un hueco para el diámetro exterior del círculo y lo soldamos allí.
En dos placas de acero de 12 mm de espesor, 180 mm de largo y 50 mm de ancho en un extremo y 35 mm en el otro, taladre un orificio de 12 mm desde el lado estrecho. En una placa del mismo espesor, de 250 mm de largo y 45 mm de ancho, hacemos dos agujeros de 12 mm y uno de 25 mm según las marcas.
Mediante perno, arandelas y tuerca ensamblamos estas tres piezas, colocando entre dos cortas una placa larga, que colocamos con sus extremos anchos sobre la base y soldamos.
Utilizando un par de placas de 110 × 25 mm con dos orificios de 12 mm en los extremos, conectamos la palanca del círculo móvil con la palanca del accionamiento manual.
En su extremo, hasta el orificio grande, cortamos una ranura con una amoladora, insertamos una varilla-palanca de acero con una muesca en el extremo y la aseguramos mediante soldadura.
Pintamos las partes fijas de un color y las móviles de otro.
Una vez seca la pintura, montamos y probamos el dispositivo en funcionamiento, cortando varillas, refuerzos y placas.
Además, colocamos material fino en una ranura estrecha y material grueso en una ancha.
Ver el vídeo
Clases magistrales similares
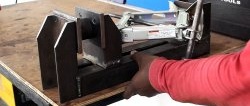
Cómo hacer un tornillo de banco potente con un martinete de diamante
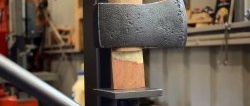
Cómo hacer una prensa hidráulica con un gato de botella.
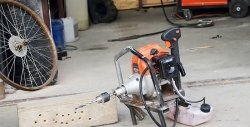
Taladro motorizado de una recortadora con sus propias manos.
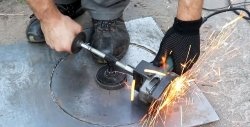
Dispositivo extraíble para cortar círculos en chapa con
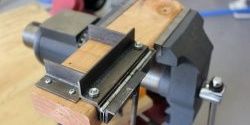
Cómo hacer una mini máquina dobladora de metal.
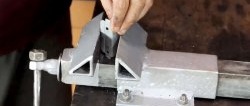
Cómo hacer un tornillo de banco confiable con restos de metal
Particularmente interesante
Comentarios (1)