Mechanical converter
Modern man is accustomed to using electrical energy everywhere. It's hard for us to imagine the absence of electricity, on which most of our meaningful lives are based. But have you ever wondered where it comes from? What moves invisible particles, making them work for the benefit of humans?
The ancient Greeks already guessed about the presence of an invisible force that sets certain objects in motion. However, the real dawn of this topic occurred only during the period of industrialization of the 19th century. It was then that the famous scientist Michael Faraday discovered the phenomenon of electromagnetic induction, which explains the occurrence of electric current in a magnetic field when a conductor moves in it. Today we invite you to test this theory experimentally.
The essence of the experiment is the manufacture of an electromechanical converter based on a DC motor, which will rotate magnets located in the frame of the inductor. As a result of the excitation of magnetic fields and the appearance of electromagnetic emf at the output, we obtain an electric current.The experience is also interesting because the voltage values obtained will be greater than those spent on operating the engine. But first things first.
The tools we need for work are: a soldering iron with solder, a lighter, a knife, and pliers with pliers. A tester will be needed for those who want to measure the output voltage on the converter.
We make two small stator frames from a steel rod. Use pliers to bend the outline and cut off the excess. The ends of the coils should also be bent (photo).
We connect the frames with superglue and put heat shrink on the middle. We warm it up with a lighter, and thus get an insulated coil core.
For winding we use thin copper wire in varnished insulation. It must be wound around the insulator area. Number of turns – 600.
Upon completion of the winding, we leave two ends of the coil - the initial and final ones. We remove the insulation by burning it with a regular lighter. This will be the stator.
On the motor shaft we attach a pair of guides made of pieces of plastic for neodymium magnets using superglue. We place them on opposite sides of the shaft to increase the area of contact with the magnets.
We attach neodymium magnets to the shaft using superglue. Please note that they can only connect if they are of different polarities. This will be the rotor of our converter.
We cut two strips of thin plastic to the size of the engine and frame. They can be slightly bent by heating the middle with a lighter.
Glue the strips to the engine body. Next, we fix the stator frame so that its open ends, without touching the magnets, are placed in the center of the rotor.
Our simplest microconverter is ready. All that remains is to connect the motor, soldering its ends with contacts, and supplement the entire circuit with a power supply. A regular 3.7 V lithium battery from a laptop is suitable as a power supply.
Measurements with a tester show an output voltage that is an order of magnitude higher than the input voltage, which means this circuit is quite working.
In fairness, it is worth noting that electromechanical converters became a thing of the past with the advent of electronic microcircuits and transistors. Today you can purchase ready-made voltage boosting modules that allow you to get high performance of about 50 V from a conventional 3.2 -3.7 V battery. They are silent, compact and rational, because with their help you can power 12 and 24 V devices such as , like coolers and stepper motors with just one battery!
The ancient Greeks already guessed about the presence of an invisible force that sets certain objects in motion. However, the real dawn of this topic occurred only during the period of industrialization of the 19th century. It was then that the famous scientist Michael Faraday discovered the phenomenon of electromagnetic induction, which explains the occurrence of electric current in a magnetic field when a conductor moves in it. Today we invite you to test this theory experimentally.
The essence of the experiment is the manufacture of an electromechanical converter based on a DC motor, which will rotate magnets located in the frame of the inductor. As a result of the excitation of magnetic fields and the appearance of electromagnetic emf at the output, we obtain an electric current.The experience is also interesting because the voltage values obtained will be greater than those spent on operating the engine. But first things first.
Materials – Tools
- 3V DC motor;
- Neodymium square magnets 10x8 mm;
- Steel rod with a cross section of 2-3 mm;
- Copper wire in varnished insulation;
- Pieces of plastic;
- 3.7 V battery;
- Copper wiring, heat shrink;
- Super glue.
The tools we need for work are: a soldering iron with solder, a lighter, a knife, and pliers with pliers. A tester will be needed for those who want to measure the output voltage on the converter.
Assembling an electromechanical voltage converter
We make two small stator frames from a steel rod. Use pliers to bend the outline and cut off the excess. The ends of the coils should also be bent (photo).
We connect the frames with superglue and put heat shrink on the middle. We warm it up with a lighter, and thus get an insulated coil core.
For winding we use thin copper wire in varnished insulation. It must be wound around the insulator area. Number of turns – 600.
Upon completion of the winding, we leave two ends of the coil - the initial and final ones. We remove the insulation by burning it with a regular lighter. This will be the stator.
On the motor shaft we attach a pair of guides made of pieces of plastic for neodymium magnets using superglue. We place them on opposite sides of the shaft to increase the area of contact with the magnets.
We attach neodymium magnets to the shaft using superglue. Please note that they can only connect if they are of different polarities. This will be the rotor of our converter.
We cut two strips of thin plastic to the size of the engine and frame. They can be slightly bent by heating the middle with a lighter.
Glue the strips to the engine body. Next, we fix the stator frame so that its open ends, without touching the magnets, are placed in the center of the rotor.
Our simplest microconverter is ready. All that remains is to connect the motor, soldering its ends with contacts, and supplement the entire circuit with a power supply. A regular 3.7 V lithium battery from a laptop is suitable as a power supply.
Measurements with a tester show an output voltage that is an order of magnitude higher than the input voltage, which means this circuit is quite working.
Conclusion
In fairness, it is worth noting that electromechanical converters became a thing of the past with the advent of electronic microcircuits and transistors. Today you can purchase ready-made voltage boosting modules that allow you to get high performance of about 50 V from a conventional 3.2 -3.7 V battery. They are silent, compact and rational, because with their help you can power 12 and 24 V devices such as , like coolers and stepper motors with just one battery!
Watch the video
Similar master classes
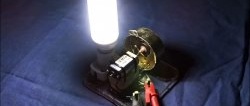
Mechanical converter from a microwave oven motor
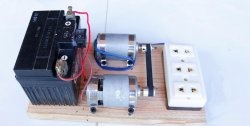
Mechanical converter 12 - 220 V
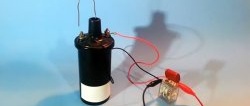
How to make a simple high voltage converter from
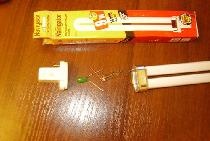
A simple converter for powering energy-saving lamps
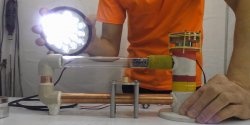
An electric generator based on a thermoacoustic engine is not
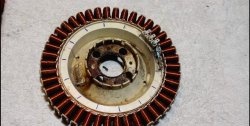
Electric generator - conversion of a washing machine engine
Particularly interesting
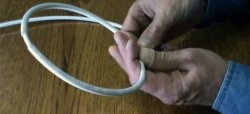
Cable antenna for digital TV in 5 minutes
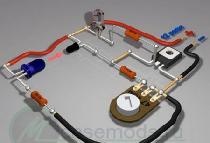
A selection of simple and effective schemes.
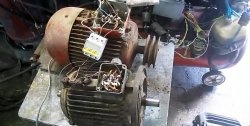
Three-phase voltage from single-phase in 5 minutes
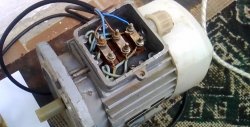
Starting a three-phase motor from a single-phase network without a capacitor
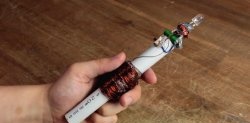
Eternal flashlight without batteries
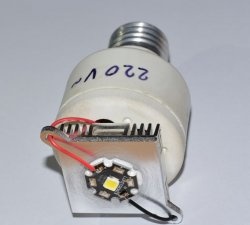
How to make an inexpensive but very powerful LED lamp
Comments (5)