Thin soldering iron tip
If you decide to repair broken headphones, a Bluetooth headset, or any other device that has a thin and small microcircuit, you will need a soldering iron with a thin tip. But sometimes it happens that this very sting, due to some circumstances, is not at hand. You can, of course, go to the nearest specialized store and buy what you need, but it is not a fact that the tool you need will be available there. Or you can get creative and do everything with an ordinary, standard sting. But why take the risk and suffer when a thin sting can be made in literally five minutes, without leaving home, from materials that are available in almost any person’s barn or pantry. We will prepare the required materials and begin production.
Required:- Copper wire, tip thickness required.
- Aluminium foil.
- Pliers.
- File.
- Wire cutters.
- Scissors.
- A tube from an indoor antenna, or any other, made of any metal, suitable in size for the soldering iron hole.
Making a thin soldering tip
Everything is indecently simple, but reliable and effective. Using wire cutters, we separate the length of copper wire we need.Using scissors, cut off a long strip of aluminum foil, the width of which is less than the piece of wire you have chosen, exactly as much as the tip should stick out of the soldering iron. Using a file, we give the tip of the wire, which will be the tip itself, the tip shape you need.
We wrap the foil on the wire to the thickness of the inner diameter of the tube you have.
The foil should be wound as tightly as possible, the speed of heating of the tip depends on this - the tighter the fit of the layers to each other, the faster it will heat up. Using a file or needle file, cut off a piece of tube equal in width to the width of the foil wound on the wire.
Now we insert the wire wrapped in foil into the tube.
The tighter this design is, the better. To secure the stability of the wire inside the tube with foil, using a knife blade or scissors, bend the edges of the tube inward, as if clogging it inside.
If you couldn’t find a suitable tube, simply wind the foil to the thickness of a standard tip and wrap it with thin copper wire. Well, we insert a new tip into the soldering iron!
The effectiveness of such a sting is no lower than that of a sting bought in a store. Before connecting the device to the power supply, dip the sharpened tip of the tip into soldering acid so that solder can stick to it without any problems.
Now you can use it. But do not forget that this is only a temporary way out of the current situation. You can use this design two or three times. Not more. Then, when the foil inside the tube burns out, the heating of the device will be much longer than usual, and the tip-wire will begin to fall out of the tube, so if possible, still buy a real tip at the store.
Similar master classes
Particularly interesting
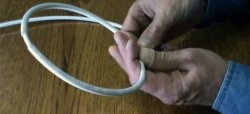
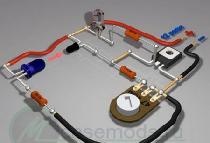
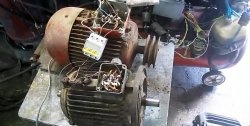
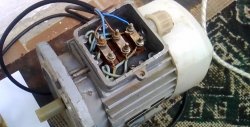
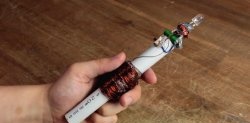
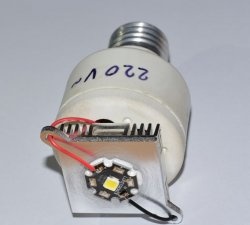