How to make a reliable electrode holder
Anyone who has ever dealt with welding has probably paid attention to the clamping of the electrode - one awkward movement, and the rod changes angle, or may even fall out. Of course, professional welders do not encounter such situations, but an amateur would like something more reliable - rigid fixation of the electrode will allow him to perform welding work efficiently and accurately.
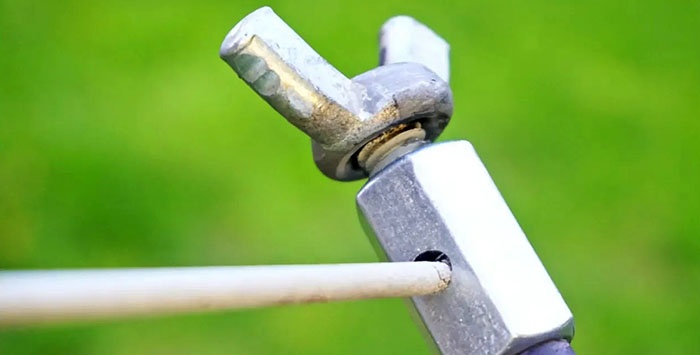
First of all, mark the center of the elongated nut, and then clamp it in a vice. Using a conventional drill, drill a through hole. The drill diameter should be about 1/3 larger than the possible electrode thickness of .6-8 mm. Make sure that the drill is strictly perpendicular to the edge of the nut.
Then we clamp the bolt in a vice and use a grinder to cut off the head. We weld a wing nut in this place.The length of the free thread must be no less than the distance from the edge of the long nut to the center of the hole made.
We unscrew the handle from a non-working angle grinder, drill or other similar tool.
The inner bolt is easily knocked out.
We clamp it in a vice and drill a hole for our stud.
Now you can start assembling.
We screw the stud and the wing bolt into the wide nut so that they do not reach the edge of the hole made.
Next, we insert the entire structure into the handle and visually mark the place to which the fixing nut is to be tightened.
Then we twist the double nut, and on the opposite side we install the nut to the desired depth. We wind the wire going to the welding machine and clamp it with another nut, using two open-end wrenches for this.
We place the pin with the wire inside the handle and finally fix it with a double nut from the outside. Insert the electrode into the hole and tighten the wing bolt with a little force. Now you can start welding.
Throughout all the work, tools such as a drill, grinder and welding machine were used. All of them require increased attention, since failure to comply with basic safety rules and neglect of personal protective equipment (work gloves, goggles, welding mask and long-sleeved clothing made of non-flammable materials) can cause injuries, sometimes quite serious.
Having carried out test welding, I can say with confidence that our homemade holder is a full replacement for industrial analogues.It securely fixes the electrode, and in cases of sticking it is quite easy to detach it from the surface to be welded (in the factory handle it often jumps out of the clamp and remains welded to the workpiece).
The only drawback can be considered the fact that this handle is made of plastic, albeit durable. During prolonged use, heating occurs in any case, and the handle may become deformed. Otherwise, it turned out to be an excellent handle, the cost of which is three nuts and two bolts.
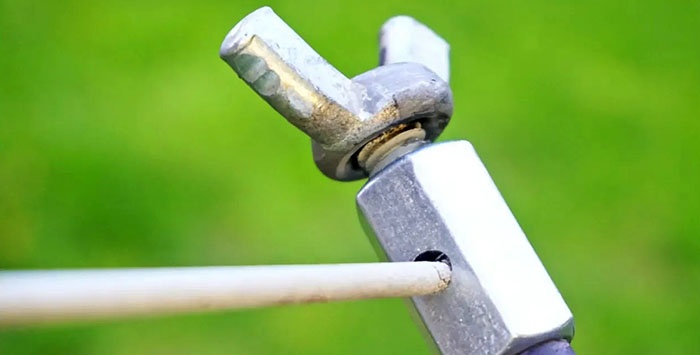
What materials will you need?
- Bolt (35 mm) and stud (70 mm) with thread 12;
- Extended nut (25-30 mm);
- Two regular nuts;
- Coupling nut (wing);
- Plastic holder (side handle) for an angle grinder.
Preparatory work
First of all, mark the center of the elongated nut, and then clamp it in a vice. Using a conventional drill, drill a through hole. The drill diameter should be about 1/3 larger than the possible electrode thickness of .6-8 mm. Make sure that the drill is strictly perpendicular to the edge of the nut.
Then we clamp the bolt in a vice and use a grinder to cut off the head. We weld a wing nut in this place.The length of the free thread must be no less than the distance from the edge of the long nut to the center of the hole made.
We unscrew the handle from a non-working angle grinder, drill or other similar tool.
The inner bolt is easily knocked out.
We clamp it in a vice and drill a hole for our stud.
Now you can start assembling.
Assembly of an exclusive reliable electrode holder
We screw the stud and the wing bolt into the wide nut so that they do not reach the edge of the hole made.
Next, we insert the entire structure into the handle and visually mark the place to which the fixing nut is to be tightened.
Then we twist the double nut, and on the opposite side we install the nut to the desired depth. We wind the wire going to the welding machine and clamp it with another nut, using two open-end wrenches for this.
We place the pin with the wire inside the handle and finally fix it with a double nut from the outside. Insert the electrode into the hole and tighten the wing bolt with a little force. Now you can start welding.
What you shouldn't forget
Throughout all the work, tools such as a drill, grinder and welding machine were used. All of them require increased attention, since failure to comply with basic safety rules and neglect of personal protective equipment (work gloves, goggles, welding mask and long-sleeved clothing made of non-flammable materials) can cause injuries, sometimes quite serious.
Trial
Having carried out test welding, I can say with confidence that our homemade holder is a full replacement for industrial analogues.It securely fixes the electrode, and in cases of sticking it is quite easy to detach it from the surface to be welded (in the factory handle it often jumps out of the clamp and remains welded to the workpiece).
The only drawback can be considered the fact that this handle is made of plastic, albeit durable. During prolonged use, heating occurs in any case, and the handle may become deformed. Otherwise, it turned out to be an excellent handle, the cost of which is three nuts and two bolts.
Watch the video
Similar master classes
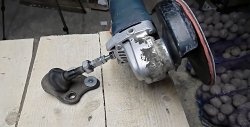
Movable bracket for attaching an angle grinder from a ball joint
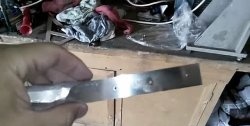
How to burn a hole in hardened steel
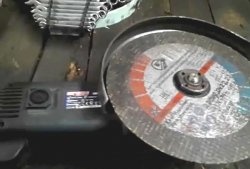
A simple modification to the grinder for easy unscrewing of the nut
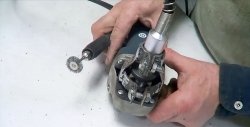
If your Dremel breaks, it doesn’t matter: a grinder can replace it
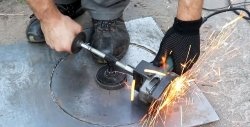
Removable device for cutting circles in sheet metal with
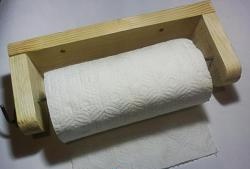
Paper towel holder
Particularly interesting
Comments (18)