Drilling machine centering attachment for precision drilling
If it is necessary to drill a central hole on a part that will rotate, a lathe is usually used. In this case, the drill is clamped motionless, and the workpiece itself is pushed onto it. However, not everyone has a lathe, and there is no desire to turn to a lathe every time for small things. To center small parts, you can make an attachment to the drilling machine from a regular drill chuck, and do similar work yourself.
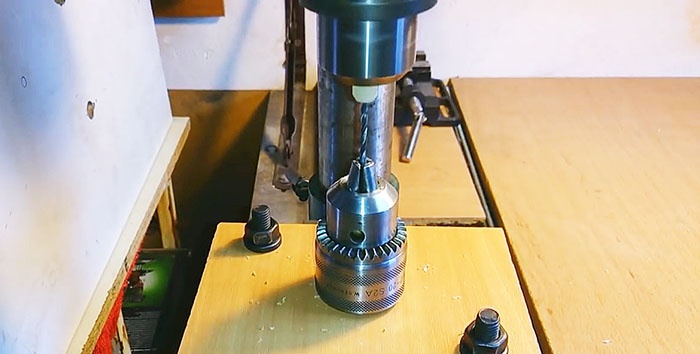
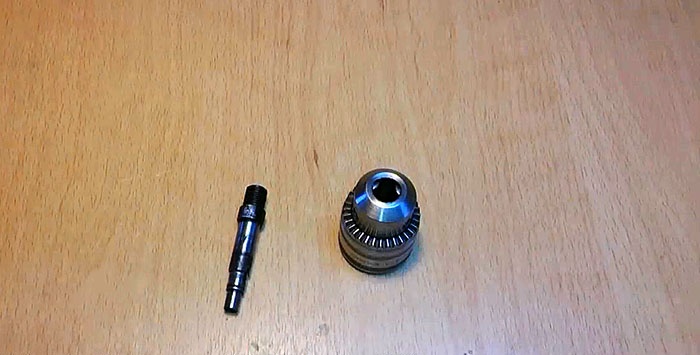
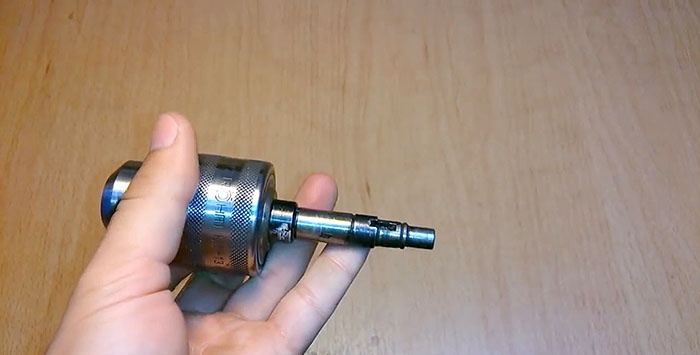
In my case, the attachment will be made from a jaw chuck with a shaft. If you don’t have an old drill to disassemble, you can simply buy a chuck with an SDS-plus adapter. You need to cut the shaft or adapter using any available method. It should be shortened so that a tail comes out of the cartridge corresponding to the thickness of the available chipboard. Using an engraver, I cut the shaft at the 18mm mark.
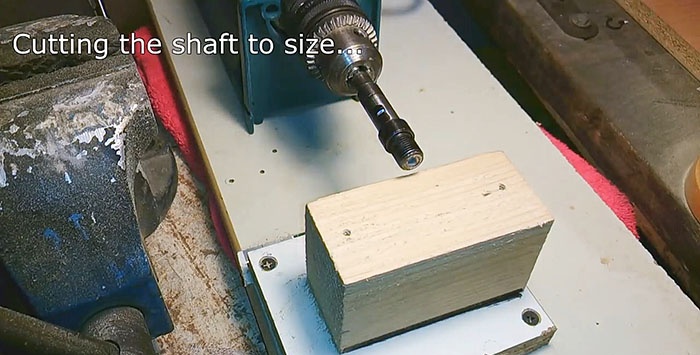
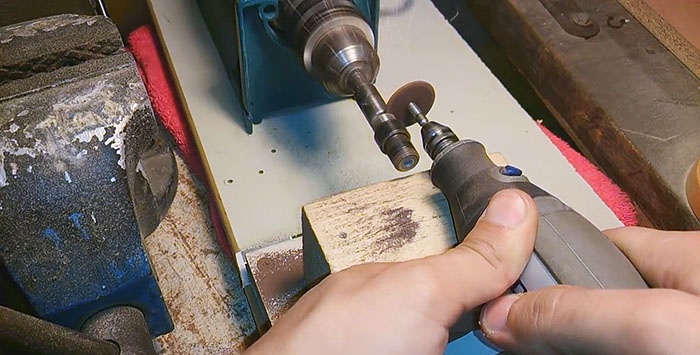
Next you need to take chipboard. It will be used as a stand on the drilling machine table.The size of the workpiece is determined individually, but 15x20 cm is enough. The center is marked on the chipboard. To find it, draw diagonals between the corners.

At the point of their intersection, a hole is drilled 1 mm larger than the thickness of the cut tail of the adapter or shaft.
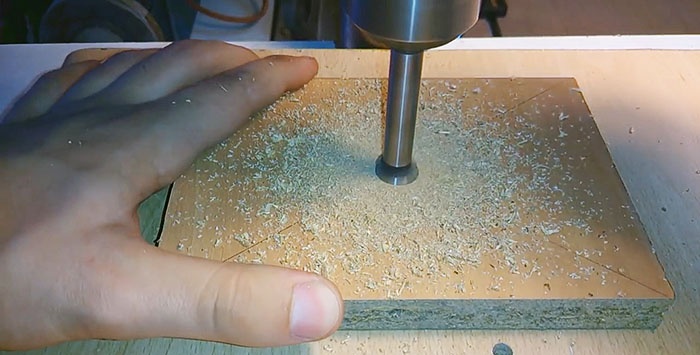
The hole is coated with epoxy glue, after which the cartridge holder is pressed into it. All you have to do is wait until the epoxy hardens.
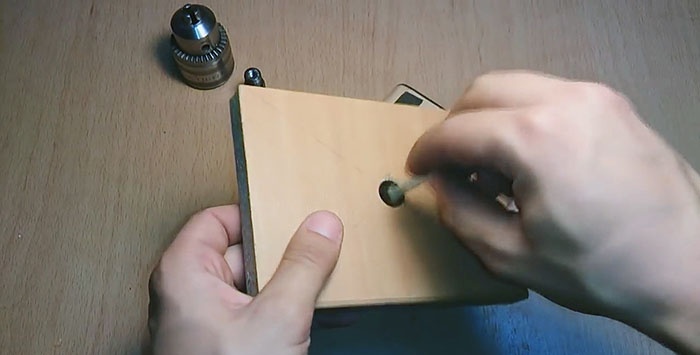
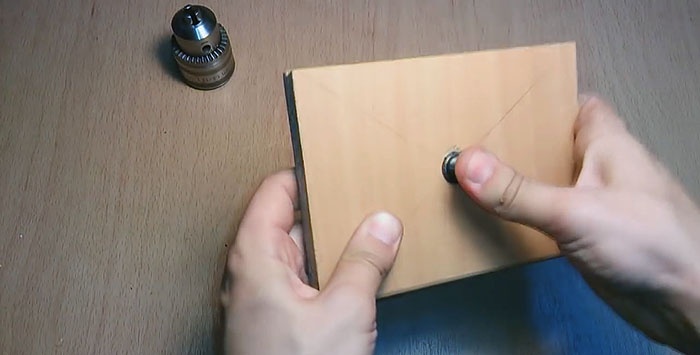
The chipboard with the shaft is placed on the machine table and holes are marked to fix it. It is enough to drill 2 holes diagonally.
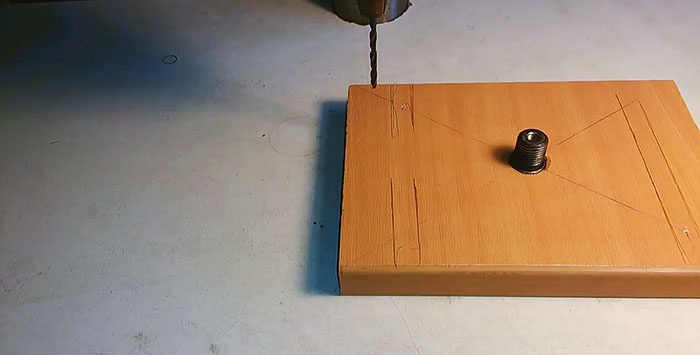
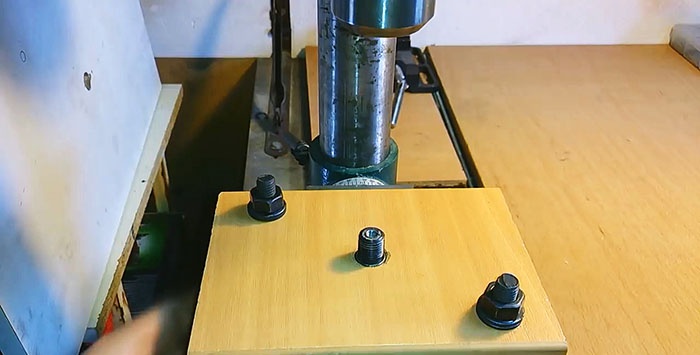
The base of the attachment is lightly clamped with bolts and nuts on the machine table. The cartridge is screwed onto the protruding shaft.
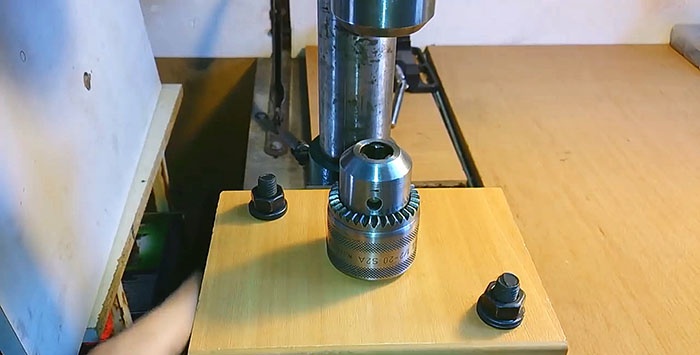
A drill or straight rod is inserted into the machine. In this case, its protruding part must fall into the attachment cartridge in order to be clamped by its jaws. This allows for centering. Afterwards, the mounting bolts must be tightened securely.
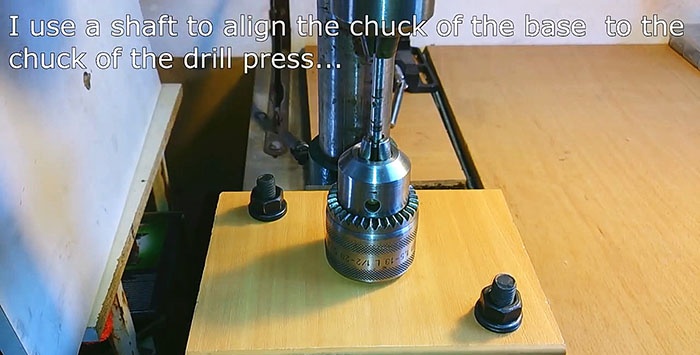

The resulting design copies the operating principle of a lathe. Now, by holding the drill still in the attachment chuck and fixing small parts for drilling in the machine, you can make even, centered holes.
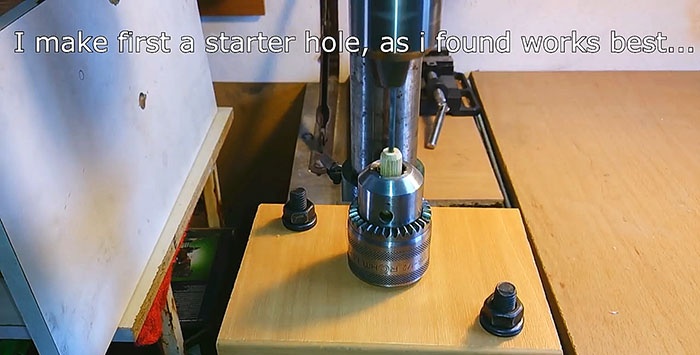
Rotation test on the shaft.
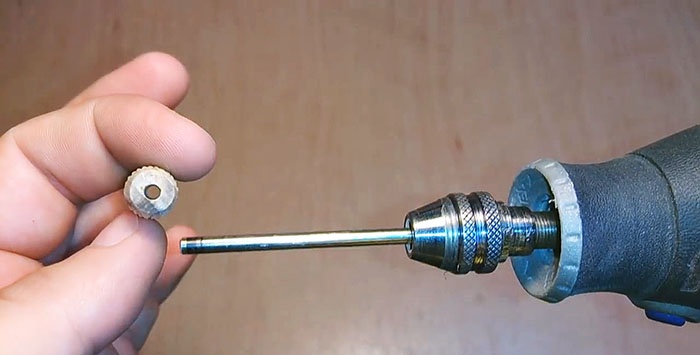
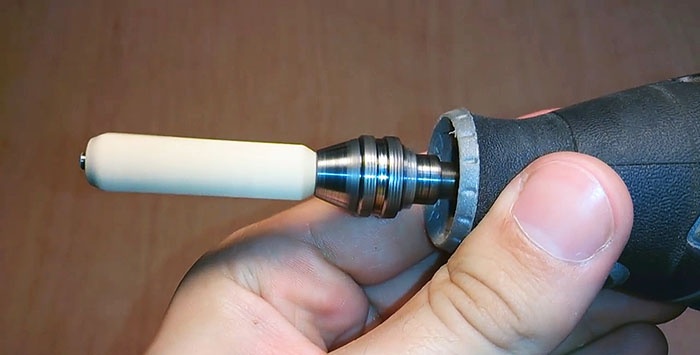
This design will be useful when expanding the bore diameter in gears, pulleys, etc.
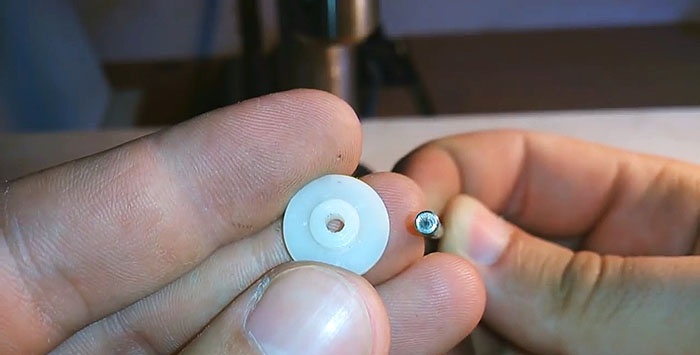
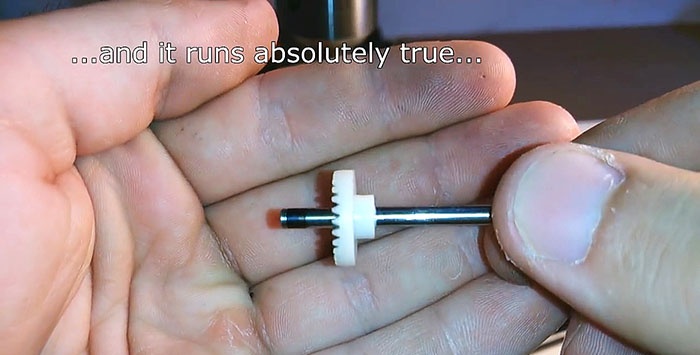
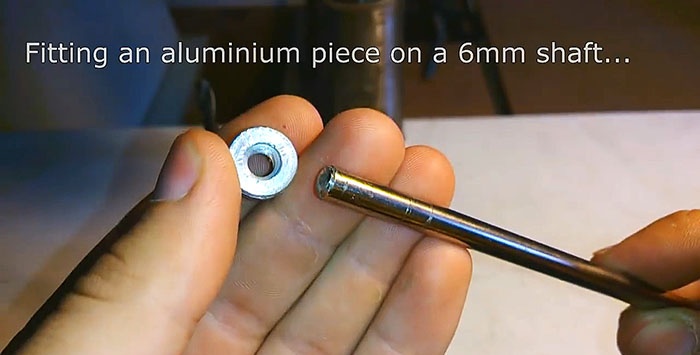
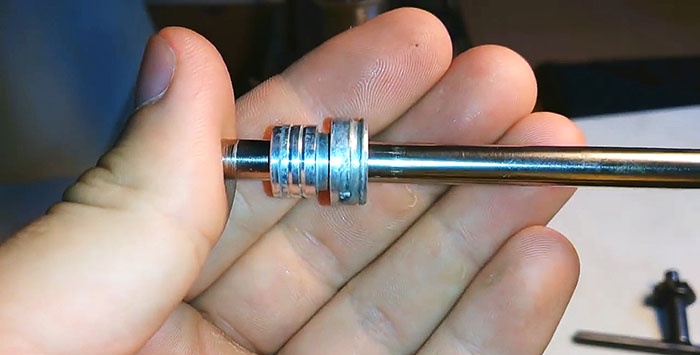
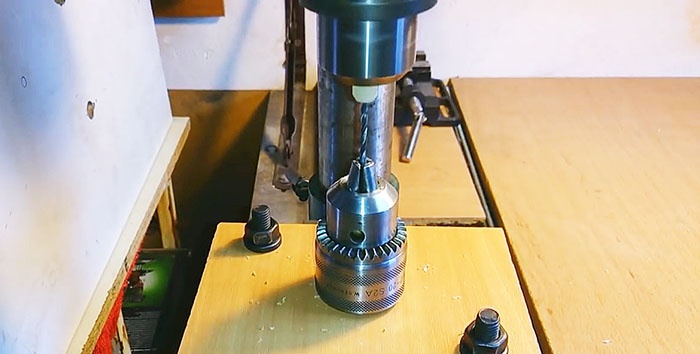
Materials:
- drill chuck with shaft or SDS-plus adapter;
- a piece of chipboard;
- epoxy adhesive;
- 2 bolts with nuts.
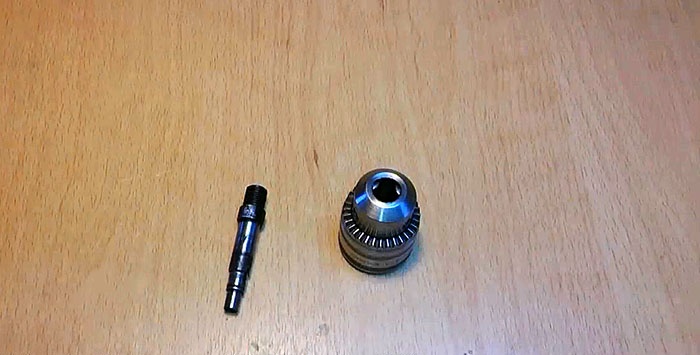
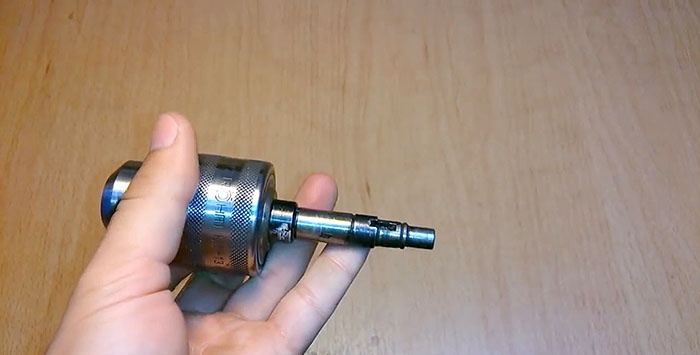
Assembling the console
In my case, the attachment will be made from a jaw chuck with a shaft. If you don’t have an old drill to disassemble, you can simply buy a chuck with an SDS-plus adapter. You need to cut the shaft or adapter using any available method. It should be shortened so that a tail comes out of the cartridge corresponding to the thickness of the available chipboard. Using an engraver, I cut the shaft at the 18mm mark.
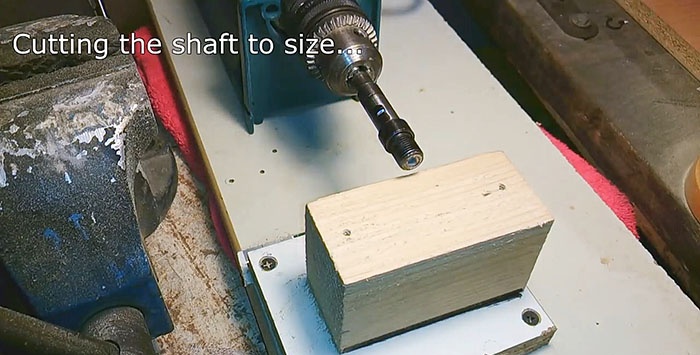
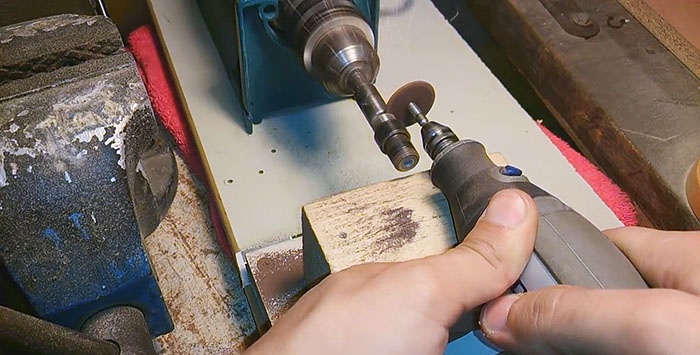
Next you need to take chipboard. It will be used as a stand on the drilling machine table.The size of the workpiece is determined individually, but 15x20 cm is enough. The center is marked on the chipboard. To find it, draw diagonals between the corners.

At the point of their intersection, a hole is drilled 1 mm larger than the thickness of the cut tail of the adapter or shaft.
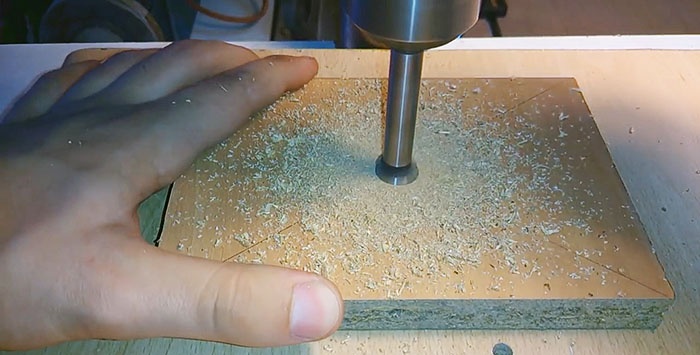
The hole is coated with epoxy glue, after which the cartridge holder is pressed into it. All you have to do is wait until the epoxy hardens.
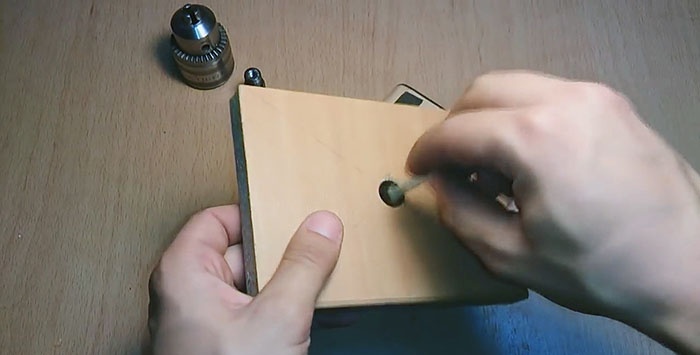
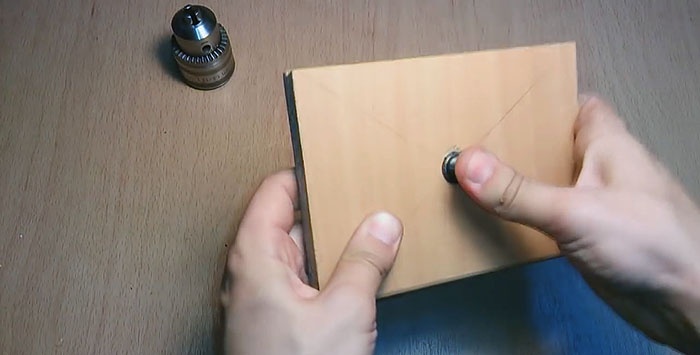
The chipboard with the shaft is placed on the machine table and holes are marked to fix it. It is enough to drill 2 holes diagonally.
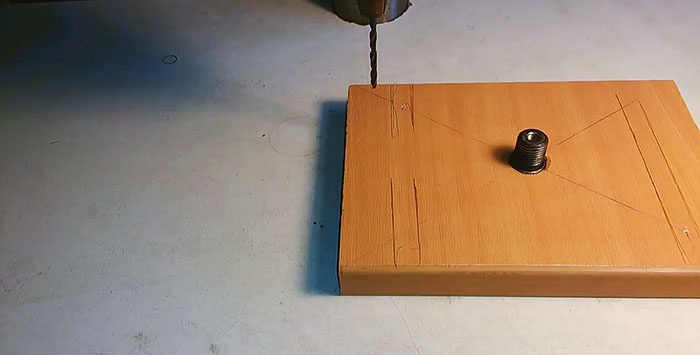
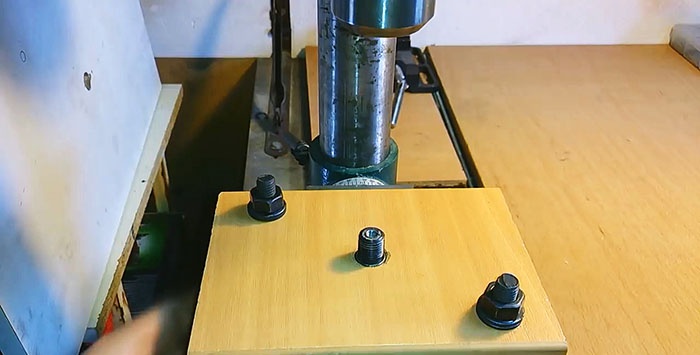
The base of the attachment is lightly clamped with bolts and nuts on the machine table. The cartridge is screwed onto the protruding shaft.
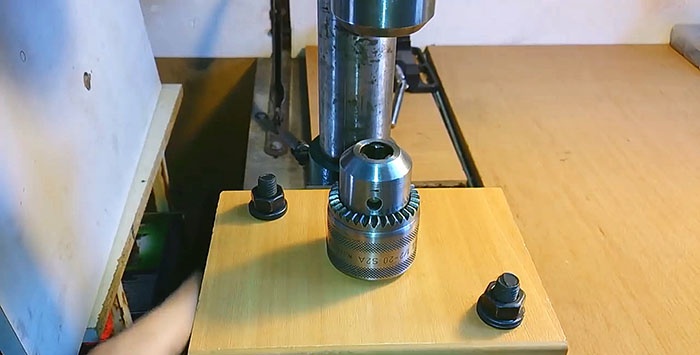
A drill or straight rod is inserted into the machine. In this case, its protruding part must fall into the attachment cartridge in order to be clamped by its jaws. This allows for centering. Afterwards, the mounting bolts must be tightened securely.
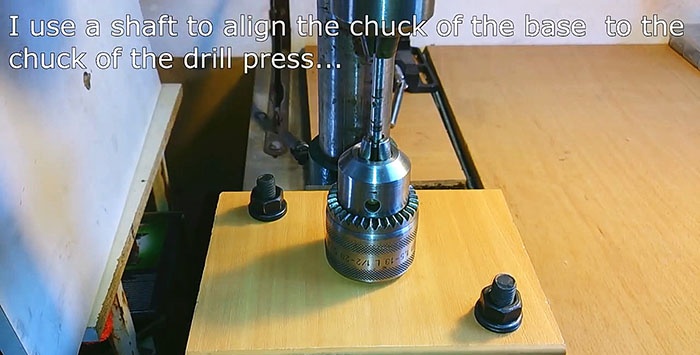
How to use?

The resulting design copies the operating principle of a lathe. Now, by holding the drill still in the attachment chuck and fixing small parts for drilling in the machine, you can make even, centered holes.
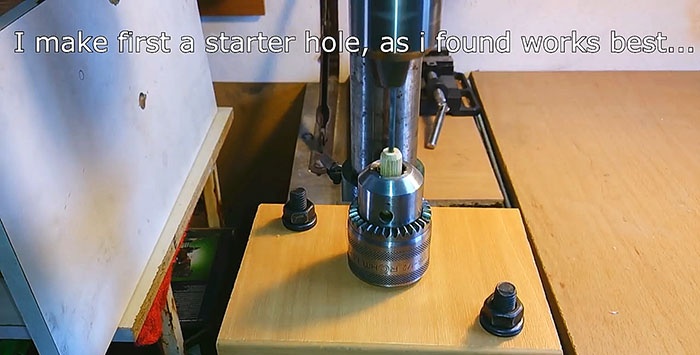
Rotation test on the shaft.
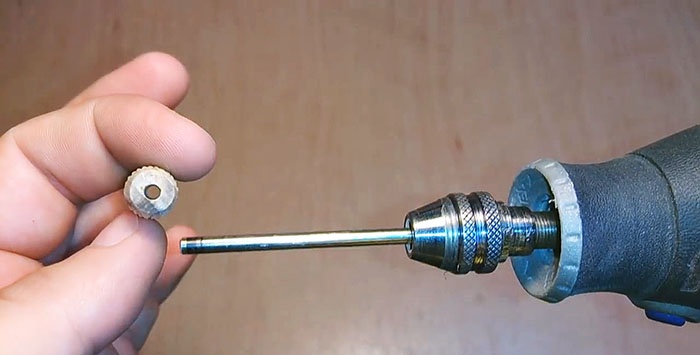
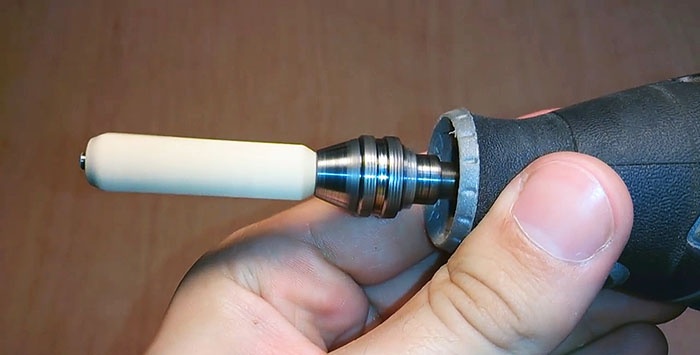
This design will be useful when expanding the bore diameter in gears, pulleys, etc.
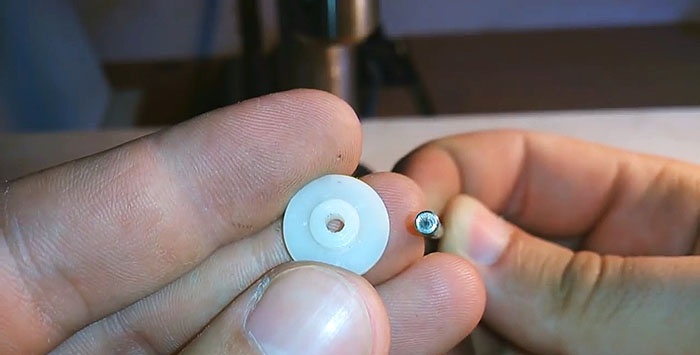
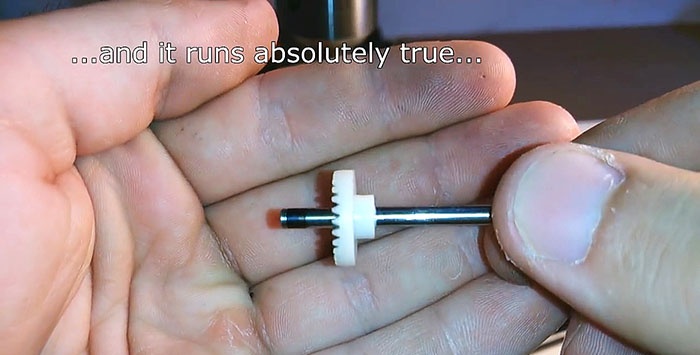
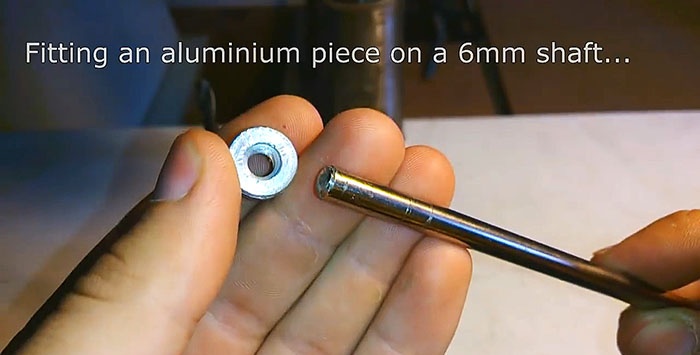
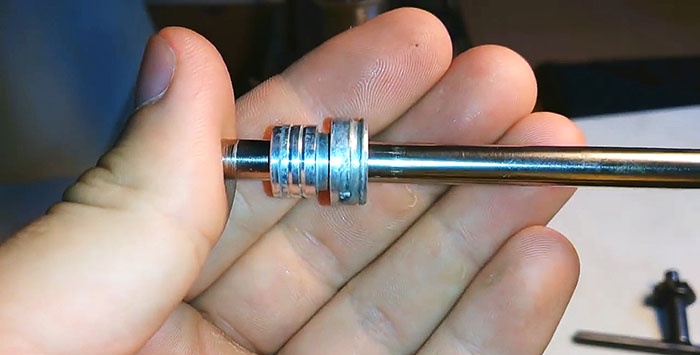
Watch the video
Similar master classes
Particularly interesting
Comments (1)