Soldering strands of aluminum and copper wire
So, let's talk about how to solder aluminum. Those who have faced this task know that aluminum is difficult to solder. This is due to a thin oxide film that quickly forms on the surface of this metal in the open air. Therefore, special fluxes are used for soldering aluminum. I will demonstrate the aluminum soldering process using the example of tinning and soldering strands of wire.
When installing electrical wiring, I always prefer solder connections. I believe that this method provides better electrical contact compared to conventional twisting of wires without soldering or crimping them into a sleeve or tip.
We will need:
Let's start by soldering twisted aluminum wires.Before twisting the wires, you need to make sure that the surface of the aluminum conductors is clean. Otherwise, you need to strip the wire with a knife. The surface of the wire should be light silver, not dark gray.
We twist with pliers.
For soldering aluminum we use a special flux. It may have a specific brand F-61A, F-59A, F-64, etc., or simply be called “flux for soldering aluminum.” A 25 ml bottle costs approximately 45 rubles and will last a long time.
Using a brush, apply a thin layer of flux to the twist on all sides.
Wet the soldering iron tip, heated to operating temperature, with solder by lightly touching it. Stroking the twist with the working surface of the tip, apply solder to it.
Solder and aluminum are similar in color, but this does not prevent you from observing how the solder spreads over the surface of the wires, filling the gaps between them. You should not overdo it with the amount of solder; a thin layer on the surface of the aluminum is sufficient; frozen drops should be avoided.
I solder copper strands in the same way, only the flux in this case is a solution of rosin in acetone. I prepare it as follows. I pour about 30 ml of acetone into the bottle and gradually add rosin, previously crushed into powder, into it. By stirring I achieve complete dissolution of the rosin. As a result, the solution should acquire the color of weak tea. I also apply flux with a brush; the consumption of rosin is negligible, and thanks to the fluidity of acetone, the solution penetrates into the smallest crevices. If you use undissolved rosin, it doesn’t work out so neatly; the excess then has to be removed.
When installing electrical wiring, it is prohibited to directly connect wires with current-carrying conductors made of copper and aluminum. As a result of electrochemical processes, an oxide film is formed at the interface between these metals, which increases the contact resistance. The presence of moisture activates the reaction. As a result, the junction begins to heat up, which further accelerates the corrosion process. Copper and aluminum are connected through a third metal. Typically, a bolted connection is used with a steel washer installed between the wires, or special clamps that prevent direct contact of the wires.
If it is necessary to connect wires with copper and aluminum conductors, I proceed as follows.
I pre-tin the copper and aluminum wires that need to be connected, that is, I cover them with a thin layer of solder.
At the same time, I use a different flux for each metal, but I use the same solder. After that, I twist the wires and solder the twist on the outside. As a result, the copper and aluminum wires are connected through a layer of solder separating them. Tin and lead included in the solder are chemically neutral to copper and aluminum, which eliminates the occurrence of electrochemical corrosion. The outer layer of solder applied to the twist seals the contact and protects it from external influences.
Sometimes you can hear the opinion that soldering twists carries a potential danger. It is believed that when the twist is overheated, the solder melts and, as it drips, damages the insulation of other wires. Let's figure this out.
The twist itself, especially when soldered, provides an area of electrical contact that is several times larger than the cross-section of the main wire.This means that when the electrical wiring is overloaded, the heating of the twist will be minimal. In this case, the wire will overheat along its entire length, which can lead to melting of the insulation much earlier than melting of the solder. The reason for this situation is not the presence of twisting or soldering, but the absence of a circuit breaker or its incorrect choice.
As for the “destructive” effect of molten solder, during the soldering process you can make sure that drops of it that accidentally fall from the soldering iron tip do not even burn through the newspaper on the table.
When performing soldering, follow basic safety rules. Working with an electric soldering iron involves the following dangers:
When installing electrical wiring, I always prefer solder connections. I believe that this method provides better electrical contact compared to conventional twisting of wires without soldering or crimping them into a sleeve or tip.
Required tools and materials
We will need:
- a regular soldering iron with a power of 40 watts;
- knife for stripping and stripping wires;
- flux for soldering aluminum (F-61A, F-59A, F-64, etc.);
- a solution of rosin in acetone or alcohol;
- lead-tin solder;
- trimming aluminum and copper wires with a cross-section of 2.5 - 4 square meters. mm.
Let's start soldering
Soldering twisted aluminum wires
Let's start by soldering twisted aluminum wires.Before twisting the wires, you need to make sure that the surface of the aluminum conductors is clean. Otherwise, you need to strip the wire with a knife. The surface of the wire should be light silver, not dark gray.
We twist with pliers.
For soldering aluminum we use a special flux. It may have a specific brand F-61A, F-59A, F-64, etc., or simply be called “flux for soldering aluminum.” A 25 ml bottle costs approximately 45 rubles and will last a long time.
Using a brush, apply a thin layer of flux to the twist on all sides.
Wet the soldering iron tip, heated to operating temperature, with solder by lightly touching it. Stroking the twist with the working surface of the tip, apply solder to it.
Solder and aluminum are similar in color, but this does not prevent you from observing how the solder spreads over the surface of the wires, filling the gaps between them. You should not overdo it with the amount of solder; a thin layer on the surface of the aluminum is sufficient; frozen drops should be avoided.
Soldering copper twist
I solder copper strands in the same way, only the flux in this case is a solution of rosin in acetone. I prepare it as follows. I pour about 30 ml of acetone into the bottle and gradually add rosin, previously crushed into powder, into it. By stirring I achieve complete dissolution of the rosin. As a result, the solution should acquire the color of weak tea. I also apply flux with a brush; the consumption of rosin is negligible, and thanks to the fluidity of acetone, the solution penetrates into the smallest crevices. If you use undissolved rosin, it doesn’t work out so neatly; the excess then has to be removed.
Twisted copper and aluminum wire
When installing electrical wiring, it is prohibited to directly connect wires with current-carrying conductors made of copper and aluminum. As a result of electrochemical processes, an oxide film is formed at the interface between these metals, which increases the contact resistance. The presence of moisture activates the reaction. As a result, the junction begins to heat up, which further accelerates the corrosion process. Copper and aluminum are connected through a third metal. Typically, a bolted connection is used with a steel washer installed between the wires, or special clamps that prevent direct contact of the wires.
If it is necessary to connect wires with copper and aluminum conductors, I proceed as follows.
I pre-tin the copper and aluminum wires that need to be connected, that is, I cover them with a thin layer of solder.
At the same time, I use a different flux for each metal, but I use the same solder. After that, I twist the wires and solder the twist on the outside. As a result, the copper and aluminum wires are connected through a layer of solder separating them. Tin and lead included in the solder are chemically neutral to copper and aluminum, which eliminates the occurrence of electrochemical corrosion. The outer layer of solder applied to the twist seals the contact and protects it from external influences.
Sometimes you can hear the opinion that soldering twists carries a potential danger. It is believed that when the twist is overheated, the solder melts and, as it drips, damages the insulation of other wires. Let's figure this out.
The twist itself, especially when soldered, provides an area of electrical contact that is several times larger than the cross-section of the main wire.This means that when the electrical wiring is overloaded, the heating of the twist will be minimal. In this case, the wire will overheat along its entire length, which can lead to melting of the insulation much earlier than melting of the solder. The reason for this situation is not the presence of twisting or soldering, but the absence of a circuit breaker or its incorrect choice.
As for the “destructive” effect of molten solder, during the soldering process you can make sure that drops of it that accidentally fall from the soldering iron tip do not even burn through the newspaper on the table.
Conclusion
When performing soldering, follow basic safety rules. Working with an electric soldering iron involves the following dangers:
- electric shock if it malfunctions (phase breakdown on the body and soldering iron tip);
- the possibility of getting a burn (the melting point of lead-tin solders is about 200°C).
Watch the video
Similar master classes
Particularly interesting
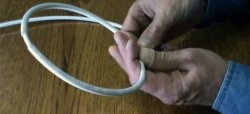
Cable antenna for digital TV in 5 minutes
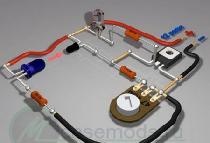
A selection of simple and effective schemes.
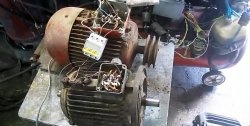
Three-phase voltage from single-phase in 5 minutes
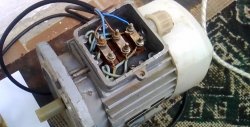
Starting a three-phase motor from a single-phase network without a capacitor
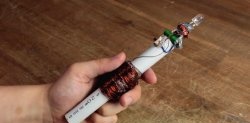
Eternal flashlight without batteries
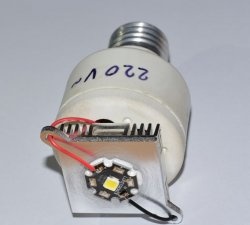
How to make an inexpensive but very powerful LED lamp
Comments (22)