Homemade crimp for crimping tubular lugs on a cable
To crimp tubular terminals on a wire, a special crimping tool is required. Usually only those who do professional electrical installation have it; in other cases, purchasing it is not advisable. To perform a small amount of work, you can make homemade crimping from inexpensive materials, thereby avoiding unnecessary expenses.
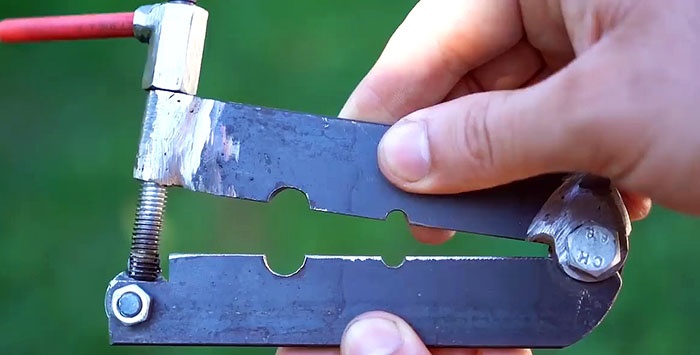
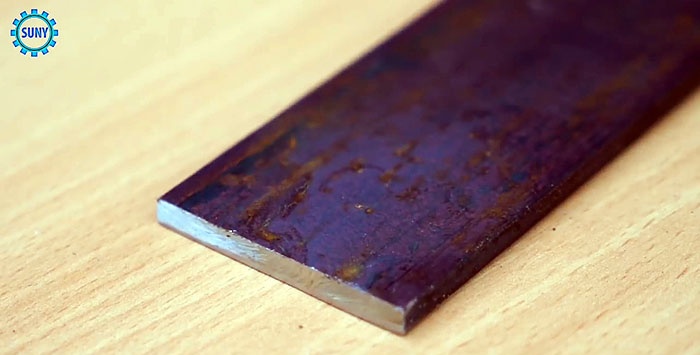
The working part of the tool will be made of a steel strip 5 cm wide. A piece literally 15 cm long is taken and drawn as in the photo.
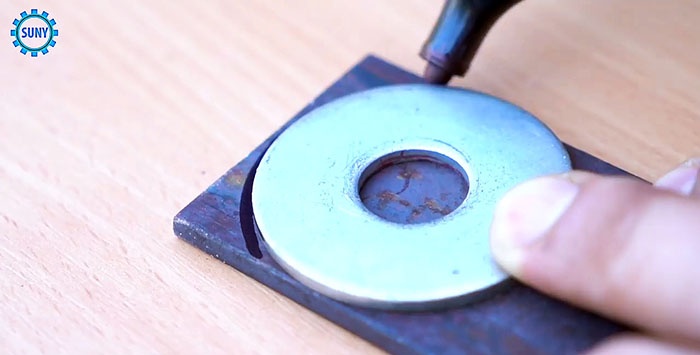
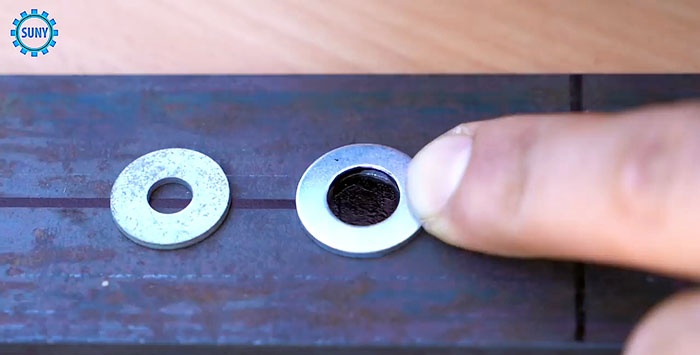
It will be spread lengthwise into 2 jaws, between which you need to make holes for different diameter tips. In the example there are 2 of them, but it is better to grind all the popular sizes at once.
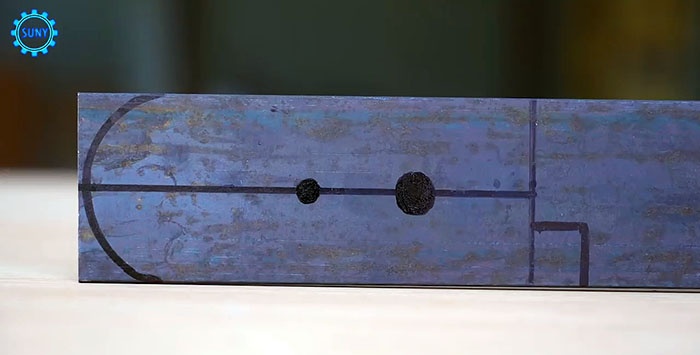
The cut piece is cut in half using a thin cutting disc.
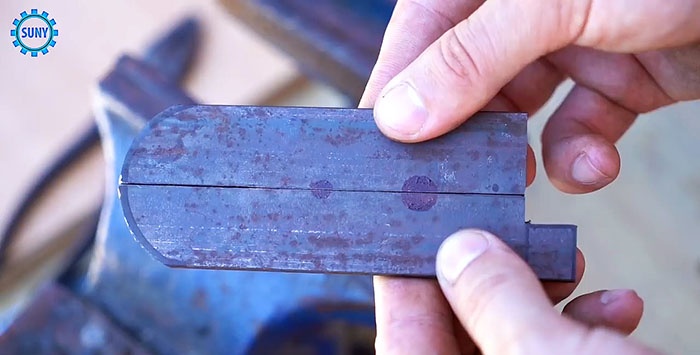
After this, you need to make holes between the jaws to obtain the contact part of the crimp.For this, it is better to use a grinder rather than a drill, since the cutouts should be angular, not round.
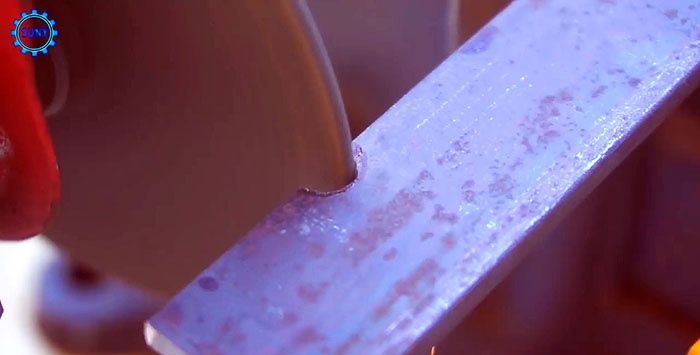
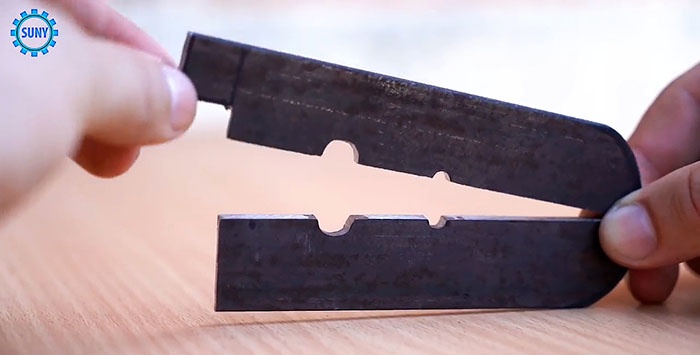
To connect the workpieces together to obtain pliers, you need to make eyes on them. To do this, a washer is welded to each sponge, after which they are pulled together with a bolt and nut.
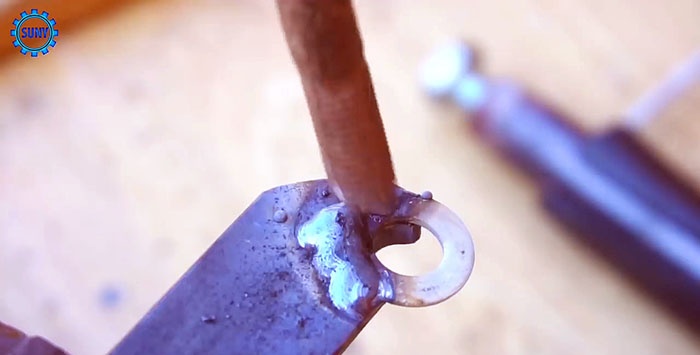
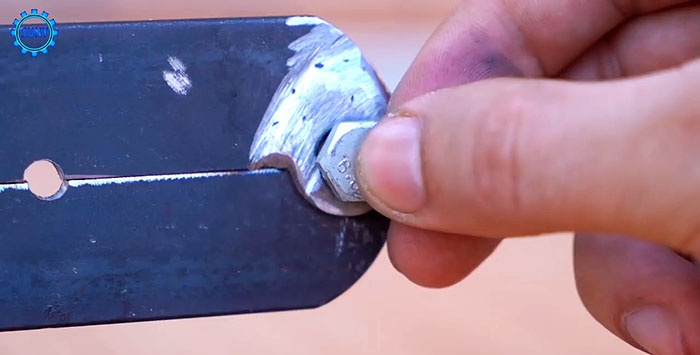
A hole is drilled on the protrusion of the elongated jaw of the tool, to which a modified bolt with a welded washer instead of a head is screwed.
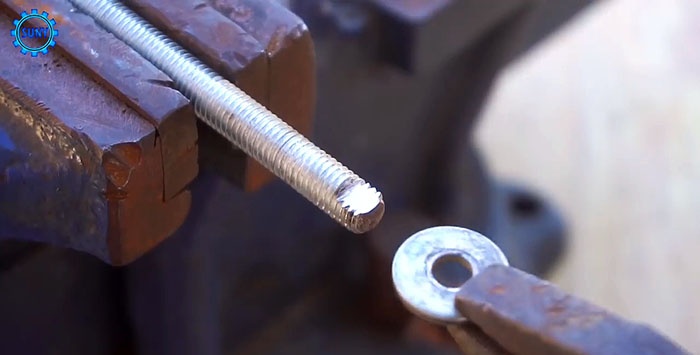
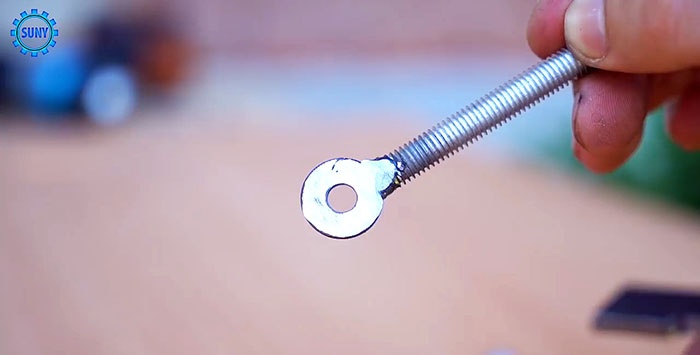
A piece of tube is welded onto the second jaw.
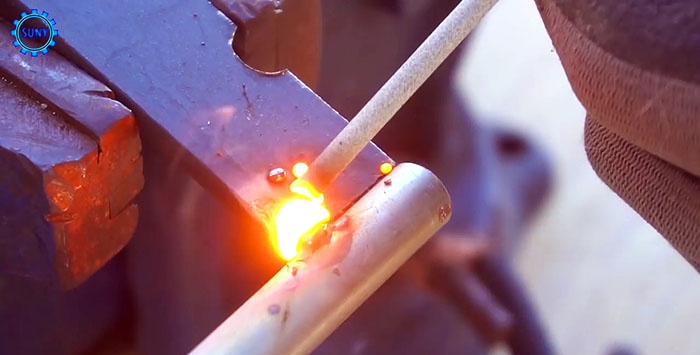
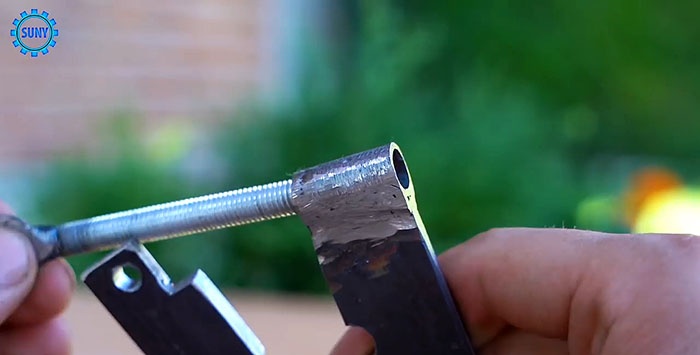
To obtain a mechanism for tightening the jaws, a bolt with a washer instead of a head is fixed to the bottom of the guillotine and passed through a tube on the second jaw. An elongated nut with a welded handle is screwed onto it. The wide nut has an increased area of contact with the thread, so it will not break off under pressure.
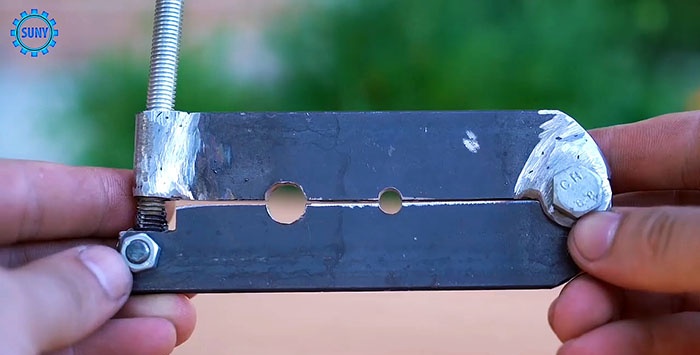
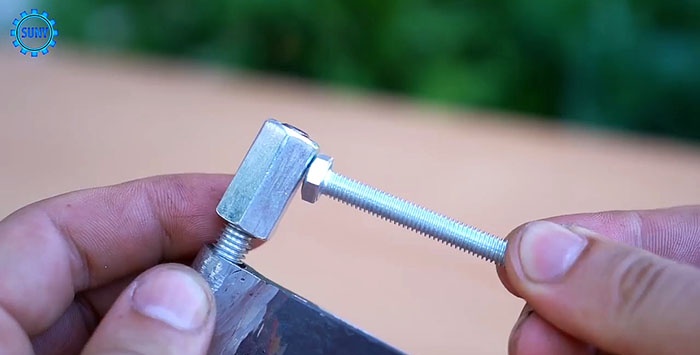
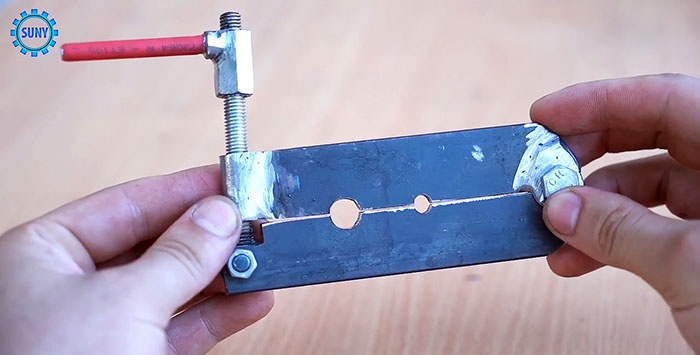
To use the tool, you need to insert a stripped wire with a tip between its pliers.
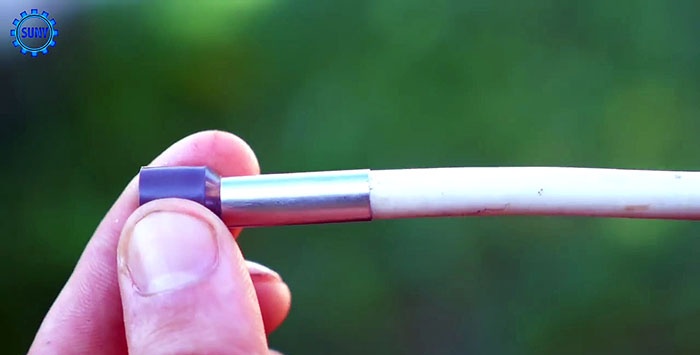
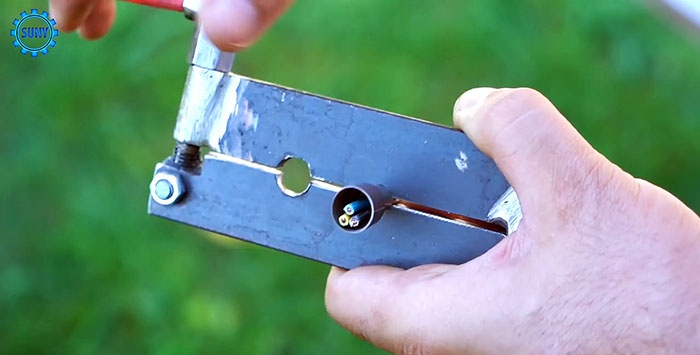
By rotating the elongated nut with a handle, you need to squeeze its jaws, thereby deforming the tube.
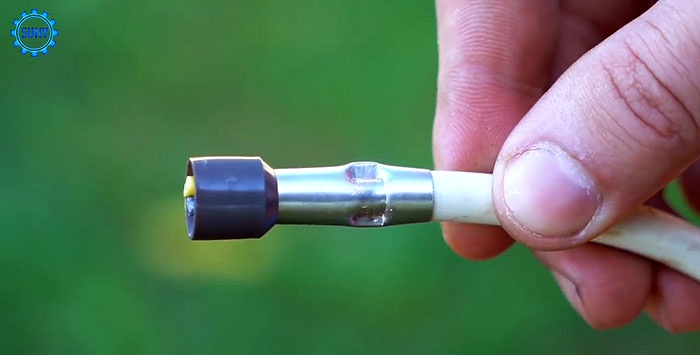
To increase the contact area, crimping is done several times in increments of a couple of millimeters. When using a powerful tube, when deformation requires great effort, you can rotate the nut with a wrench.
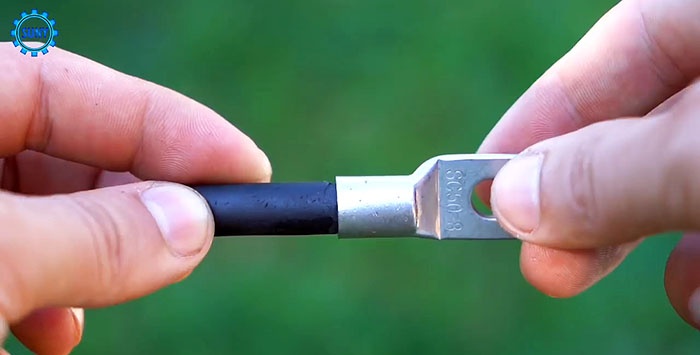
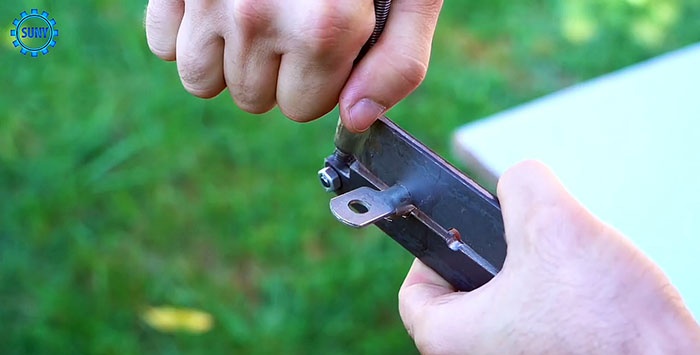
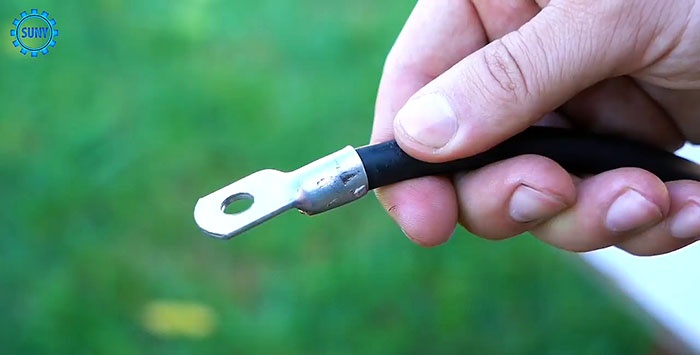
Assembling such a crimp will cost pennies, but it compresses the tips much more accurately than a vice or pliers, although it does not reach the level of a real crimper.
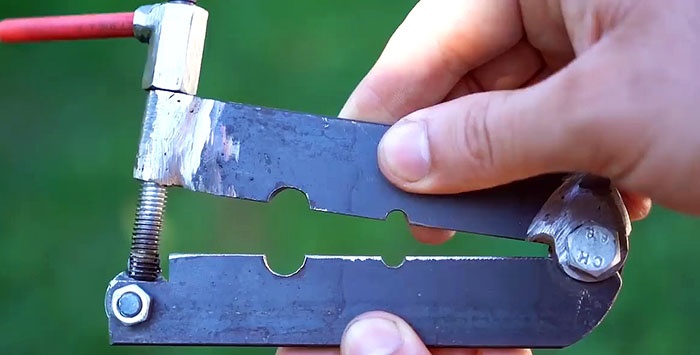
Materials:
- steel strip 5 cm wide;
- 3 M8 washers;
- 2 short M8 bolts with nuts;
- long M8 bolt;
- extended nut M8;
- tube with an internal diameter of 9-10 mm.
Making crimp
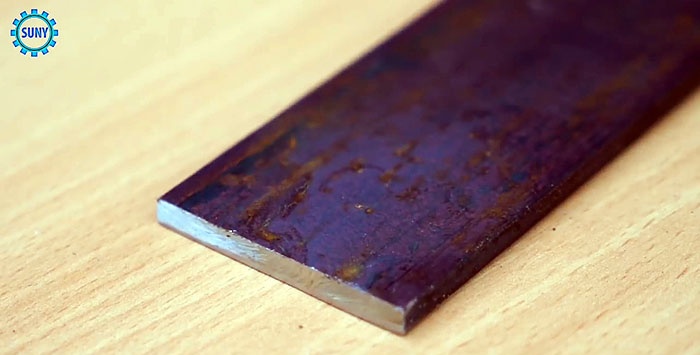
The working part of the tool will be made of a steel strip 5 cm wide. A piece literally 15 cm long is taken and drawn as in the photo.
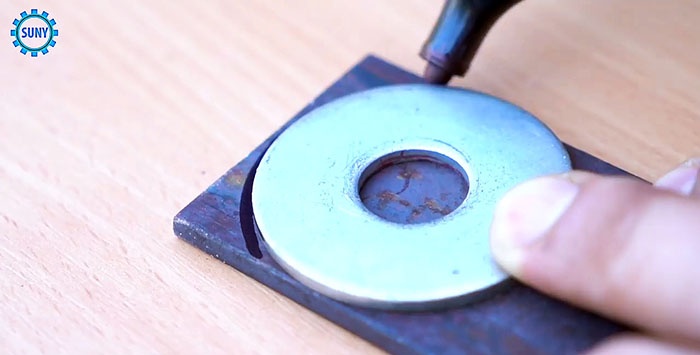
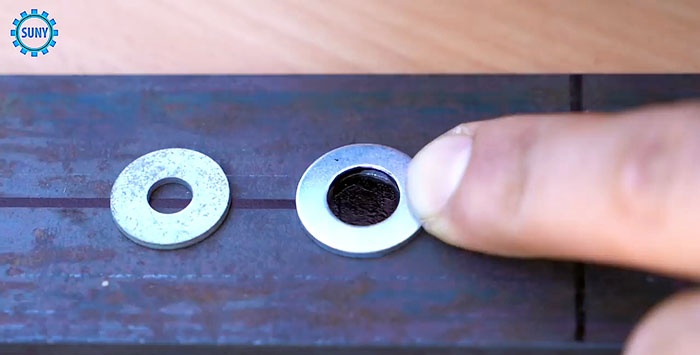
It will be spread lengthwise into 2 jaws, between which you need to make holes for different diameter tips. In the example there are 2 of them, but it is better to grind all the popular sizes at once.
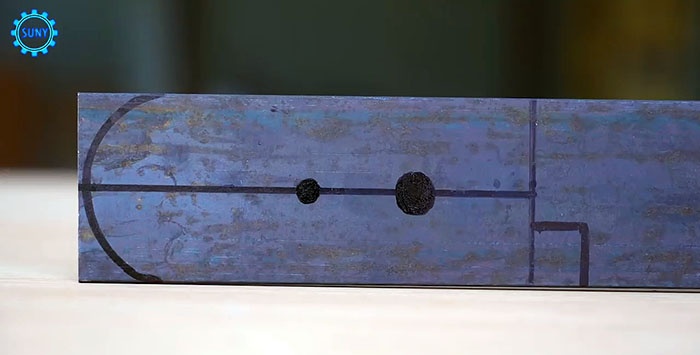
The cut piece is cut in half using a thin cutting disc.
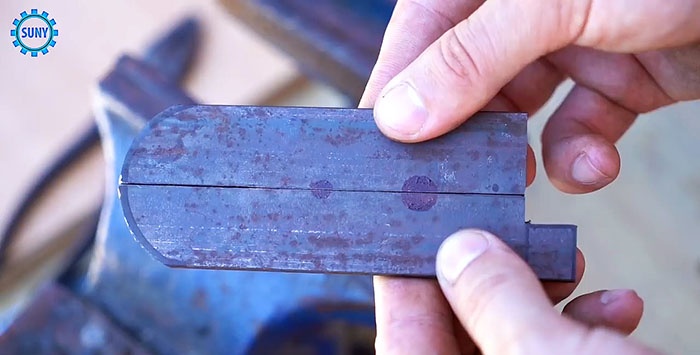
After this, you need to make holes between the jaws to obtain the contact part of the crimp.For this, it is better to use a grinder rather than a drill, since the cutouts should be angular, not round.
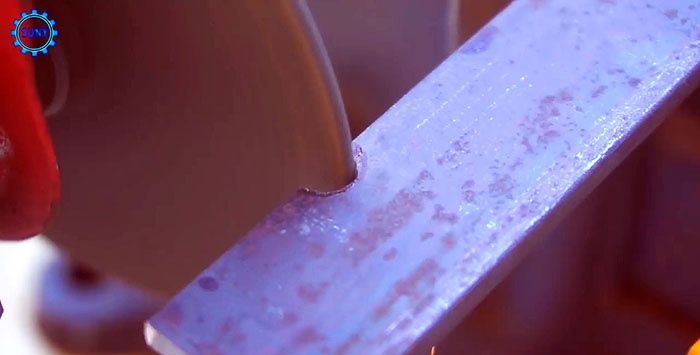
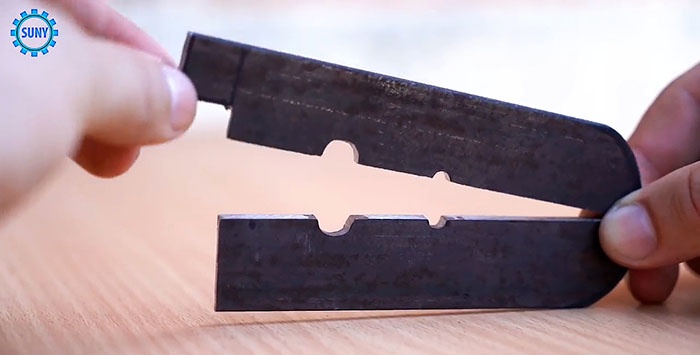
To connect the workpieces together to obtain pliers, you need to make eyes on them. To do this, a washer is welded to each sponge, after which they are pulled together with a bolt and nut.
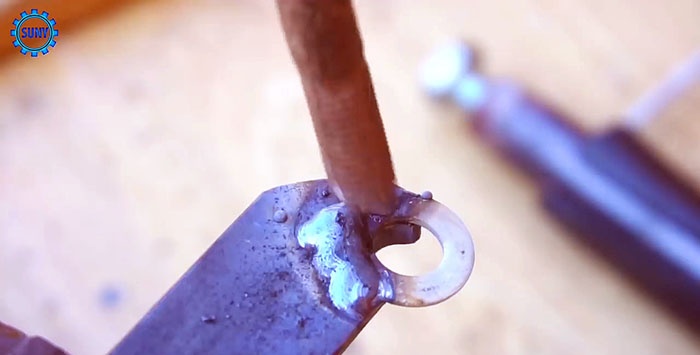
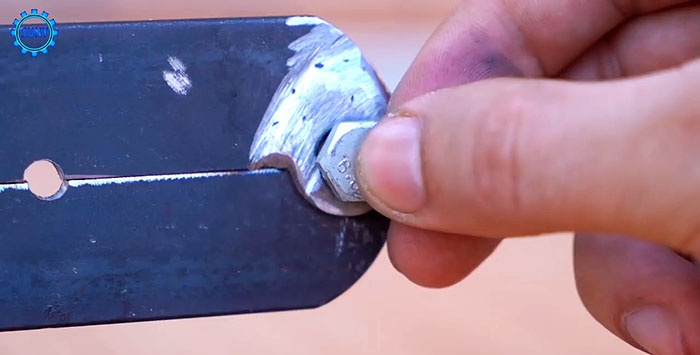
A hole is drilled on the protrusion of the elongated jaw of the tool, to which a modified bolt with a welded washer instead of a head is screwed.
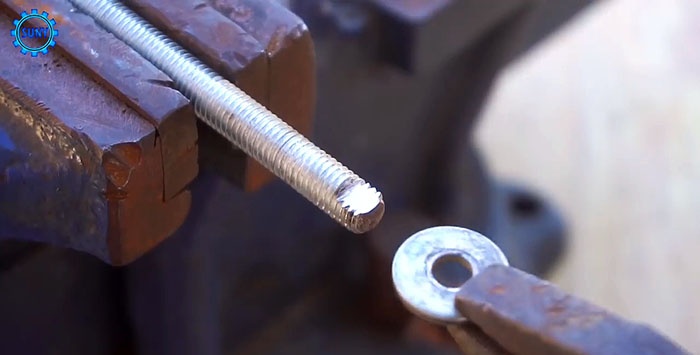
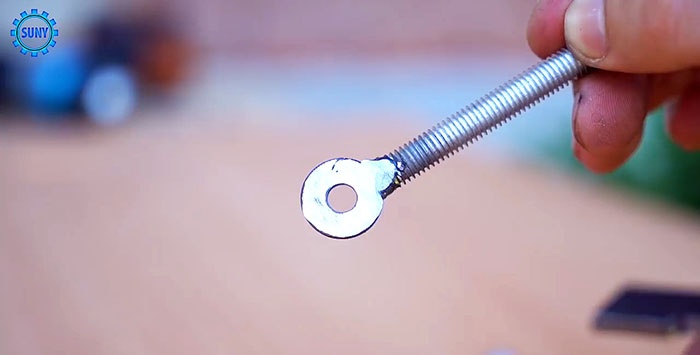
A piece of tube is welded onto the second jaw.
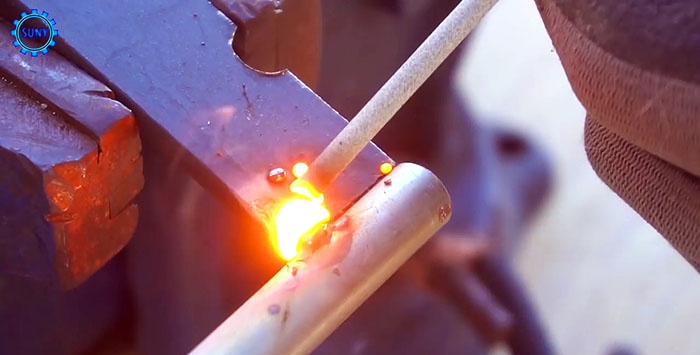
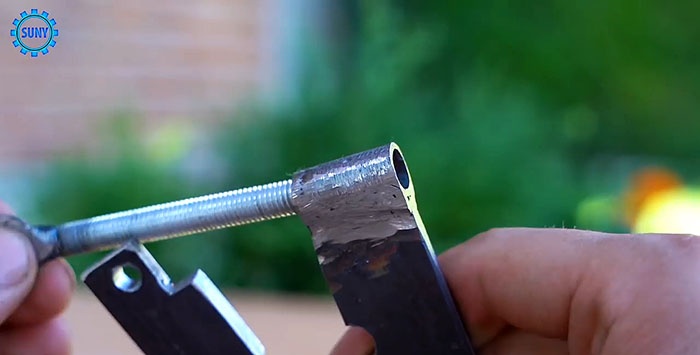
To obtain a mechanism for tightening the jaws, a bolt with a washer instead of a head is fixed to the bottom of the guillotine and passed through a tube on the second jaw. An elongated nut with a welded handle is screwed onto it. The wide nut has an increased area of contact with the thread, so it will not break off under pressure.
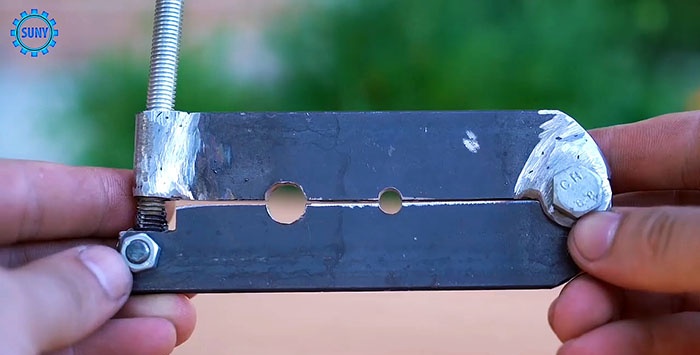
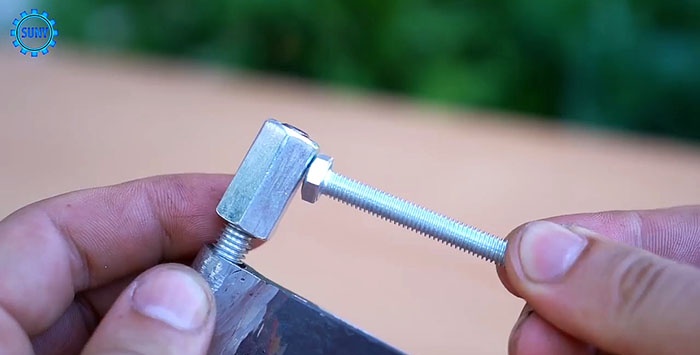
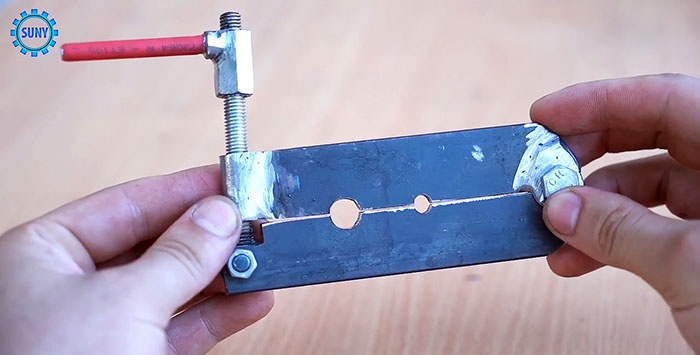
To use the tool, you need to insert a stripped wire with a tip between its pliers.
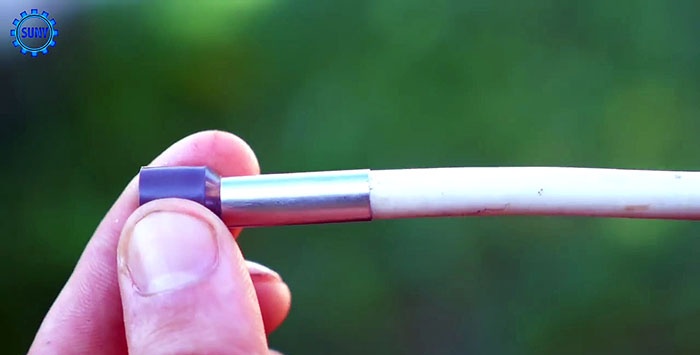
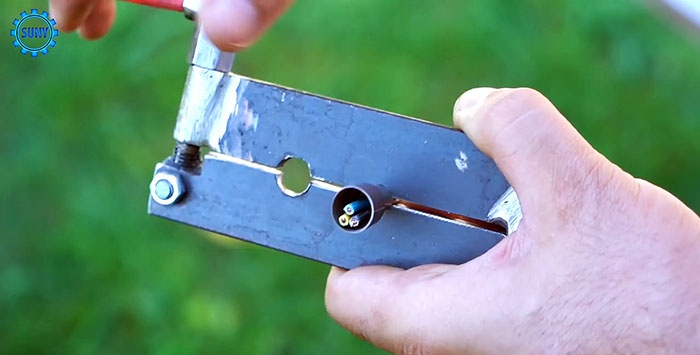
By rotating the elongated nut with a handle, you need to squeeze its jaws, thereby deforming the tube.
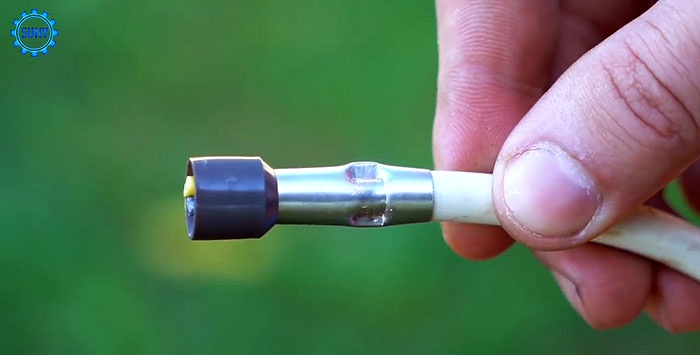
To increase the contact area, crimping is done several times in increments of a couple of millimeters. When using a powerful tube, when deformation requires great effort, you can rotate the nut with a wrench.
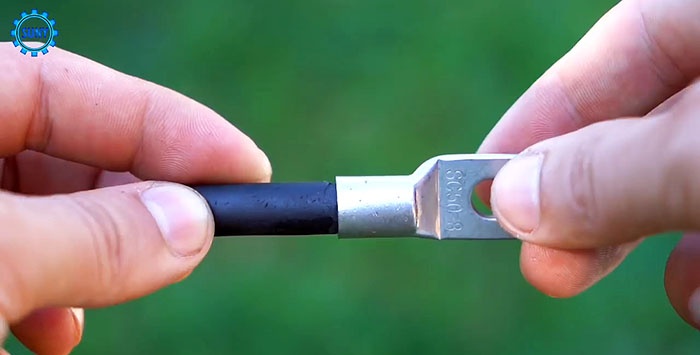
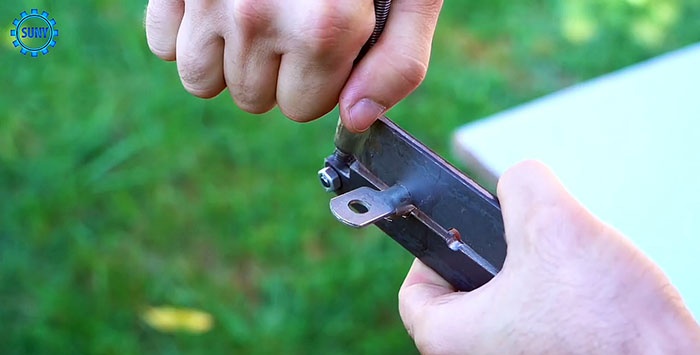
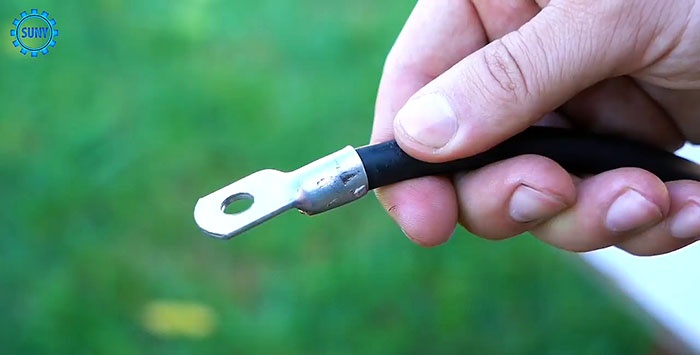
Assembling such a crimp will cost pennies, but it compresses the tips much more accurately than a vice or pliers, although it does not reach the level of a real crimper.
Watch the video
Similar master classes
Particularly interesting
Comments (2)