Simple DIY clamp
If you don’t have a factory clamp on hand to secure the hose to a pipe, tap or pump nozzle, then this can be done using annealed steel wire and pliers. But the reliability of such a connection will be low, since the sharp edges of the tool can damage the wire, and the tightening torque is difficult to regulate. How to make the process controlled?
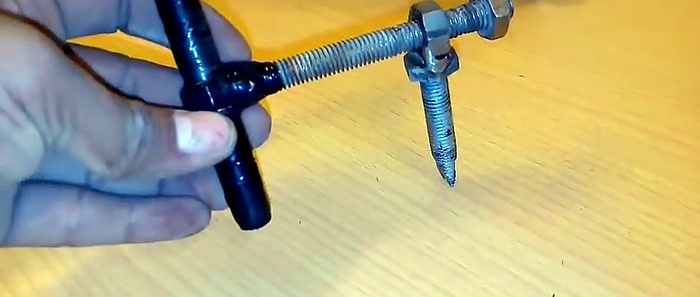
In addition to the annealed wire and pliers already mentioned above, we will need the following accessories:
We sharpen the end of the short bolt shaft into a blunt wedge and make a shallow rounded slot in the middle. We weld a nut on top to the head of the upgraded bolt in a vertical position.
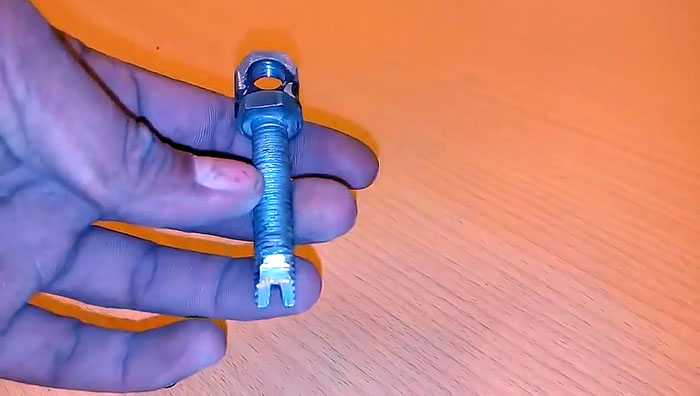
We weld the nut to the long bolt in the same way. We screw the pin into it to the middle and wrap it and the adjacent part of the bolt with the nut with PVC electrical tape to secure the connection and make it easier to use.
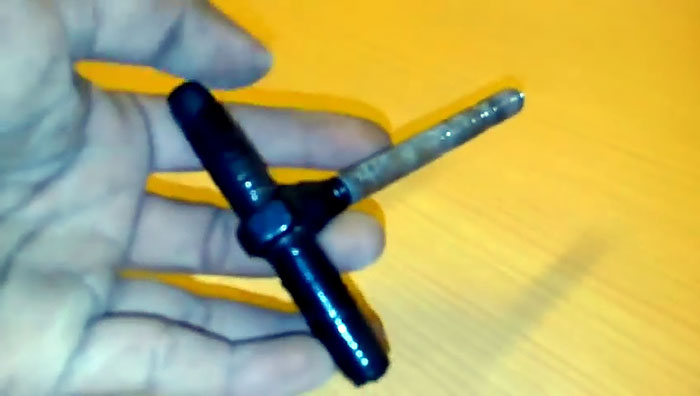
In the center of the rod and, stepping back about 2 cm towards the end, we drill two through transverse holes, parallel to each other, with a diameter of 2.5 mm.
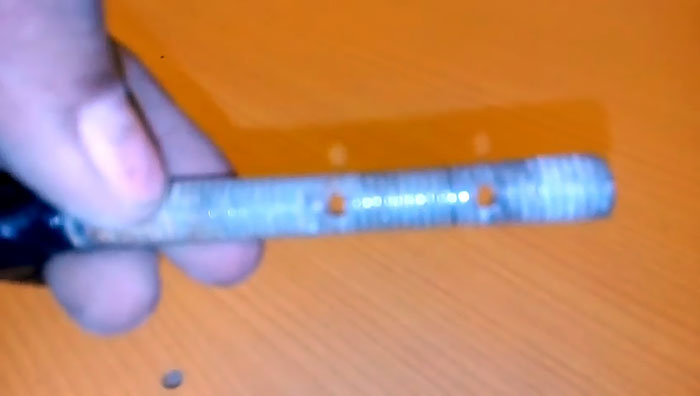
We screw the bolt with holes into the nut welded to the short bolt until the holes are on opposite sides of the nut at approximately the same distance. Our homemade product is ready to go.
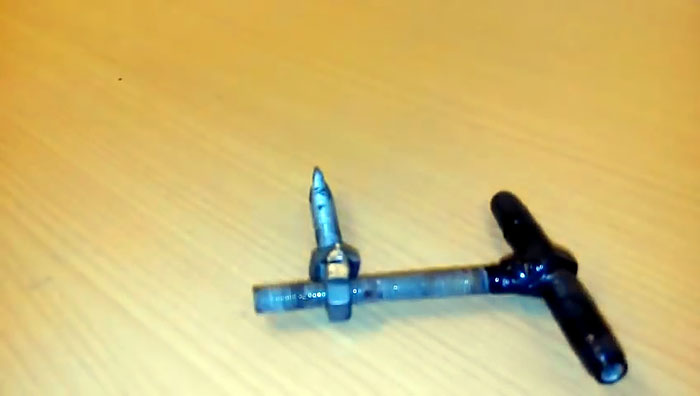
As an example, we will attach the hose to the fitting of the union nut. It is clear that instead of it, there may be a pipe, a pump pipe, a tap, etc.
Bend the wire in half and cut it from the skein using wire cutters or pliers.
We place it in the place where the wire clamp should be and thread the ends through the loop.
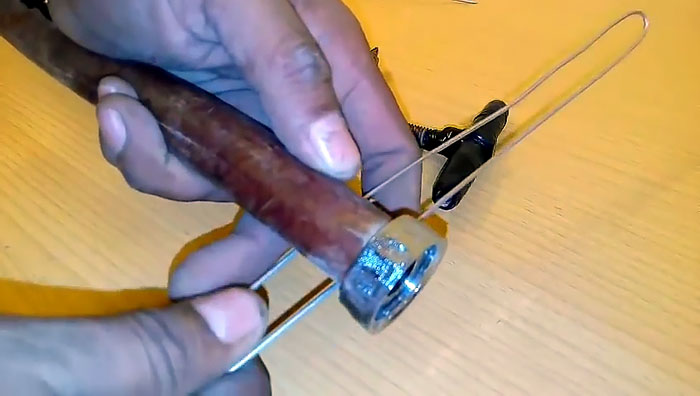
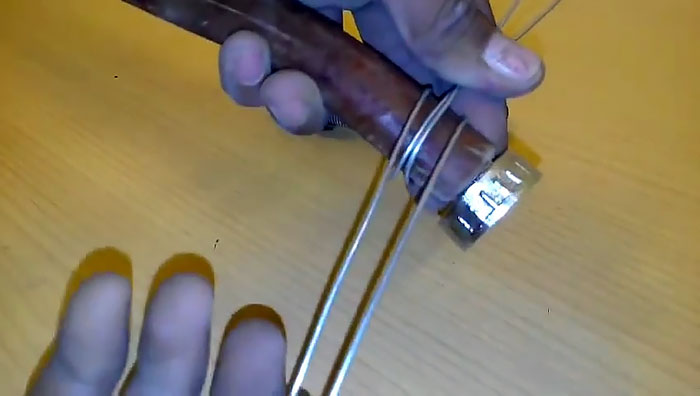
We wrap a piece of wire with a bent end around the hose and thread the ends through the loop again.
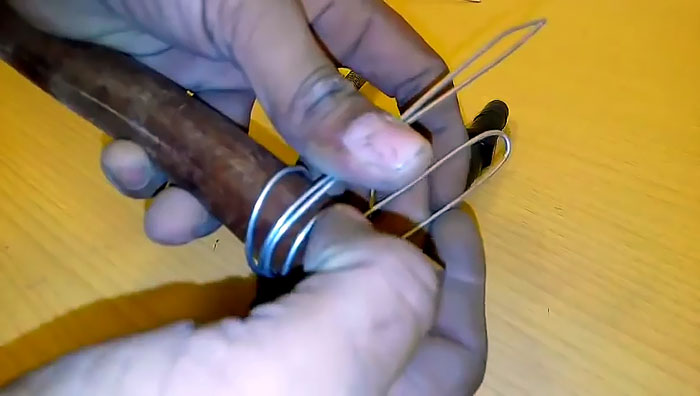
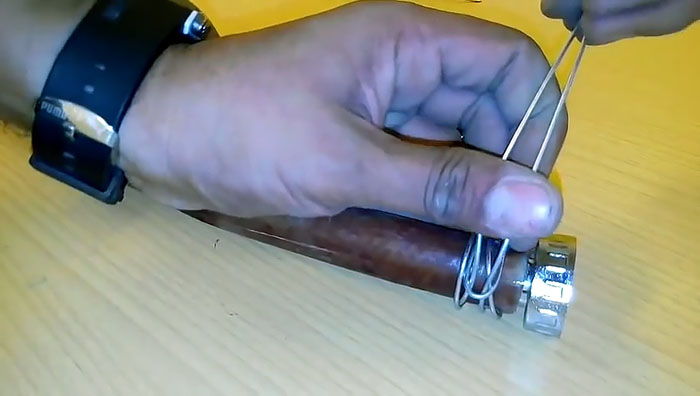
We thread the free ends of the wire into the holes on the long rod of the clamp bolt, and rest the short bolt with the notch against the wire loop.
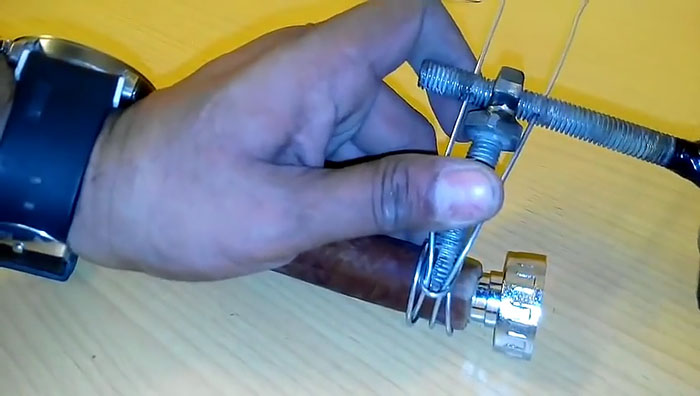
We cut off, leaving small ends, the excess wire on the back side of the holes with wire cutters or pliers.
We rotate the bolt with holes in any direction (in our case to the right), making sure that the wire ends do not jump out of the holes, and the loop does not pop out of the recess of the short bolt. We compress the rings with pliers if they have moved away from each other.

We continue rotating until the wire loops tightly wrap around the hose and provide a tight connection with the union nut fitting.
After this, we rotate the device around the wire loop, using it as an axis of rotation, 180 degrees.
We release the tightening device by rotating it counterclockwise in our case, and cut off the excess wire with wire cutters. We tap the wire ends to the hose.
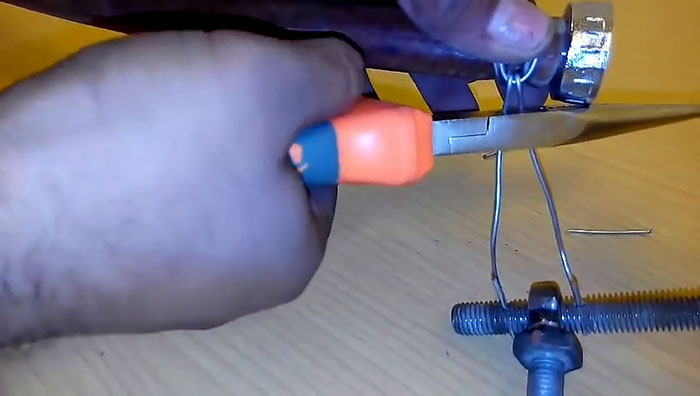
The result is a sealed and durable connection, since in this case there is no danger of damage to the wire and it is possible to control the tightening.

Now you can put the homemade clamp in a secluded place until next time, and in order not to lose its parts, screw another nut onto the bolt with holes.
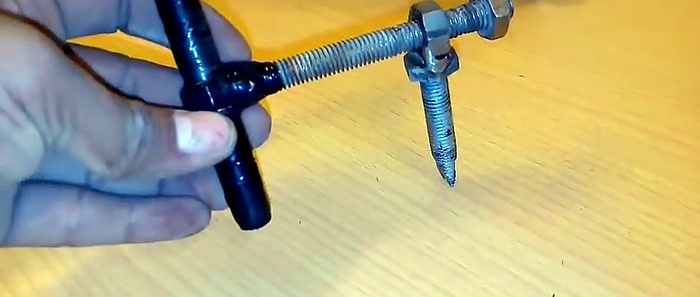
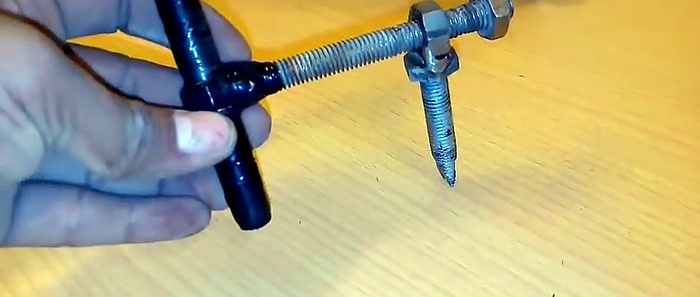
Will need
In addition to the annealed wire and pliers already mentioned above, we will need the following accessories:
- two bolts of the same diameter;
- two identical nuts;
- hairpin and PVC tape;
- fitting with union nut;
- a piece of flexible hose.
Making a homemade clamp
We sharpen the end of the short bolt shaft into a blunt wedge and make a shallow rounded slot in the middle. We weld a nut on top to the head of the upgraded bolt in a vertical position.
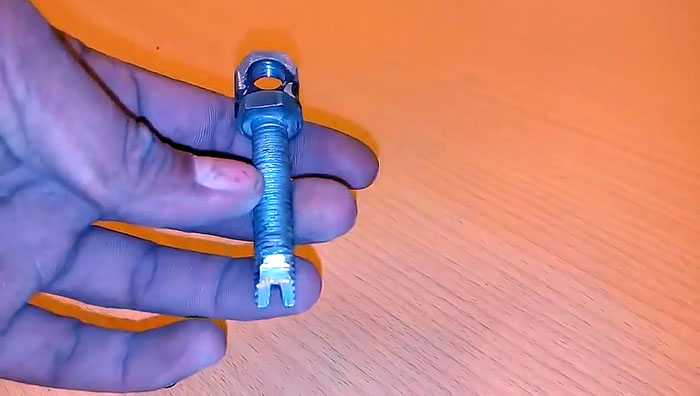
We weld the nut to the long bolt in the same way. We screw the pin into it to the middle and wrap it and the adjacent part of the bolt with the nut with PVC electrical tape to secure the connection and make it easier to use.
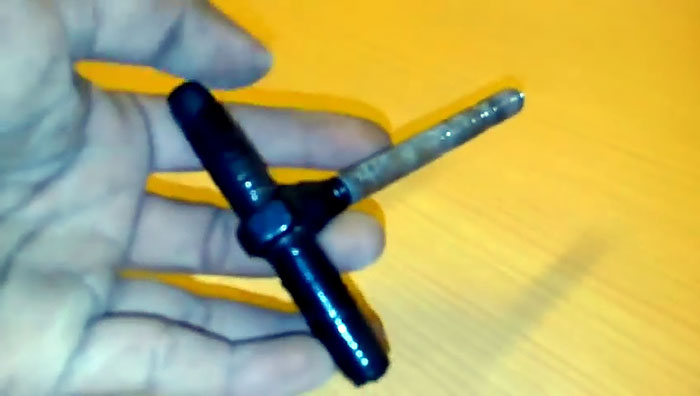
In the center of the rod and, stepping back about 2 cm towards the end, we drill two through transverse holes, parallel to each other, with a diameter of 2.5 mm.
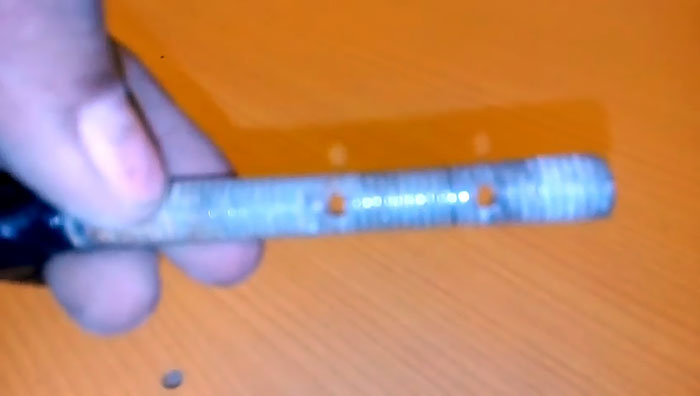
We screw the bolt with holes into the nut welded to the short bolt until the holes are on opposite sides of the nut at approximately the same distance. Our homemade product is ready to go.
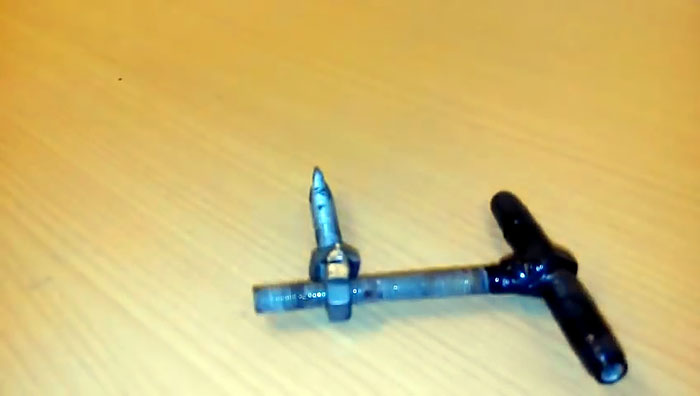
Using the clamp in practice
As an example, we will attach the hose to the fitting of the union nut. It is clear that instead of it, there may be a pipe, a pump pipe, a tap, etc.
Bend the wire in half and cut it from the skein using wire cutters or pliers.
We place it in the place where the wire clamp should be and thread the ends through the loop.
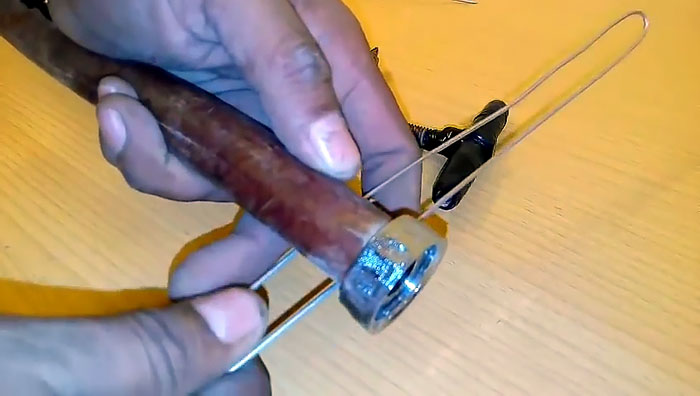
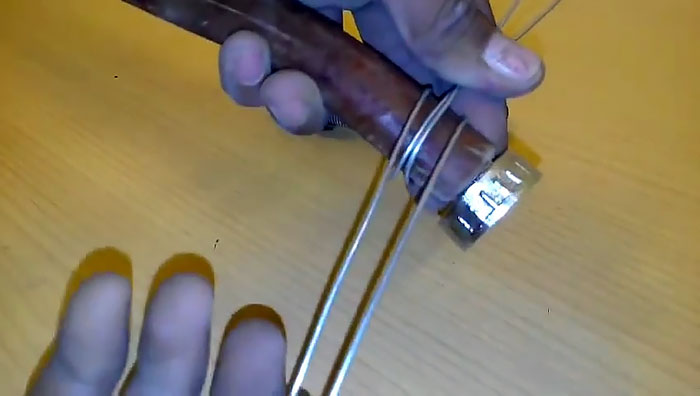
We wrap a piece of wire with a bent end around the hose and thread the ends through the loop again.
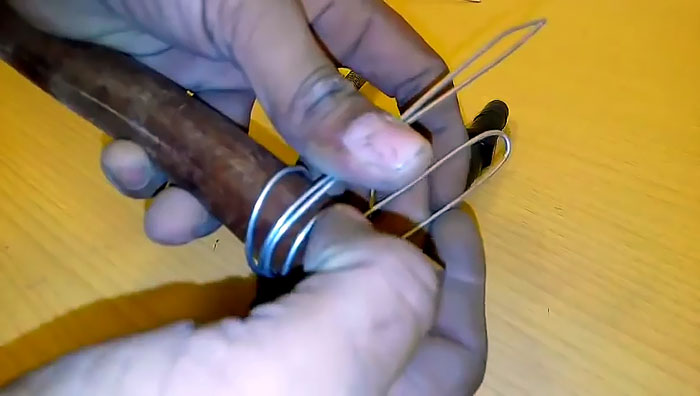
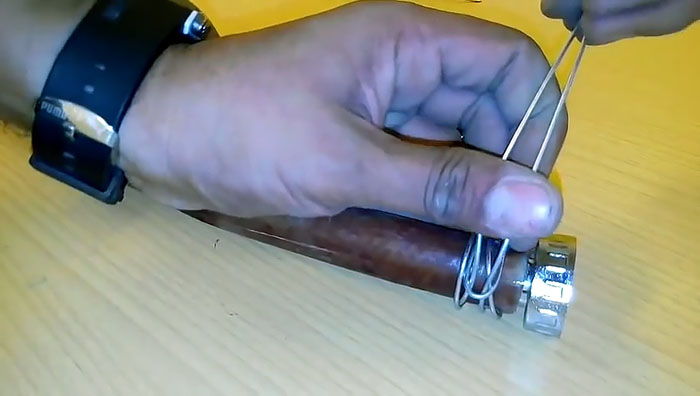
We thread the free ends of the wire into the holes on the long rod of the clamp bolt, and rest the short bolt with the notch against the wire loop.
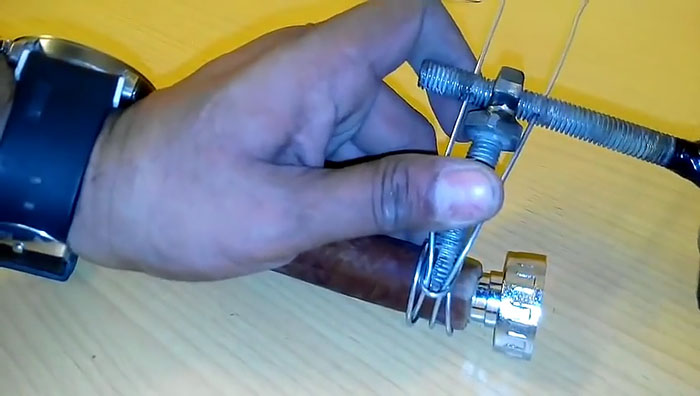
We cut off, leaving small ends, the excess wire on the back side of the holes with wire cutters or pliers.
We rotate the bolt with holes in any direction (in our case to the right), making sure that the wire ends do not jump out of the holes, and the loop does not pop out of the recess of the short bolt. We compress the rings with pliers if they have moved away from each other.

We continue rotating until the wire loops tightly wrap around the hose and provide a tight connection with the union nut fitting.
After this, we rotate the device around the wire loop, using it as an axis of rotation, 180 degrees.
We release the tightening device by rotating it counterclockwise in our case, and cut off the excess wire with wire cutters. We tap the wire ends to the hose.
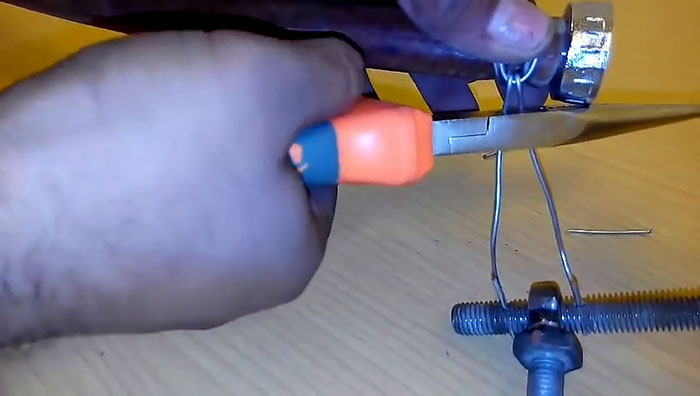
The result is a sealed and durable connection, since in this case there is no danger of damage to the wire and it is possible to control the tightening.

Now you can put the homemade clamp in a secluded place until next time, and in order not to lose its parts, screw another nut onto the bolt with holes.
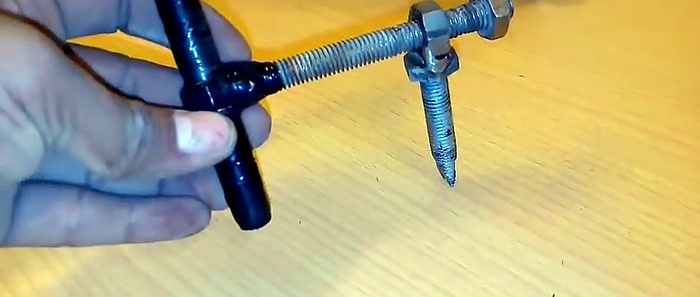
Watch the video
Similar master classes
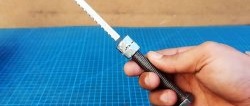
4 necessary tools from a regular bolt
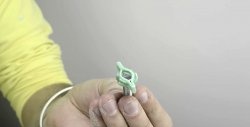
How to make a wing bolt from a regular bolt and a PET bottle
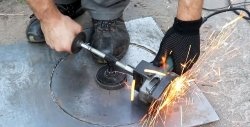
Removable device for cutting circles in sheet metal with
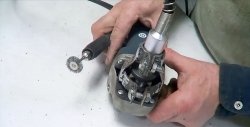
If your Dremel breaks, it doesn’t matter: a grinder can replace it
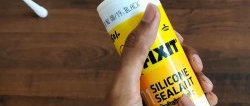
How to use silicone sealant from a tube without a gun
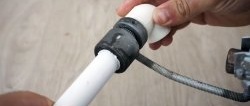
No electricity needed! Simple gas soldering iron for welding
Particularly interesting
Comments (5)