How to quickly make a hinge for a knife sharpener
This unit sets and holds constant the sharpening angle of the tools, which is the determining characteristic in relation to the cutting properties and stability of the blade.
Each tool has its own sharpening angle and depends on the grade of steel used and the type of material being cut.
You can make such a knot yourself in 10 minutes without much expense or effort. At the same time, its functionality will not be inferior to the factory product.
Will need
To work, we will need quite accessible, inexpensive materials, products and tools:
- ball bearing;
- bolt or stud with nut;
- thermoplastic granules (polymorphus) - ;
- container with hot water;
- drill with the required drill bit;
- knife.
The process of making a hinge for a knife sharpener
Preparing polymorphus for work. Read more about this miracle material here - https://home.washerhouse.com/en/5097-termoplastik-samozatverdevajuschij-material-dlja-remonta-i-tvorchestva.html
To do this, heat or pour water into a pan at a temperature of 65 to 90 degrees Celsius. We pour thermoplastic granules into it. Once they become transparent, the thermoplastic is ready to be molded.
We pull it out into a bundle, kneading it with our fingers, and wrap it around the outside of the ball bearing around the entire circumference, trying not to stick to the internal element, which must remain movable.
We thin the girth and assemble the thermoplastic into a short lever, but so that its cross-section is sufficient to ensure the required strength of this element after hardening.
We wrap a piece of polymorphus around the end of a part of the bolt with a nut, which should be completely hidden in the thickness of the thermoplastic, including its outer end. After all, in the finished product this nut will bear all the threading forces.
We cut off excess plastic from one and the other part using a sharp knife. Then we dip their ends into hot water for a short time and combine these two products into one.
We carefully smooth the joint and give it a smooth shape to eliminate stress concentration during operation of the finished unit.
We trim the edges of the hole in the plastic connected to the inner frame with a knife so that nothing prevents it from moving freely in any direction.
We unscrew the bolt from the nut embedded in thermoplastic, since it has served its purpose (helped to create access to the nut), and it can simply be removed.
Using a drill at low speeds, we drill a hole in the plastic just below the ball bearing for the vertical stand, the longitudinal axis of which should be perpendicular to the axis of the bearing. Using a knife, carefully remove the plastic shavings formed after drilling.
Our homemade hinge is ready for use, and it is in no way inferior to its factory counterpart. It can also be bolted anywhere on a vertical stand, providing the desired sharpening angle for the cutting tool.The rod inserted into the hinge will move freely in any direction, providing processing of the blade along the entire length.
Watch the video
Similar master classes
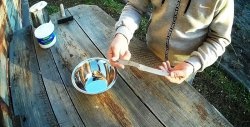
How to make a durable and anatomical knife handle in 10 minutes
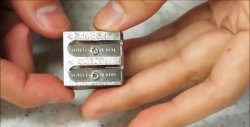
Sharpening and hardening the pencil sharpener blade
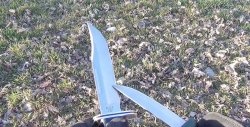
5 ways to sharpen a knife without a sharpener while traveling
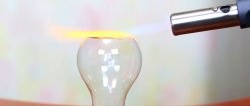
3 useful ideas from a burnt-out incandescent lamp
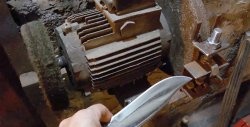
The simplest device for sharpening knives at 30 degrees
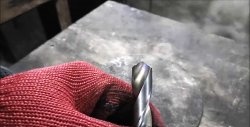
How to properly sharpen a drill by hand
Particularly interesting
Comments (2)