How to solder aluminum for centuries without a special flux
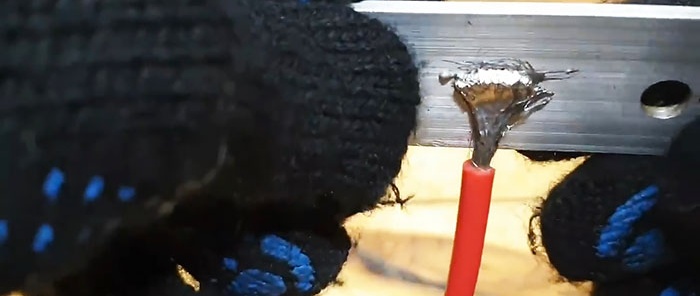
The surface of aluminum is covered with an oxide film, which interferes with soldering. Even if the solder sticks, under load everything falls off. The problem can be partially solved by using specialized fluxes and solders, but there is a simpler method that is much more reliable. In this case, you can solder with the most common inexpensive POS-61 solder.
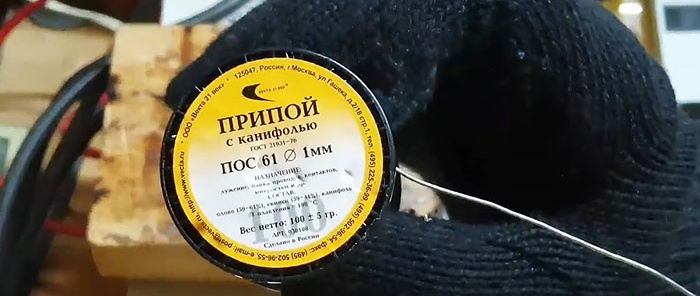
Materials and tools:
- powerful soldering iron 60 W or more;
- solder;
- machine oil;
- flux.
Tinning and soldering of aluminum
A couple of drops of machine oil are applied to the aluminum surface. Its qualities and properties do not matter. It can be synthetic, semi-synthetic, mineral, even sunflower will do.
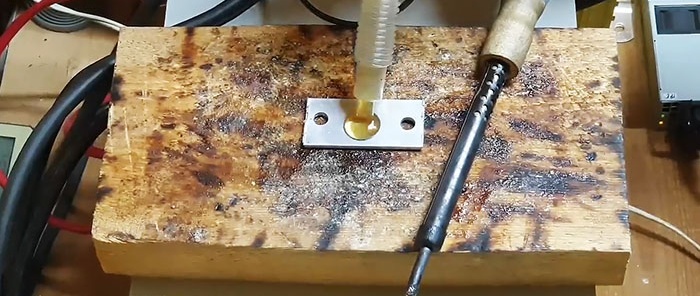
Next, the soldering iron tip is lowered directly into the oil, resting against the aluminum surface. Then solder is applied to it and deposited in the required amount. All this is accompanied by a burning smell, so it is better to work with the hood on or in the fresh air.
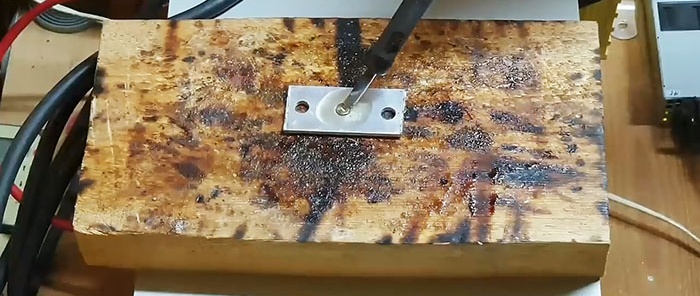
The soldering iron tip must be held until the aluminum part warms up. After this, you can start tinning, but only in the area that is under the oil.You should move the tip back and forth, as if rubbing solder into the surface. This allows the oxide film to be removed and creates micro-scratches for better tin adhesion. In this case, new oxidation does not occur under the oil, since there is no air access.
If a part overheats, you can take breaks to let it cool down. The longer you tin like this, the stronger the solder will hold. On average, tinning will take 1-2 minutes. It is necessary to ensure that the solder completely spreads over the required area. At first it will gather into a ball, but after another minute it will spread evenly throughout the workpiece.
After tinning the aluminum, the wire is prepared. It also needs to be tinned. If it is made of copper, then regular flux is first applied, then everything is generously tinned with tin. It is better to immediately apply more solder.
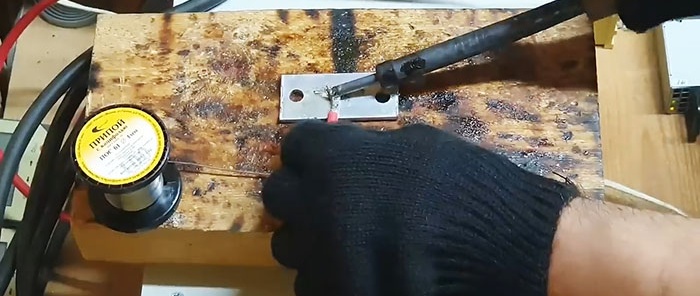
Next, the tinned wire is applied to the tinned aluminum surface. The soldering iron tip rests on top and the parts heat up. As soon as the tin melts at the point of contact, the tip moves further. If there is not enough solder in places, you need to add it.
The larger the workpiece, the longer it takes to heat it up, so in such cases it makes sense to use a more powerful soldering iron. After soldering, the parts are set aside until they cool naturally. The remaining oil is wiped off with alcohol; if it doesn’t interfere, you can leave it like that.
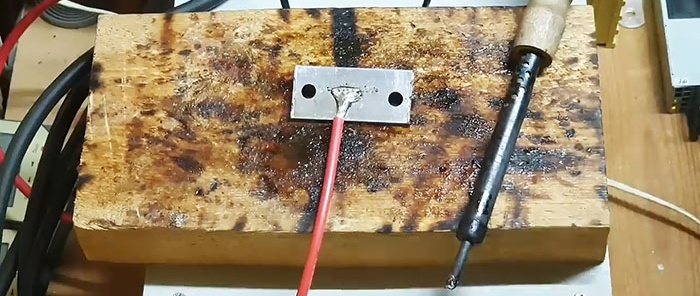
The proposed method allows you to solder tightly to aluminum. It is almost impossible to tear off the wire; it is more likely that its core will break than a solder disconnection will occur.
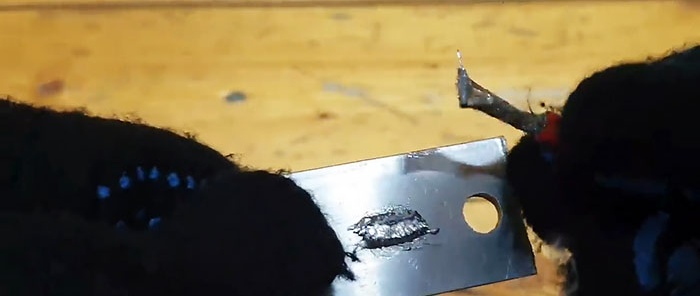
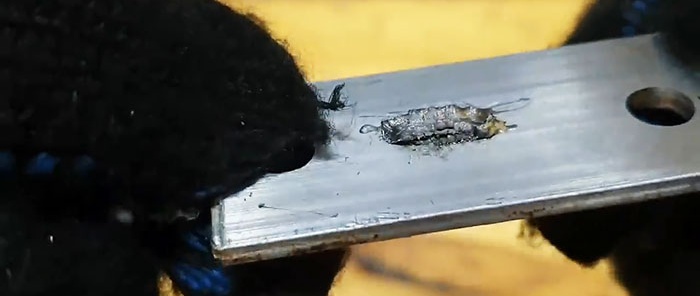
Of course, high-speed soldering will not work with this method, but this is the specificity of aluminum. At home, you won’t be able to make a connection faster and with the same quality using any other method.In this case, you do not need to buy a special flux. If you don’t have machine oil at hand, you can get by with vegetable oil, which is also a plus.
Watch the video
Similar master classes
Particularly interesting
Comments (2)