How to simply solder aluminum tightly with regular solder
Soldering aluminum with standard solder using conventional technology is unreliable and impossible. The tin on it rolls into a ball, not wanting to stick, and if it does stick, the result is a weak connection that breaks under the slightest load. To prevent this from happening, you need to solder in a special way, and then even ordinary solder will hold tight.
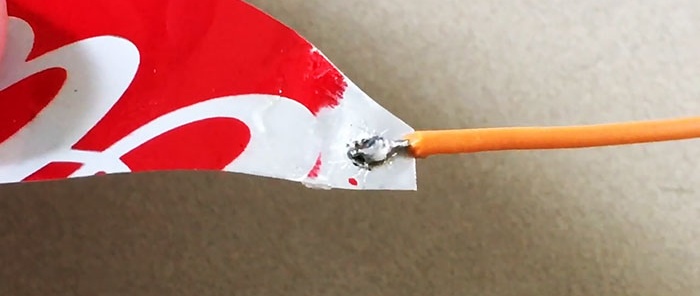
Materials:
- solder 60/40 - http://alii.pub/64fqb2
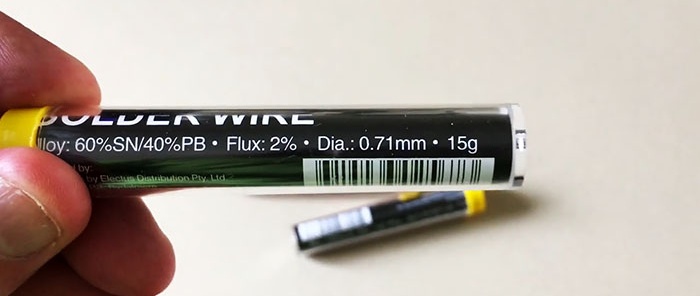
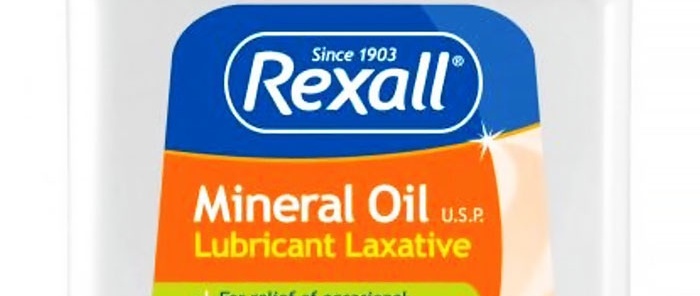
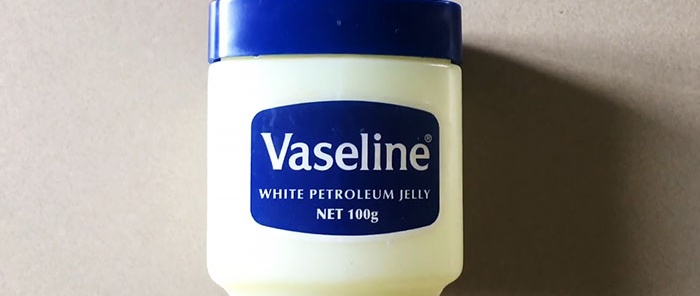
How to solder aluminum correctly
An oxide film instantly forms on the surface of the aluminum, which prevents adhesion between the base and the solder. To prevent it from interfering, you need to create an airless environment at the soldering site. To do this, apply a thin layer of Vaseline to the area of aluminum that has been cleaned of dirt. You can use mineral or other automotive oil instead.
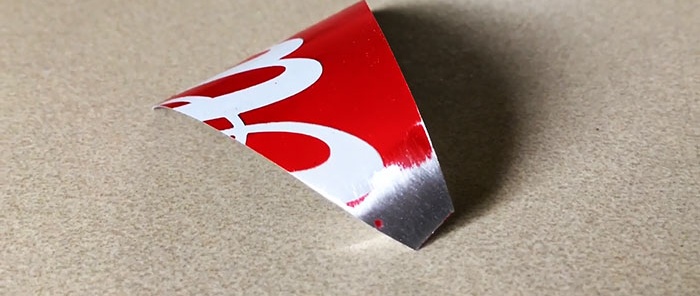
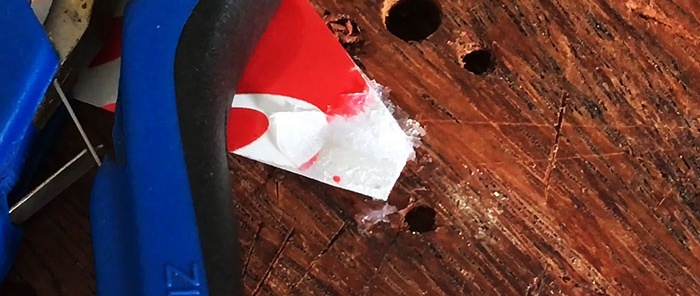
If Vaseline was used, then you need to apply a soldering iron tip to it so that it melts into liquid oil. After this, take a mounting knife or other sharp object and use it to scratch the aluminum under the Vaseline. It is important that the scratches are made on a surface that is sealed from air.As soon as the Vaseline begins to thicken, it should be melted again with a soldering iron tip. You need to actively rub with a knife blade to remove the oxide film on the metal, and in addition to create a relief to which the solder will then stick well.
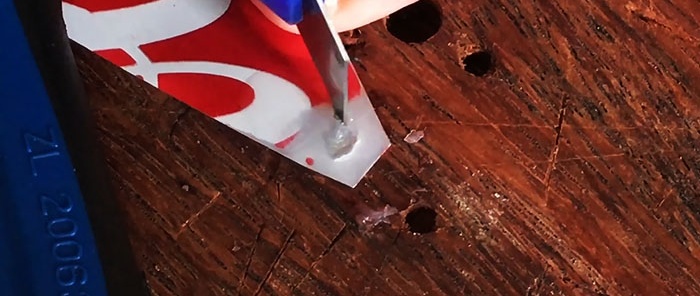
After removing the oxide film, the oil is not erased. A soldering iron tip is applied to the soldering site, and the aluminum is heated to operating temperature. Then the required amount of solder is deposited. It will sit right in the oil.
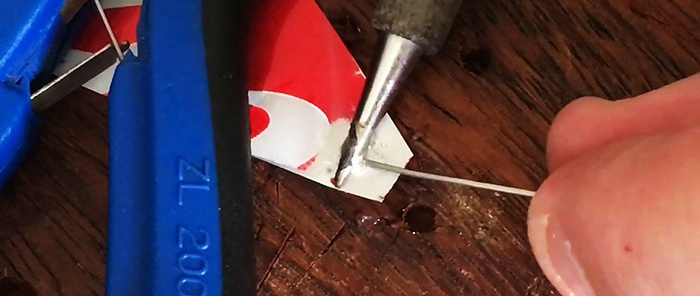
A drop of solder is lightly rubbed over the prepared surface. You need to press it into the resulting scratches. The solder will push the oil to the sides so it won't interfere with adhesion. The absence of an oxide film will allow the tin to stick to the aluminum, rather than forming into a ball that easily falls off.
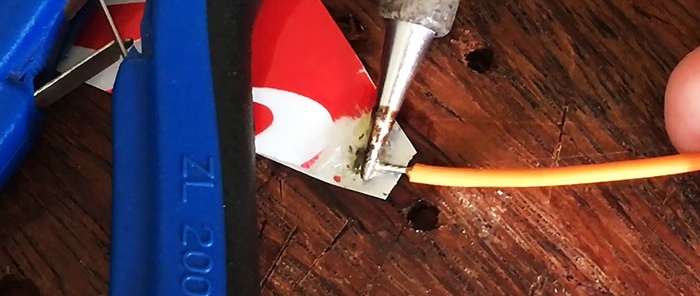
Then, tinned wires, wire, or whatever is needed can be applied to the surface prepared with oil and friction. They will be soldered in a second, without taking all the tin from the aluminum, as usually happens. After soldering, the remaining oil is removed with a cotton swab soaked in alcohol.
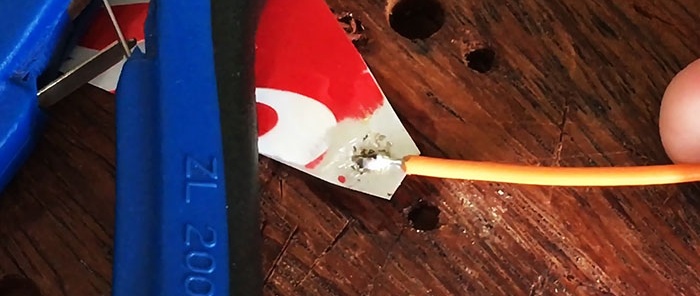
This method allows you to achieve the same soldering reliability as when connecting two copper elements. Moreover, unlike another common method with oil, when the oxide film is removed by five minutes of friction with a hot soldering iron tip, tearing it off with a knife is faster.