How to make a knife handle from bottle caps
The handle made of cork tree bark is ideal for equipping hunting and fishing knives, which have a blade with a tang. It is always warm, slightly elastic, and does not sink, so a knife dropped into water remains on the surface. If desired, you can make it yourself from wine bottle caps and place it on a homemade blade or an old knife.
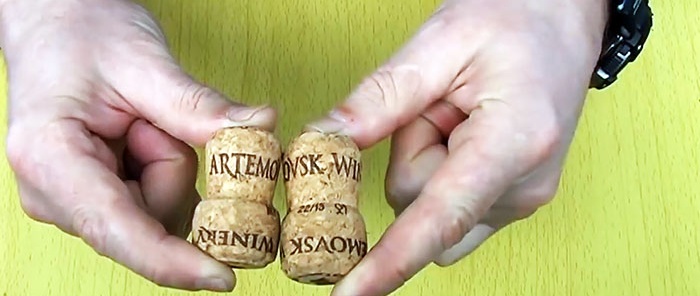
Necessary materials:
- wine or champagne corks - 10-12 pcs.;
- sandpaper P36;
- waterproof glue (you can use Moment Crystal, 88 or another compatible with the cork);
- epoxy adhesive;
- cyanoacrylate adhesive for flexible joints;
- acetone;
- M6 stud;
- nut M6;
- block of hard wood.
Making the handle
The plates for the inlaid handle are made from wine corks. Since they are deformed after being removed from the neck of the bottle, they need to be aligned. To do this, the plugs are heated in the microwave for 1 minute, after which they themselves return to the correct shape.
The plate is glued together from 2 corks. Before this, they cut off one side lengthwise.
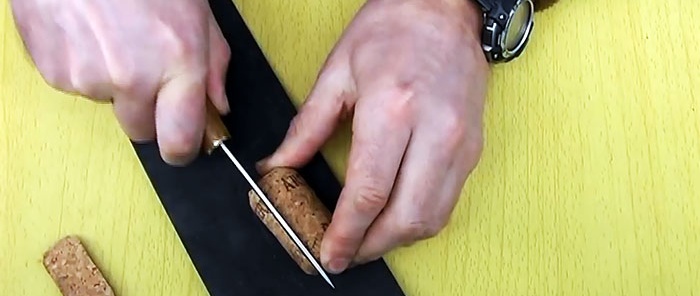
The resulting cut is sanded using coarse P36 sandpaper, glued with double-sided tape to a flat base.The cork is rubbed in by moving towards itself. It is enough to do it 5-10 times and the cut will be smooth. It is necessary that when joining the sections of 2 plugs there is no gap left.
Having cut and sanded 2 corks, you need to coat the prepared sides with glue 88 or Moment.
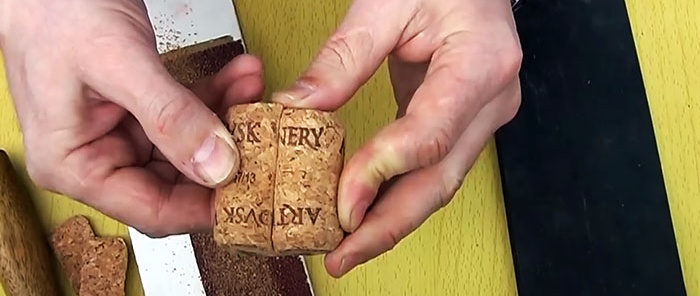
Afterwards, a pause is made according to the instructions until the solvent evaporates from the glue, and the 2 plugs are connected together. They need to be squeezed very tightly together.
After gluing, 2 wide sides of the corks are cut off, parallel to each other.
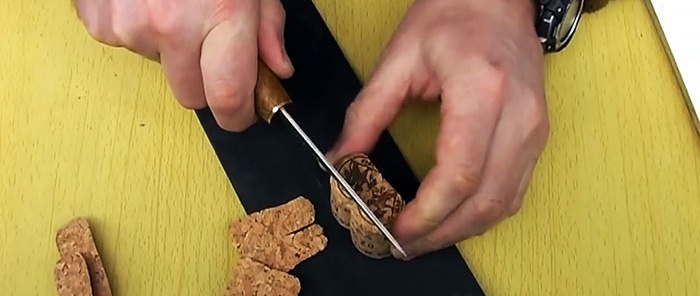
The result is a typesetting plate. You should make 5-6 such plates and sand their sides.
The records will be assembled onto the shank. To do this, a through slot is cut in their center with a jigsaw file.
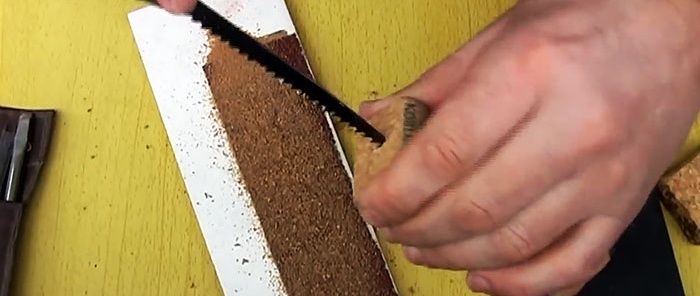
You need to make a cut in the first plate in the direction of gluing, and in the second one across the seam. Thus, in the future, the component elements of the handle will support each other and will not be able to come apart along the length.
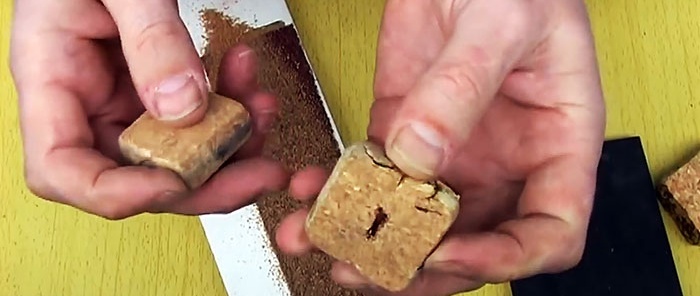
To make the knife float, its back and bolster should be cut from hard wood.
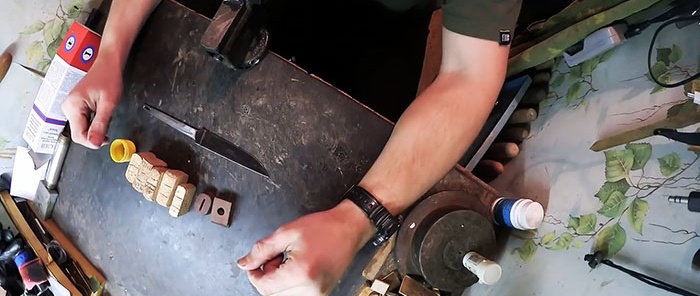
To secure and tighten the plates, a thread must be cut at the end of the shank. In most cases this is not possible, so you can simply weld a stud with an M6 thread or rivet it.
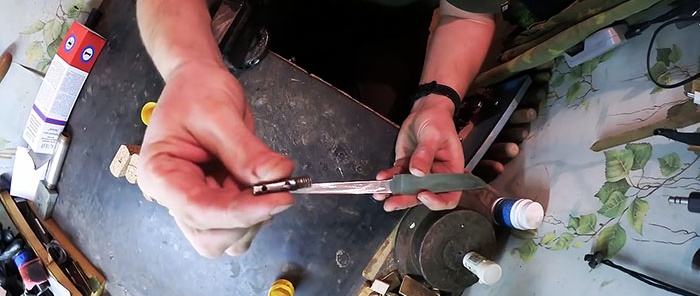
A bolster is placed on the shank, then plates are assembled alternating the direction of the slot.
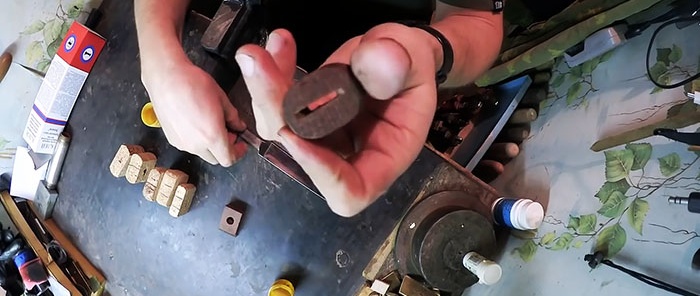
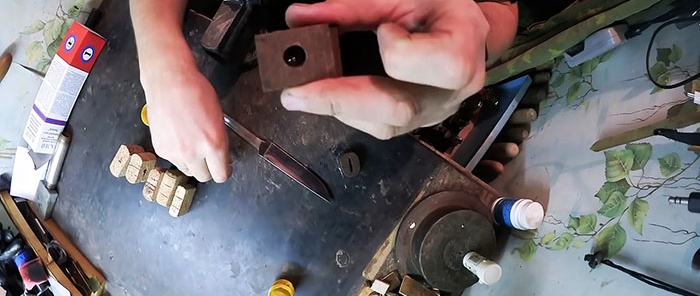
Before installation, all elements are lubricated at the joints with epoxy glue.
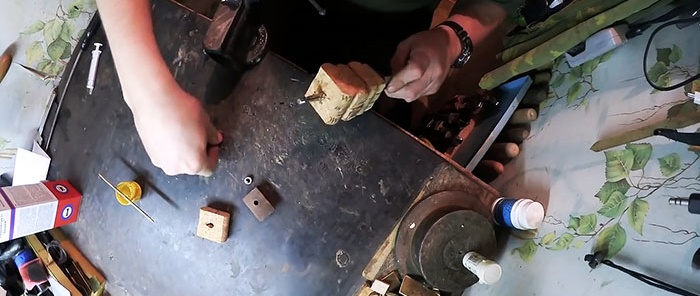
Their number is selected in such a way that the handle is 5 mm longer than the shank. Then the backplate is placed. There is no longer a slot in it, but a round through hole for the pin. At the outer end it expands to accommodate an M6 nut with ground edges.
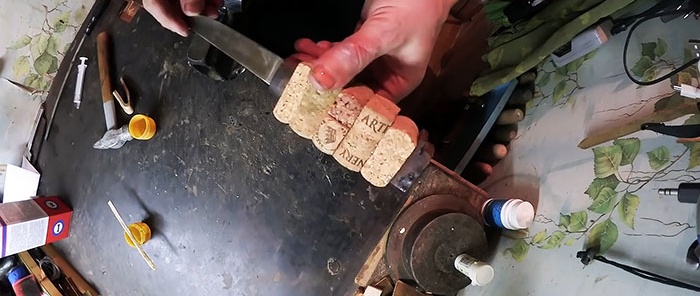
The nut is then tightened and compresses the plates.The remaining mounting hole for the nut in the end of the butt plate is sealed with a small plug cut from scraps.
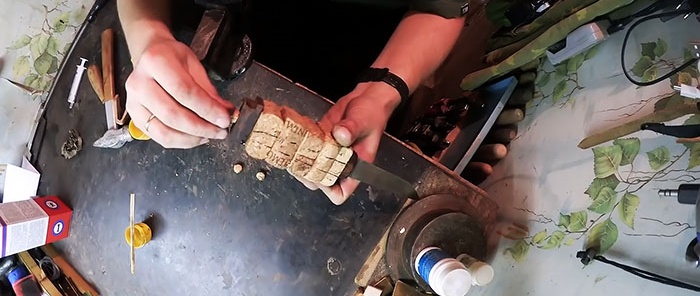
After the epoxy has dried, the rough handle is cut with a knife to the desired shape.
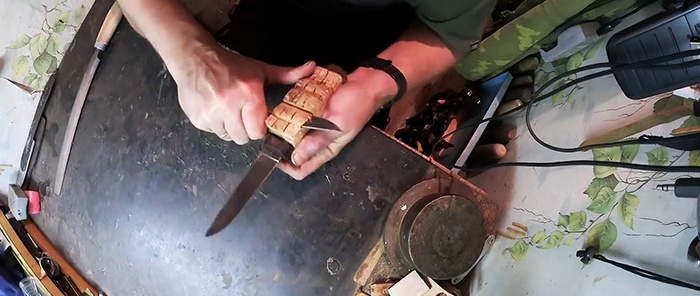
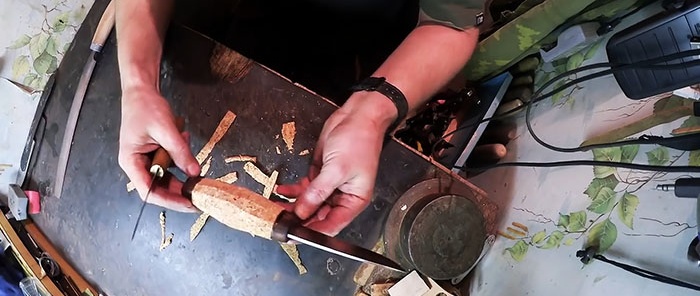
Then it is sanded with sandpaper.
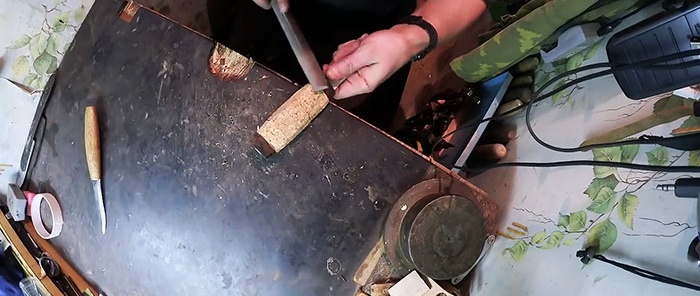
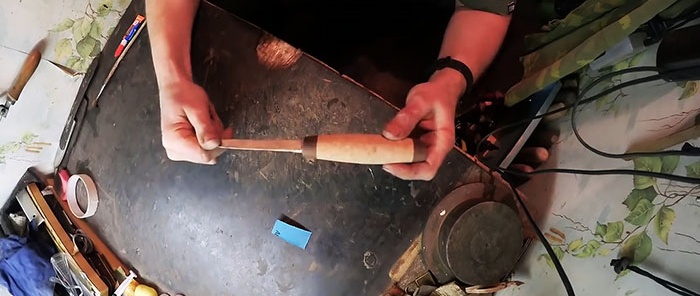
To prevent the cork from absorbing water, it must be soaked. To do this, mix 50 parts of acetone and 1 part of cyanoacrylate glue for flexible joints.
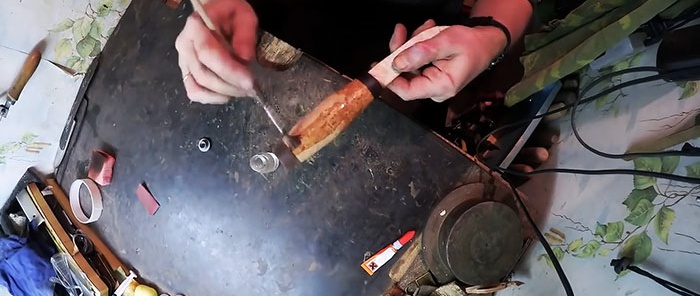
The resulting solution penetrates deeply into the pores of the handle, hardens there and prevents moisture absorption. Impregnation is applied at intervals of 15 minutes until the surface of the handle becomes glossy. Then, for an even shine, it is wiped with a cloth with acetone to erase surface deposits.
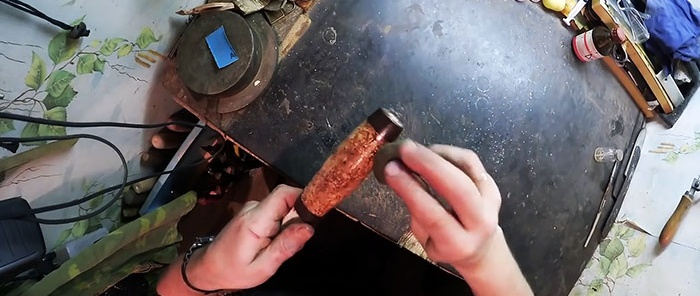
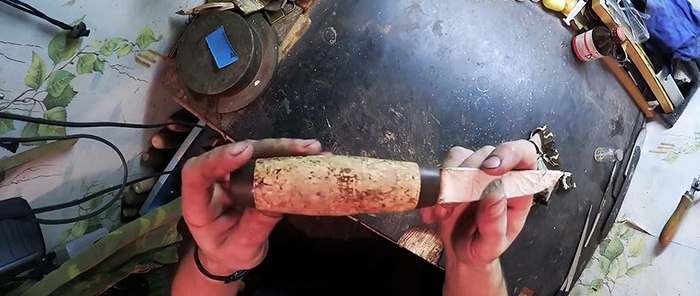
To make such a handle, you will have to spend at least 1 working day, but then the knife will not drown in the river while hunting or fishing. The cork handle is always warm, it does not rub your hand, it looks beautiful, and does not rot, so it is suitable for any working blade with a tang.
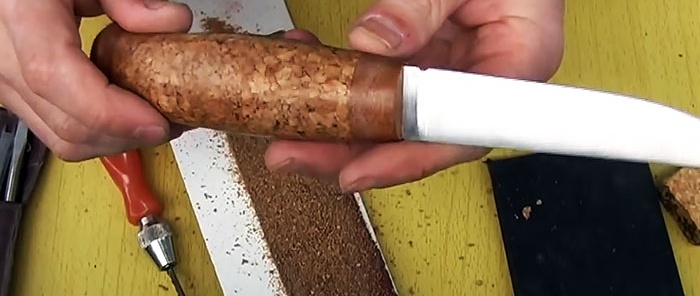
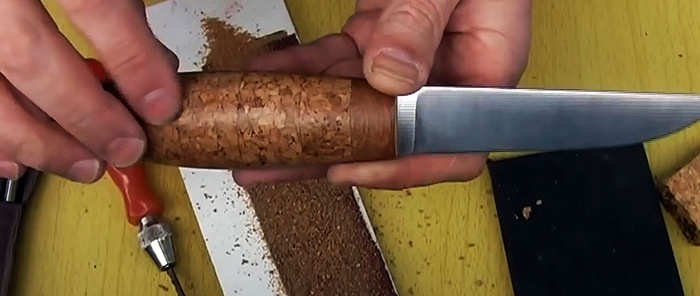
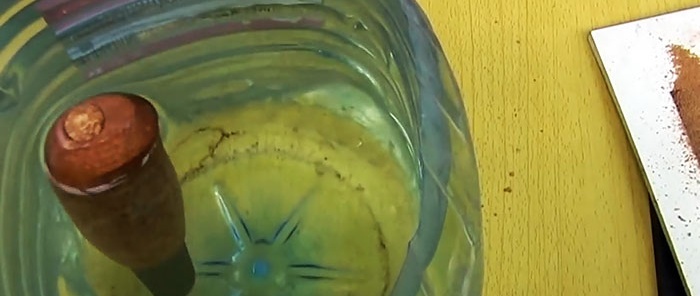