How to make a low-voltage mini cutting machine from a cardan cross
For those who do not have a workshop and have to work directly in the apartment, an important parameter when choosing electrical equipment is its noise level. Finding such a tool is not so easy, but much of what you need can be done with your own hands, for example, a cutting machine.
Basic materials:
- motor 12 - 24 V, 200 W, 6000 rpm -
- power unit;
- profile pipe 100x50 mm;
- profile pipe 20x20 mm;
- universal joint;
- bearings 2 pcs.;
- sheet steel 3 mm;
- corner 25x25 mm;
- pulleys 2 pcs.;
- drive belt.
Mini machine manufacturing process
For the base of the machine, you need to cut 220 mm of a 100x50 mm profile pipe.
It is necessary to attach the universal joint to it. It can be welded, but it is better to screw it in order to be able to adjust the cutting angle. To do this, a hole is drilled in the pipe, offset to the side, and a nut with a sleeve is machined out. Using the latter, the hinge can be screwed on.
A piece of pipe is welded onto one axis of the cross. A housing with two bearings and a plate for mounting the electric motor are welded onto its end.
At the opposite end of the base, 2 longitudinal slots are made for the sliding vice.
Then the jaws of the vice are cut out from the corner. One of them is screwed to the base in front of the slots. The second one should be sliding. To do this, a strip is screwed to it with 2 screws so that they can move along the slots. Also, from the square you need to make a stop with a threaded thread, during rotation in which the pins can be unclenched or compressed in a vice.
The rotating bracket of the machine must be extended by welding a piece of pipe at an angle. A plastic or wooden handle will be screwed to it.
Next, the parts are assembled. Bearings with a sleeve between them are inserted into the housing on a rotating bracket. You need to insert a bolt with a pulley through them. Then the engine is screwed on, also with a pulley, and the belt is tensioned. You will need to make the belt protection from a bent channel or loose along a profile pipe.
You also need to install a cover to protect against sparks.
It can be removed from a broken grinder or purchased separately. Then the vice is assembled, the power supply is connected to the motor, and the cutting disc is installed. The entire machine is ready for use. For convenience, it is advisable to install the engine start button on the lever.
A self-assembled machine with such an engine is capable of cutting both metal and wood, depending on the equipment, and does it relatively quietly.
Watch the video
Similar master classes
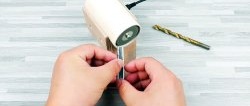
Make this machine and forget about stupid drills forever
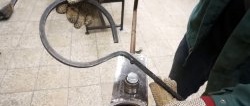
How to make a bending machine from bearings
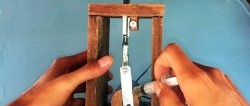
Do-it-yourself mini jigsaw 3.7 V
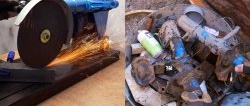
How to make a cutting machine from an angle grinder and old shock absorbers

Working design of a homemade lathe
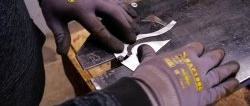
How to make a simple machine for shaped cutting of metal from a drill
Particularly interesting
Comments (5)