9 ways to properly and reliably connect wires without a soldering iron. Auto electrician tips
When doing electrical installations, especially in auto electrics, you have to do a lot of splicing of wires. Depending on how well this is done, the reliability and durability of the contact depends. Let's consider 9 options for connecting wires.
1. Twisting with heat shrink
The edges of the wires are stripped of 3 cm of insulation, folded parallel and twisted.
Then they are separated, the twist is tucked to the side and heat shrink is placed on top.
We obtain a moisture-resistant connection with a sufficient contact length for current transmission without loss.
Due to heat shrink compression, it will not come undone when stretched.
2. Power twist
If the twisted wire is under tension, then it is better to make the connection a little differently. The stripped wire strands are folded crosswise in the center and twisted together several times.
The edges are then wound each onto the opposite core in the direction of the insulation. This twist will not break even without heat shrinking.
3. Conventional connection sleeve
The edges of the wires are stripped of insulation, joined in a sleeve and crimped with crimping pliers. We get a quick, fairly strong, but not waterproof connection.
4. Connection sleeve with heat shrink
You can also use a sleeve with heat shrink. It is installed using pliers, just like a regular one, but after that it is additionally heated. After shrinking, such a connection will be waterproof.
5. Heat-shrinkable sleeve with solder
For connection, you can use a heat-shrinkable sleeve with solder. You need to join the edges of the wires in it, then heat it with a hairdryer. Inside it there is solder, which solders the wires. The tube itself has additional sealing rings along the edges, so after shrinking it is guaranteed not to let water through.
6. Terminal block and crimp lugs
It is convenient to connect the wires with a terminal block, but to do this, crimp lugs should be placed on the stripped wires. This method allows you to disconnect the line if necessary. It is good to use for connecting lighting fixtures.
7. Flat insulated connector
When you need to make a very compact and quick disconnectable connection, you can use flat insulated connectors. They are crimped on the edges of the wires, then connected to each other. Please note that these connectors are not water resistant.
8. Round insulated connector
It is also convenient to use a round connector. It is available in a wide range of sizes, including large gauge wires. The circular connector also does not provide moisture resistance.
9. End terminal block
It is possible to make a reliable connection of the wires by twisting them, and then inserting it into the terminal block and clamping it. It provides insulation and also enhances contact.One wire is tucked in and secured to the terminal block with a tie for reliability.
Watch the video
Similar master classes
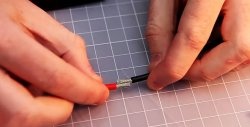
The strongest connection of large cross-section wires without thickening
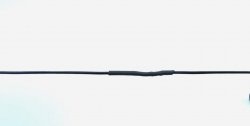
The most reliable connection of wires without a soldering iron
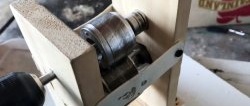
How to make a machine from rotors from electric motors for fast
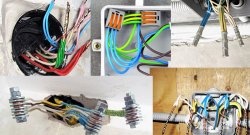
Methods for connecting wires in a junction box
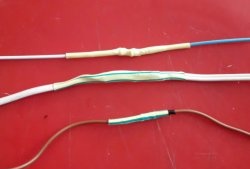
Twisting of wires without soldering that cannot be broken
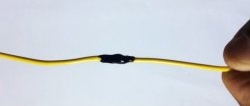
How to make a twist waterproof
Particularly interesting
Comments (0)