3 reliable wire connections with and without soldering
When performing electrical installations, it may be necessary to connect wires. This is done in different ways. Often everything is solved by twisting and soldering, but you can also use faster, more reliable methods.
1. Twisting with soldering
To make this connection, you need to strip the edges of the wires by 30-50 mm. The exposed strands cross in the center and wrap around each other.
After this they need to be soldered.
You can insulate the connection with heat shrink or electrical tape.
This method is more reliable, since the slightest oxidation of the cores is excluded. The method is intended for splicing wires from the same metal. But there are also disadvantages - very poor moisture resistance of the connection.
2. Crimp sleeve with heat shrink
The stripped edges of the wires can be crimped with pliers into a sleeve with heat shrink.
Then it warms up to shrink the tube. We get a very fast connection with good insulation.
Moreover, they can splice wires from different metals.
3. Heat shrink with solder
It is very convenient and quick to connect wires with heat shrink and solder. To do this, their edges are cleaned. Then the bare wires are inserted into the tube up to the solder ring.
When heated with a hairdryer, the heat shrink will shrink, while the solder in the center solders the cores, and the glue rings on the sides will ensure a 100% waterproof connection.
This method is used only when splicing cores of one metal, but it does not require crimping pliers.
Connecting tubes are inexpensive and you can immediately purchase a case of various diameters - http://alii.pub/5rlh3q
Simple twisting, the most unreliable but fast connection
This is the fastest, simplest and at the same time the most unreliable connection method, which can be used, but it is better not to use it when splicing wires with cores of the same metal. Their edges are cleaned and twisted together. Then the twist is folded and wrapped with electrical tape.
Watch the video
Similar master classes

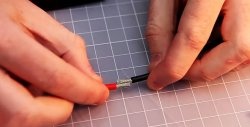
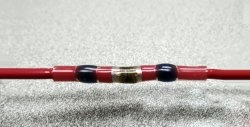
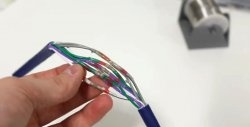
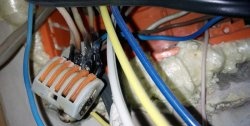
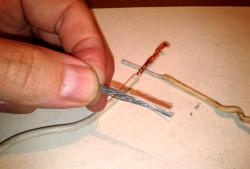