How to make a reliable wood chipper from junk
In gardens and summer cottages, after pruning trees and thinning bushes, harvesting vegetables, and cleaning the area, a lot of branches, tops and weeds are formed. To dispose of them, there are expensive factory shredders. In order not to waste money, you can make it yourself from waste materials.
Will need
Materials:- flange electric motor;
- two square steel plates;
- old saw blade;
- various bolts, nuts and washers;
- bushing with a stepped outer surface;
- bent corner;
- steel strip;
- steel welded pipe;
- round pipe;
- spray paint in two colors, etc.
Wood chipper manufacturing process
Taking into account the power and dimensions of the flanged electric motor, we cut out two steel plates, find their centers and drill holes to match the diameter of the motor axis.
On one plate, in proportion to the diameter and location of the holes on the electric motor flange, we drill matching holes.
We fix the plate in a vice and use a file to transform the round holes into square ones to secure it with bolts with a square headrest to the engine flange.
We cut out a plate of the given dimensions from an old saw blade and drill a hole in the center.
In the plates on the diagonals along the markings opposite the corners, we drill four holes for long bolts.
Between them we drill three more holes at the same distance from the center as the four previously drilled. At a slightly larger radius from the center, we drill seven more holes.
We put a bushing on the electric motor shaft with a plate fixed to the flange with the larger outer surface towards the top.
We place a sharpened knife of the required shape and two clamping rings on it.
In the four holes in the corners of the plate, located at a smaller radius from the center, we insert bolts from below, which we secure on top of the plate with nuts. We screw the tall ones on top of these standard nuts and also tighten them.
We put a second plate on the four long bolts and the motor shaft so that it rests on the ends of the tall nuts.
We secure it to the shaft with a washer and a hex bolt, using the central threaded hole at the end of the shaft, as well as nuts screwed onto the long bolts.
To adjust the knife relative to the top plate, washers are placed between the nuts on the bolts.
We cut off the bolt rods above the nuts with a grinder.
For the base of the engine, we make a frame from a bent angle by welding and fasten it to the base with bolts.
We cover seven bolts located at a smaller radius from the center of the plates with a steel strip of width equal to the distance between the plates.
We insert seven more bolts into the holes located at a larger radius from the center and tighten them with nuts.The strip is between the bolts along the entire circumference and therefore cannot move either outward or inward.
On the outer plate between the electric motor shaft and the bolts, we cut out a square hole, to which we weld a steel welded pipe (receiver) with a beveled end, through which we will feed materials for grinding into the shredder.
In four sections of a round pipe, equal in length, we make slots at one end, insert them into the shelf of the bent corner, oriented downwards and slightly to the sides for stability, and weld them.
We paint the homemade product in two colors, in accordance with the functionality (safety) of the parts being painted, and it is ready for use.
Watch the video
Similar master classes
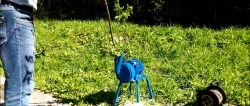
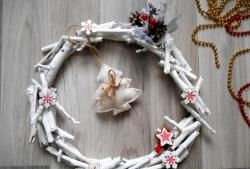
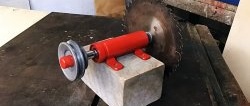
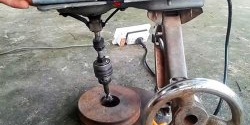
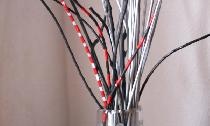
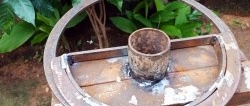