How to make a device for twisting a strip into a spiral without heating
Elements twisted into a spiral from a steel strip serve both as part of the power structure of window and door grilles and as a decorative decoration. Their manufacture using universal tools requires the participation of two people and often heating of the workpiece. But, if you make a fairly simple device at virtually no cost, then this operation can be performed by one person without any heating.
Will need
- A piece of old pipe;
- tape measure and marker;
- round steel rod;
- steel corner;
- I-beam;
- welding machine;
- drill, etc.
The round rod should fit into the pipe without much effort.
The process of manufacturing a device for coiling a spiral
On the pipe and the steel round rod at both ends we make markings for the transverse and longitudinal design cuts, respectively. From the pipe and steel rod, according to the markings, we cut two fragments of the required length.
We make cuts in the fragments of the rod according to the markings and insert them into the pipe fragments flush on one side and make markings on the pipe sections, focusing on the cuts in the inserts, and also make cuts in them.
On the other hand, we weld the inserts to the pipe fragments from the inside.
We press two equal length fragments of a steel angle on both sides to the top flange of the I-beam so that the flanges of the angles lie on the flange of the I-beam and are symmetrical to each other.
In the gap between the flanges of the corners, we lay a length of pipe with an insert welded into it longitudinally so that the cut is oriented vertically and weld it to the corners, and this unit should move freely along the flange of the I-beam.
To prevent this unit from jumping off the I-beam flange to the outer flanges of the corners from the inside under the I-beam flange in the longitudinal direction, we weld along a piece of reinforcement of the required diameter.
We center the second fragment of the pipe with an insert with a cut, freely moving inside the pipe, using a straightened steel strip. We place a steel plate under it, thick enough to center the cuts in height.
We weld the plate with the tube and insert along the line of the I-beam end.
We weld a knob with a handle to the outer end of the fixed unit insert.
We insert a steel strip into the cuts of the inserts, pressing the movable unit against the workpiece, and rotate the handle, then the strip gradually transforms into a spiral. Moreover, the more revolutions are made, the thicker the spiral will be.
Watch the video
Similar master classes
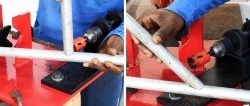
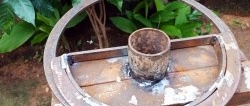
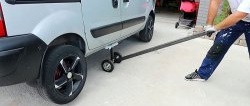
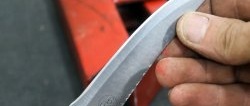
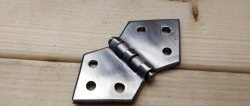
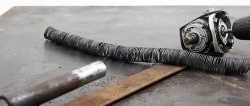