Now it’s convenient to sharpen knives: how to make a simple sharpening device
Working with a dull knife is difficult and dangerous. If it slips off the material, it can injure your fingers. Manual editing requires experience, as it is difficult to maintain the sharpening angle along the length of the blade. Good devices for this purpose cost several thousand rubles. Fortunately, it is possible to do it yourself. To do this, it is enough to have metalworking and welding skills.
Work on a homemade product begins with the preparation of the following materials and products:
In your work you will also have to use a vice, welding machine, grinder, drill and scissors.
The sharpening angle of knives depends on their purpose.We will focus on home kitchen knives, for which it is 25-30 degrees. First, we cut off the required length of the square pipe and form a cut at one end at an angle of 25-30 degrees.
We form a steel plate of the appropriate dimensions and weld it along the contour to the inclined section of the square pipe.
We clean the seams with a grinder and remove metal deposits. We make the surface of the inclined plate smooth, and the contours without nicks or irregularities.
In two small rectangular plates, moving away from one end along the length, we drill holes. We round the corners of the plates above the holes. We weld them vertically to the short plane of the square pipe connected to the inclined end, slightly retreating from the other end and the side edges. Moreover, the holes should be on top.
In a square pipe of a smaller cross-section, we drill through holes in the opposite edges in the center, slightly moving away from the end. We also form the second end of the pipe at an angle of 25-30 degrees, using a grinder.
We place a smaller pipe between the “ears”, and using a suitable bolt and nut, connect them so that the smaller pipe can rotate freely around the bolt.
We weld a steel plate to the inclined plane of the end of the smaller pipe, which would completely cover the lower one in width and length.
We drill a larger hole in the top of the U-shaped plate and weld a nut of the required size under a bolt of the required length. We weld the legs of the resulting structure vertically to the larger square pipe so that the smaller square pipe is between them.
For beauty and protection, we paint the device from an aerosol can. We glue strips of rubber to the mating inclined plates, covering their dimensions with a margin.
After the glue has hardened, use scissors to cut off the excess rubber protruding beyond the contours of the plates.
We clamp the base of the homemade product in a vice. We place the butt of the knife blade between the plates and secure it with a bolt in the U-shaped plate. Now the knife can be sharpened or edited without fear of disturbing the sharpening angle.
Will need
Work on a homemade product begins with the preparation of the following materials and products:
- two sections of square pipes of different sections;
- two steel plates of equal width but different lengths;
- pairs of identical rectangular strips of steel;
- two different pairs of bolts and nuts;
- U-shaped blank from steel strip;
- rubber strips;
- glue for gluing rubber to metal;
- a can of aerosol paint.
In your work you will also have to use a vice, welding machine, grinder, drill and scissors.
Fixture manufacturing process
The sharpening angle of knives depends on their purpose.We will focus on home kitchen knives, for which it is 25-30 degrees. First, we cut off the required length of the square pipe and form a cut at one end at an angle of 25-30 degrees.
We form a steel plate of the appropriate dimensions and weld it along the contour to the inclined section of the square pipe.
We clean the seams with a grinder and remove metal deposits. We make the surface of the inclined plate smooth, and the contours without nicks or irregularities.
In two small rectangular plates, moving away from one end along the length, we drill holes. We round the corners of the plates above the holes. We weld them vertically to the short plane of the square pipe connected to the inclined end, slightly retreating from the other end and the side edges. Moreover, the holes should be on top.
In a square pipe of a smaller cross-section, we drill through holes in the opposite edges in the center, slightly moving away from the end. We also form the second end of the pipe at an angle of 25-30 degrees, using a grinder.
We place a smaller pipe between the “ears”, and using a suitable bolt and nut, connect them so that the smaller pipe can rotate freely around the bolt.
We weld a steel plate to the inclined plane of the end of the smaller pipe, which would completely cover the lower one in width and length.
We drill a larger hole in the top of the U-shaped plate and weld a nut of the required size under a bolt of the required length. We weld the legs of the resulting structure vertically to the larger square pipe so that the smaller square pipe is between them.
For beauty and protection, we paint the device from an aerosol can. We glue strips of rubber to the mating inclined plates, covering their dimensions with a margin.
After the glue has hardened, use scissors to cut off the excess rubber protruding beyond the contours of the plates.
We clamp the base of the homemade product in a vice. We place the butt of the knife blade between the plates and secure it with a bolt in the U-shaped plate. Now the knife can be sharpened or edited without fear of disturbing the sharpening angle.
Watch the video
Similar master classes
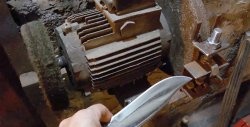
The simplest device for sharpening knives at 30 degrees
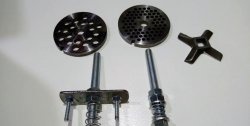
Device for sharpening meat grinder knives
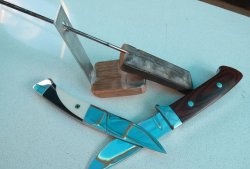
A simple tool for sharpening knives at a fixed angle
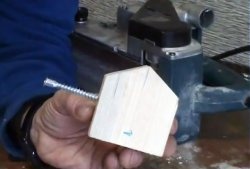
How to quickly make a device for sharpening drills
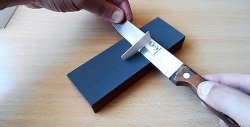
A simple device for checking the correct angle when manually
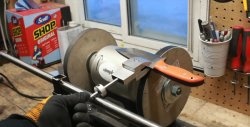
How to make a complex sharpener for simple knife sharpening
Particularly interesting
Comments (5)