How to make a device for winding springs from a grinder gearbox
Almost all mechanisms that surround us in everyday life contain springs that periodically wear out and require replacement. It is not always possible to find an analogue, especially for equipment from previous years of production. You can get out of this difficult situation by making a spring with your own hands. To do this, we will make a simple machine from scrap materials, spending a little time and having basic skills in working with metal.
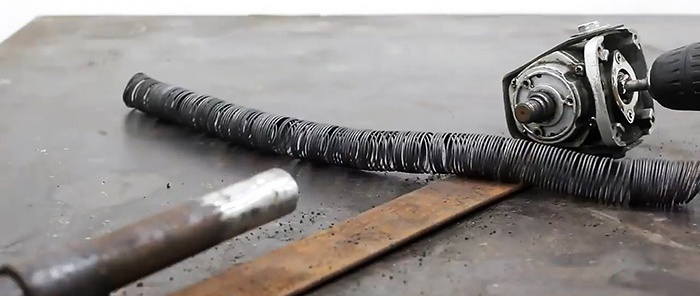
Most of the materials and equipment that we need for work can be found in a home workshop:
We will have to use: welding machine, grinder, wrenches, drill, vice, etc.
We clean the ends of the old round pipe of the required diameter.
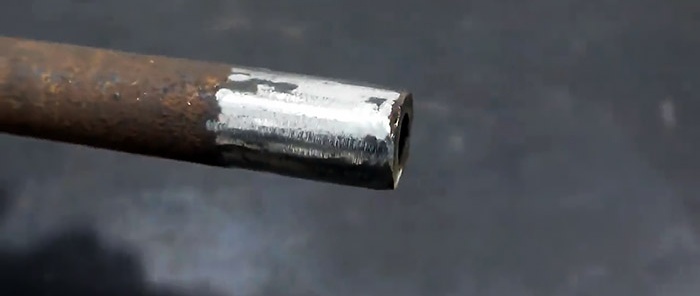
We weld a hex nut of suitable size to one end of it and grind the welding area with a grinder.We screw the nut that we just welded to the pipe onto the output shaft of the gearbox of the faulty angle grinder.
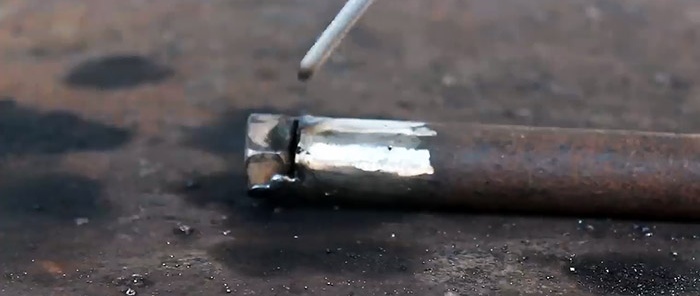
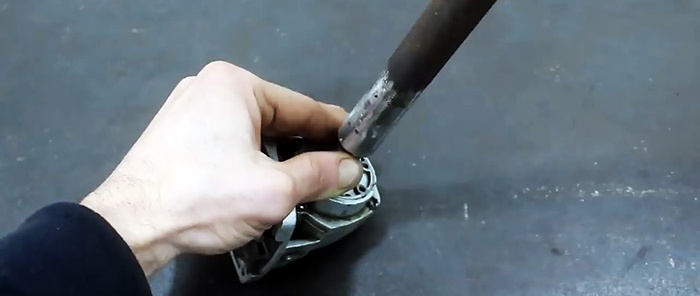
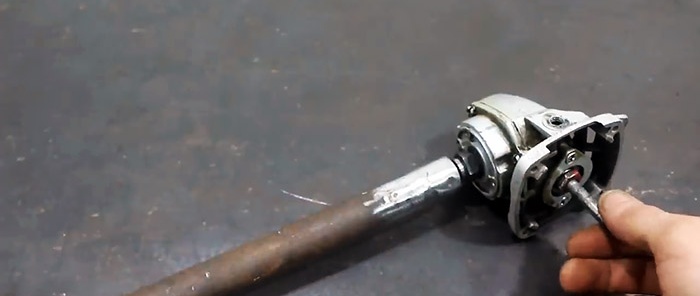
To one edge of a fairly wide and strong steel strip, slightly longer than the pipe with the gearbox, we weld a U-shaped bracket with holes at the ends, one of which is oblong.
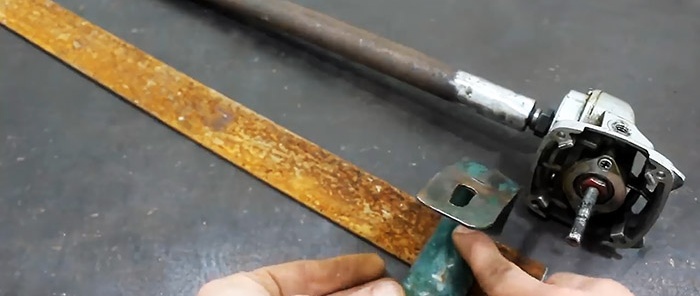
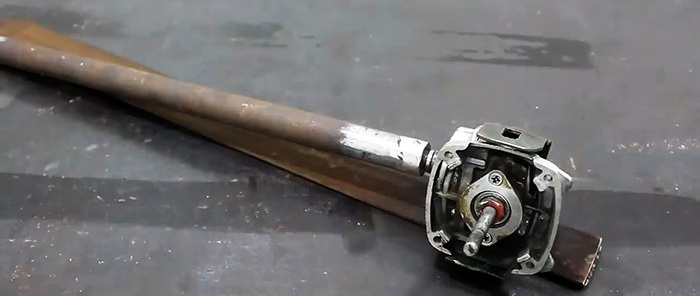
We place the gearbox inside the bracket, orienting the screwed pipe along the steel strip. Using bolts and washers, secure the gearbox to the bracket using the appropriate holes.
On the free end of a long pipe we put a short piece of round pipe of suitable size, under which we install a fragment of a square pipe and sequentially weld all these parts to each other.
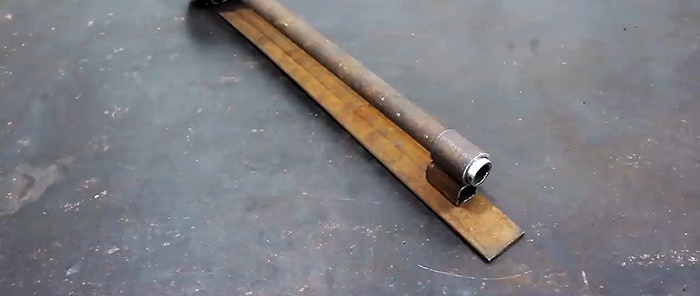
We twist a long pipe with a nut from the output shaft of the gearbox, clamp it in a vice and, stepping back slightly from the nut, drill a transverse hole in its wall with a drill. We insert the pipe with the nut forward into the fixed support from the outside, apply grease to its free end and screw it back onto the output shaft of the gearbox.
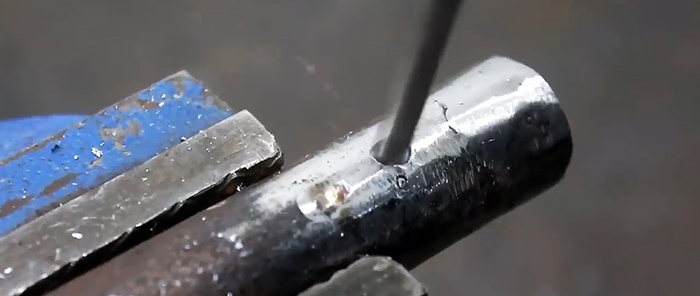
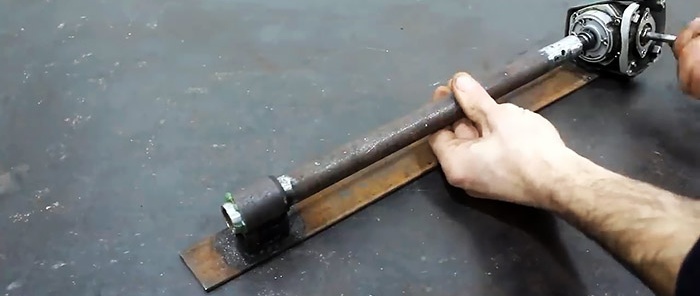
We clamp the drive axis of the gearbox into the drill chuck and, turning on the tool, check the machine at idle speed. At the same time, the pipe on the output shaft of the gearbox also begins to rotate.
Let's check the machine in action. We insert the end of the wire into the hole in the pipe and, slightly pulling it, turn on the drill. The pipe, rotating, begins to wind a spring around itself and the more wire we take, the longer the spring will be.
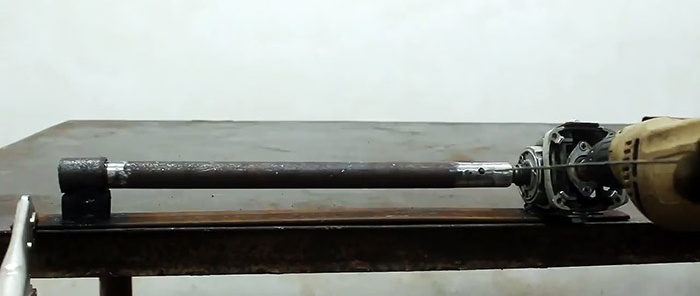

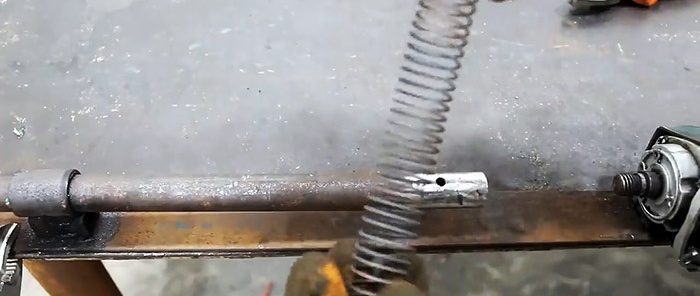
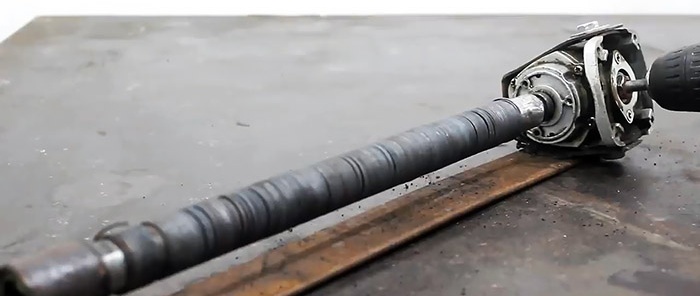
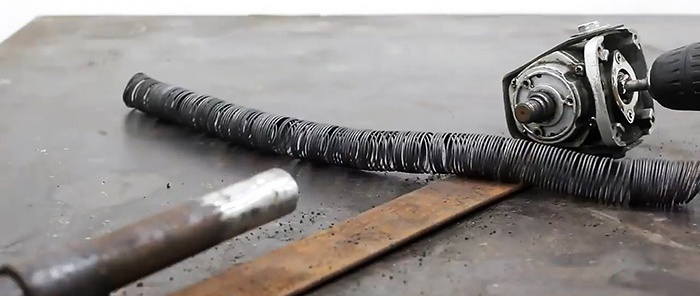
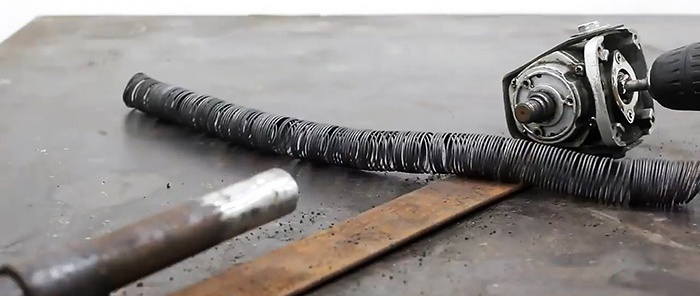
Will need
Most of the materials and equipment that we need for work can be found in a home workshop:
- steel pipe and nut;
- gearbox from a faulty grinder;
- steel strip;
- U-shaped bracket;
- bolts and washers;
- sections of round and square pipes;
- pieces of wire.
We will have to use: welding machine, grinder, wrenches, drill, vice, etc.
Device manufacturing process
We clean the ends of the old round pipe of the required diameter.
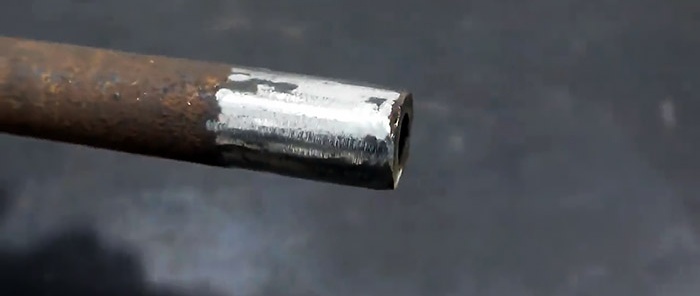
We weld a hex nut of suitable size to one end of it and grind the welding area with a grinder.We screw the nut that we just welded to the pipe onto the output shaft of the gearbox of the faulty angle grinder.
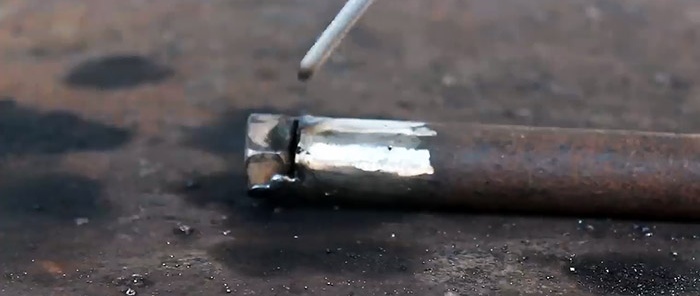
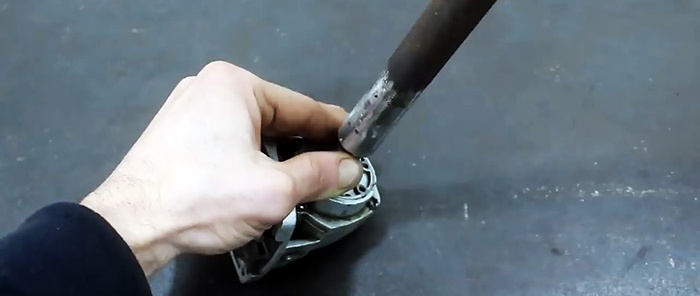
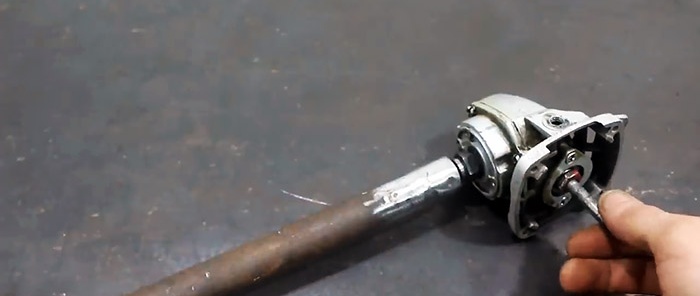
To one edge of a fairly wide and strong steel strip, slightly longer than the pipe with the gearbox, we weld a U-shaped bracket with holes at the ends, one of which is oblong.
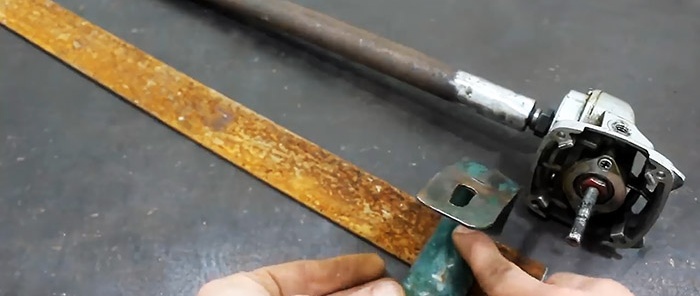
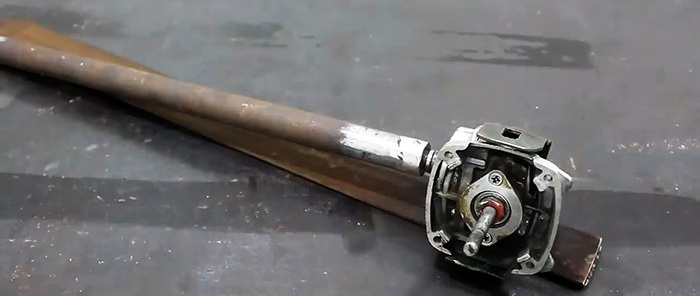
We place the gearbox inside the bracket, orienting the screwed pipe along the steel strip. Using bolts and washers, secure the gearbox to the bracket using the appropriate holes.
On the free end of a long pipe we put a short piece of round pipe of suitable size, under which we install a fragment of a square pipe and sequentially weld all these parts to each other.
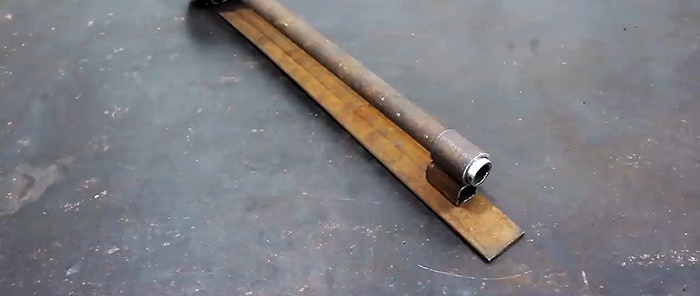
We twist a long pipe with a nut from the output shaft of the gearbox, clamp it in a vice and, stepping back slightly from the nut, drill a transverse hole in its wall with a drill. We insert the pipe with the nut forward into the fixed support from the outside, apply grease to its free end and screw it back onto the output shaft of the gearbox.
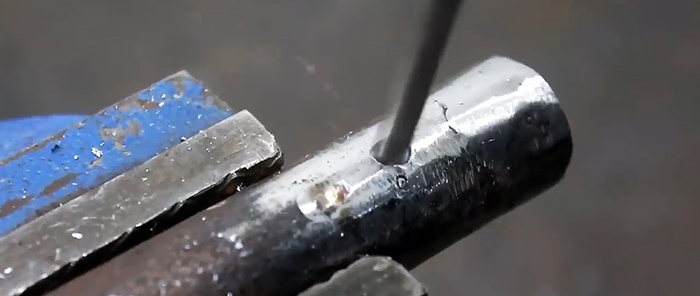
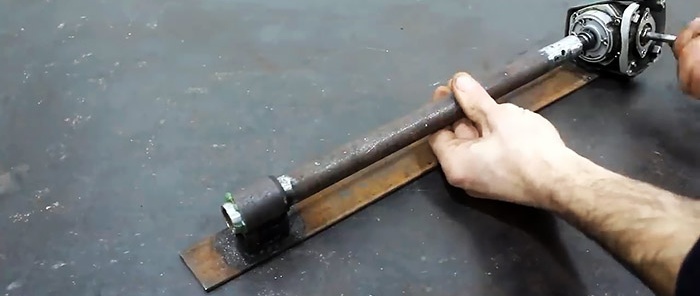
We clamp the drive axis of the gearbox into the drill chuck and, turning on the tool, check the machine at idle speed. At the same time, the pipe on the output shaft of the gearbox also begins to rotate.
Let's check the machine in action. We insert the end of the wire into the hole in the pipe and, slightly pulling it, turn on the drill. The pipe, rotating, begins to wind a spring around itself and the more wire we take, the longer the spring will be.
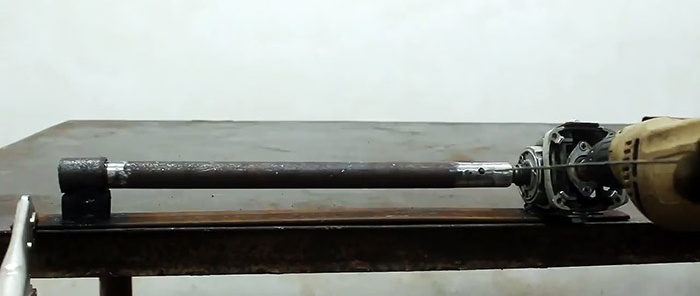

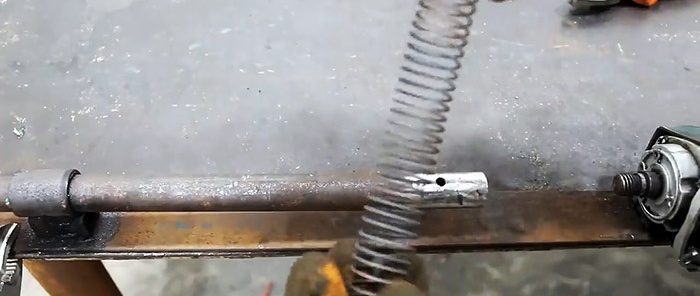
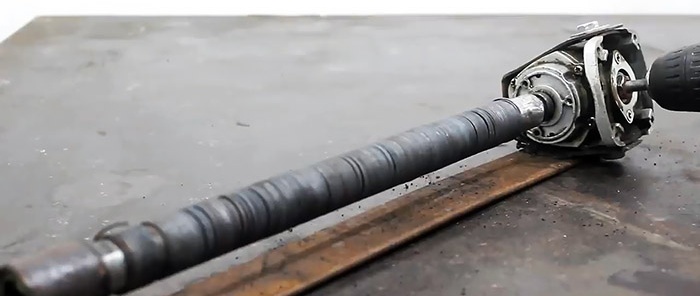
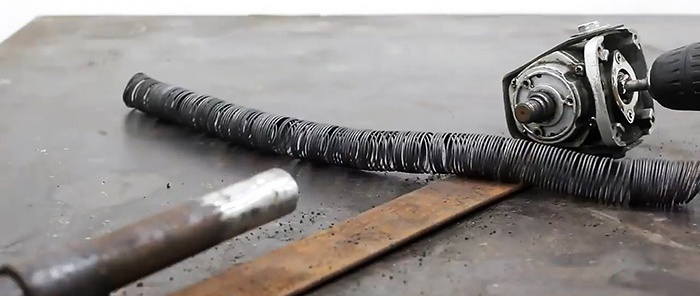
Watch the video
Similar master classes
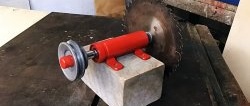
How to make a shaft for a circular saw from scrap materials
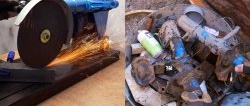
How to make a cutting machine from an angle grinder and old shock absorbers
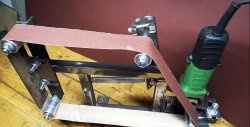
How to make a super grinder yourself from an ordinary grinder
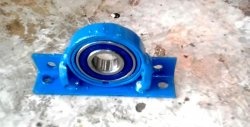
How to quickly make a bearing housing from a pipe
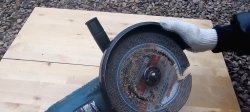
An easy way to unscrew the nut of an angle grinder
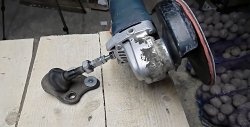
Movable bracket for attaching an angle grinder from a ball joint
Particularly interesting
Comments (0)