How to make a bearing and pulley puller from an old sprocket
In order not to spend money on buying a factory puller in a store, you can make it yourself from waste materials and this does not require any special knowledge or professional experience. It is enough to have basic skills in handling a few simple metal tools.
Will need
Materials:
- old star;
- bolts and nuts;
- thrust bolt with nut;
- metal paint.
Tools: bench vice, wrenches, grinder, welding machine, round file, grinder, clamp, drilling machine, etc.
High-quality and durable drills on AliExpress at a discount - http://alii.pub/5zwmxz
The process of making a two-jaw puller from an old sprocket
We remove the sprocket from the old assembly by unscrewing the nuts from the tightening bolts. We separate the sprocket rim from the hub by cutting the four spokes using a grinder according to the markings.
We mark the rim of the star and cut it into pieces according to the markings.
We put two large fragments of the rim together and weld them in two places for joint processing, successively with a grinder, a round file, and finish with grinding on a grinder.
Long-lasting discs for angle grinders on AliExpress at a discount - http://alii.pub/61bjly
We drill through holes in them from one rounded end, and form protrusions on the other.
We also cut the sprocket hub into four parts and begin processing a pair of fragments with two holes in each. We mainly process them on a grinder, rounding the outer contours.
We insert bolts into the holes of one fragment cut from the hub, then put one fragment on each bolt obtained from the rim, with the teeth facing outward. Place the second fragment cut from the hub on top of the bolts. We tighten the entire resulting assembly with nuts.
Place the thrust bolt nut on the top fragment between the two nuts in the middle and mark the size of the nut in plan on the fragment. We clamp the assembly in a vice and make through cuts according to the marks on both transverse fragments.
We insert the thrust bolt nut into the slot, orienting its rod vertically downwards, and weld the remaining parts of the transverse fragments cut from the hub to the bolt nut.
Welding electrodes for general purposes on AliExpress at a discount - http://alii.pub/606j2h
We unscrew the thrust bolt from the nut and sharpen its end on the grinder, and also make a cylindrical belt by grinding off a couple of adjacent threads.
We paint the resulting structure in two colors, taking into account ergonomics and safety.
Using the resulting two-jaw puller, you can easily press pulleys, bearings and other parts sitting on the shafts or axles with tension from the shafts.
Watch the video
Similar master classes
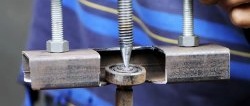
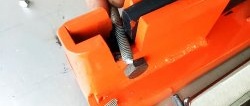
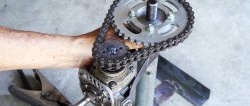
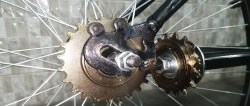
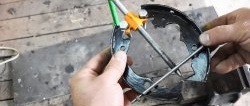
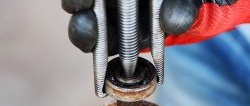