Two in one: how to make a belt grinder and polishing machine from a washing machine motor and an old shock absorber
Purchasing these factory-made machines will be very expensive. Working with hand tools of this type is characterized by low productivity, requires a lot of time and is associated with a large expenditure of physical effort. If you assemble such a combined machine based on a washing machine motor and an old shock absorber, all the mentioned problems will disappear.
Will need
Materials:
- washing machine motor;
- old car shock absorber;
- corners straight and bent along a radius;
- screws, nuts, bolts and washers;
- bearing support on feet;
- multilayer plywood;
- front bicycle wheel hub;
- plates of different shapes and thicknesses;
- brass door awning;
- galvanized sheet;
- sanding belt;
- extension spring, etc.
Tools: measuring and marking tools, grinder, file, welding, wood saw, drill, sandpaper, tap, die, etc.
High-quality and durable drills on AliExpress at a discount - http://alii.pub/5zwmxz
Manufacturing process of combined belt grinding and polishing machine
We disassemble the shock absorber and leave the rod.
We prepare four corners, bent along a radius, and weld a frame from them. We weld the cross member from the corner, taking into account the mounting points for the motor from the washing machine.
We weld the corners vertically to the cross member from the outside and close to the motor mounting points. Taking into account the location of the motor shaft, rod extension and bearing support, we weld a corner transversely to the opposite end of the frame.
We drive wooden blocks planed to size into the holes of the motor legs and saw them off flush with the ends of the holes. We fix the motor to the frame with screws, screwing them into wooden inserts.
We drill 5 disks of the required diameter from multilayer plywood with holes in the center. After sanding the sides, we assemble them together using wood glue. For strength, we compress it with a device consisting of two disks, a bolt and a nut.
We place a cylinder of disks on the end of the rod, which we connect to the motor shaft, and attach the bearing support to the base from an angle. Turn on the motor and sand the surface of the cylinder with sandpaper.
We give the bicycle wheel hub the desired profile.
We fit a plastic pipe onto it with tension and trim the ends. We check the accuracy of fastening the hub with the mounted pipe to the curved plate.
We drill a hole in the corner from the corner of the stand. We weld two nuts transversely to the flat end of the plate at the ends. We adjust part of the loop to the plate nuts and connect them with a bolt to the nut.
We place and secure this unit between the curved plate and the hub with the plastic pipe.Thanks to the adjusting bolt in the plate, the position of the sleeve with the tube can be changed relative to the plate.
We cut it out, cut it where necessary, and bend the galvanized sheet so that we get a casing over the motor with slots for ventilation.
We shorten the rod behind the bearing support. We grind the end to a smaller diameter to the estimated length and cut the thread with a die.
We attach the support table and tape clamp to the frame.
We put a sanding belt on the drive and spring-loaded tension roller. We attach a polishing disc to the end of the rod shaft and our machine is ready for work.
We attach 4 adjustable supports to the frame from below to align the machine in a horizontal position. Now you can successfully grind and polish various parts and workpieces, as well as sharpen knives and other tools.
Long-lasting discs for angle grinders on AliExpress at a discount - http://alii.pub/61bjly
Watch the video
Similar master classes
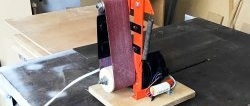
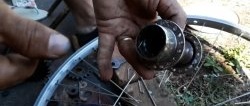
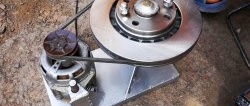
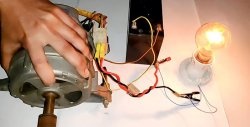
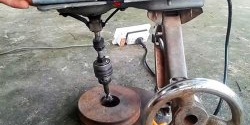
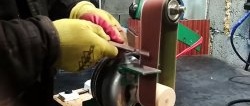