How to make concrete fence posts that are 4 times cheaper than metal ones and more durable
If instead of metal pillars you cast concrete ones, using plastic sewer pipes as formwork, you can save a lot of money, and in terms of durability they will not be inferior to steel ones. Any physically strong adult can cope with such work.
Will need
Materials:
- steel equal angle;
- profile square pipe;
- 2 sewer plastic pipes with a diameter of 110 mm;
- mortgages and fittings;
- cement, sand, gravel and water;
- pigment red and black;
- microfiber;
- remnants of tin;
- soap solution.
Tools: welding machine, container for mixing concrete mortar, trowel and trowel, mechanical stirrer, piece of plastic film.
The process of manufacturing concrete pillars in formwork from plastic sewer pipes
We weld sections of a profile square pipe to the corner transversely at equal distances, which we lay on solid supports, for example, bricks, and achieve a horizontal position of the corner.
In two sewer pipes made of plastic with a diameter of 110 mm, we cut out longitudinal strips and lay them with slits up along the corner on both sides and press them with brackets made of profile square pipes in the shape of the letter P to each other and to the base.
We lubricate the inside of the pipes that serve as formwork with a soap solution so that the hardening concrete does not stick to the plastic. At the ends of the pipes we install plugs cut from tin, as well as mortgages and fittings.
Using a mechanical mixer, mix a solution of cement and sand in a ratio of 1 to 3 with the addition of a small amount of microfiber, 0.15 kg of liquid glass, as well as a tablespoon of red and black pigment.
We pour the solution into the pipes, not forgetting to compact it and smooth the surface. We leave the solution in the formwork for a day, covering it with plastic wrap so that the water from the solution does not evaporate too quickly.
After 24 hours we remove the formwork. We start with the staples, then remove the plugs. We find out that the walls of the pipes easily lag behind the concrete. We lower the pipes with concrete to the ground, turn them over with the cuts down and remove the pipes from the concrete pillar, lifting them by one end.
We keep the pillars for several days so that they gain sufficient strength, after which they can be used for their intended purpose. Although their production takes some time, they cost four times less than metal ones and are much more durable.
Watch the video
Similar master classes
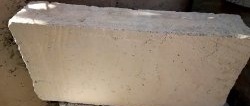
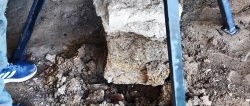
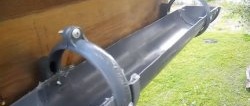
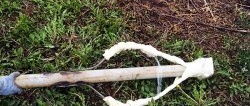

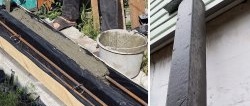