Useful tips for expanding the capabilities of your soldering iron and solder
How to solder a wire efficiently
Soldering a wire to a printed circuit board pin without flux will be unreliable with a pre-tinned wire. The quality of soldering will increase significantly if flux in the form of rosin or acid is present on the soldering iron tip along with the solder.
High-quality soldering of thick wires
To connect multi-core wires made of aluminum and copper, we remove their ends from the sheaths and the cores from the insulation for the length of the twist.
We fluff up the strands, insert them into each other in a counter-parallel motion and twist them using the opposite rotation from the center of the twist. We apply flux to the twist, heat it from below with a soldering iron tip, add solder and evenly cover the entire length of the twist with it.
We put a heat-shrinkable cambric on the twist and heat it with a hairdryer.
Soldering wires without a soldering iron
Flatten the solder with a hammer and cut the required length with side cutters.
We wind a strip of solder onto the wire sheath in the form of a spiral. We twist the ends of the wires, apply flux, slide the spiral over the twist and melt it so that it covers the entire length of the twist.
We put on a thermal cambric and cool it with a hairdryer or the same lighter.
Making a convenient homemade sting
We replace the standard tip in the soldering iron with an element made from a piece of copper wire, bent in the middle until parallel to contact in one plane.
We deflect the end with the loop in the transverse plane by about 30 degrees.
We insert the free ends into the soldering iron and tighten the fixing screws. We get a tool convenient for soldering electronic boards.
Watch the video
Similar master classes
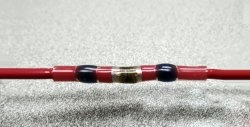
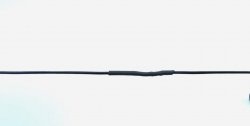
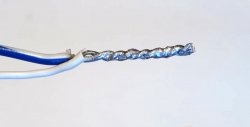
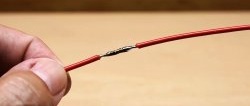
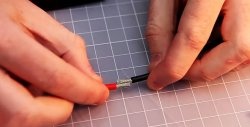
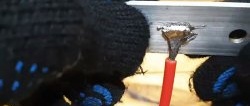