Soft starter for power tools
Many electric tools, especially from previous years, are not equipped with a soft start device. Such tools are launched with a powerful jerk, which results in increased wear on bearings, gears and all other moving parts. Cracks appear in varnish insulating coatings, which are directly related to premature failure of the tool.
To eliminate this negative phenomenon, there is a not very complicated circuit based on an integrated power regulator, which was developed back in the Soviet Union, but it is still not difficult to buy on the Internet. Price from 40 rubles and above. It is called KR1182PM1. Works well in a variety of control devices. But we will assemble a soft start system.
Soft starter circuit diagram
Now let's look at the diagram itself.
As you can see, there are not very many components and they are not expensive.
Will need
- Microcircuit – KR1182PM1.
- R1 – 470 Ohm. R2 – 68 kilo-ohms.
- C1 and C2 – 1 microfarad - 10 volts.
- C3 – 47 microfarads – 10 volts.
A breadboard for mounting circuit components “so as not to bother with making a printed circuit board.”
The power of the device depends on the brand of triac that you install.
For example, the average value of the open state current for different triacs:
- BT139-600 - 16 amperes,
- BT138-800 - 12 amperes,
- BTA41-600 - 41 amperes.
Assembling the device
You can install any others that you have and that suit your power, but you need to take into account that the more powerful the triac, the less it will heat up, which means the longer it will work. Depending on the load, you need to use a cooling radiator for the triac.
I installed the BTA41-600, you don’t have to install a radiator for it at all, it is powerful enough and will not heat up during repeated short-term operation, at a load of up to two kilowatts. I simply don’t have a more powerful tool. If you plan to connect a more powerful load, then think about cooling.
Let's assemble the parts for installing the device.
We also need a “closed” socket and a power cable with a plug.
It is good to adjust the breadboard to size using large scissors. It cuts easily, simply and neatly.
We place the components on the breadboard. It’s better to solder a special socket for the microcircuit; it costs a penny, but makes the work much easier. There is no risk that you will overheat the legs of the microcircuit, you do not need to be afraid of static electricity, and if the microcircuit burns out, it can be replaced in a couple of seconds. It is enough to take out the burnt one and insert the whole one.
We solder the parts immediately.
We place new parts on the board, checking the diagram.
We solder it carefully.
For a triac, the sockets need to be slightly drilled.
And so on in order.
We insert and solder the jumper and other parts.
We solder.
We check compliance with the circuit and insert the microcircuit into the socket, not forgetting the key.
We insert the finished circuit into the socket.
We connect the power to the outlet and circuit.
Checking work
Let's check the device in operation.
Carefully! All elements of the circuit are under direct voltage of 220 volts! Life threatening!We finally assemble the device.
We carry out a final check for functionality.
In order not to confuse this device with a simple extension cord, it must be marked in any way. I did this using a self-adhesive price tag and tape.
Please watch the video testing this device. The change in device behavior upon startup is clearly shown.
Good luck to you in your affairs and concerns.
Watch a video of the device working
Similar master classes
Particularly interesting
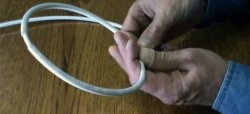
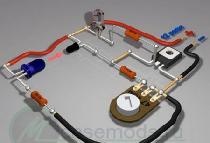
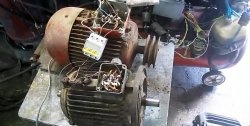
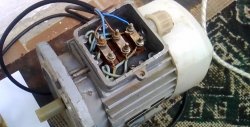
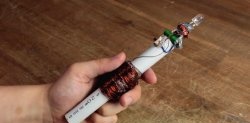
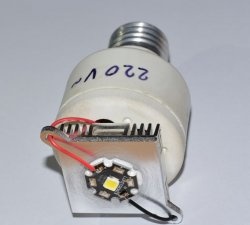