How to make high-quality solder paste with your own hands
When soldering, it is very convenient to use solder paste. You can buy it or make it yourself. When heated, homemade paste flows better than factory paste. When soldering twists, it penetrates deeper, which ensures a reliable connection. Its use prevents overheating of parts, since when melted it changes color from dark to light, allowing you to react in time and remove the burner.
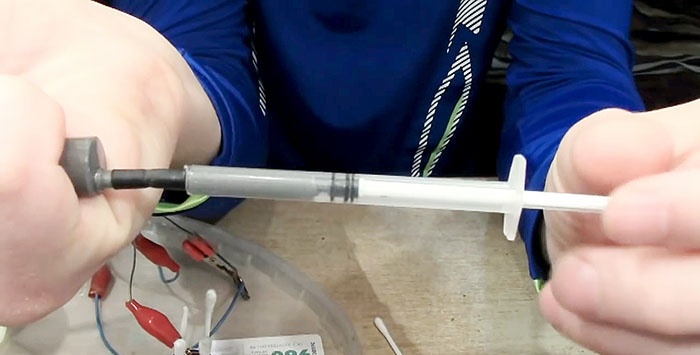
The solder rod needs to be rubbed into a fine powder. To do this, you can use a metal file, which takes a long time, or use a drill with a wood disc.
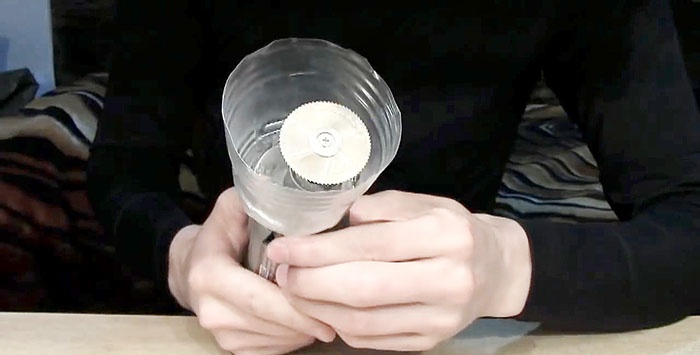
Unlike a file, its teeth do not become clogged with solder. Since sawdust scatters when sawed with a drill, you will need to build a collection for it from a cut-off disposable glass.In this case, the solder itself must be in the bag to preserve all the powder.
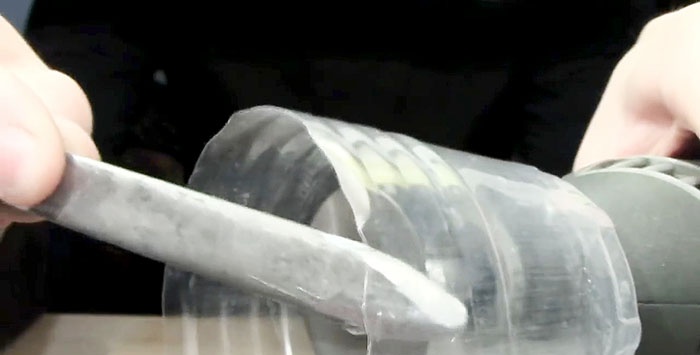
It is important to feed the rod onto the edge of the cutting disc at an acute angle, then it will be rubbed into finer dust. Be sure to keep your hands away from the disc.
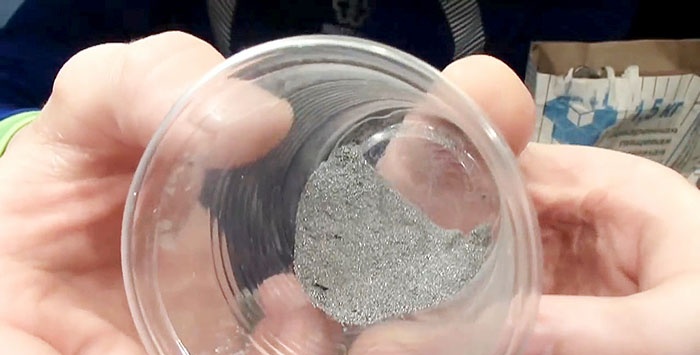
The resulting sawdust is poured into a mortar. Coarse salt is added to them and everything is rubbed with force with a pestle. As you grind, you need to add new salt, since the crystals of the old one are destroyed.
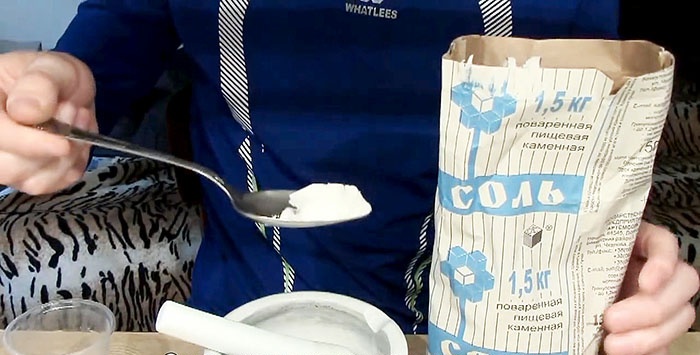
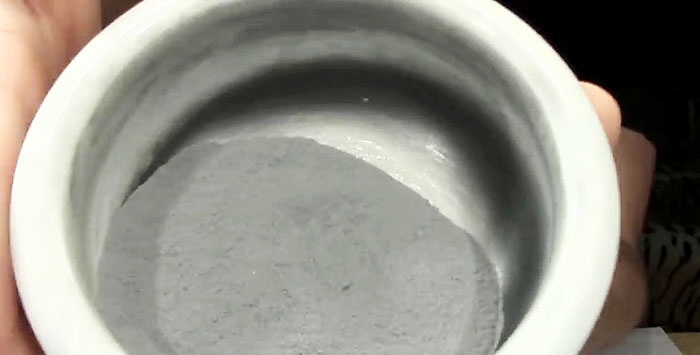
Grinded sawdust is diluted in water. The salt dissolves, resulting in the remaining residue being crushed solder. To completely desalt it, you will need to rinse it a couple of times. After sediment has settled, the water is drained.
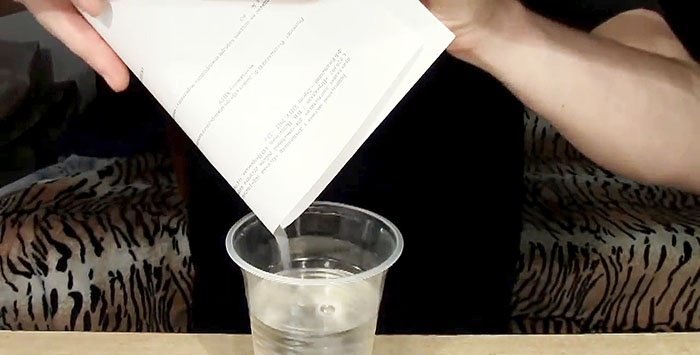
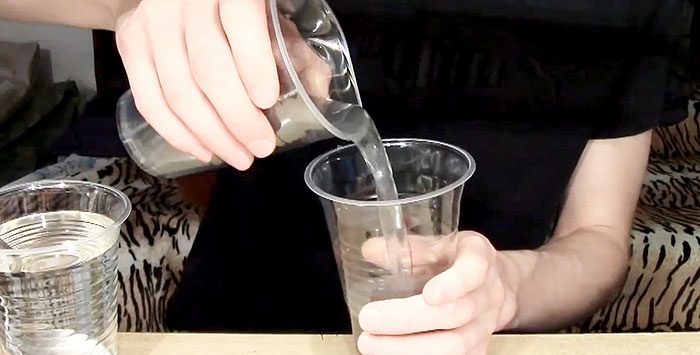
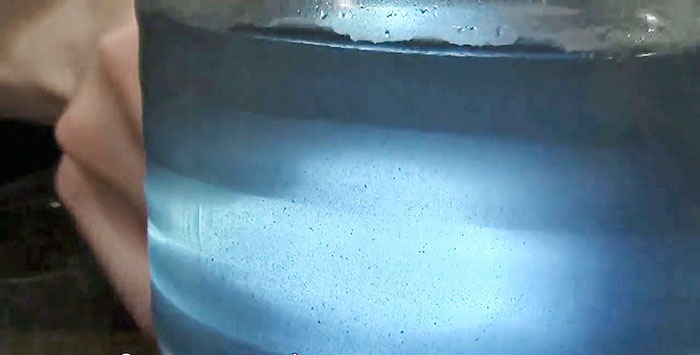
Starch is diluted in a small amount of cold water. After stirring it to weigh all the particles, the solution is poured into boiling water.
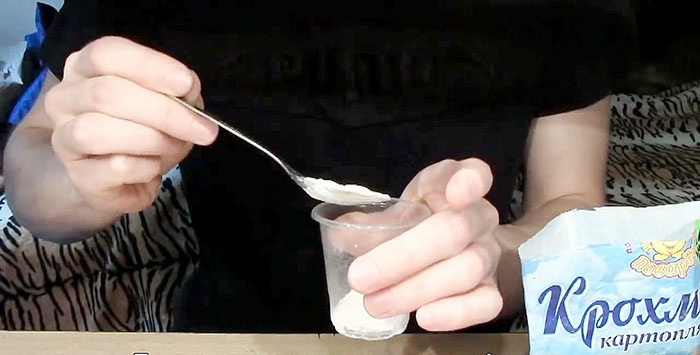
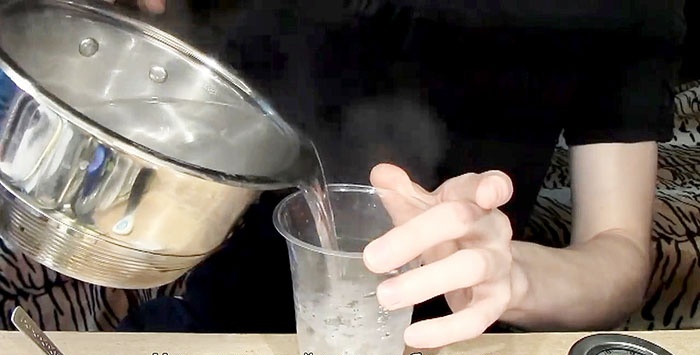
A little water is added to the wet sediment of solder filings. The mixture is stirred until the particles are weighed and poured into hot jelly. After very thorough stirring, the glass with the combined solutions is left alone until a precipitate forms.
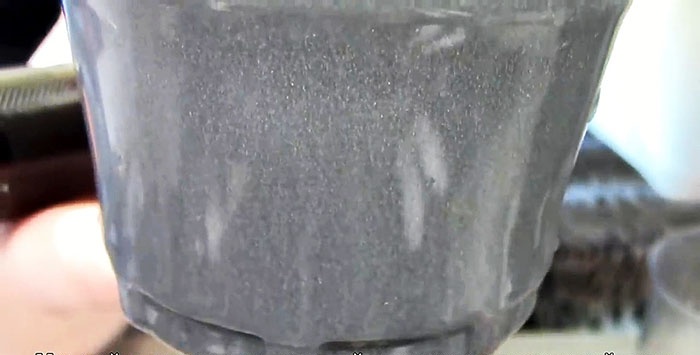
In a thick jelly mass, only heavy solder settles to the bottom. Its lighter small particles float to the top. The jelly is poured into another container so as not to disturb the sediment. The paste is made only from small floating particles. To extract them, you will need to add more water to the jelly to reduce the concentration of starch, thereby reducing the thickness. This will allow the suspension to sink a little. Afterwards, the top layer of the solution without solder powder must be drained. The procedure is repeated until the starch concentration becomes negligible and the precipitate begins to fall out quickly.
After rinsing the starch, the sediment of small particles of solder must be squeezed out by folding it into a napkin.After rough dehydration, the mass is dried in a paper tray. This battery will take 10 minutes. The dried sediment has stuck together lumps. You can rub them with your finger through a napkin.
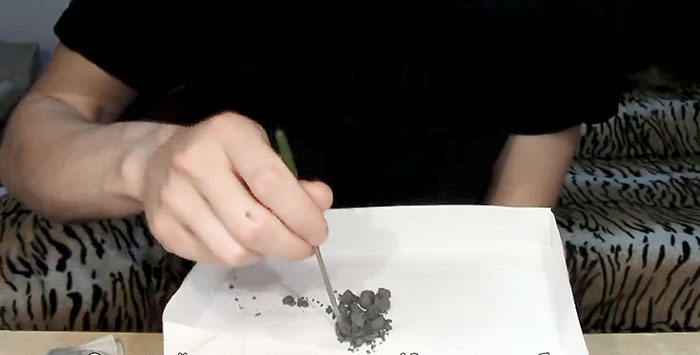
Soldering flux is added to dried fine sawdust. The flux/powder ratio is approximately 40/60 by volume. The ingredients are mixed into a paste.
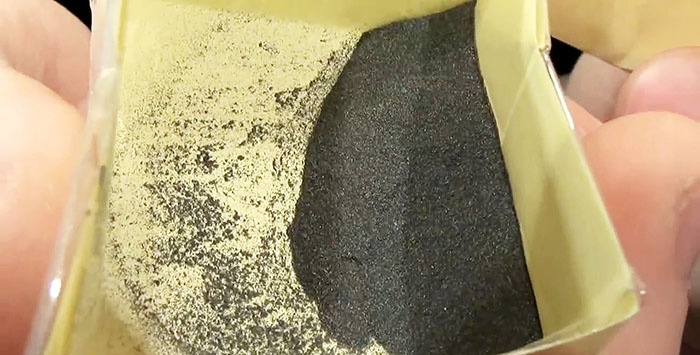
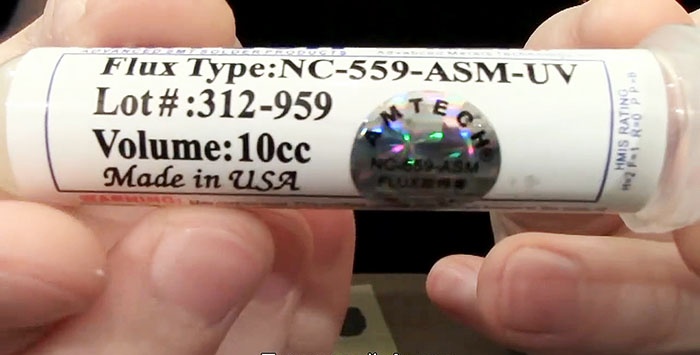

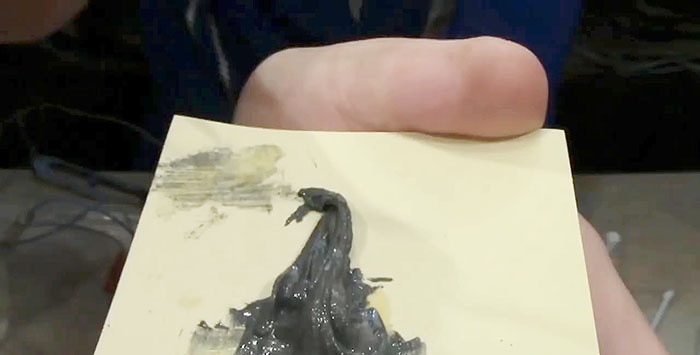
The paste is placed in a 5 mm medical syringe with an elongated piston. Its spout must be connected to the insulin syringe using heat-shrink tubing.
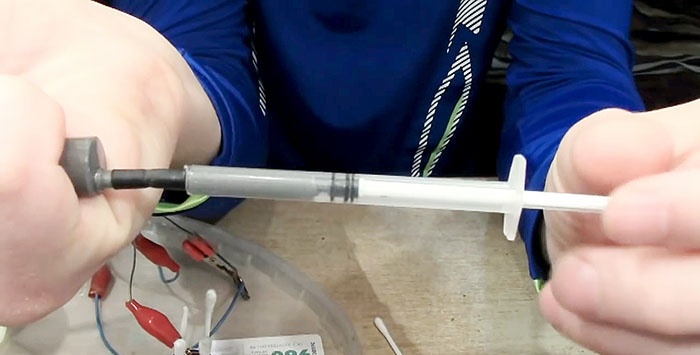
Press the plunger of the large syringe to squeeze the paste into the insulin syringe. With this method, it will flow without forming air pockets.
Subsequently, the resulting paste can be squeezed out through a thin needle of a medical syringe, or a thicker one from flux. This will allow you to adjust the feed depending on the size of the parts being soldered. The advantage of this paste is its ability to penetrate deeply into small capillaries. Of course, it is not so easy to make, but the process is interesting, and soldering with it is a pleasure.
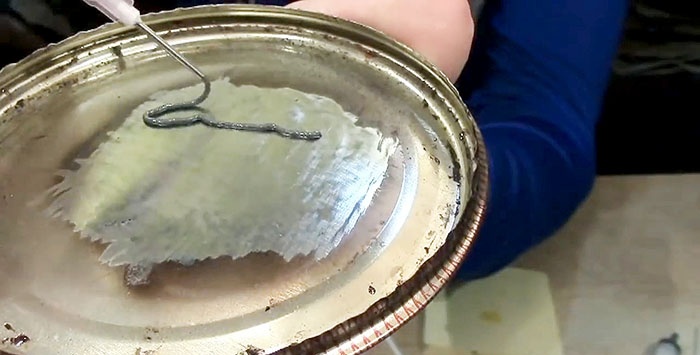
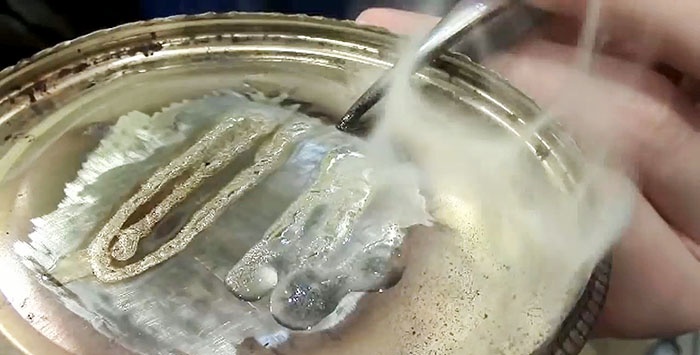
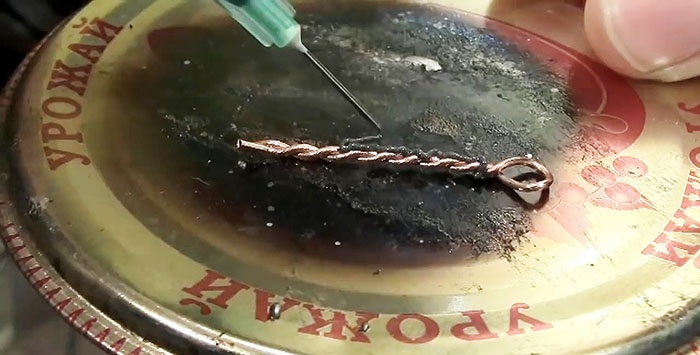
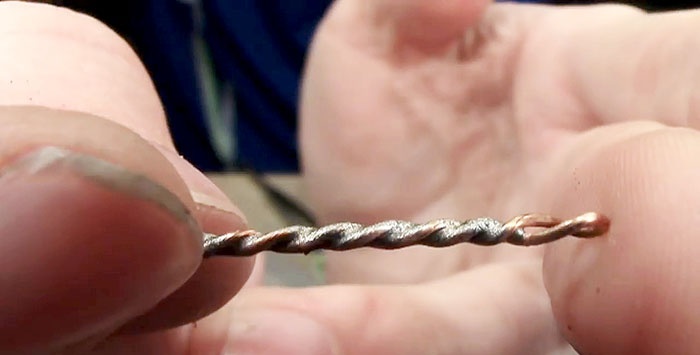
Soldering LED.
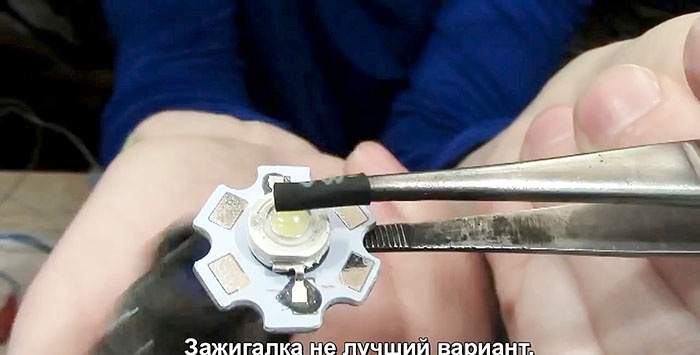
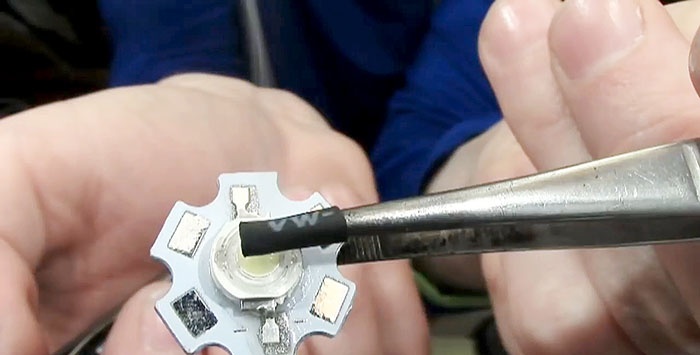
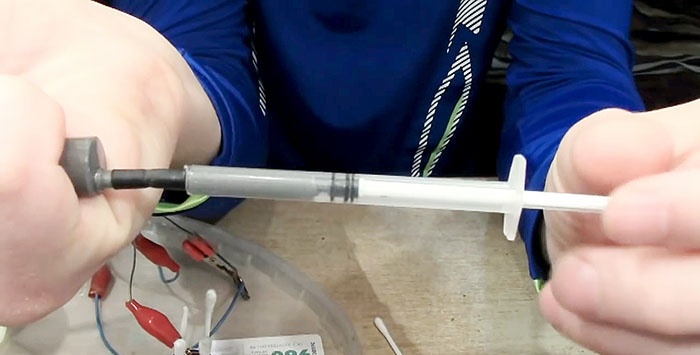
Materials and tools:
- a drill with a 40 mm cutting disc for wood or a file for metal;
- disposable cups 0.5 l;
- pestle and mortar;
- solder;
- soldering flux;
- coarse salt;
- starch;
- 5 cc syringe;
- insulin syringe;
- heat-shrink tubing.
Preparation of solder paste
The solder rod needs to be rubbed into a fine powder. To do this, you can use a metal file, which takes a long time, or use a drill with a wood disc.
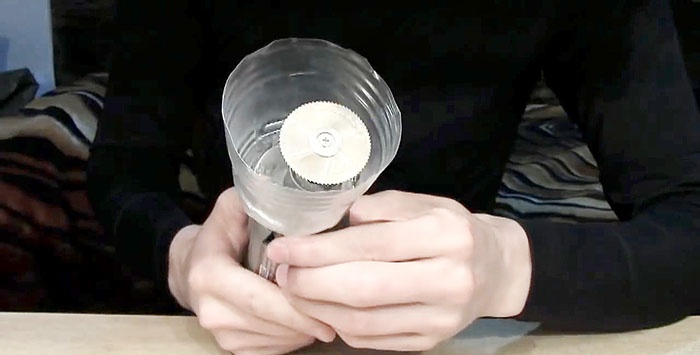
Unlike a file, its teeth do not become clogged with solder. Since sawdust scatters when sawed with a drill, you will need to build a collection for it from a cut-off disposable glass.In this case, the solder itself must be in the bag to preserve all the powder.
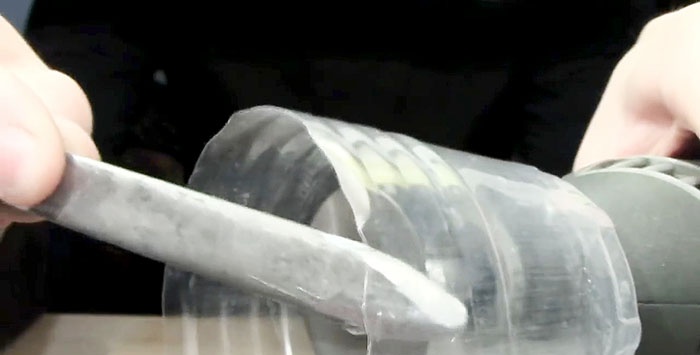
It is important to feed the rod onto the edge of the cutting disc at an acute angle, then it will be rubbed into finer dust. Be sure to keep your hands away from the disc.
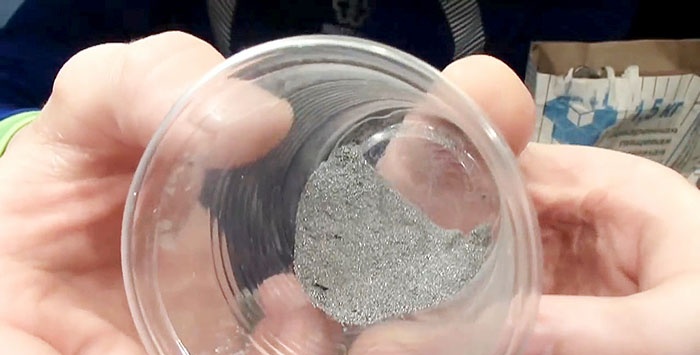
The resulting sawdust is poured into a mortar. Coarse salt is added to them and everything is rubbed with force with a pestle. As you grind, you need to add new salt, since the crystals of the old one are destroyed.
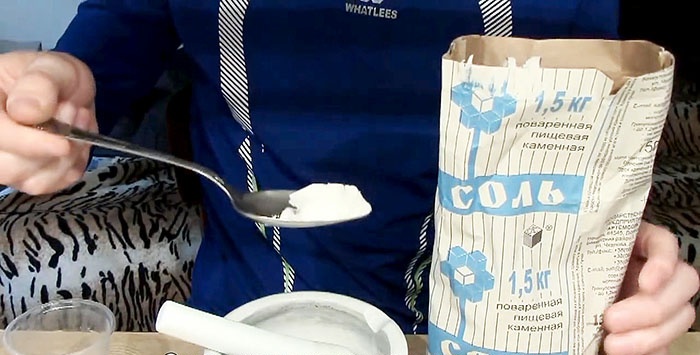
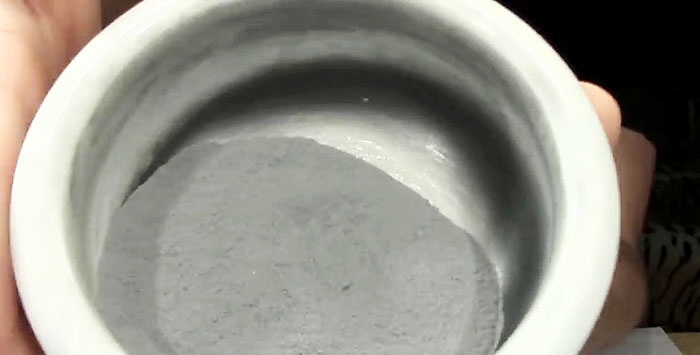
Grinded sawdust is diluted in water. The salt dissolves, resulting in the remaining residue being crushed solder. To completely desalt it, you will need to rinse it a couple of times. After sediment has settled, the water is drained.
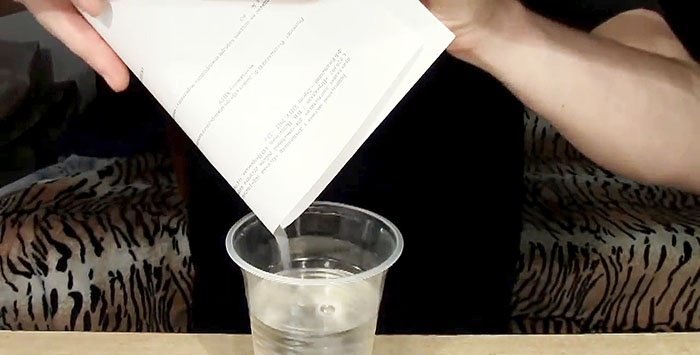
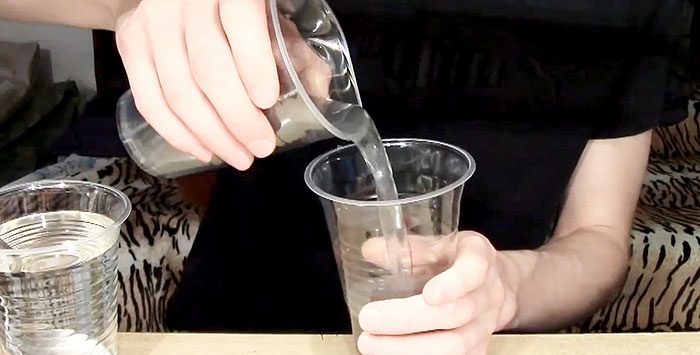
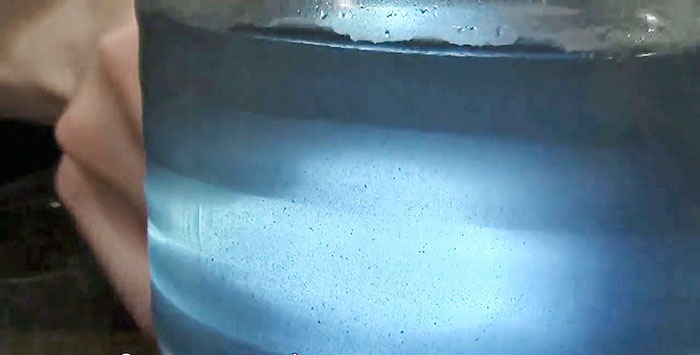
Starch is diluted in a small amount of cold water. After stirring it to weigh all the particles, the solution is poured into boiling water.
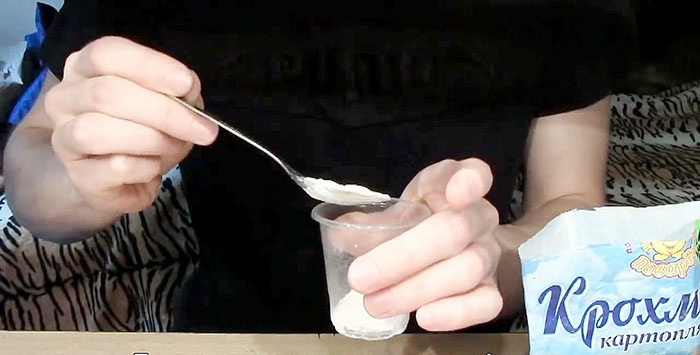
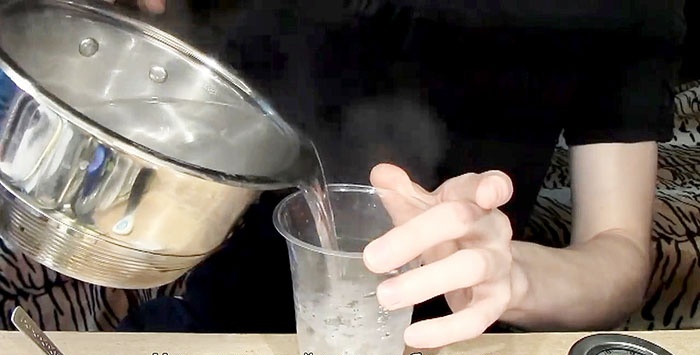
A little water is added to the wet sediment of solder filings. The mixture is stirred until the particles are weighed and poured into hot jelly. After very thorough stirring, the glass with the combined solutions is left alone until a precipitate forms.
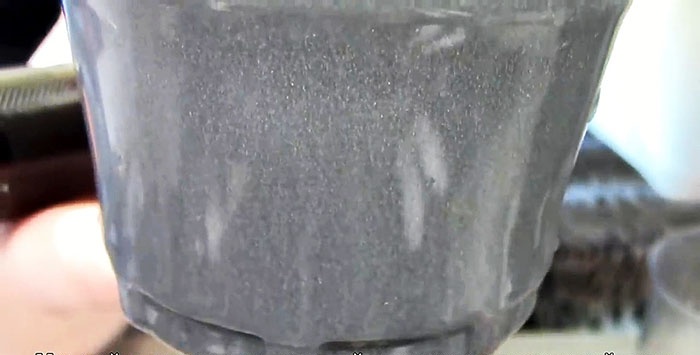
In a thick jelly mass, only heavy solder settles to the bottom. Its lighter small particles float to the top. The jelly is poured into another container so as not to disturb the sediment. The paste is made only from small floating particles. To extract them, you will need to add more water to the jelly to reduce the concentration of starch, thereby reducing the thickness. This will allow the suspension to sink a little. Afterwards, the top layer of the solution without solder powder must be drained. The procedure is repeated until the starch concentration becomes negligible and the precipitate begins to fall out quickly.
After rinsing the starch, the sediment of small particles of solder must be squeezed out by folding it into a napkin.After rough dehydration, the mass is dried in a paper tray. This battery will take 10 minutes. The dried sediment has stuck together lumps. You can rub them with your finger through a napkin.
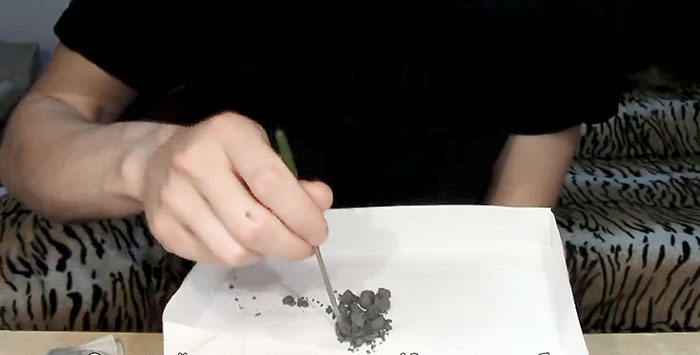
Soldering flux is added to dried fine sawdust. The flux/powder ratio is approximately 40/60 by volume. The ingredients are mixed into a paste.
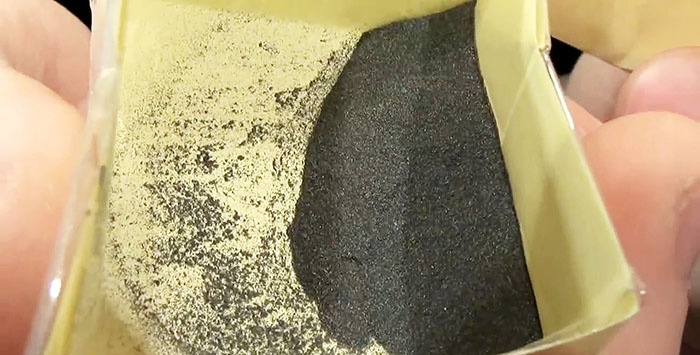
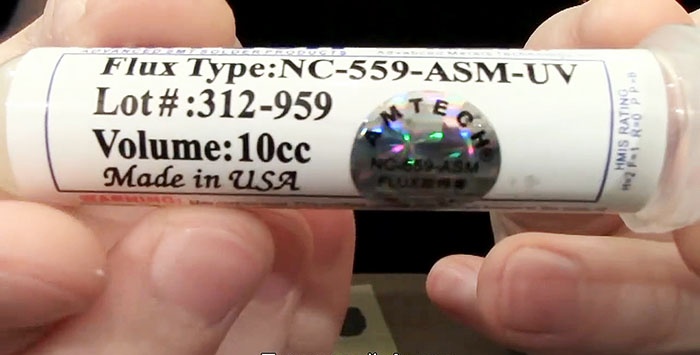

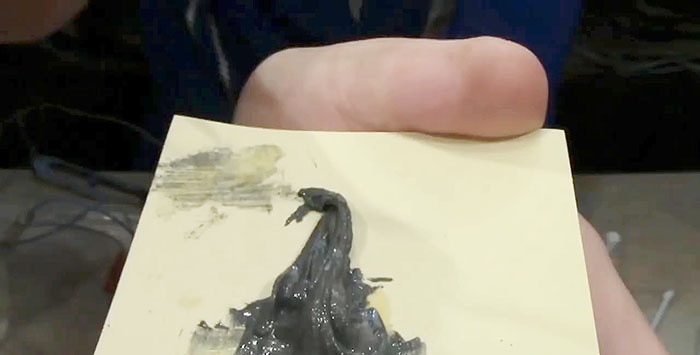
The paste is placed in a 5 mm medical syringe with an elongated piston. Its spout must be connected to the insulin syringe using heat-shrink tubing.
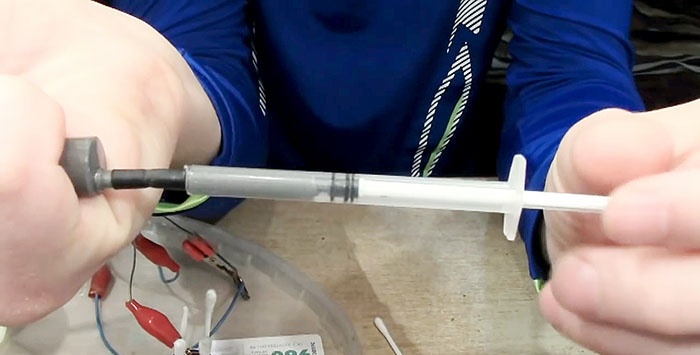
Press the plunger of the large syringe to squeeze the paste into the insulin syringe. With this method, it will flow without forming air pockets.
Subsequently, the resulting paste can be squeezed out through a thin needle of a medical syringe, or a thicker one from flux. This will allow you to adjust the feed depending on the size of the parts being soldered. The advantage of this paste is its ability to penetrate deeply into small capillaries. Of course, it is not so easy to make, but the process is interesting, and soldering with it is a pleasure.
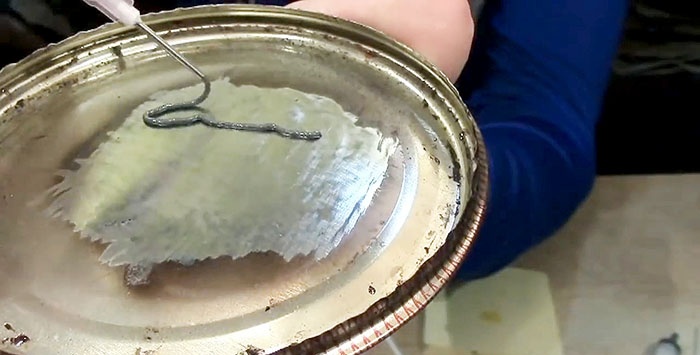
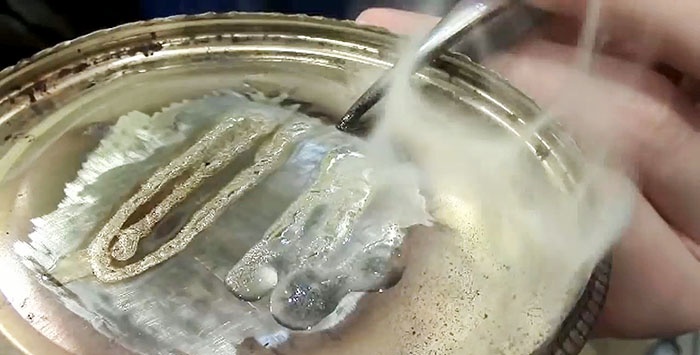
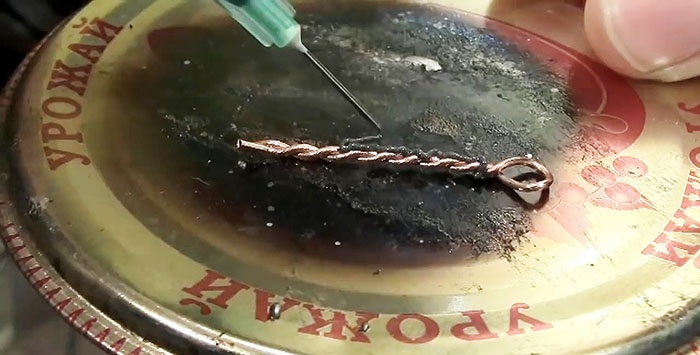
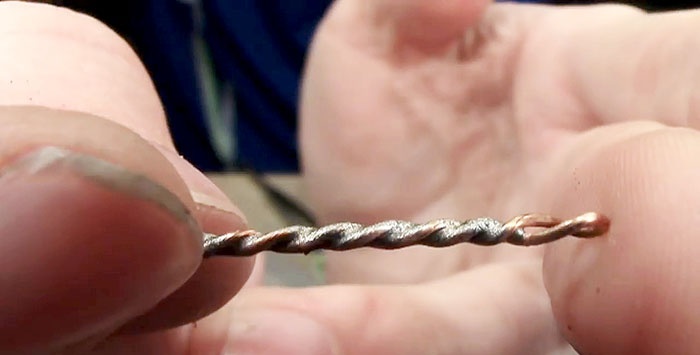
Soldering LED.
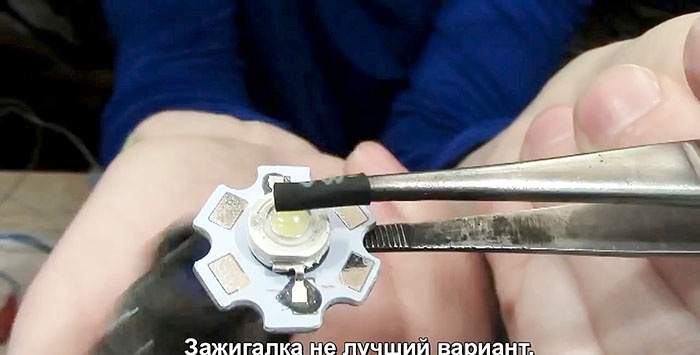
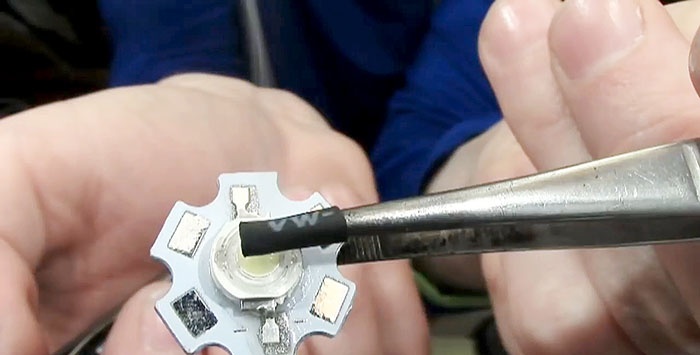
Watch the video
Similar master classes
Particularly interesting
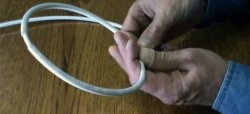
Cable antenna for digital TV in 5 minutes
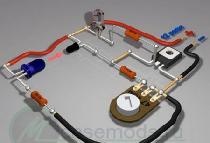
A selection of simple and effective schemes.
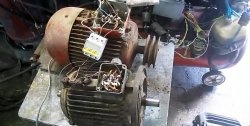
Three-phase voltage from single-phase in 5 minutes
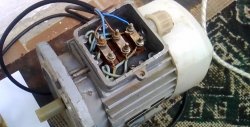
Starting a three-phase motor from a single-phase network without a capacitor
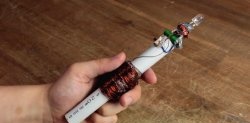
Eternal flashlight without batteries
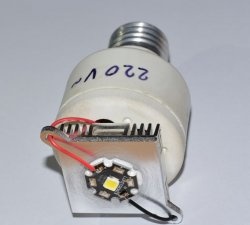
How to make an inexpensive but very powerful LED lamp
Comments (5)