How else can you make a square hole?
Making a square hole in durable metals without special equipment is not easy. However, this can also be done on universal machines. But for this you will have to make the so-called in advance. Watts drill and template for it.
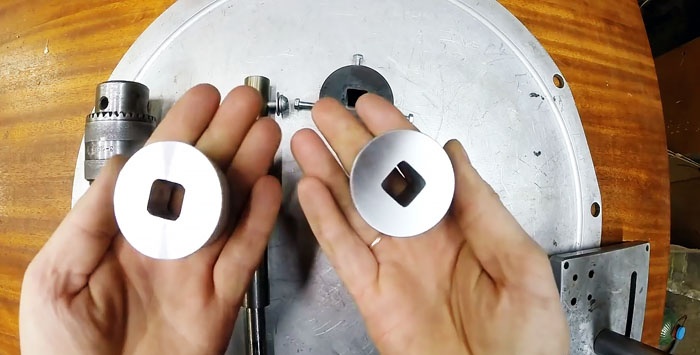
Also, to make a Watts drill, you need a high-speed steel rod, and for a template, a steel circle.
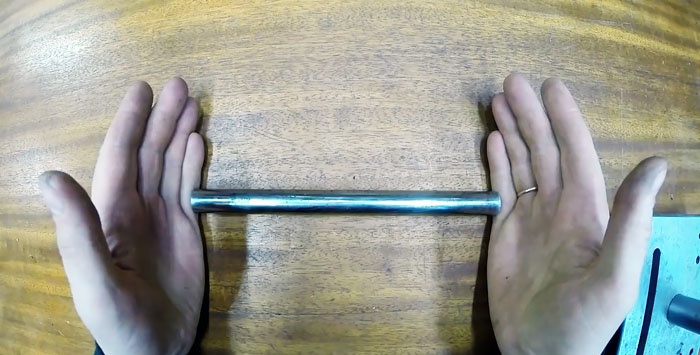
Using an NGF-110 milling machine, we make three longitudinal grooves on the workpiece. The process will proceed with effort, since the material characteristics of a carbide cutter are not much higher than those of a high-speed cutter.
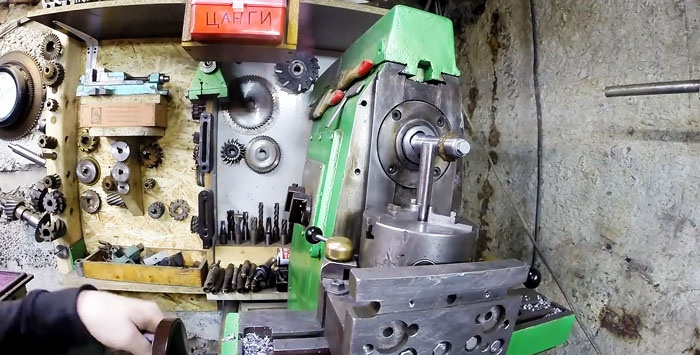
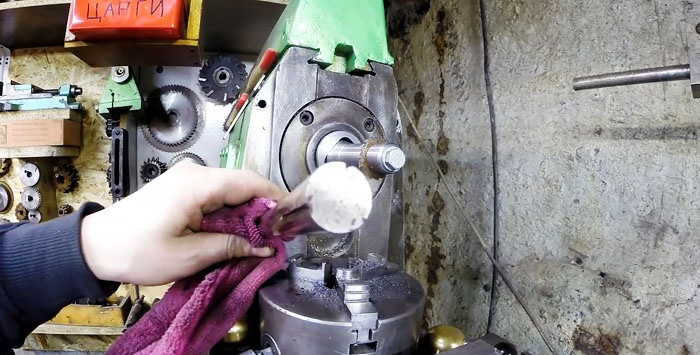
Next, we clamp the workpiece with the grooves in a vice and make the profile of the three cutting teeth using a grinder, starting from the slots. We sharpen the end of the drill, but do not sharpen the side edges.
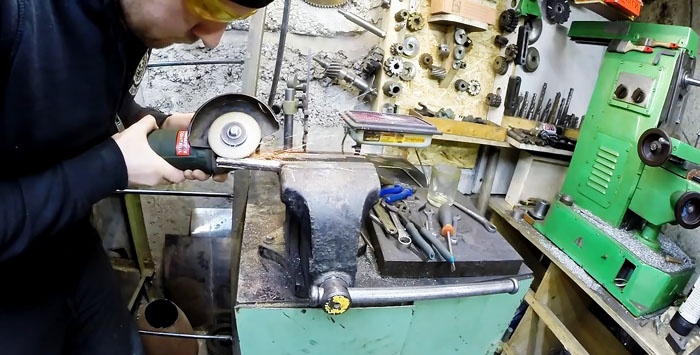
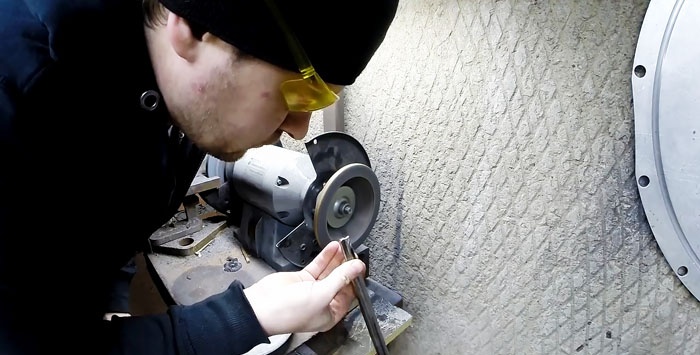
On special equipment for making square holes, the Watts drill not only rotates around its longitudinal axis, but the axis itself makes a trajectory described by four ellipsoidal arcs. But we will choose a different path.
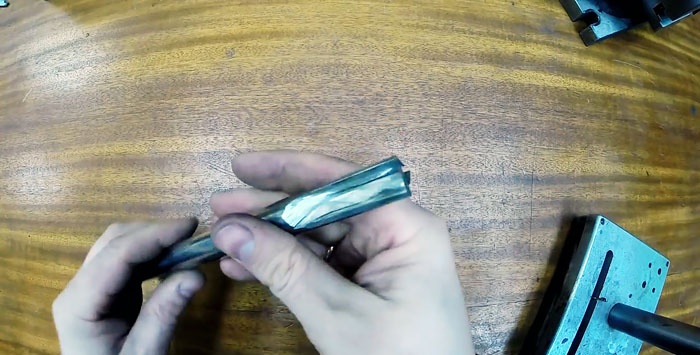
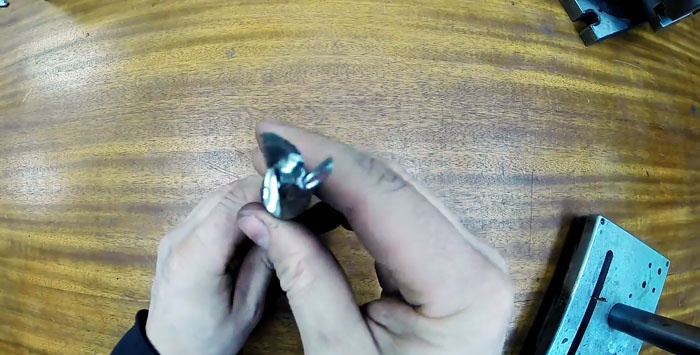
The second part is a template in which the Watts drill will rotate. In our case, the drill diameter is 15 mm. This means that the square made by him will be 15x15 mm.
To make sure that the Watts drill does not jam in the real template, we place it in a strip of plastic with a 15x15 mm square and begin to rotate the drill. It should not bite or cut off shavings from the sides of the square.
We clamp the copier blank into the lathe chuck and grind the end. Then use a 15 mm drill to drill a through hole in the center and drill it out with a large diameter drill to the required depth.
Using a pass-through cutter, we adjust the internal diameter of the large hole and grind the workpiece from the outside. Closer to the front end of the template, drill 4 holes evenly in a circle, cut threads for bolts to secure the copier to the workpiece in which a square hole will be made.
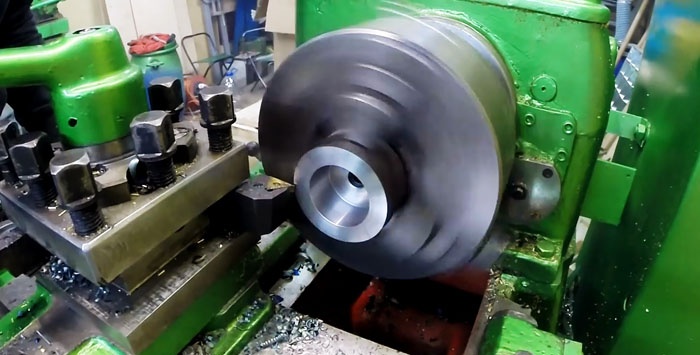
Using a scriber and a dividing head, we draw four lines on the back side of the template blank, which, intersecting, form a described square of 15×15 mm around a hole with a diameter of 15 mm.
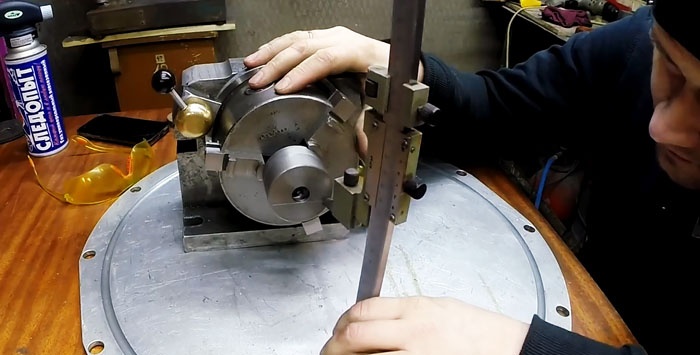
In the inner corners of the marked square, drill 4 holes with a thin drill. We clamp the copier cup in a vice and use a file to form a square hole from a round hole. The template and Watts drill are designed to work together.
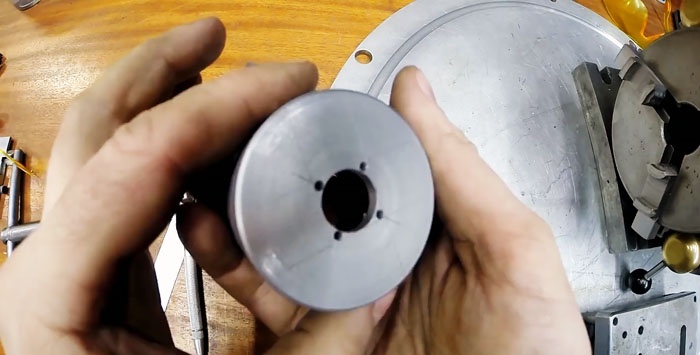
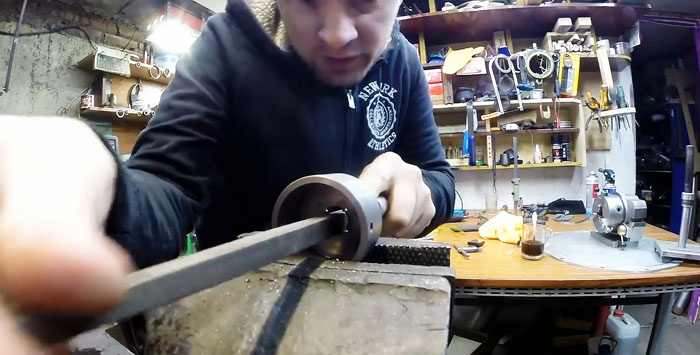

To harden, heat the template in a muffle furnace and lower it into a container with machine oil.

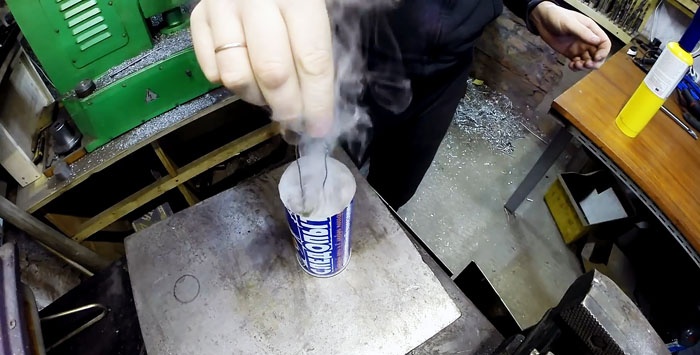
To reduce the distortion of the Watts drill during operation, we make an extension for it.This will allow the square hole to be made coaxial in length. We secure the drill in the extension with two bolts.
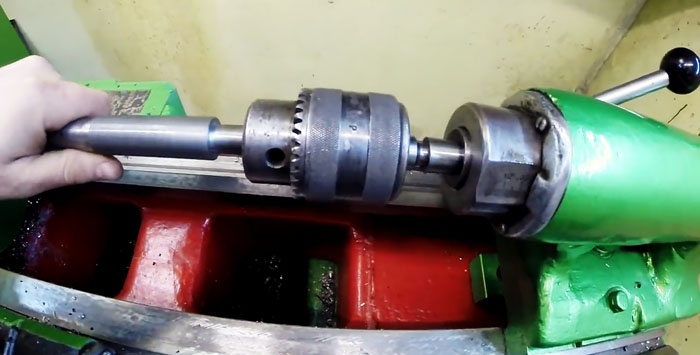
We fix the drill with an extension in the headstock of the lathe. To test the tool, let's make a square hole in the aluminum material.
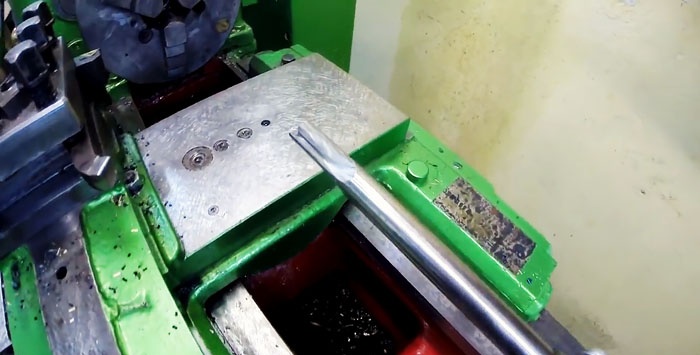
We grind the end and side surface of the workpiece.
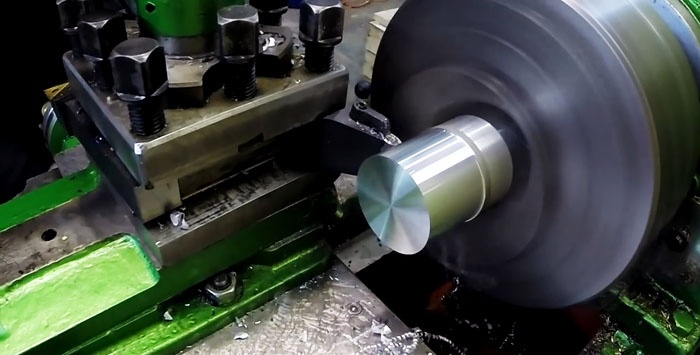
We install the template on the workpiece and use a drill to make a small round hole in the place of the future square.
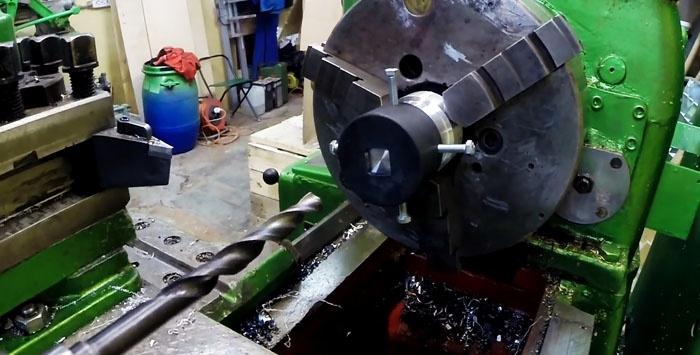
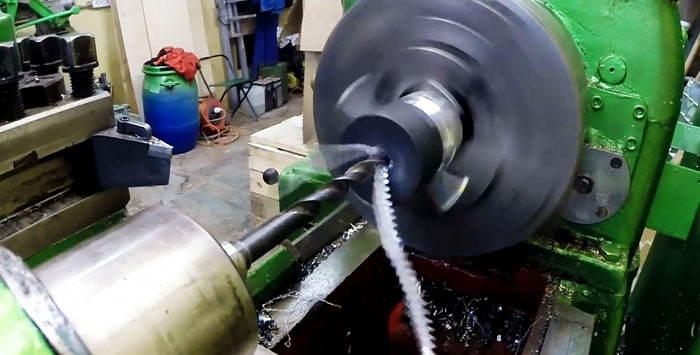
To soften the collision of the Watts drill with the template square, lubricate this place with CV joint grease.
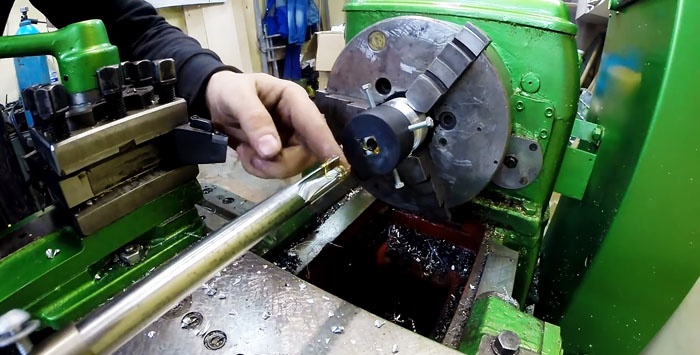
We insert the drill into the square of the copier and rotate the workpiece by the chuck by hand. If you don’t feel any jamming or biting, turn on the machine.
We move the tool forward and see the complex movements made by the drill in the area of the template. After some time, chips begin to emerge, which indicates that the process has begun.
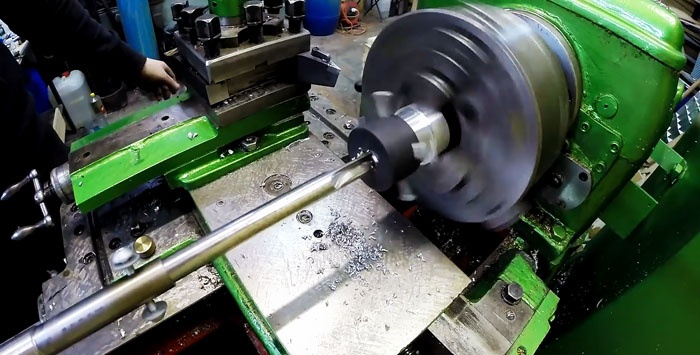
Having reached the desired depth, turn off the machine, remove the headstock with the tool, remove the template and separate a cylinder about 30 mm long from the workpiece with a cutting tool.
We make sure that the square hole is made along the length without disturbing the alignment and transverse size. Our devices passed the first test successfully.
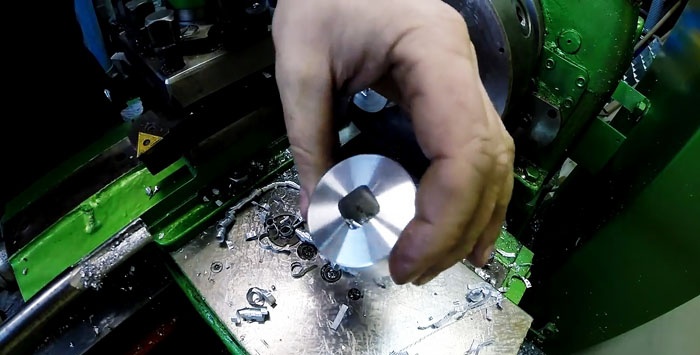
Let's move on to a more complex process - making a square hole in a steel blank. We also grind it along the end and side surface. We wrap and secure the template. We bring the tool and start drilling.
The vibration of the drill and the appearance of chips indicate that the process is in progress. We feed the tool at the same 30 mm. Then remove the template and cut off the blank with the resulting square hole.
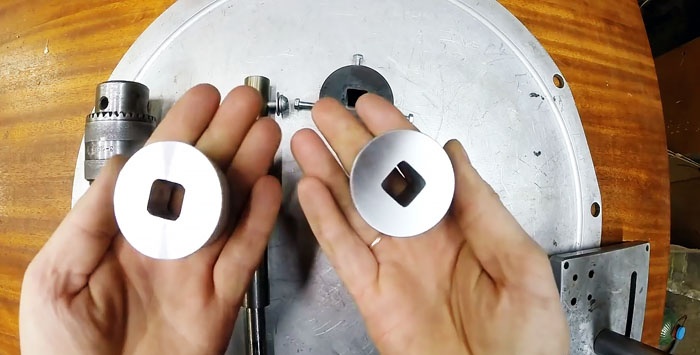
After grinding the ends of the workpieces with square holes, we make sure that they are of high quality in the longitudinal and transverse directions, regardless of the material - aluminum or steel.
The drill and template square also remained intact and did not even become dull, i.e. they are ready for work again.
It is clear that for each size of a square hole you need a separate Watts drill, and the template, if you get creative, can be made universal within certain limits.
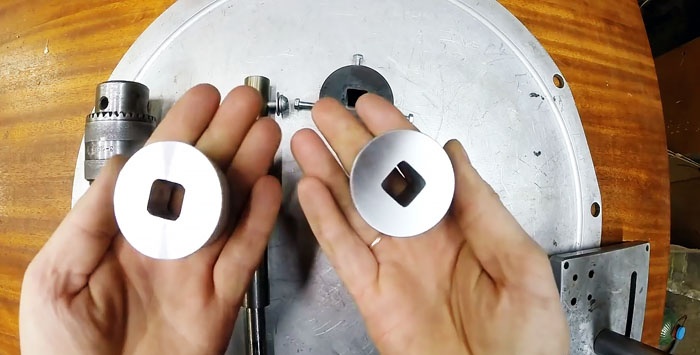
Will need
- lathe and milling machine;
- Bulgarian;
- metal file;
- passing and cutting cutters;
- twist drills;
- disk cutter;
- spanners;
- hardening equipment;
- calipers;
- cutting fluid.
Also, to make a Watts drill, you need a high-speed steel rod, and for a template, a steel circle.
Making a Watts drill
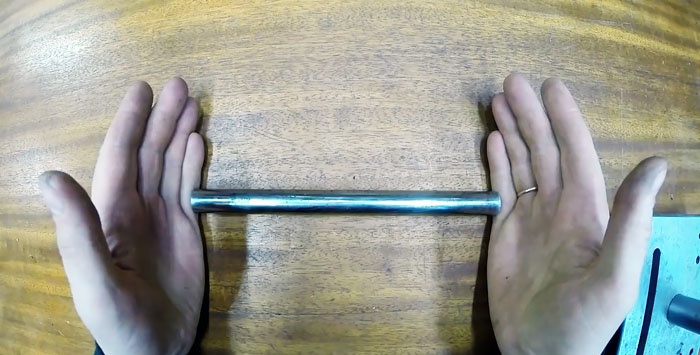
Using an NGF-110 milling machine, we make three longitudinal grooves on the workpiece. The process will proceed with effort, since the material characteristics of a carbide cutter are not much higher than those of a high-speed cutter.
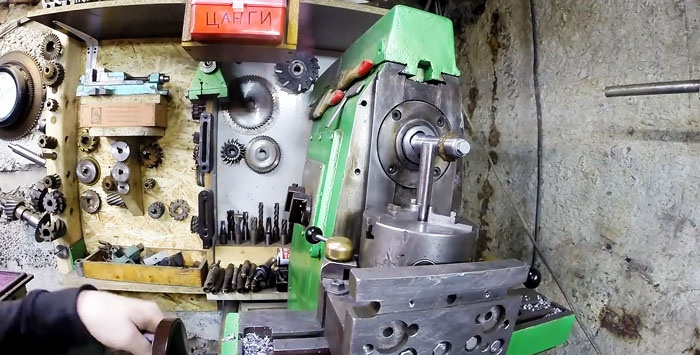
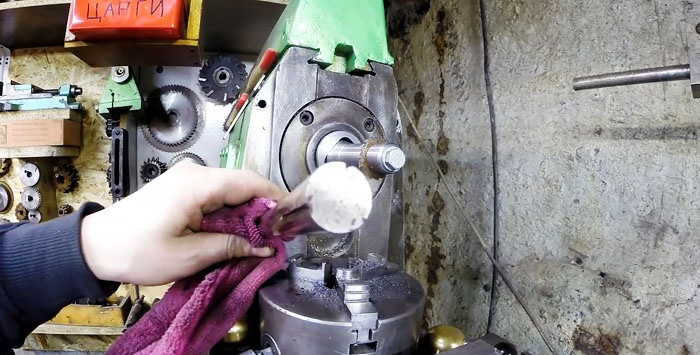
Next, we clamp the workpiece with the grooves in a vice and make the profile of the three cutting teeth using a grinder, starting from the slots. We sharpen the end of the drill, but do not sharpen the side edges.
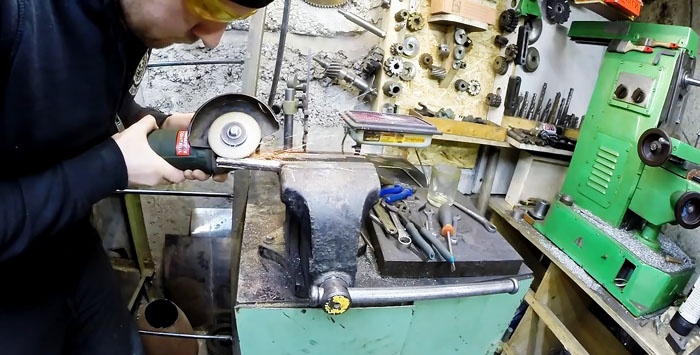
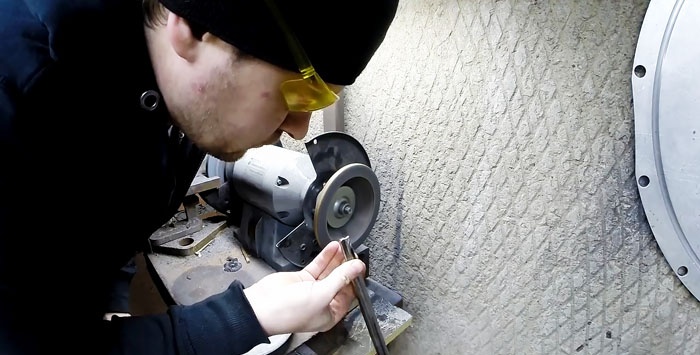
On special equipment for making square holes, the Watts drill not only rotates around its longitudinal axis, but the axis itself makes a trajectory described by four ellipsoidal arcs. But we will choose a different path.
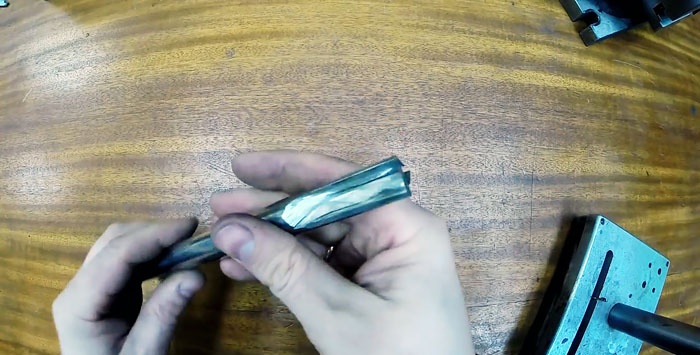
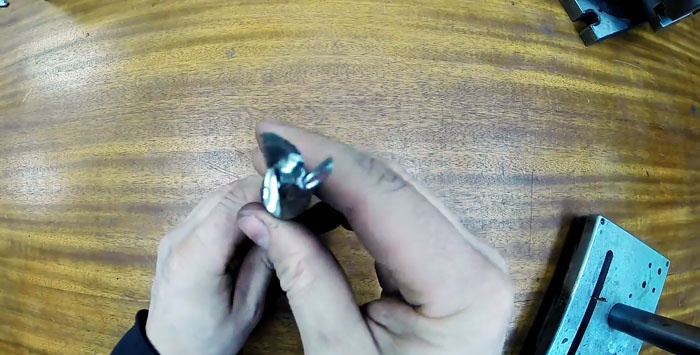
Making a template
The second part is a template in which the Watts drill will rotate. In our case, the drill diameter is 15 mm. This means that the square made by him will be 15x15 mm.
To make sure that the Watts drill does not jam in the real template, we place it in a strip of plastic with a 15x15 mm square and begin to rotate the drill. It should not bite or cut off shavings from the sides of the square.
We clamp the copier blank into the lathe chuck and grind the end. Then use a 15 mm drill to drill a through hole in the center and drill it out with a large diameter drill to the required depth.
Using a pass-through cutter, we adjust the internal diameter of the large hole and grind the workpiece from the outside. Closer to the front end of the template, drill 4 holes evenly in a circle, cut threads for bolts to secure the copier to the workpiece in which a square hole will be made.
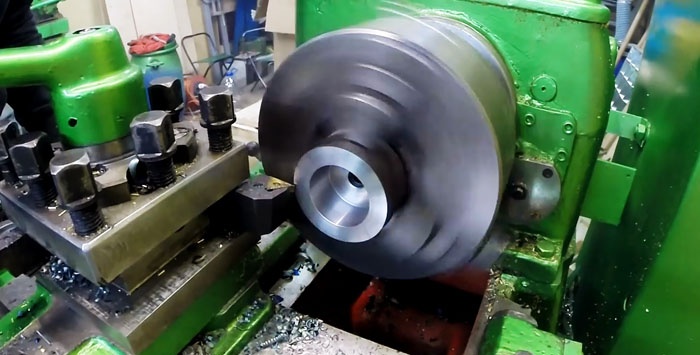
Using a scriber and a dividing head, we draw four lines on the back side of the template blank, which, intersecting, form a described square of 15×15 mm around a hole with a diameter of 15 mm.
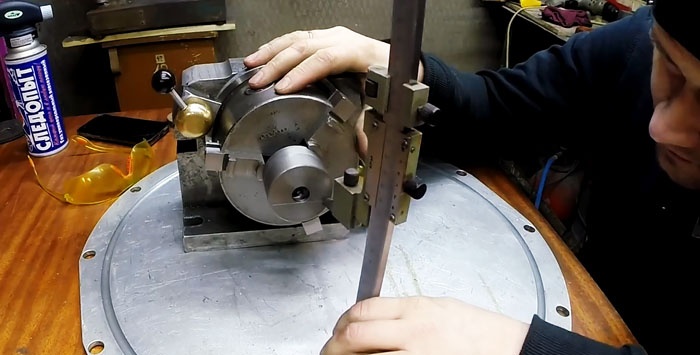
In the inner corners of the marked square, drill 4 holes with a thin drill. We clamp the copier cup in a vice and use a file to form a square hole from a round hole. The template and Watts drill are designed to work together.
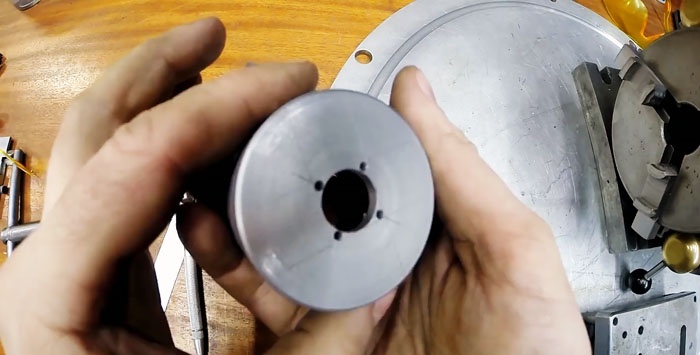
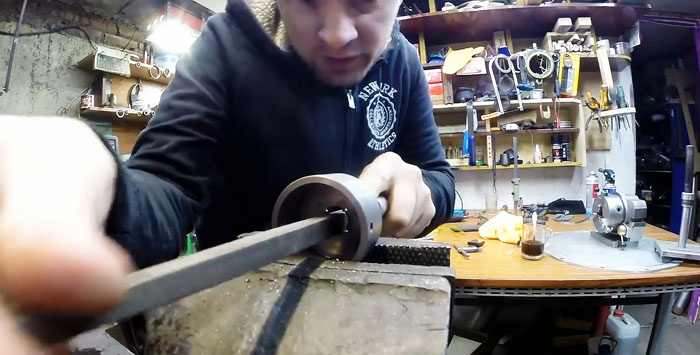

To harden, heat the template in a muffle furnace and lower it into a container with machine oil.

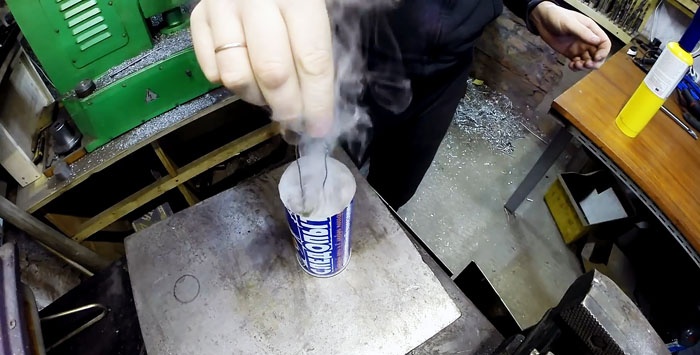
To reduce the distortion of the Watts drill during operation, we make an extension for it.This will allow the square hole to be made coaxial in length. We secure the drill in the extension with two bolts.
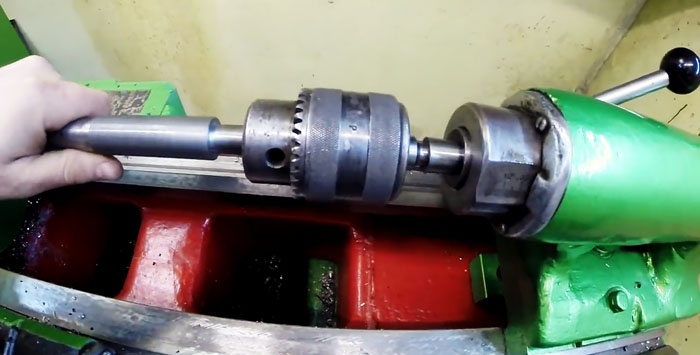
Process of making a square hole
We fix the drill with an extension in the headstock of the lathe. To test the tool, let's make a square hole in the aluminum material.
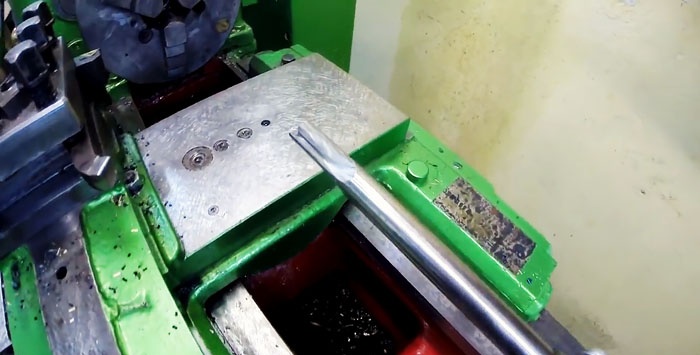
We grind the end and side surface of the workpiece.
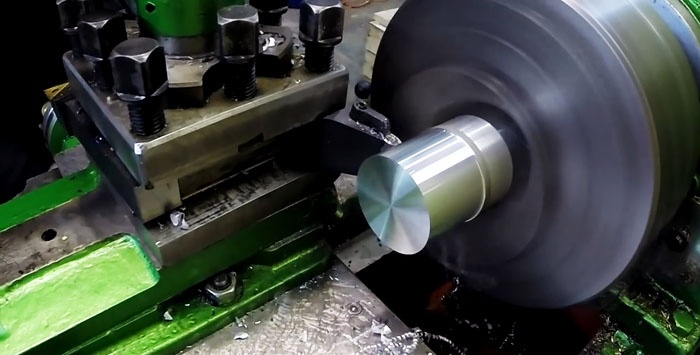
We install the template on the workpiece and use a drill to make a small round hole in the place of the future square.
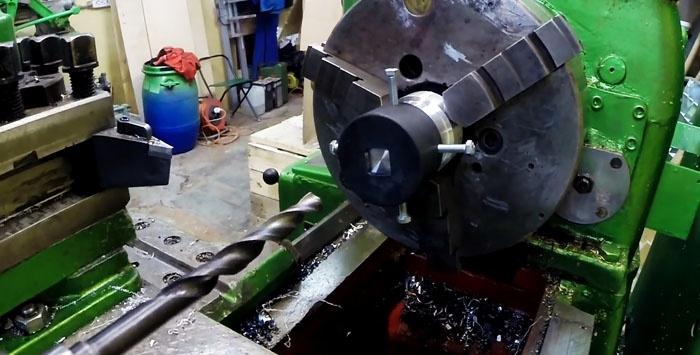
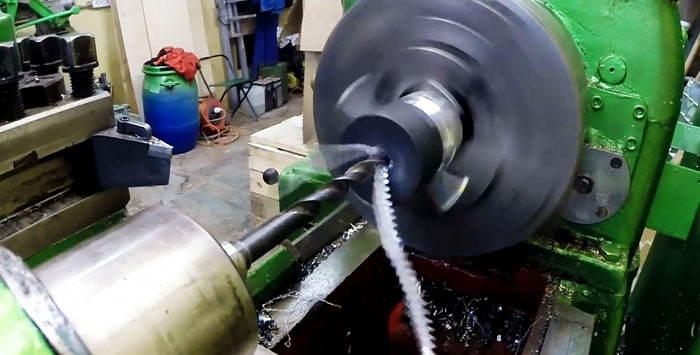
To soften the collision of the Watts drill with the template square, lubricate this place with CV joint grease.
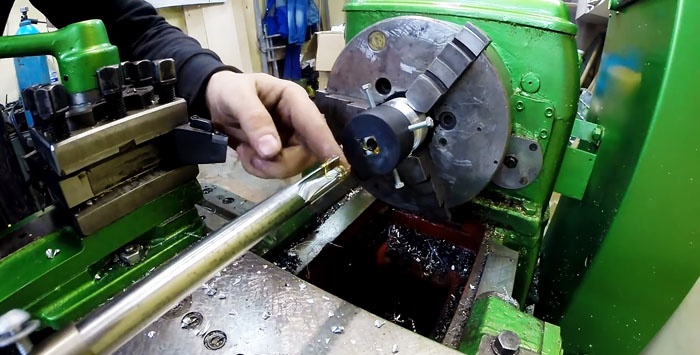
We insert the drill into the square of the copier and rotate the workpiece by the chuck by hand. If you don’t feel any jamming or biting, turn on the machine.
We move the tool forward and see the complex movements made by the drill in the area of the template. After some time, chips begin to emerge, which indicates that the process has begun.
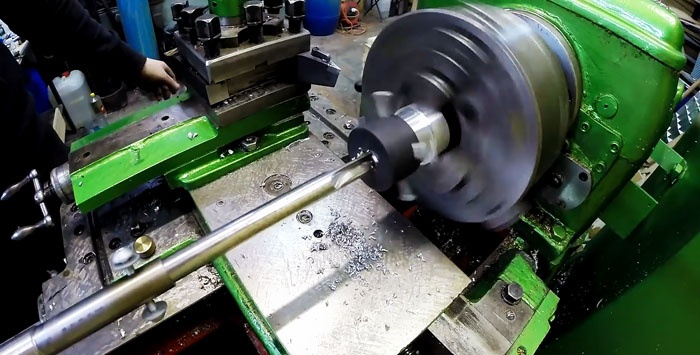
Having reached the desired depth, turn off the machine, remove the headstock with the tool, remove the template and separate a cylinder about 30 mm long from the workpiece with a cutting tool.
We make sure that the square hole is made along the length without disturbing the alignment and transverse size. Our devices passed the first test successfully.
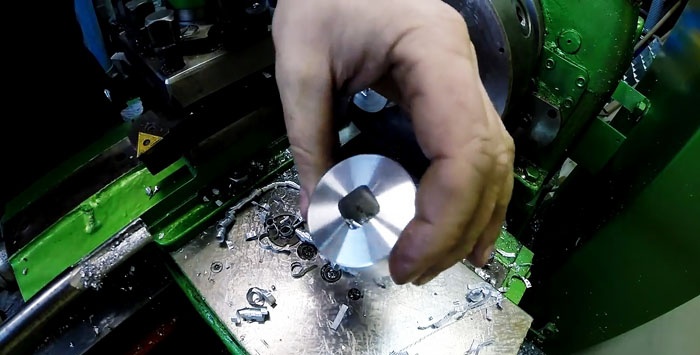
Let's move on to a more complex process - making a square hole in a steel blank. We also grind it along the end and side surface. We wrap and secure the template. We bring the tool and start drilling.
The vibration of the drill and the appearance of chips indicate that the process is in progress. We feed the tool at the same 30 mm. Then remove the template and cut off the blank with the resulting square hole.
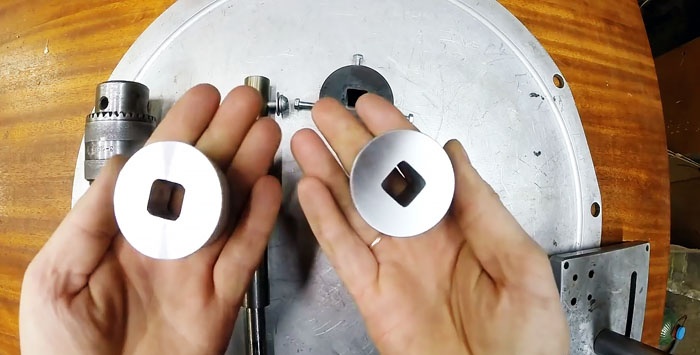
results
After grinding the ends of the workpieces with square holes, we make sure that they are of high quality in the longitudinal and transverse directions, regardless of the material - aluminum or steel.
The drill and template square also remained intact and did not even become dull, i.e. they are ready for work again.
It is clear that for each size of a square hole you need a separate Watts drill, and the template, if you get creative, can be made universal within certain limits.
Watch the video
Similar master classes
Particularly interesting
Comments (1)