A device for quickly applying plaster with your own hands
Hand plastering is a labor-intensive and difficult process. But if you mechanize it, you can do the job even without having any skills in this matter, and with high quality.
You can assemble a plaster sprayer from the following materials and products:
To work you need: hacksaw, grinder, grinder, hammer and mallet, vice, lathe and drilling machine, welding, gun for installing blind rivets, as well as protective gloves.
We cut three pieces of different lengths from the pipe, and one from the metal strip. We process them on a grinder to remove burrs and rust. Moreover, we perform this and other operations with gloves so as not to damage our hands.
We core the wall of a short tube along its diameter in three places - in the center and closer to the ends, symmetrically to the first mark.We drill holes along them: the central one is through, the side ones are one-sided.
We also perform three drillings in the strip workpiece, which should coincide in place with the holes in the short tube.
We bend the ends of the strip at right angles in one direction and get a part in the form of a symmetrical bracket.
On a lathe, we drill central blind holes in three bolts from the head side.
Then we cut the rods with a hacksaw and remove the undrilled parts.
Using magnetic fastening, install the tube with the holes facing up and weld flange nuts to them. We screw the bolts with holes into them and tighten them with a wrench.
Using a magnetic square, we weld the long tube at a right angle to the central through hole on the other side of the short tube.
We weld a coupling with an external thread to the second end of the long pipe.
We weld a bracket to the ends of the short tube of the resulting assembly so that its holes are opposite the drillings in the bolts.
To one side of the bracket we weld a plate cut to size from a thin sheet of metal along its entire contour.
On a lathe, we make a through hole in the center of a round steel rod, grind it to size and form a belt for the fitting.
We weld it to the pipe, placing a steel washer between them.
We screw a long tube into the tap on one side, and a short one with a welded fitting on the other.
In the removed faucet handle, drill a hole for the spring and bend it longitudinally 90 degrees. We put the handle in place, insert one end of the spring into the hole, and weld the other to the tube.
We cut out the elements of a hopper for the solution from a thin sheet of metal.
We bend them according to the markings using a rubber mallet.We drill holes and connect the parts using blind rivets and a gun.
We attach the hopper to the open side of the bracket so that the holes on its strip are aligned with the drillings in the bracket and fit snugly against them. We attach the handle horizontally to the top edge of the hopper using rivets.
After painting, the plaster applicator is ready for use.
We connect the compressor hose to the fitting, put a portion of the solution into the hopper, open the tap, and begin intensively and efficiently plastering the walls.
Will need
You can assemble a plaster sprayer from the following materials and products:
- round pipe;
- strips of thick metal;
- thin sheet metal;
- bolts and flange nuts – 3 pairs;
- round steel bar;
- tap with handle;
- extension springs;
- a can of aerosol paint;
- compressor at a pressure of 6-8 bar.
To work you need: hacksaw, grinder, grinder, hammer and mallet, vice, lathe and drilling machine, welding, gun for installing blind rivets, as well as protective gloves.
The process of making a plastering machine
We cut three pieces of different lengths from the pipe, and one from the metal strip. We process them on a grinder to remove burrs and rust. Moreover, we perform this and other operations with gloves so as not to damage our hands.
We core the wall of a short tube along its diameter in three places - in the center and closer to the ends, symmetrically to the first mark.We drill holes along them: the central one is through, the side ones are one-sided.
We also perform three drillings in the strip workpiece, which should coincide in place with the holes in the short tube.
We bend the ends of the strip at right angles in one direction and get a part in the form of a symmetrical bracket.
On a lathe, we drill central blind holes in three bolts from the head side.
Then we cut the rods with a hacksaw and remove the undrilled parts.
Using magnetic fastening, install the tube with the holes facing up and weld flange nuts to them. We screw the bolts with holes into them and tighten them with a wrench.
Using a magnetic square, we weld the long tube at a right angle to the central through hole on the other side of the short tube.
We weld a coupling with an external thread to the second end of the long pipe.
We weld a bracket to the ends of the short tube of the resulting assembly so that its holes are opposite the drillings in the bolts.
To one side of the bracket we weld a plate cut to size from a thin sheet of metal along its entire contour.
On a lathe, we make a through hole in the center of a round steel rod, grind it to size and form a belt for the fitting.
We weld it to the pipe, placing a steel washer between them.
We screw a long tube into the tap on one side, and a short one with a welded fitting on the other.
In the removed faucet handle, drill a hole for the spring and bend it longitudinally 90 degrees. We put the handle in place, insert one end of the spring into the hole, and weld the other to the tube.
We cut out the elements of a hopper for the solution from a thin sheet of metal.
We bend them according to the markings using a rubber mallet.We drill holes and connect the parts using blind rivets and a gun.
We attach the hopper to the open side of the bracket so that the holes on its strip are aligned with the drillings in the bracket and fit snugly against them. We attach the handle horizontally to the top edge of the hopper using rivets.
After painting, the plaster applicator is ready for use.
We connect the compressor hose to the fitting, put a portion of the solution into the hopper, open the tap, and begin intensively and efficiently plastering the walls.
Watch the video
Similar master classes
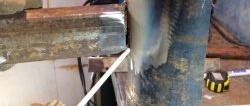
Welding thin metal with your own hands
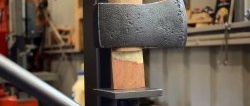
How to make a hydraulic press from a bottle jack
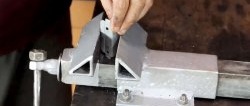
How to make a reliable vice from leftover metal
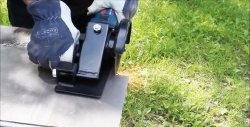
How to increase the functionality of an angle grinder with removable equipment
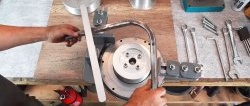
How to make a pipe bender from a car flywheel and a Bendix starter
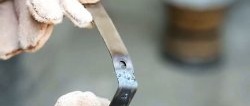
Welding thin metal using a battery
Particularly interesting
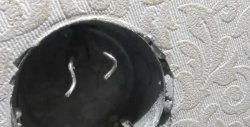
How to install a socket if there are short wires left
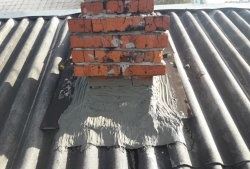
How to eliminate gaps between the chimney and slate
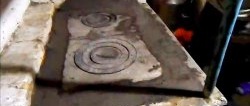
How to mix an ultra-reliable solution for the oven that does not give
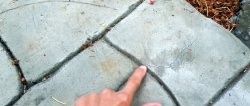
There will be no more cracks: What to add to concrete to make it
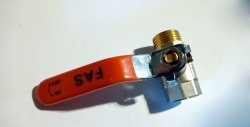
Never buy ball valves without checking with me
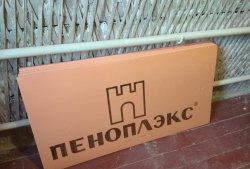
New technology for floor insulation with penoplex
Comments (1)