Built-in mini sauna in a private house
The project to build a bathhouse-sauna was conceived and implemented in 2006. For these purposes, I used a room of approximately 7 square meters. m in a house in which it was originally planned to locate a toilet, washbasin, bathtub or shower. I made an original decision. In this small room I placed a steam room for two people in a sitting position, a shower stall and a toilet. But all other rooms of the house (kitchen-dining room, living room with fireplace, etc.) became the rest room.
The materials and tools used during construction are described in the text for each stage of construction. The amount of materials is calculated by each person according to their volume of work.
To implement my project, I placed the wall between the steam room and the shower stall at an angle of approximately 60 degrees. Thus, both rooms have a trapezoidal plan. In the narrowest part of the shower stall, the floor level is lowered and a drain connected to the sewer is installed.
The stove and the entrance door of the steam room are located in its narrow part, which has a number of advantages:
firstly, the steam from the heater evenly heats the entire top shelf;
secondly, it is very convenient to light the stove, since you don’t need to enter the steam room to do this - you just open the door and add firewood, i.e. there is no need to buy a more expensive stove with the ability to fire from the dressing room.
For the partition, I purchased partition blocks with dimensions 400x400x100 mm. The choice of foam concrete blocks is justified by the fact that it has low thermal conductivity, is easy to saw with a hacksaw, and has precise dimensions, which makes it possible to create a minimum seam width. as well as special glue for laying foam concrete 25 kg.

I started the work with markings, which I made on the floor screed with chalk.The first row of the long part of the partition and the narrow part of the partition, next to the stove, to a height of about 1 meter (foam concrete next to the stove can be destroyed by temperature changes while using the sauna) was made of red brick with cement mortar. To prevent moisture from the floor from penetrating into the foam concrete, a water repellent can be added to the solution. Also, in order to bring the standard width of the brick into line with the width of the blocks, I cut 20 mm from the bricks along the long side with a “grinder” with a diamond blade.
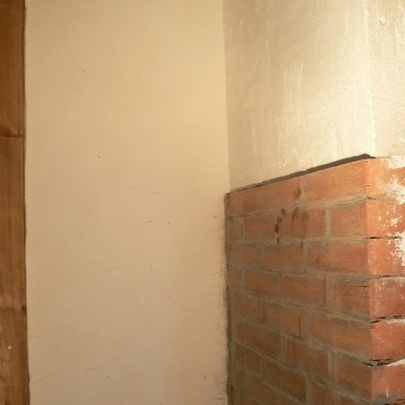
For the internal water supply I chose metal-plastic pipes.
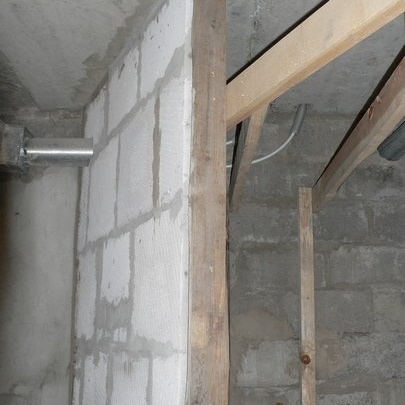
Considering the properties of metal-plastic (installation does not require welding, pipes are easily cut with a hacksaw or a special pipe cutter, they bend easily and take any shape, they are easily connected to fittings using a wrench, they can withstand light defrosting, which is quite possible in a country house, if you forgot drain the water before frost, can be easily repaired in case of damage) made a wiring diagram, calculated the length of the pipe, the number and type of fittings. I marked the installation locations of plumbing equipment and pipe laying routes on the walls and made grooves 20-30 mm deep. Pipes are buried in the wall only in those places where tiles will subsequently be laid.
When laying pipes, a slight slope of the pipes should be maintained to the lowest point of the system, at which a drain valve is installed to empty the system before freezing. Pipes that do not pass through the wall are passed into tubular thermal insulation made of foamed polyethylene. Pipes laid in grooves are fixed in the wall with cement-sand mortar.
Further work on arranging the steam room. Let's start with the markings. First of all, you need to decide on the height of the ceiling.And the recommendations here are as follows: the top shelf should be 10 - 15 cm above the heater, and the distance from the top shelf to the ceiling should be 110 cm. Having measured the heater, I calculated that the ceiling in the steam room should be 220 cm, while the height is only the room is 273 cm. I do not recommend increasing the height of the steam room ceiling - there will be no steam and you will have to heat it for hours.
I decided to nail the lining horizontally, so I placed the bars on the walls vertically. The bars on the outer wall have a cross section of 50x50 mm, on the wall adjacent to the garage 50x80 mm, on the partition 20x80 mm with a length of all bars 230 cm.
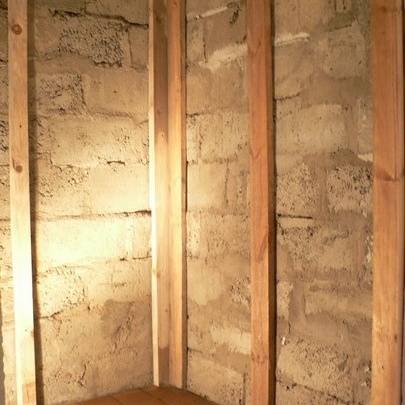
We install the bars using dowel-nails 100 mm long in the main walls and 70 mm long in the partition. The sequence of actions for fastening the bar is as follows: drill four holes in each bar for a dowel-nail, install the bars in increments of approximately 50 cm at a distance of 1 cm from the floor (so as not to rot), and first drive the topmost dowel-nail into each block and a lath to check the flatness of the bars along the walls in the upper part.
I installed bars with a thickness of only 20 mm on the partition because the foam concrete from which it is made has good thermal insulation properties, which means there is no need to additionally insulate this wall. Before attaching the bars to the partition, it is necessary to glue aluminum foil.
We make the ceiling frame from 40x100 mm boards. First, a horizontal strapping is attached to the vertical bars along the perimeter of the steam room, and intermediate bars are attached to it in increments of 50 cm using steel corners and screws.
The place where the chimney will pass through the ceiling must be made of metal. I used available galvanized steel for this.
Now you need to mark the hole for the passage of the chimney. The easiest way to do this is using a real stove, temporarily placing it in the steam room and using a plumb line to mark the contours of the hole. Then the sheet is removed and a hole with a diameter of 130 mm is made according to the markings using a grinder and pliers, which is 10 mm larger than the diameter of the chimney. The wooden frame elements in the chimney area must be protected from the infrared radiation that comes from it. To do this, asbestos fabric is attached to the frame using a stapler, which should then be covered with foil. And only after this the sheet can be finally secured using all the fasteners. When the frame is ready, we check its strength by pulling ourselves up several times on the ceiling bars, and proceed to insulation.
I lined the walls of the steam room that need insulation with 50 mm thick bars. This is in order to lay insulation of the same thickness between them. I used ROCKWOOL basalt wool. We sew the insulation with aluminum foil, securing it to the bars with staples. At the joints, the foil is overlapped and taped with metallized tape. You need to do the same with the ceiling, only the insulation is laid after the clapboard has been hemmed.
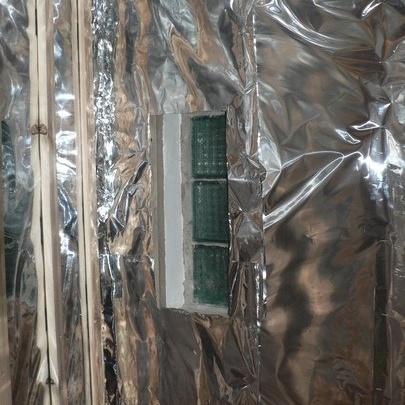
First, wooden antiseptic blocks with a cross-section of 50x50 mm are mounted on the ceiling of the washing room, and then foam plastic is inserted into the spaces between the bars. Then the ceiling was lined with PVC siding. The choice of siding in those days was scarce. I had to take a white one 100mm wide.
Alder lining was used to cover the steam room. Alder has dense matte wood with a pleasant aroma.Before covering, boards must be sorted by color, which for alder can vary from soft pink to copper brown, and these two colors can be present on the same board.
I ended up with three piles of boards matched by color. On the ceiling, which is where you need to start working, I used light and plain boards.
To fasten the lining I used finishing galvanized nails with a conical head, which almost blend in color with the wood.
The lining was sawed with an electric miter saw Makita LS1040. He put boards from two other piles on the walls and began nailing them from the stove from top to bottom. This work does not tolerate haste and fuss; I recommend choosing each board according to color, accuracy of shape, measuring the length and only then sawing it off. Low-quality boards can be used on the back wall under the shelves, and jointed boards can also be used there. I covered the walls, shelves and door with Supi Saunavaha (Tikkurila Finland) - a colorless protective composition containing natural wax, which has proven itself in long-term use.
According to my design project, the floor in the steam room is covered with unglazed terracotta tiles measuring 15x15 cm. This material harmonizes well with the brick wall next to the stove, and the color matches well with the alder lining with which I lined the inside of the steam room. I made the seams 5 mm wide and rubbed them with a dark gray fugue; I used the same fugue to decorate the seams in the brickwork.
I made the floor in the washing room with electric heating. This will allow you to quickly and effectively warm up one small room, creating comfortable conditions in it, without turning on the heating of the entire house.
A reinforcing mesh was laid on the foam insulation; a heating cable was attached to it, and then a screed 5 cm thick was made.
In the part of the floor where there will be a shower stall, you should make a smooth lowering of approximately 50 mm, having previously installed a shower drain. The ladder mesh should be 15-20 mm higher than the concrete screed, since the floor tiles still need to be laid, but its level should coincide with the level of the ladder mesh. Let the concrete set for 3-4 days.
The floor was tiled with green porcelain tiles, and the walls were covered with glazed ceramic tiles, also in two shades of green.
A built-in sauna appeared in a country house located on a small plot of land.
Construction It took four months, of which only one month was a full-fledged vacation.
In the video you can see all the details of my project, and on my channel you will also find the continuation of construction and the condition of the sauna after 14 years of operation.
Materials:
- - partition blocks with dimensions 400x400x100 mm;
- - glue for foam concrete masonry;
- - Red brick;
- - metal-plastic pipes;
- - tubular thermal insulation made of foamed polyethylene;
- - wooden blocks 50x50 mm, 50x20 mm;
- - dowel-nails;
- - board 40x100 mm;
- - steel corners;
- - screws;
- - aluminium foil;
- - asbestos fabric;
- - Cink Steel;
- - alder paneling;
- - insulation (ROCKWOOL basalt wool, polystyrene foam),
- - metallized tape;
- - PVC siding;
- - finishing galvanized nails with a conical head;
- - colorless protective composition Supi Saunavaha (Tikkurila Finland);
- - lamps;
- - RCD;
- - unglazed terracotta tiles measuring 15x15 cm;
- - fugue;
- - shower drain;
- - ceramic tiles on the floor and walls.
Tools:
- - “grinder” with a diamond disc;
- - hacksaw for metal;
- - hammer drill;
- - pliers;
- - stapler;
- - electric miter saw Makita LS1040.
The materials and tools used during construction are described in the text for each stage of construction. The amount of materials is calculated by each person according to their volume of work.
DIY built-in mini sauna in a private house
To implement my project, I placed the wall between the steam room and the shower stall at an angle of approximately 60 degrees. Thus, both rooms have a trapezoidal plan. In the narrowest part of the shower stall, the floor level is lowered and a drain connected to the sewer is installed.
The stove and the entrance door of the steam room are located in its narrow part, which has a number of advantages:
firstly, the steam from the heater evenly heats the entire top shelf;
secondly, it is very convenient to light the stove, since you don’t need to enter the steam room to do this - you just open the door and add firewood, i.e. there is no need to buy a more expensive stove with the ability to fire from the dressing room.
For the partition, I purchased partition blocks with dimensions 400x400x100 mm. The choice of foam concrete blocks is justified by the fact that it has low thermal conductivity, is easy to saw with a hacksaw, and has precise dimensions, which makes it possible to create a minimum seam width. as well as special glue for laying foam concrete 25 kg.

I started the work with markings, which I made on the floor screed with chalk.The first row of the long part of the partition and the narrow part of the partition, next to the stove, to a height of about 1 meter (foam concrete next to the stove can be destroyed by temperature changes while using the sauna) was made of red brick with cement mortar. To prevent moisture from the floor from penetrating into the foam concrete, a water repellent can be added to the solution. Also, in order to bring the standard width of the brick into line with the width of the blocks, I cut 20 mm from the bricks along the long side with a “grinder” with a diamond blade.
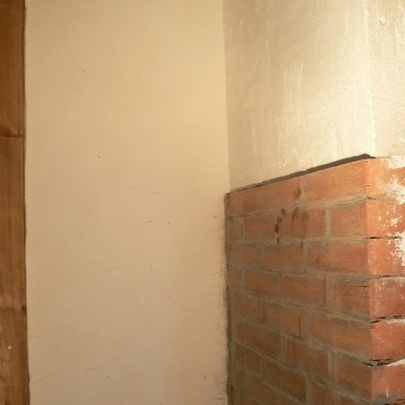
For the internal water supply I chose metal-plastic pipes.
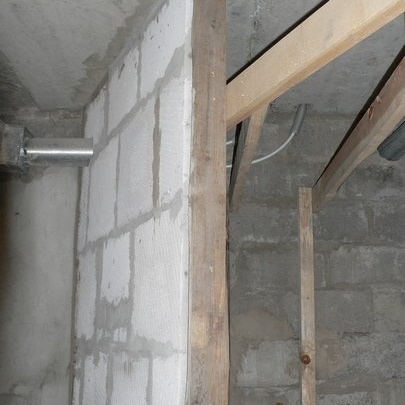
Considering the properties of metal-plastic (installation does not require welding, pipes are easily cut with a hacksaw or a special pipe cutter, they bend easily and take any shape, they are easily connected to fittings using a wrench, they can withstand light defrosting, which is quite possible in a country house, if you forgot drain the water before frost, can be easily repaired in case of damage) made a wiring diagram, calculated the length of the pipe, the number and type of fittings. I marked the installation locations of plumbing equipment and pipe laying routes on the walls and made grooves 20-30 mm deep. Pipes are buried in the wall only in those places where tiles will subsequently be laid.
When laying pipes, a slight slope of the pipes should be maintained to the lowest point of the system, at which a drain valve is installed to empty the system before freezing. Pipes that do not pass through the wall are passed into tubular thermal insulation made of foamed polyethylene. Pipes laid in grooves are fixed in the wall with cement-sand mortar.
Further work on arranging the steam room. Let's start with the markings. First of all, you need to decide on the height of the ceiling.And the recommendations here are as follows: the top shelf should be 10 - 15 cm above the heater, and the distance from the top shelf to the ceiling should be 110 cm. Having measured the heater, I calculated that the ceiling in the steam room should be 220 cm, while the height is only the room is 273 cm. I do not recommend increasing the height of the steam room ceiling - there will be no steam and you will have to heat it for hours.
I decided to nail the lining horizontally, so I placed the bars on the walls vertically. The bars on the outer wall have a cross section of 50x50 mm, on the wall adjacent to the garage 50x80 mm, on the partition 20x80 mm with a length of all bars 230 cm.
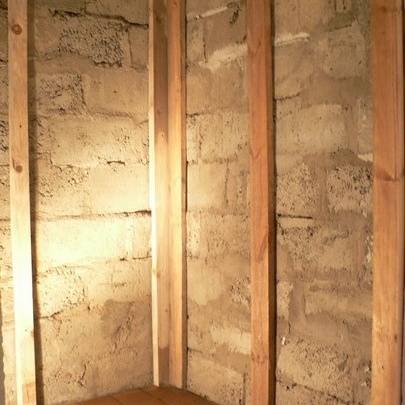
We install the bars using dowel-nails 100 mm long in the main walls and 70 mm long in the partition. The sequence of actions for fastening the bar is as follows: drill four holes in each bar for a dowel-nail, install the bars in increments of approximately 50 cm at a distance of 1 cm from the floor (so as not to rot), and first drive the topmost dowel-nail into each block and a lath to check the flatness of the bars along the walls in the upper part.
I installed bars with a thickness of only 20 mm on the partition because the foam concrete from which it is made has good thermal insulation properties, which means there is no need to additionally insulate this wall. Before attaching the bars to the partition, it is necessary to glue aluminum foil.
We make the ceiling frame from 40x100 mm boards. First, a horizontal strapping is attached to the vertical bars along the perimeter of the steam room, and intermediate bars are attached to it in increments of 50 cm using steel corners and screws.
The place where the chimney will pass through the ceiling must be made of metal. I used available galvanized steel for this.
Now you need to mark the hole for the passage of the chimney. The easiest way to do this is using a real stove, temporarily placing it in the steam room and using a plumb line to mark the contours of the hole. Then the sheet is removed and a hole with a diameter of 130 mm is made according to the markings using a grinder and pliers, which is 10 mm larger than the diameter of the chimney. The wooden frame elements in the chimney area must be protected from the infrared radiation that comes from it. To do this, asbestos fabric is attached to the frame using a stapler, which should then be covered with foil. And only after this the sheet can be finally secured using all the fasteners. When the frame is ready, we check its strength by pulling ourselves up several times on the ceiling bars, and proceed to insulation.
I lined the walls of the steam room that need insulation with 50 mm thick bars. This is in order to lay insulation of the same thickness between them. I used ROCKWOOL basalt wool. We sew the insulation with aluminum foil, securing it to the bars with staples. At the joints, the foil is overlapped and taped with metallized tape. You need to do the same with the ceiling, only the insulation is laid after the clapboard has been hemmed.
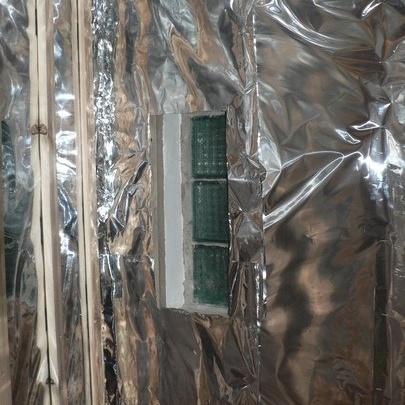
First, wooden antiseptic blocks with a cross-section of 50x50 mm are mounted on the ceiling of the washing room, and then foam plastic is inserted into the spaces between the bars. Then the ceiling was lined with PVC siding. The choice of siding in those days was scarce. I had to take a white one 100mm wide.
Alder lining was used to cover the steam room. Alder has dense matte wood with a pleasant aroma.Before covering, boards must be sorted by color, which for alder can vary from soft pink to copper brown, and these two colors can be present on the same board.
I ended up with three piles of boards matched by color. On the ceiling, which is where you need to start working, I used light and plain boards.
To fasten the lining I used finishing galvanized nails with a conical head, which almost blend in color with the wood.
The lining was sawed with an electric miter saw Makita LS1040. He put boards from two other piles on the walls and began nailing them from the stove from top to bottom. This work does not tolerate haste and fuss; I recommend choosing each board according to color, accuracy of shape, measuring the length and only then sawing it off. Low-quality boards can be used on the back wall under the shelves, and jointed boards can also be used there. I covered the walls, shelves and door with Supi Saunavaha (Tikkurila Finland) - a colorless protective composition containing natural wax, which has proven itself in long-term use.
According to my design project, the floor in the steam room is covered with unglazed terracotta tiles measuring 15x15 cm. This material harmonizes well with the brick wall next to the stove, and the color matches well with the alder lining with which I lined the inside of the steam room. I made the seams 5 mm wide and rubbed them with a dark gray fugue; I used the same fugue to decorate the seams in the brickwork.
I made the floor in the washing room with electric heating. This will allow you to quickly and effectively warm up one small room, creating comfortable conditions in it, without turning on the heating of the entire house.
A reinforcing mesh was laid on the foam insulation; a heating cable was attached to it, and then a screed 5 cm thick was made.
In the part of the floor where there will be a shower stall, you should make a smooth lowering of approximately 50 mm, having previously installed a shower drain. The ladder mesh should be 15-20 mm higher than the concrete screed, since the floor tiles still need to be laid, but its level should coincide with the level of the ladder mesh. Let the concrete set for 3-4 days.
The floor was tiled with green porcelain tiles, and the walls were covered with glazed ceramic tiles, also in two shades of green.
Let's summarize
A built-in sauna appeared in a country house located on a small plot of land.
Construction It took four months, of which only one month was a full-fledged vacation.
Advantages
- Short construction time
- No outside specialists, teams, or equipment were involved
- Small amount of financing
- Combining several functions in one room allows you to use it rationally: a toilet and shower constantly, and a steam room occasionally.
- The small volume of the steam room allows you to quickly heat it up in 40 minutes, while a small armful of firewood is consumed.
- There is no need to build a rest room since all other rooms of the house become a rest room.
Flaws
- The steam room can only accommodate two people sitting or one lying down
- It heats up quickly, but also cools down quickly, so you have to add firewood if 4 people take turns steaming.
- If you are steaming and wood is burning in the stove, then a lot of heat comes from the chimney, which is not pleasant for everyone.
Watch the video
In the video you can see all the details of my project, and on my channel you will also find the continuation of construction and the condition of the sauna after 14 years of operation.
Similar master classes
Particularly interesting
Comments (1)