Fast metal shears driven by an electric drill
Cutting sheet steel with a grinder is accompanied by a lot of sparks, smoke and noise, so an angle grinder is not the best choice for this purpose. For large-scale work, it is better to make metal shears driven by a drill. They cut steel without flying scale or burning, and they do it faster.
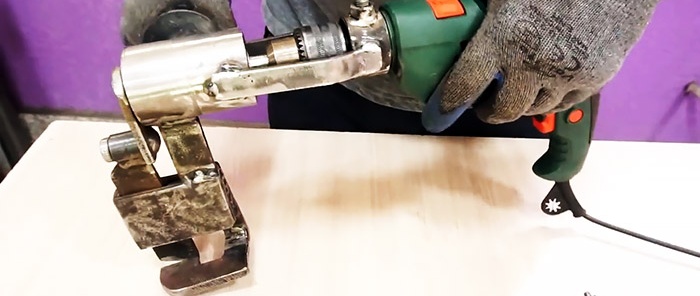
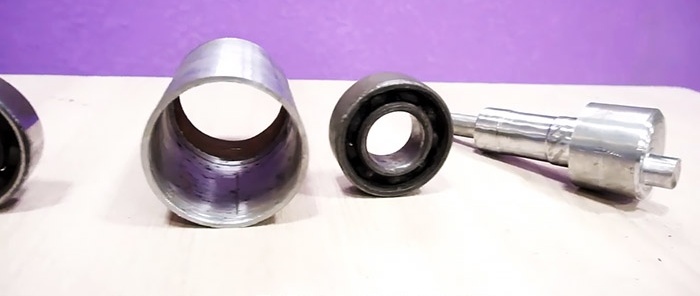
It is necessary to turn an eccentric for the scissors on a lathe from round timber. It provides a seat for bearings and a thin shank for fixation in the drill chuck. The length of the entire workpiece should be 12-14 mm.
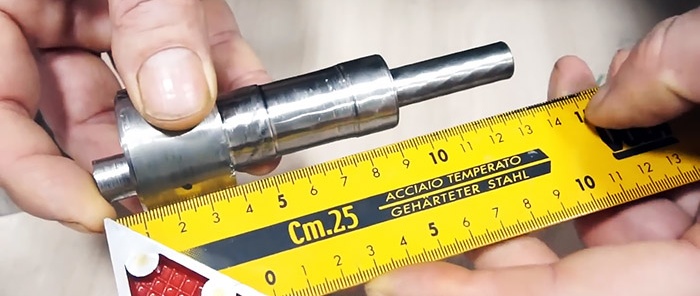
2 bearings are installed on the eccentric. They are spread along the edges of their bore diameter and fixed by welding. Then the eccentric with bearings is placed in the pipe section. Before this, holes are made in the pipe opposite the location of the bearings. The upper races are welded through them.
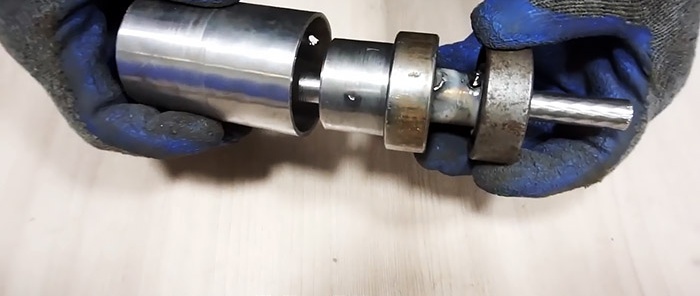
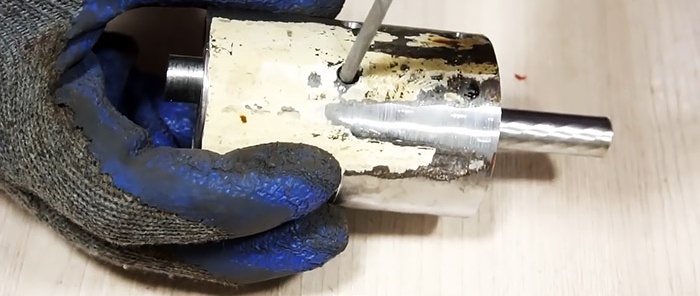
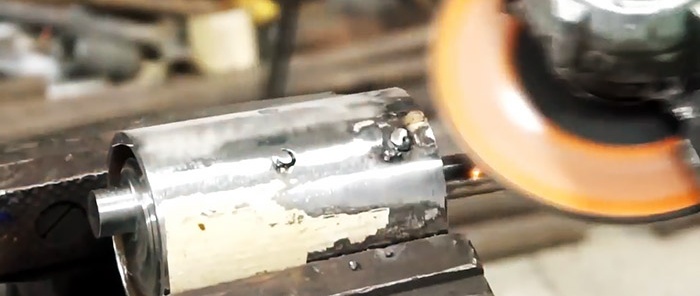
A lever for the eccentric is cut from sheet steel.
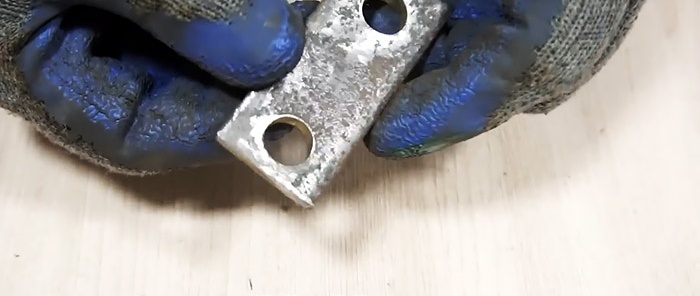
A knife with a beveled blade will be attached to it. The knife is lowered on one side.
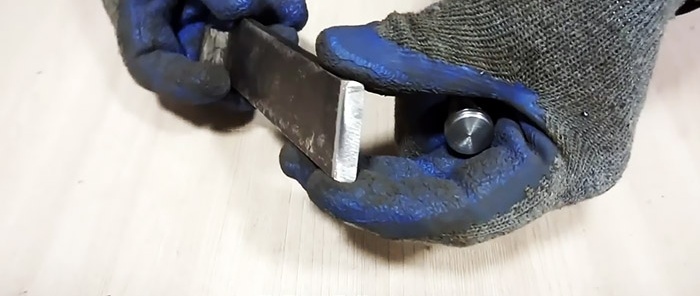
A bushing with the same diameter as the hole in the lever is welded to the back of the knife.
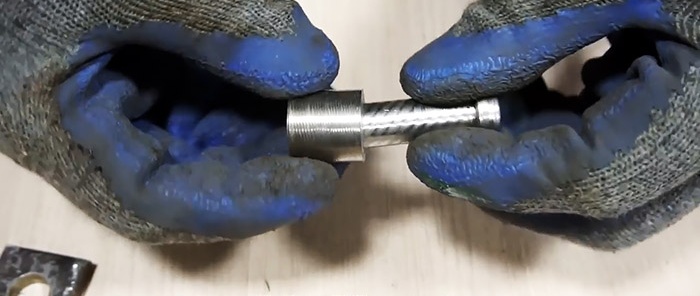
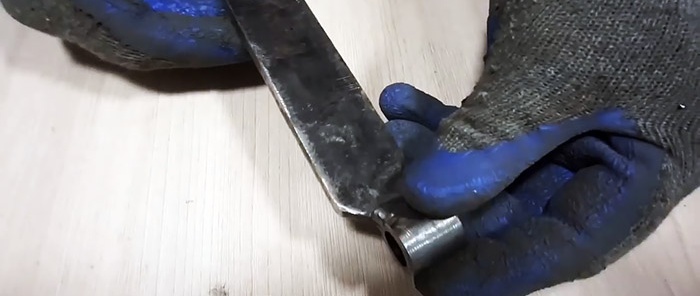
The knife and lever are connected with a finger, the end of which is welded.
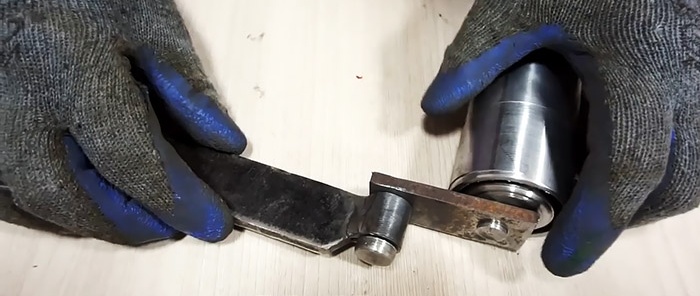
Next, a guide for the knife is made. To do this, a strip is welded to the pipe in which the eccentric with bearings is located. Flags made of thinner sheet steel are welded to it on both sides, between which the knife will slide.
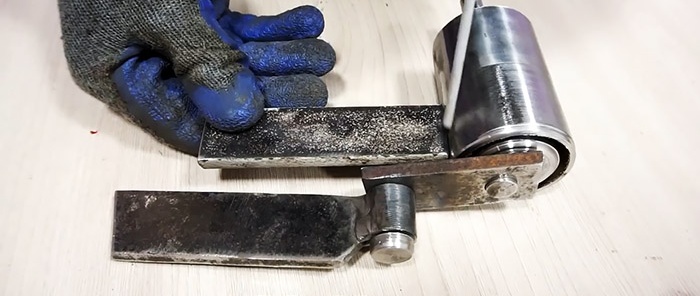
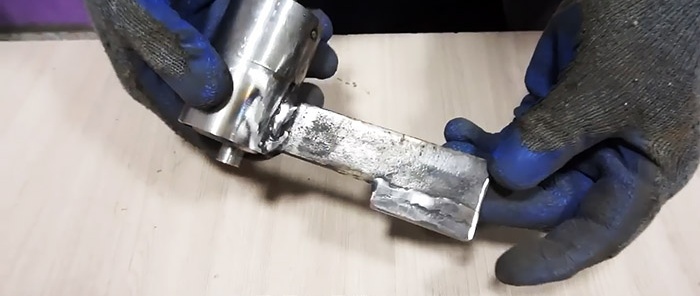
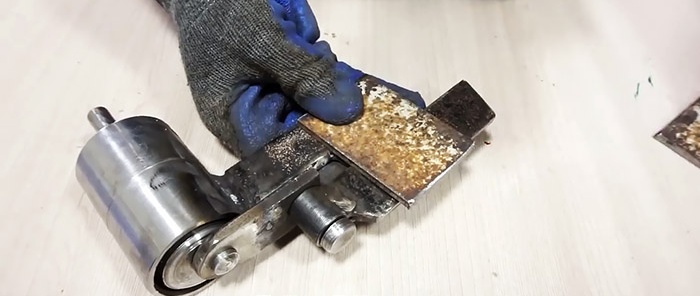
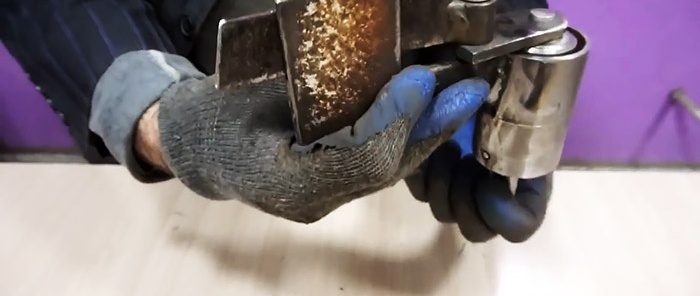
After checking and adjusting the made mechanisms, you need to harden the knife. It is heated red hot and cooled in oil. After this, the knife is installed in place, and the gap on the back side of the guide flags is welded with an insert.
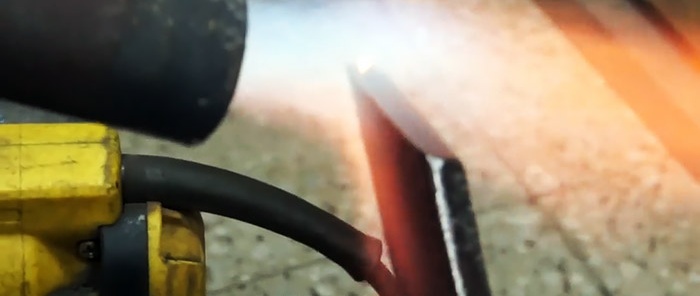
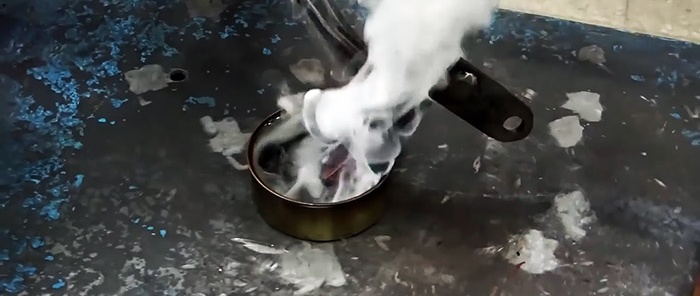
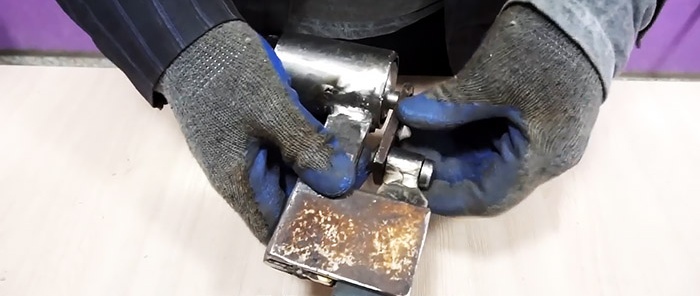
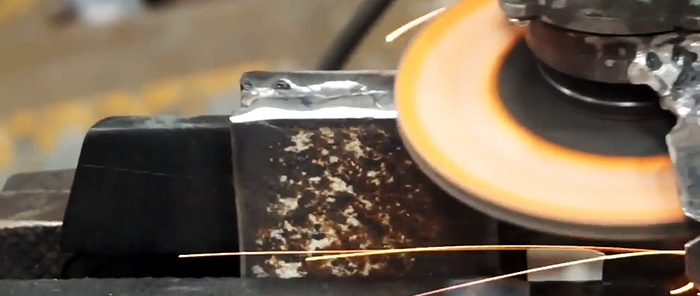
The next step is to cut out the bottom knife. It can be made from a flat file or other suitable steel. The knife is welded to a strip located perpendicular to it. Then the strip is aligned relative to the upper knife and welded to the guide with flags.
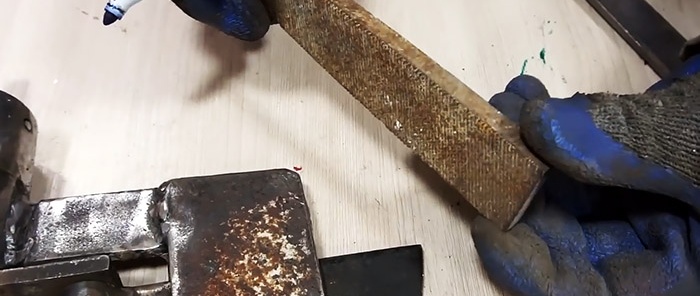
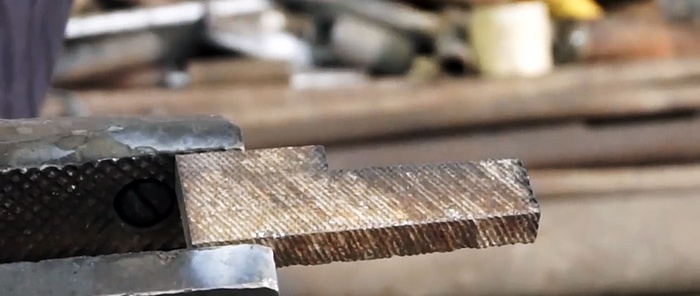
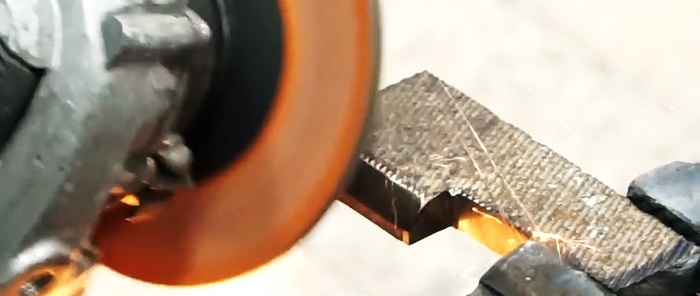
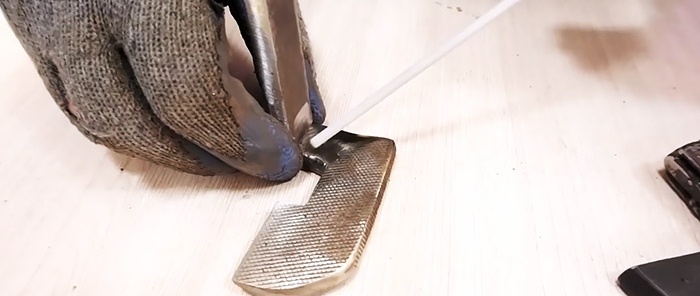
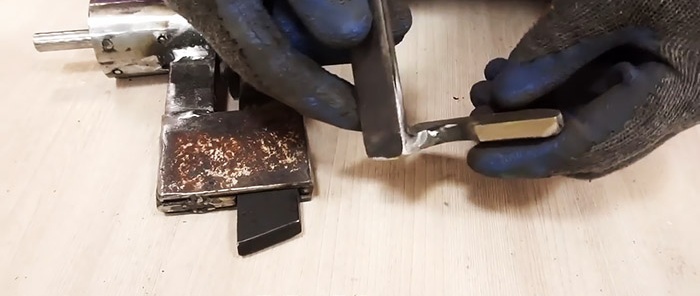
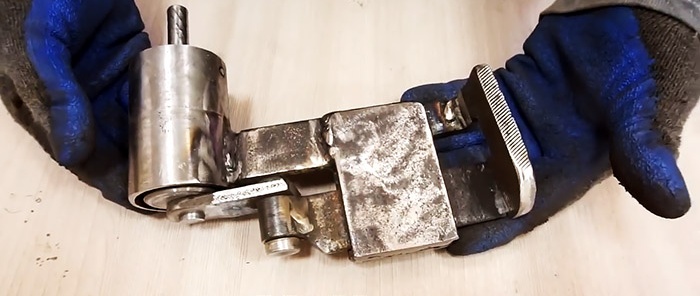
To attach the adapter, you need to take a piece of pipe with an internal diameter corresponding to the size of the drill body at the location where the standard handle is installed. A hole is made in the pipe, a nut is welded around it, and a bolt is screwed into it. As a result of tightening it, the pipe will be securely held on the drill. After this, the adapter shank is clamped into the chuck. Then the body of the scissors and the tube on the drill are welded together. For this, 2 folded strips are used.
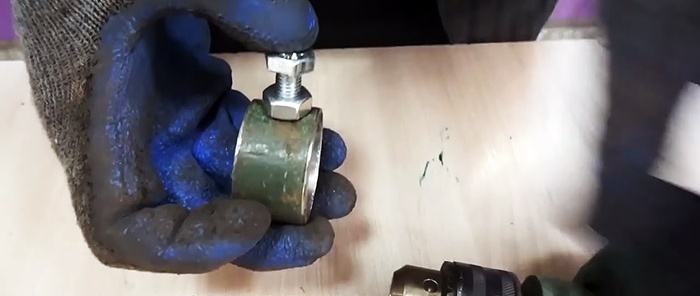
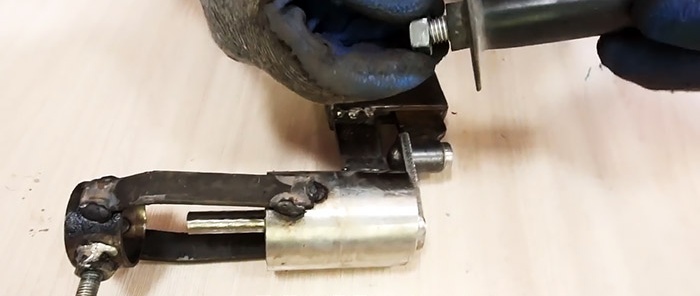
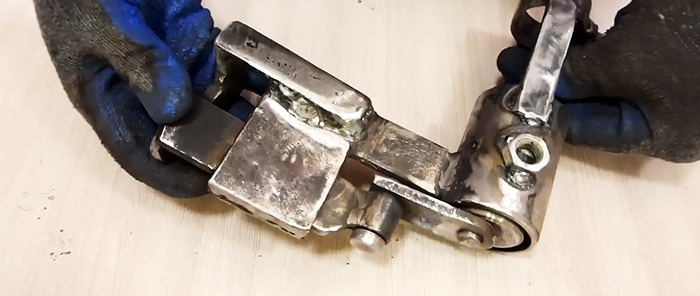
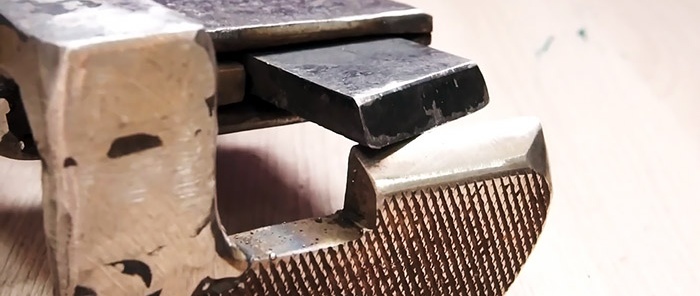
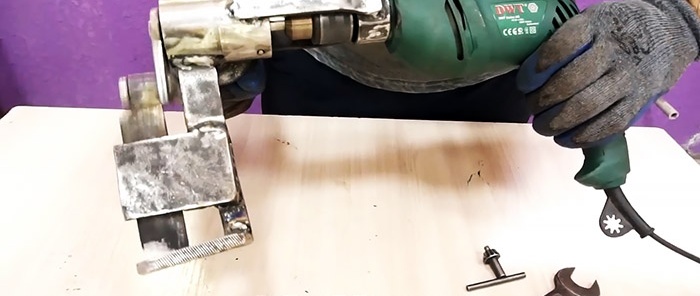
A nut is welded to the right side of the scissors body, and the handle from the grinder is screwed into it. Its presence increases the usability of the tool. Before using the scissors for the first time, you need to lubricate their rubbing parts.The resulting tool, when properly sharpened, cuts 1.5 mm steel sheets like butter, while it also has power reserves for more complex materials.
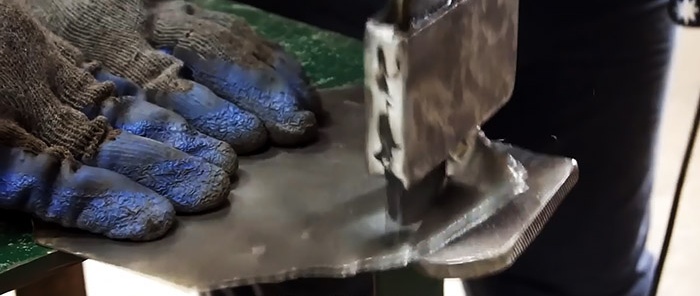
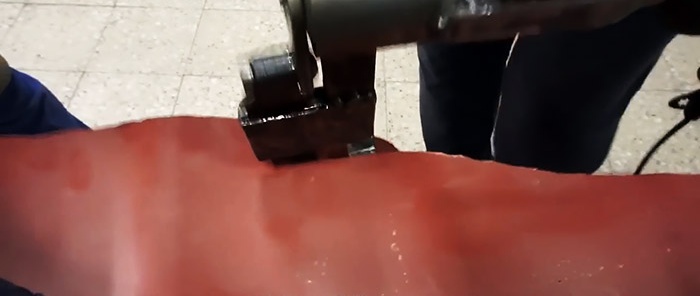
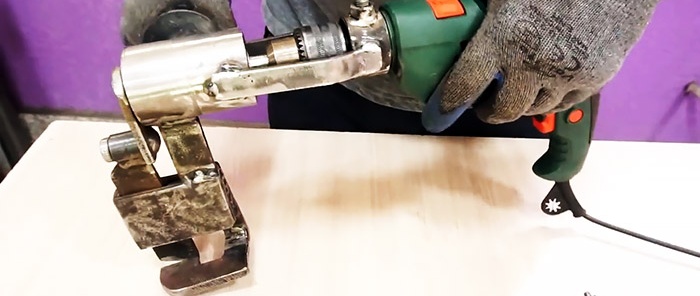
Basic materials:
- round timber 40 mm;
- bearings 2 pcs.;
- steel pipe with an internal diameter for bearings;
- sheet steel 2, 5, 10 mm;
- handle from an angle grinder;
- M8 bolt;
- M8 nuts – 2 pcs.
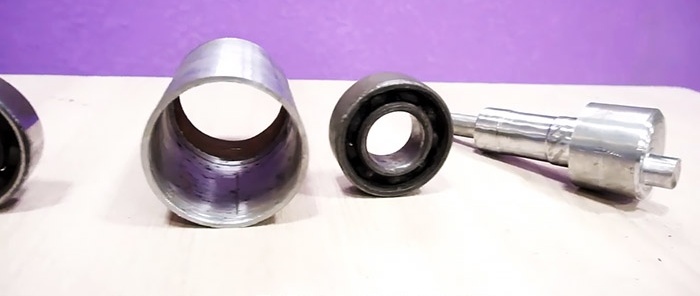
Nozzle assembly
It is necessary to turn an eccentric for the scissors on a lathe from round timber. It provides a seat for bearings and a thin shank for fixation in the drill chuck. The length of the entire workpiece should be 12-14 mm.
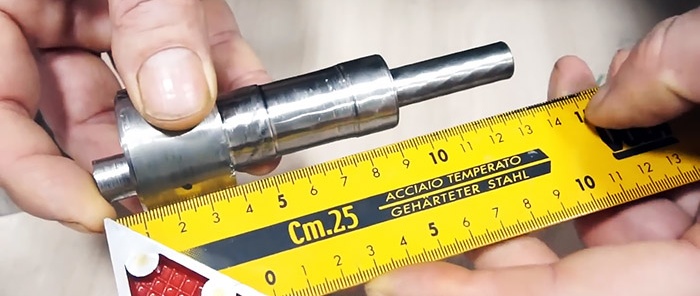
2 bearings are installed on the eccentric. They are spread along the edges of their bore diameter and fixed by welding. Then the eccentric with bearings is placed in the pipe section. Before this, holes are made in the pipe opposite the location of the bearings. The upper races are welded through them.
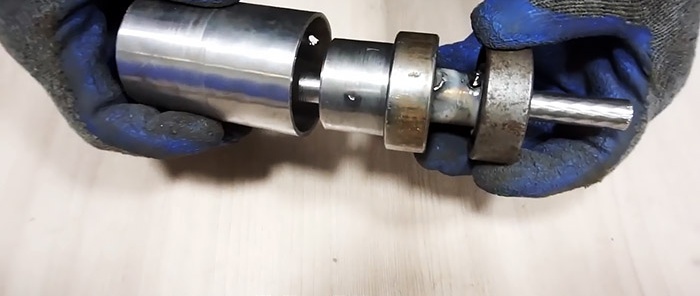
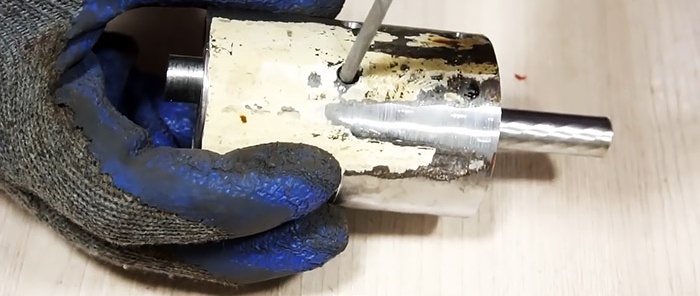
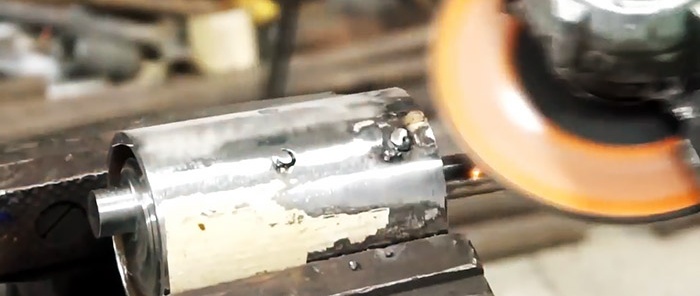
A lever for the eccentric is cut from sheet steel.
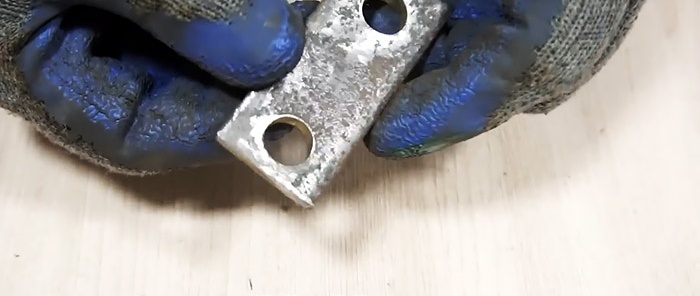
A knife with a beveled blade will be attached to it. The knife is lowered on one side.
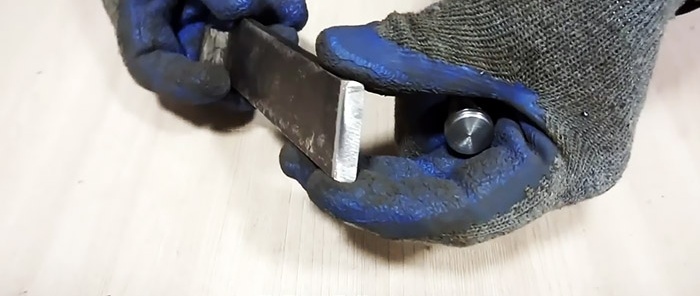
A bushing with the same diameter as the hole in the lever is welded to the back of the knife.
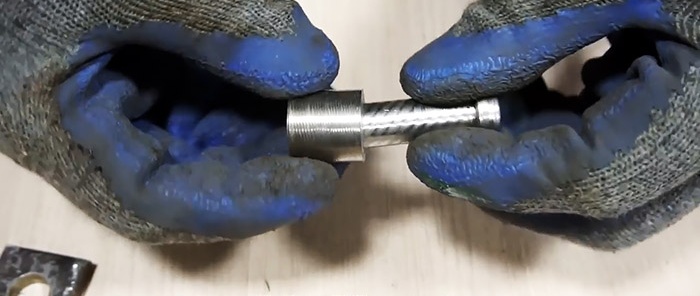
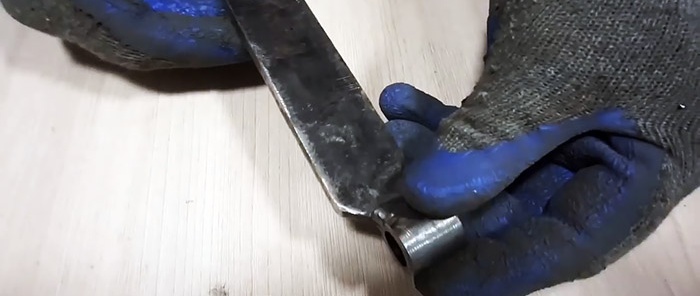
The knife and lever are connected with a finger, the end of which is welded.
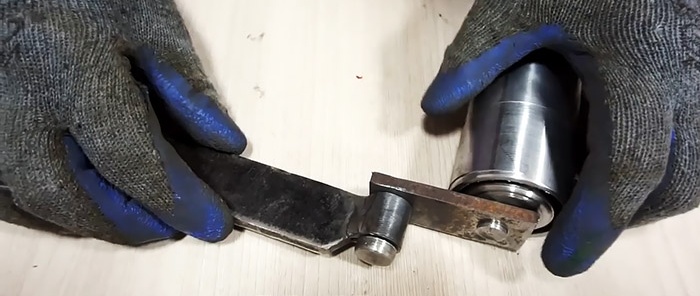
Next, a guide for the knife is made. To do this, a strip is welded to the pipe in which the eccentric with bearings is located. Flags made of thinner sheet steel are welded to it on both sides, between which the knife will slide.
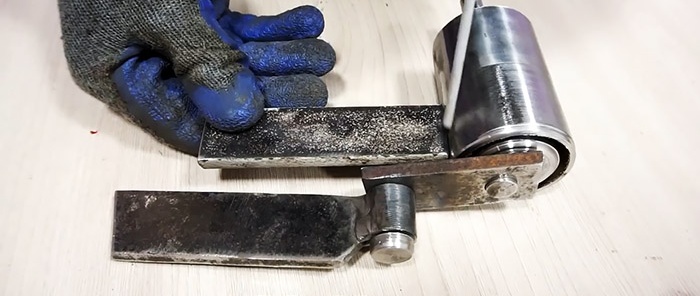
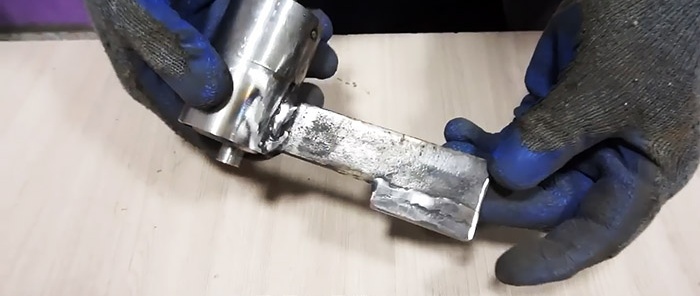
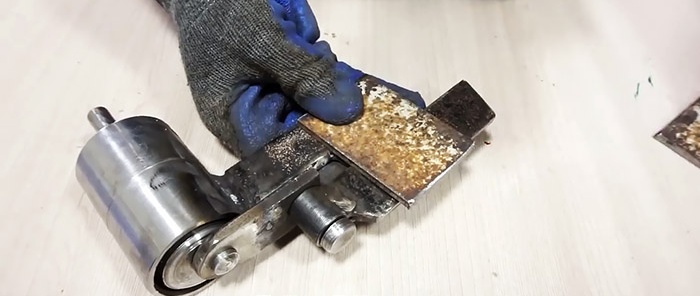
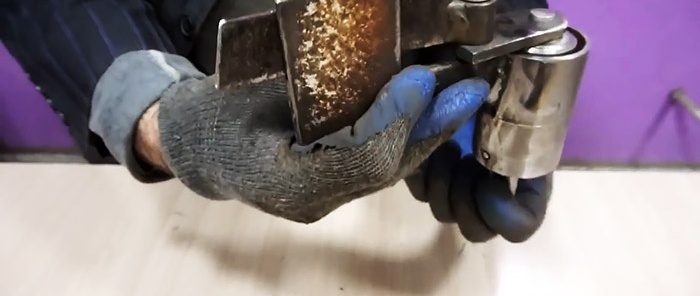
After checking and adjusting the made mechanisms, you need to harden the knife. It is heated red hot and cooled in oil. After this, the knife is installed in place, and the gap on the back side of the guide flags is welded with an insert.
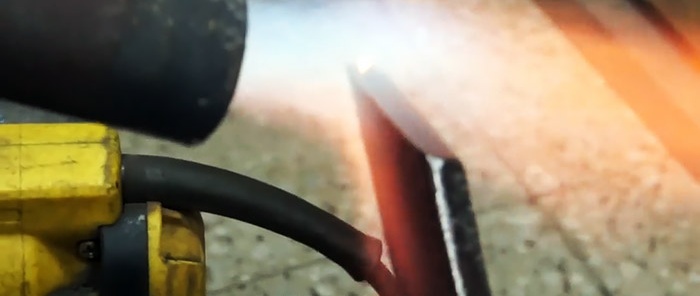
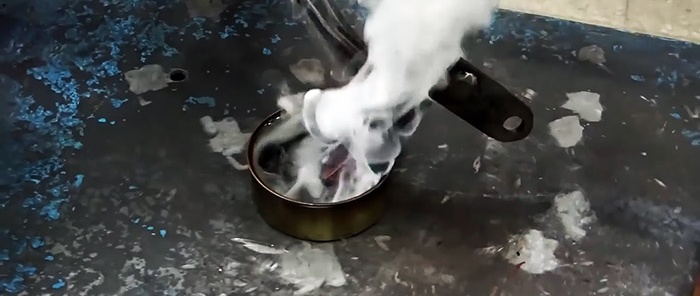
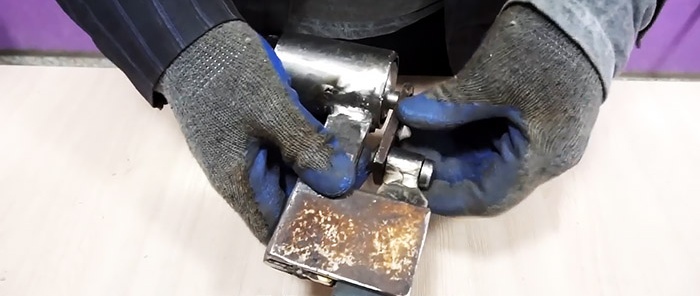
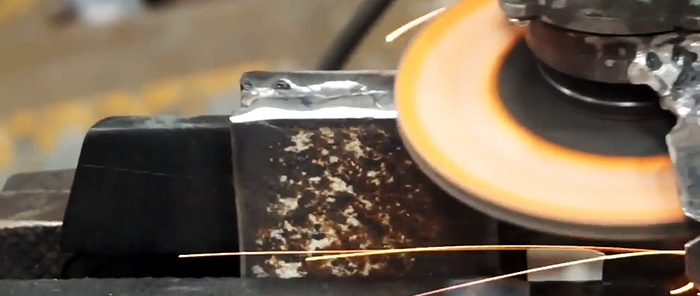
The next step is to cut out the bottom knife. It can be made from a flat file or other suitable steel. The knife is welded to a strip located perpendicular to it. Then the strip is aligned relative to the upper knife and welded to the guide with flags.
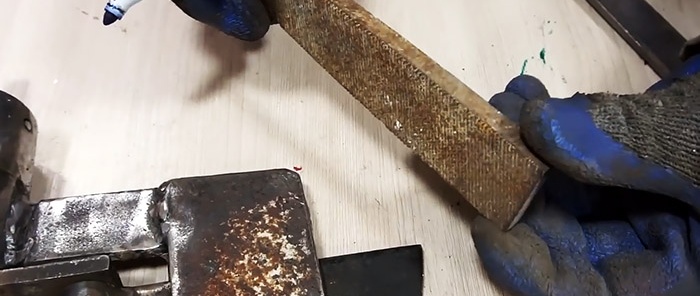
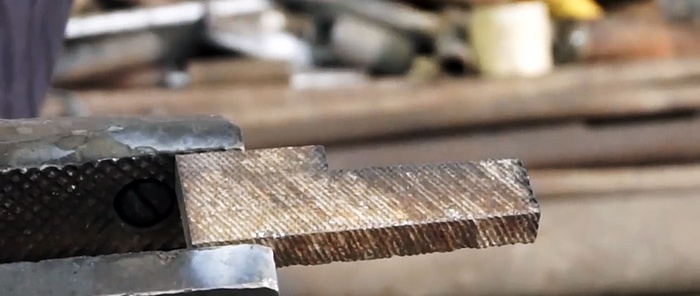
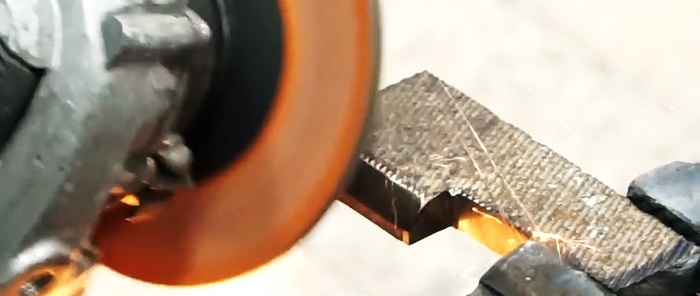
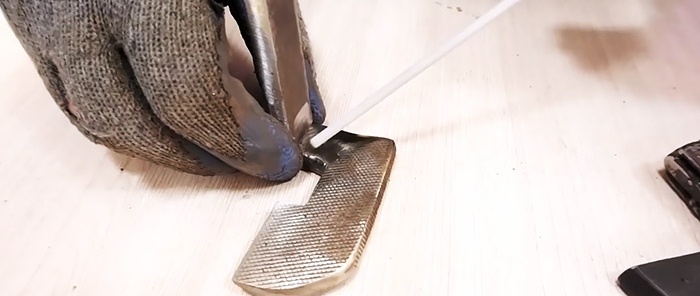
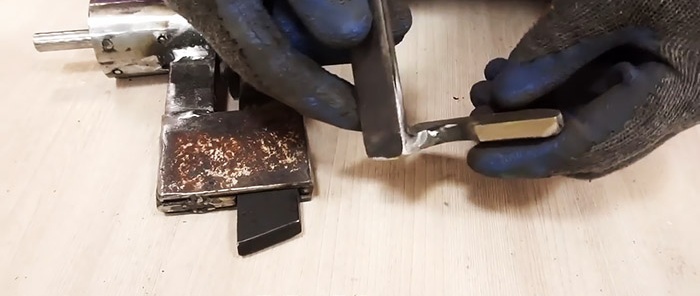
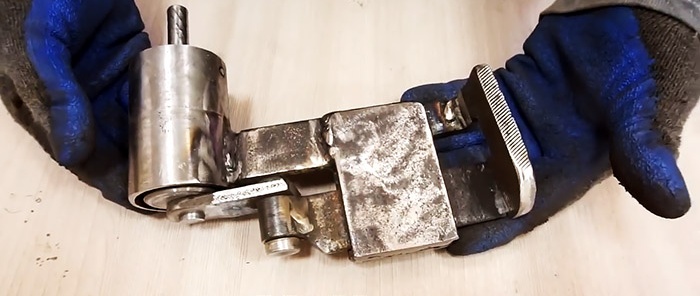
To attach the adapter, you need to take a piece of pipe with an internal diameter corresponding to the size of the drill body at the location where the standard handle is installed. A hole is made in the pipe, a nut is welded around it, and a bolt is screwed into it. As a result of tightening it, the pipe will be securely held on the drill. After this, the adapter shank is clamped into the chuck. Then the body of the scissors and the tube on the drill are welded together. For this, 2 folded strips are used.
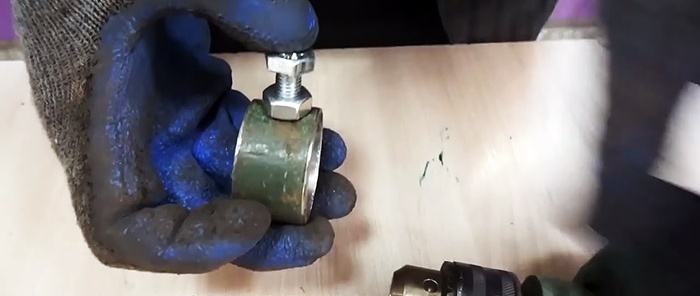
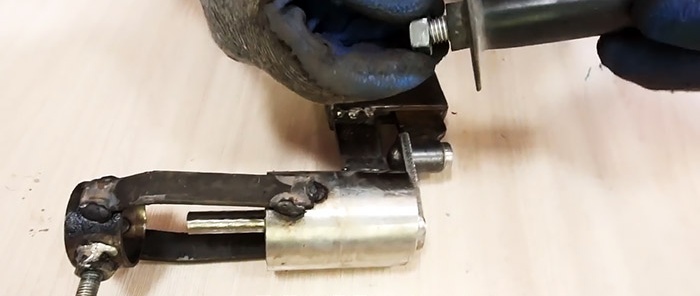
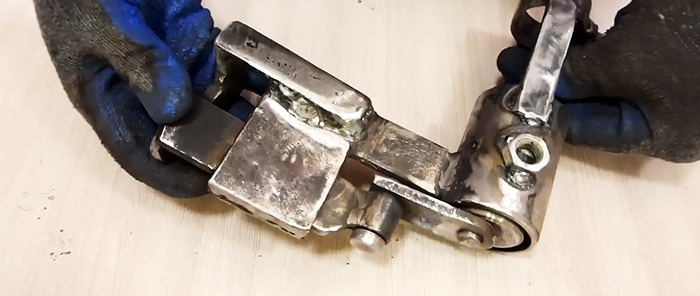
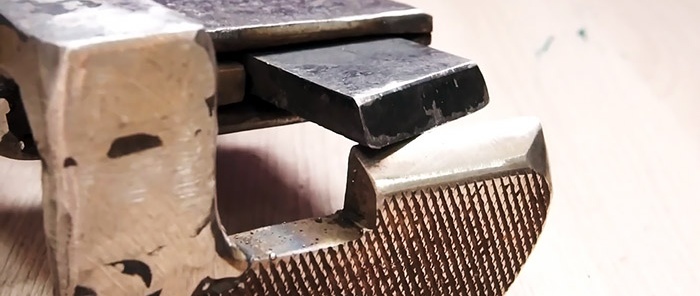
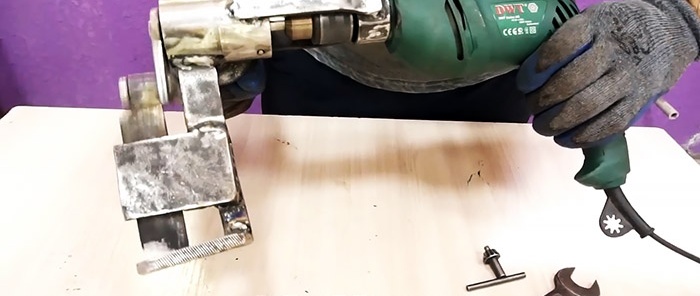
A nut is welded to the right side of the scissors body, and the handle from the grinder is screwed into it. Its presence increases the usability of the tool. Before using the scissors for the first time, you need to lubricate their rubbing parts.The resulting tool, when properly sharpened, cuts 1.5 mm steel sheets like butter, while it also has power reserves for more complex materials.
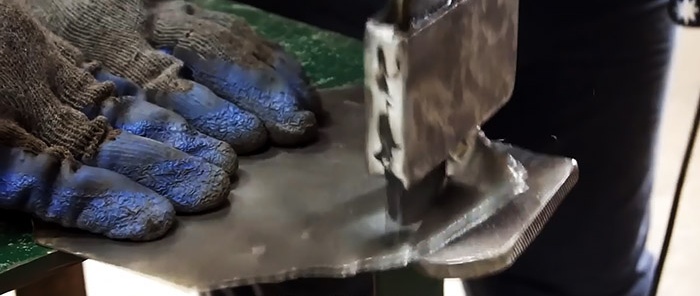
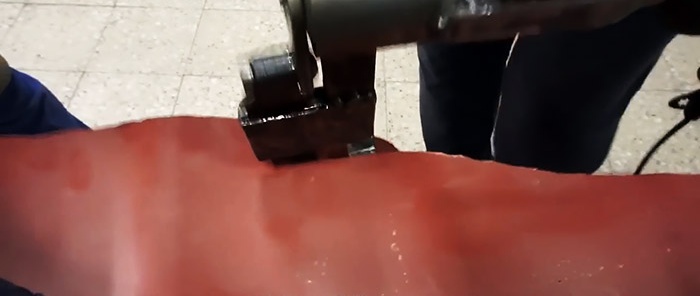
Watch the video
Similar master classes
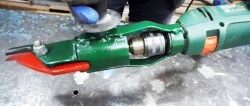
Homemade drill attachment for fast metal cutting
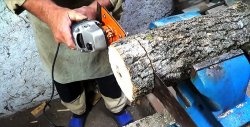
Do-it-yourself electric hacksaw from a grinder
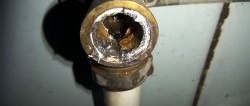
How to unscrew a broken eccentric on a faucet
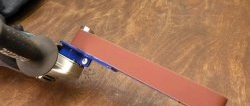
How to make a grinder attachment for an angle grinder
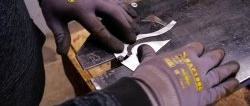
How to make a simple machine for shaped cutting of metal from a drill
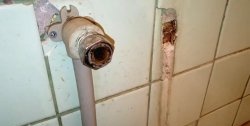
How to unscrew the eccentric of a mixer
Particularly interesting
Comments (0)