Reliable connection of profile pipes without welding or bolts
Almost always, when working with a profile pipe, connections are made using electric welding, rivets or mounting perforated angles using bolts and metal screws. However, there is another very reliable method that will allow you to connect profile pipes of different sections at right angles.
To make this connection, it is necessary that the pipes have different sections. The method allows you to make a T-shaped fastening with a thin pipe adjacent to a thicker one. To carry it out, it is necessary to draw transverse lines at the junction point on the larger pipe, displaying the contours of the walls of the smaller one. Marks are drawn along the entire circumference of the pipe.
At the adjacent end of the thinner tube, a transverse line should be marked. When drawing it, you need to retreat half the width of this pipe. It should also be carried out around the entire circumference.
Next, using a grinder with a sharpened cutting disc, you need to cut a window on one of the walls of the larger pipe between the parallel marks. First, 2 cuts are made along transverse lines. Then you need to connect them with longitudinal cuts. It is important that the distance between them is also equal to the width of the smaller pipe.
On the reverse side of the cut hole you need to make 2 longitudinal cuts. They should be exactly the opposite.
On a thin pipe, you need to make longitudinal cuts along the edges to the transverse line. Then along the line you need to cut off any 2 opposite sides. If the cut is not quite neat, then you should trim the metal at the corners using a file. It is also worth correcting the shape of the hole on a large pipe.
After this, you need to place the trimmed end of the thin pipe against the hole on the large one so that the remaining eyes on it are located opposite the longitudinal cutouts. Then it needs to be driven into the hole with hammer blows. As a result, the eyes will come out from the opposite side through longitudinal slits. Next, you need to turn the connection over and bend the protruding spikes inward.
The result is a very strong, durable connection that looks much neater than a pile of rivets, screws or bolts. If you don't have a welding machine, this is the best you can come up with.
What you will need:
- profile pipes of different sections;
- square;
- Bulgarian;
- file;
- hammer
- marker.
The process of connecting profile pipes
To make this connection, it is necessary that the pipes have different sections. The method allows you to make a T-shaped fastening with a thin pipe adjacent to a thicker one. To carry it out, it is necessary to draw transverse lines at the junction point on the larger pipe, displaying the contours of the walls of the smaller one. Marks are drawn along the entire circumference of the pipe.
At the adjacent end of the thinner tube, a transverse line should be marked. When drawing it, you need to retreat half the width of this pipe. It should also be carried out around the entire circumference.
Next, using a grinder with a sharpened cutting disc, you need to cut a window on one of the walls of the larger pipe between the parallel marks. First, 2 cuts are made along transverse lines. Then you need to connect them with longitudinal cuts. It is important that the distance between them is also equal to the width of the smaller pipe.
On the reverse side of the cut hole you need to make 2 longitudinal cuts. They should be exactly the opposite.
On a thin pipe, you need to make longitudinal cuts along the edges to the transverse line. Then along the line you need to cut off any 2 opposite sides. If the cut is not quite neat, then you should trim the metal at the corners using a file. It is also worth correcting the shape of the hole on a large pipe.
After this, you need to place the trimmed end of the thin pipe against the hole on the large one so that the remaining eyes on it are located opposite the longitudinal cutouts. Then it needs to be driven into the hole with hammer blows. As a result, the eyes will come out from the opposite side through longitudinal slits. Next, you need to turn the connection over and bend the protruding spikes inward.
The result is a very strong, durable connection that looks much neater than a pile of rivets, screws or bolts. If you don't have a welding machine, this is the best you can come up with.
Watch the video
Similar master classes
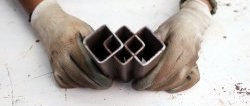
How to make a collapsible connection of profile pipes without welding
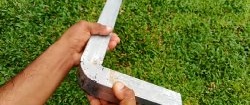
Unusual corner connection of a profile pipe
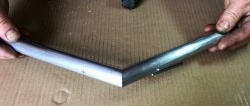
How to connect tubes at any angle without welding
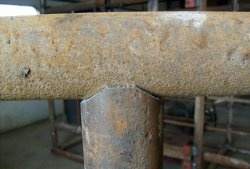
How to make a high-quality pipe saddle for angled tapping
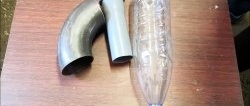
We connect 2 pipes of different diameters with a PET bottle
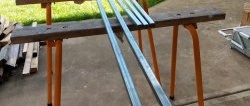
How to make a frame from a profile without welding
Particularly interesting
Comments (1)